What are the benefits of using polishing solutions for surface finishing?
Polishing solutions from Kemet meet a variety of customer needs for high precision, superior aesthetics and product finishing that meets quality standards.
Polishing solutions, particularly lubricating fluids, are becoming increasingly popular in metal surface finishing. Serving as a catalyst in mold polishing technology, these solutions contribute to superior finishing and provide an exceptional aesthetic to mold surfaces. However, detailed information on the functions of these auxiliary substances is rarely shared. Join AMS as we explore the functions and benefits of polishing solutions, along with a comprehensive guide to selecting the right polishing fluid for your specific needs in the following article!
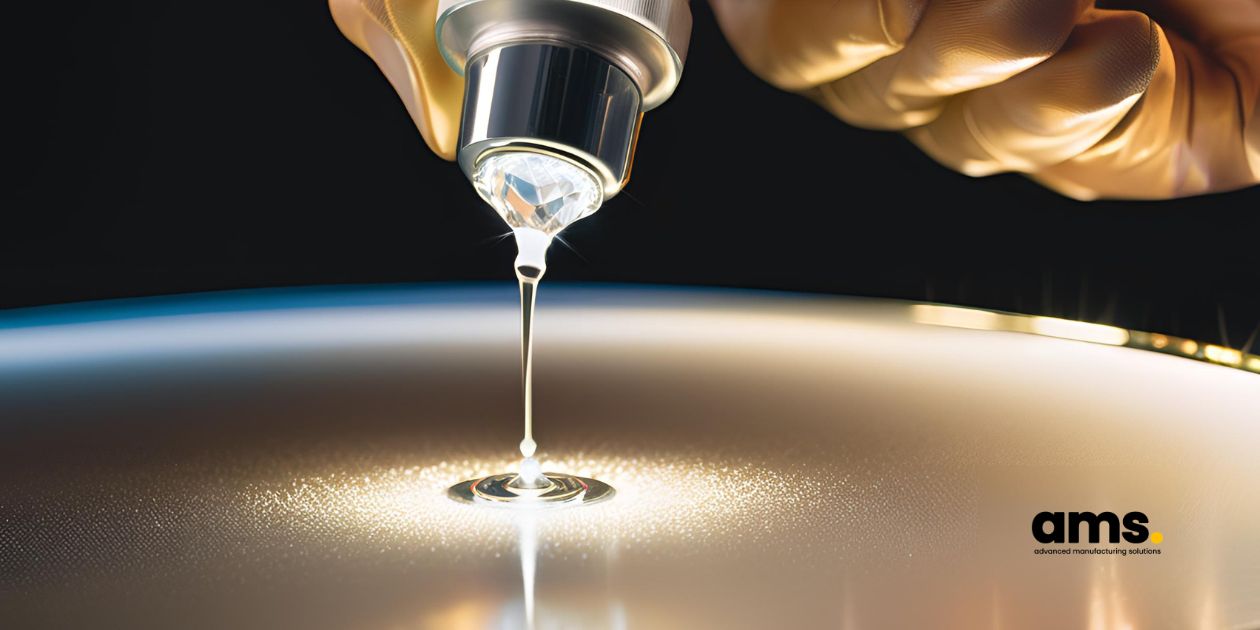
1. What is a Polishing Solution?
A polishing solution is a specialized chemical compound in liquid form, designed to support surface treatment and product finishing processes. Today, manufacturers offer a wide range of polishing solutions in various colors—such as green, milky white, and yellow—each providing unique benefits depending on the intended use.
Polishing and grinding solutions are widely used across industries like precision engineering, mold making, and metalworking. These solutions play an essential role in enhancing surface shine, boosting aesthetic appeal, and increasing durability, making them indispensable for achieving superior surface finishes.
>> See more: What is Diamond Powder Polishing?
2. Benefits of Using a Polishing Solution
2.1. Creating a High-Gloss Finish
Before products are released, they go through rigorous machining processes that often leave micro-scratches or slight irregularities on the surface. Conventional abrasive methods struggle to address these fine imperfections. Polishing solutions, containing micro-abrasive particles like diamond or CBN, effectively tackle these issues, leaving the surface with a high gloss, uniform finish, reducing surface roughness, and achieving high-quality standards.
2.2. Enhancing Durability and Wear Resistance Through a Smooth Surface Layer
In industries requiring high mechanical durability, such as precision component manufacturing or mold making, surface imperfections like scratches or roughness can become weak points. These flaws may lead to cracking or breakage under dynamic forces. By minimizing stress concentration points on the surface, polishing solutions improve product durability, allowing them to withstand higher temperatures and prolonging their operational life.
2.3. Reducing Friction and Improving Heat Dissipation
Friction, a crucial factor in mechanics, impacts the lifespan and performance of components. By creating a smooth, even surface, polishing solutions lower the friction coefficient between contact surfaces. This results in quieter operation, stable operating temperatures, and is especially beneficial for high-load surfaces in engines, shafts, and bearings.
2.4. Precision Enhancement Through Controlled Material Removal
Active ingredients in polishing solutions, such as diamond or CBN powders, interact with the surface to oxidize and remove micro imperfections without compromising part precision. Polishing solutions control the rate of material removal, preventing excessive corrosion or unwanted abrasion, ensuring an accurate and refined finish suitable for high-precision applications.
