Explore the standard mold polishing process
The 2024 Standard Mold Polishing Process offers our readers a comprehensive guide on the methods and techniques to achieve the highest quality polishing results for manufacturers. Join AMS in exploring the article below to ensure your mold surfaces are always flawless!
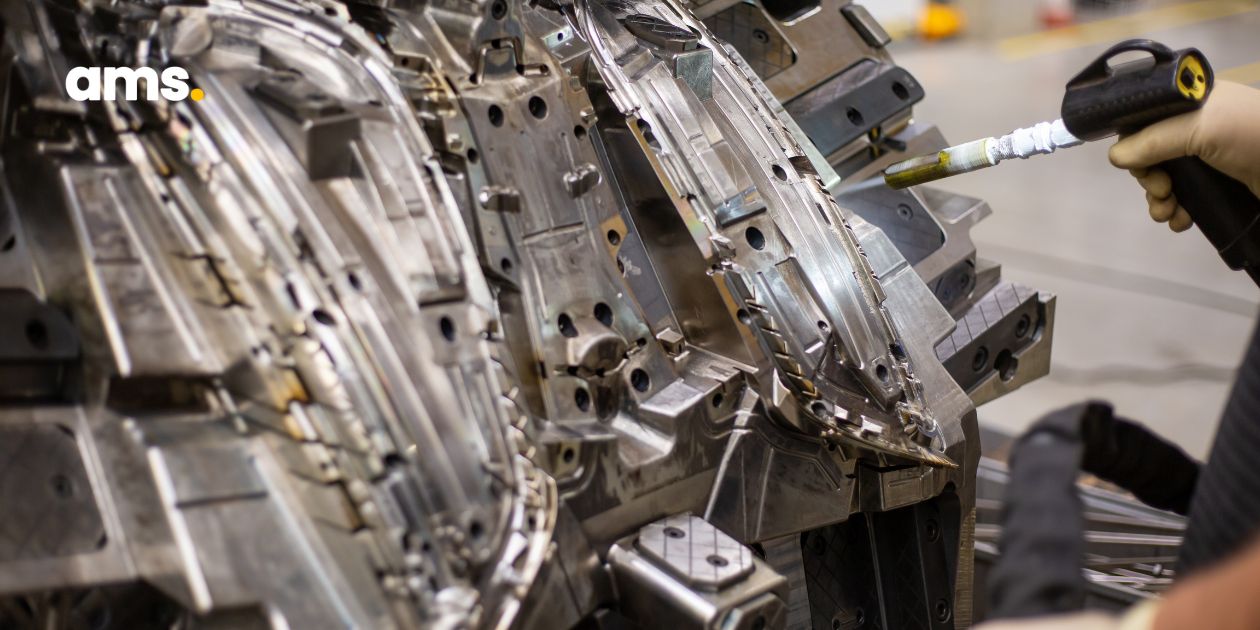
1. What is Mold Polishing?
Mold polishing is a method that uses auxiliary materials to achieve a smooth and glossy mold surface. Some typical materials include artificial diamond sets, grinding stones, felt, brooms, etc. This process is carried out through a series of cutting and abrasive actions combined with various polishing techniques.
For materials requiring a high-quality surface finish, manufacturers will employ ultra-precision polishing techniques. Abrasive solutions are applied to the workpiece surface swiftly and precisely, resulting in an outstanding finish with a surface roughness of up to 0.008 micrometers.
2. Why Is Mold Polishing Necessary?
Mold polishing is a crucial step in the plastic mold manufacturing process. It plays an essential role in various types of molds with different materials and requirements. The purpose of mold polishing is not only to enhance product quality but also to improve aesthetics, increase corrosion resistance, and reduce injection molding cycle times.
If mold polishing is not performed, manufacturers may face several issues, such as:
-
Mold Cracking and Reduced Lifespan: Unpolished molds are more prone to cracking and have lower durability due to the stress from the molding process, exposure to heat, and material residues clinging to the mold, leading to an imperfect mold surface.
-
Poor Product Quality: Products may suffer from defects such as scratches, rough surfaces, and voids due to the uneven and unpolished mold surface.
-
Reduced Production Efficiency: The manufacturing process may not run smoothly, leading to clogging issues and difficulties in mold filling, thereby reducing overall production efficiency.
The efficiency and reliability of the entire manufacturing process are crucial factors driving growth and product quality. That's why businesses should focus on a standard mold polishing process to boost productivity and optimize costs.
>> Learn more: How Regular Mold Polishing and Maintenance Bring Economic Benefits.
