The Definitive Role of HEIDENHAIN Rotary Encoders in Industrial Robotics Design
Industrial robots are known for their speed, strength, and resilience. However, they often struggle to provide precise position accuracy for certain tasks. This is particularly evident in tasks that demand both precise positioning and guided tool center point alongside substantial maneuverability. Such tasks require multiple axes, each requiring its own servo motors. Each servo motor introduces the potential for zero position error, backlash, and joint elasticities. Additionally, the machining process can impact the robot's mechanical rigidity, thus affecting accuracy.
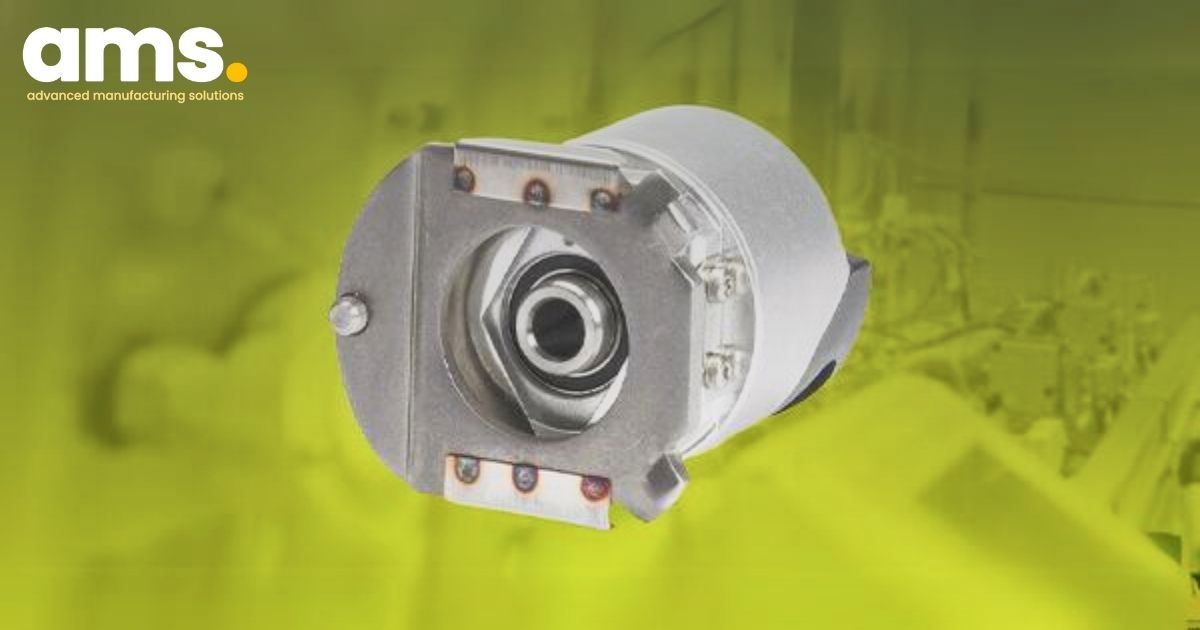
While advanced calibration methods exist and aid in repeatability, they fall short in providing absolute position accuracy, often being ten times less accurate. This limitation renders first-generation robots unsuitable for many applications, such as those within the aerospace industry. This is where encoders play a crucial role. HEIDENHAIN and AMO encoders, including the ECA 4000 angle encoder and the AMO WMRA, offer superior accuracy. In the realm of industrial robotics, rotary encoders often emerge as the most suitable option.
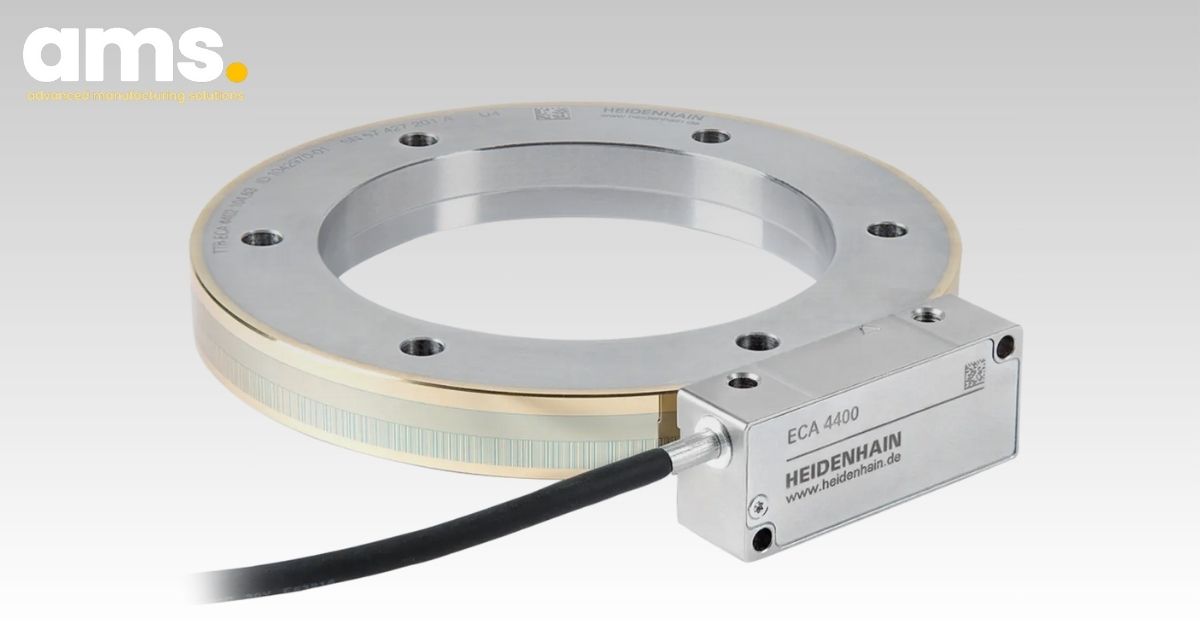
1. Benefits of Using Rotary Encoders for Robotic Applications
Encoders enhance the precision of industrial robots, enabling them to execute accurate machining and handling tasks on large components. Now, let's delve into the specifics of how this is achieved.