3. Common Polishing Fluids and How to Choose the Right One
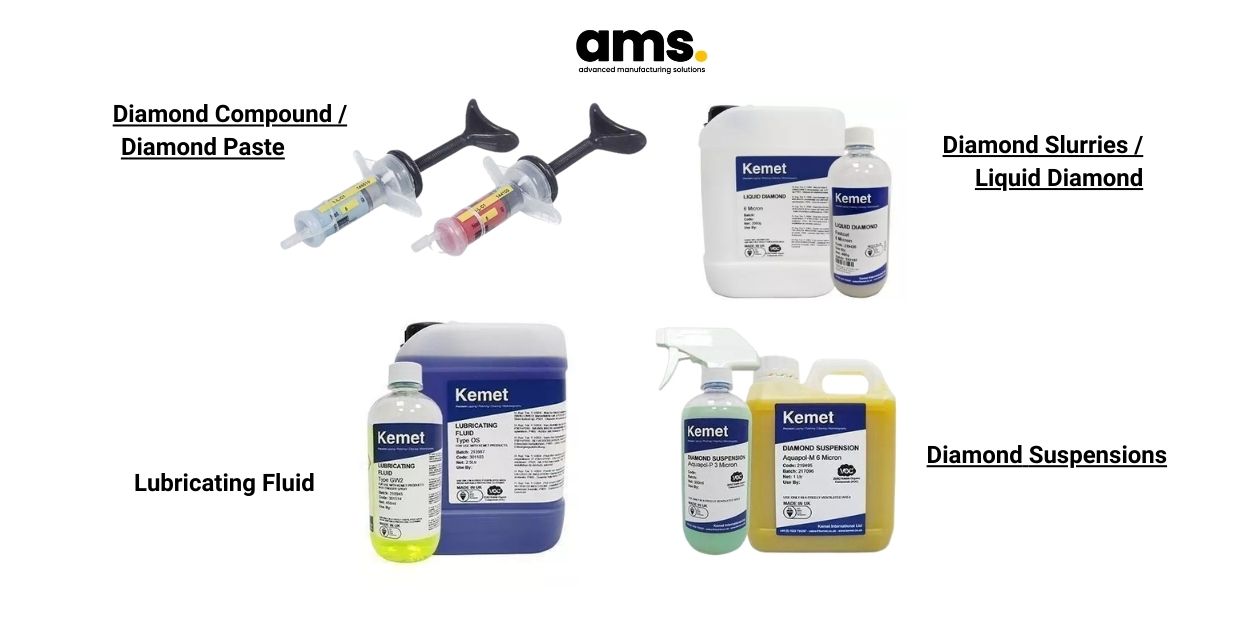
Depending on the application, the market today offers a wide variety of polishing solutions. To help businesses select the most suitable polishing fluid without worrying about substandard brands, we recommend exploring polishing solutions from Kemet, a trusted brand with over 85 years of experience providing polishing solutions for various industries.
Hard Metals (Stainless Steel, Alloys): The best option for hard materials is a diamond polishing solution, which has high hardness and creates a smooth, glossy finish. It can be optimized for both rough and fine polishing stages. Kemet's Kemet Diamond Suspension, available in different particle sizes (such as 1µm, 3µm, 6µm), is an ideal choice, or you might also consider the Kemet Type OS oil-based solution.
Soft Metals (Aluminum, Copper): For soft materials, a light abrasive polishing solution is the most suitable. Kemet's Colloidal Silica Suspension, which contains very fine diamond particles (about 0.05µm), is a great choice for soft materials. Alternatively, Kemet Type W, a water-based solution with light abrasiveness, is perfect for aluminum and copper components requiring high precision.
Non-Metallic Materials (Plastics, Ceramics, Glass): Specialized polishing solutions are required to achieve a high gloss without compromising the structure of non-metallic materials. Two excellent options for your polishing process are Kemet Type XP and Kemet Diamond Suspension (Water-Based), both suitable for sensitive materials.
4. Applications of Polishing Fluids in Various Industries
Polishing fluids are widely and diversely used across various industries, ranging from metalworking and electronics manufacturing to jewelry crafting. In addition to these areas, AMS aims to highlight other industrial sectors where polishing fluids are equally essential.
-
Die/Mold Industry: The surface requirements in this field are extremely stringent, as any imperfections can directly impact the quality and appearance of the final product.
-
Semiconductor Industry: This industry demands absolute flatness and smooth surfaces for semiconductor components and wafers. This is especially crucial in processes involving oxide film treatment and surface coatings, where any deviation in flatness can lead to production failures and costly disruptions.
-
Optics Industry: Surface quality is a critical factor, particularly for components like lenses, mirrors, and telescopes. Any defects or scratches on optical surfaces can lead to light scattering, reducing transparency and affecting optical performance.
Each industry uses different types of polishing fluids tailored to its specific needs. AMS is one of the leading technical experts in advising on the use of polishing fluids for various industrial applications. Contact us today — our team of consultants is always ready to assist you!
5. Tips for Achieving Optimal Results with Polishing Fluids
To achieve the best results when using polishing fluids, consider the following key factors:
-
Choose the Correct Concentration and Mixing Ratio: Adjust the fluid concentration to suit the material type and processing method, ensuring the polishing effectiveness is maximized.
-
Use the Right Polishing Equipment: Polishing fluids perform best when used with specialized polishing equipment, which ensures even and smooth surface finishing.
-
Proper Storage and Regular Fluid Replacement: Keep the polishing fluid in optimal condition by storing it correctly and replacing it as needed to maintain performance.
When using Kemet polishing fluids, you can be confident that your products will achieve excellent finishing while saving on maintenance costs and extending tool life.
>> See more: Supporting tools for the polishing process
6. Conclusion
AMS is honored to accompany you on your journey to finding the perfect polishing fluid for your company's needs. Beyond just fluids, AMS offers comprehensive polishing solutions tailored to a variety of requirements. Thank you, and we wish your business continued success and sustainable efficiency in production!
AMS Company, Ltd.243/9/10D To Hien Thanh, Ward 13, District 10
Hot line: 028.3868 3738/3903 - Fax: 028.3868 3797