3. Details of the 2024 Standard Mold Polishing Process
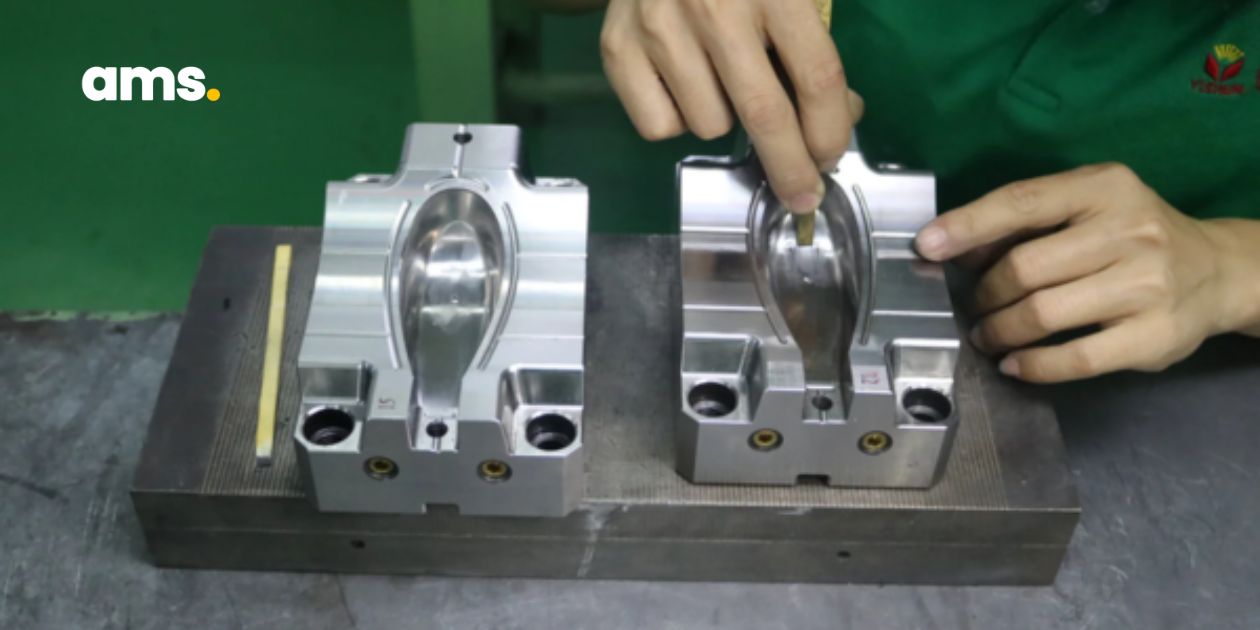
The most crucial aspect of the mold polishing process is the use of high-quality equipment, tools, and polishing accessories such as grinding stones, sandpaper, and diamond powder.
Mold polishing requires precision and a high surface finish, commonly referred to as mirror polishing. This technique demands flatness, smoothness, and geometric accuracy. Currently, there are various polishing methods, including chemical polishing, magnetic polishing, and electrochemical polishing. However, these methods do not guarantee precise dimensions, making mechanical polishing the preferred and most widely used option.
Below is the standard mold polishing process consisting of three basic steps:
3.1. Step 1: Rough polishing
The first step in the mold polishing process is rough polishing (rough grinding). Burrs appear a lot on the mechanical surface after undergoing the effects of milling, turning, punching, EDM or other processing. In order to avoid creating sparks during the grinding process, the grinding wheel is 3mm in diameter and the material is WA#400.
Next is to use an oil grinding stone for manual grinding, this step will handle the scratches left by the sanding step. The order is usually #180, #240, #320, #400, #600 or #1000. To save time, many manufacturers often start with #400.
It should be noted that when using an oil grinding stone, it is necessary to check the surface of the workpiece first and clean it with kerosene so that the grinding stone can work at its maximum capacity and is not affected by dust. For some complex molds, grinding should be done from difficult to easy, the mold cavity and dead corners are difficult to grind, so they should be prioritized for grinding first, then the flat surface.
3.2. Step 2: Medium mold polishing
After step 1, the mold surface is much smoother but does not meet the standard for fine polishing. This stage is called medium mold polishing in the entire mold polishing process.
The faint scratches are further treated using tools such as polishing brushes or sandpaper. You can use your hands or a 90-degree handheld grinder to improve grinding efficiency. In this stage, you need to use moderate grinding force, not too strong like the previous stage to avoid damaging the mold surface.
3.3. Step 3: Fine polishing
Fine polishing is the final step in the 2024 standard mold polishing process. We often use diamond powder combined with sheep wool felt. Grinding force should be very light to avoid scratching and damaging the mold surface.
For mold surfaces that require high gloss such as optical plastic injection molding, the mold polishing process needs to go through many mold grain levels from low to high, diamond powder with super fine grain size from 1μm -> 0.5μm -> 0.25μm is the optimal choice. For narrow grooves on the mold, specialized materials such as diamond files and diamond grinding heads are required to achieve the highest efficiency.
>> You may be interested in: How to use Diamond Polishing Powder
4. AMS - choose the leading reputable mold polishing material supplier in Vietnam
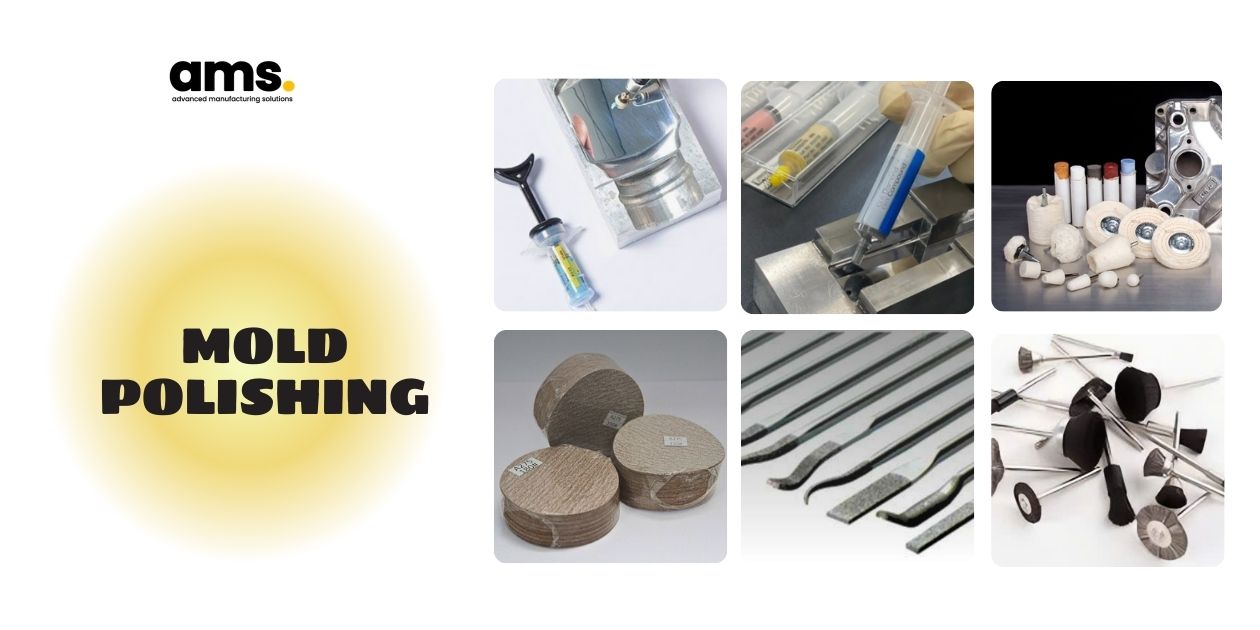
In the context of the strong development of the mold and manufacturing industry, AMS understands that the output of manufactured products increases many times over each period. According to the report of the Ministry of Industry and Trade of Vietnam, following the recovery momentum from the end of 2023 until now, industrial production continues to show a positive trend, continuing to rise, showing that Vietnam is starting a period of good growth. The Purchasing Managers' Index (PMI) of Vietnam's manufacturing industry in July 2024 reached 54.7 points, the highest level since November 2018. In addition, statistics of the mold industry have reflected the related growth, the value of the mold and precision engineering industry in Vietnam is currently over 1 billion USD/year. In particular, with a growth rate of 18%/year, this industry is attracting the attention of many domestic and foreign enterprises. Notably, Vietnamese enterprises only make 8.5% of injection molds, the rest are stamping molds. Therefore, the demand for molds for plastic, mechanical, machine parts, components, etc. production to improve product quality is very large, helping domestic enterprises increase their capacity to participate in the global supply chain. Each successful field is closely linked to each other, the development of mold production and processing leads to a great demand for reputable and quality mold polishing materials.
That is why AMS is constantly striving to bring advanced technical solutions and become the leading reputable mold polishing material supplier in Vietnam so that manufacturers can confidently develop prosperously and sustainably.
At AMS: The leading supplier of polishing products in the mold industry, we have everything you need for polishing requirements. AMS is ready to support customers with a dedicated and personalized consulting team. Contact us today!
AMS Company, Ltd.243/9/10D To Hien Thanh, Ward 13, District 10
Hot line: 028.3868 3738/3903 - Fax: 028.3868 3797