1.1. Position Sensing and Feedback
The more adept an encoder is at processing and transmitting feedback, the more precisely it can convey movement metrics and the true position of the robot's tool center point. However, this sensitivity comes with a downside: robust vibrations and electromagnetic interference can impact encoder performance. HEIDENHAIN inductive rotary encoders offer a solution to this issue. They are sturdy, resilient to intense vibrations, and their EnDat interface effectively withstands electromagnetic interference.
Furthermore, secondary rotary encoders, installed after each gear train, capture the actual position of a robot joint, guarding against zero position error and backlash, and measuring retroactive forces. The outcome is a considerable enhancement in absolute position accuracy, by 70 to 80 percent. Modular rotary encoders utilize scale drum or tape and separate scanning units, making them well-suited for the distinct challenges posed by hollow-shaft diameters and spatial constraints inherent in many robots.
1.2. Velocity and Acceleration Control
Rotary encoders facilitate precise monitoring of a robot's joint rotations, delivering high-quality velocity feedback. This real-time feedback enables operators to finely adjust acceleration, thereby gaining better control over the robot's movements. This precision ensures that the work remains accurate, repeatable, and efficient, ultimately leading to superior end products.
1.3. Multi-Axis Coordination
The interconnected nature of robot joints necessitates careful control of each axis to uphold precision and repeatability. The constant feedback facilitated by a rotary encoder is instrumental in maintaining this control across multiple axes, a crucial asset particularly in scenarios involving large components.
2. Common Types of Rotary Encoders Used in Robotics
2.1. Solid-Shaft Encoders
Shaft encoders track the speed and location of rotating shafts by linking a disc or wheel to the monitored shaft and detecting its position using a fixed sensor. As the disc passes the sensor, it produces electrical signals indicating the shaft's position and speed. There are absolute shaft encoders, which assign a distinct code to each shaft position, and incremental shaft encoders, which employ electronic pulses to gauge speed and direction.

2.2. Hollow-Shaft Encoders
Hollow-shaft encoders eliminate the need for separate couplings or adapters, leading to a smaller form factor and reduced system complexity. Their design incorporates a hollow bore or center opening, enabling the shaft to rotate within the encoder housing. This characteristic makes them particularly well-suited for use in robots, where space constraints are common. Additionally, the direct mounting of the encoder on the shaft eliminates slippage and backlash, rendering them a superior option for precise motion control.
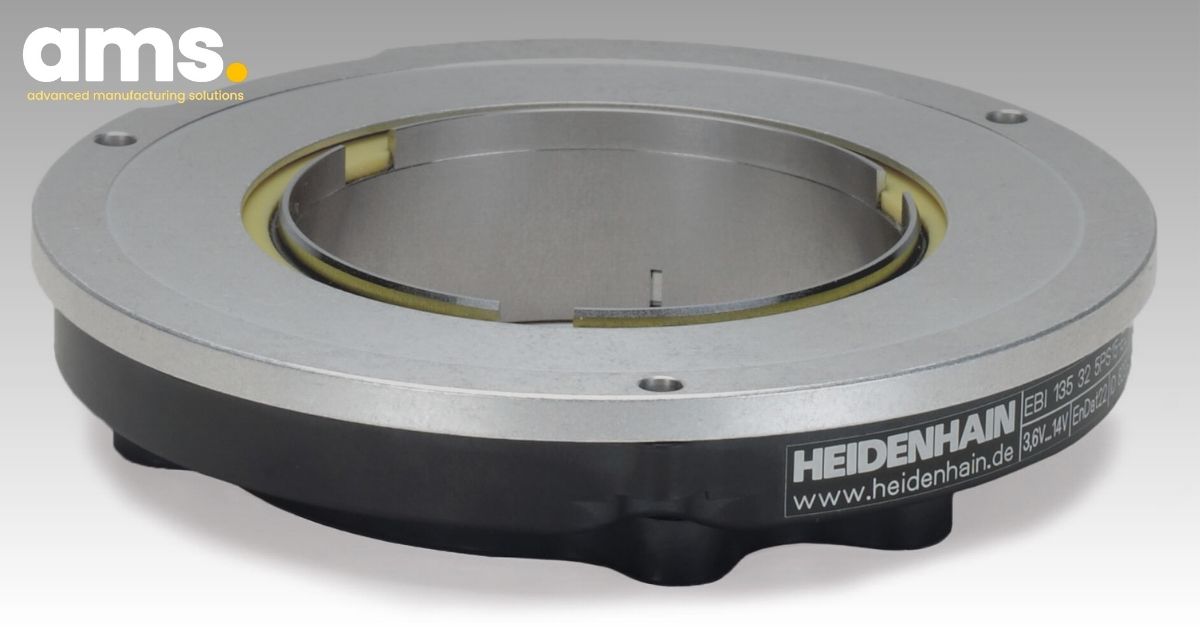
2.3. Dual Encoders
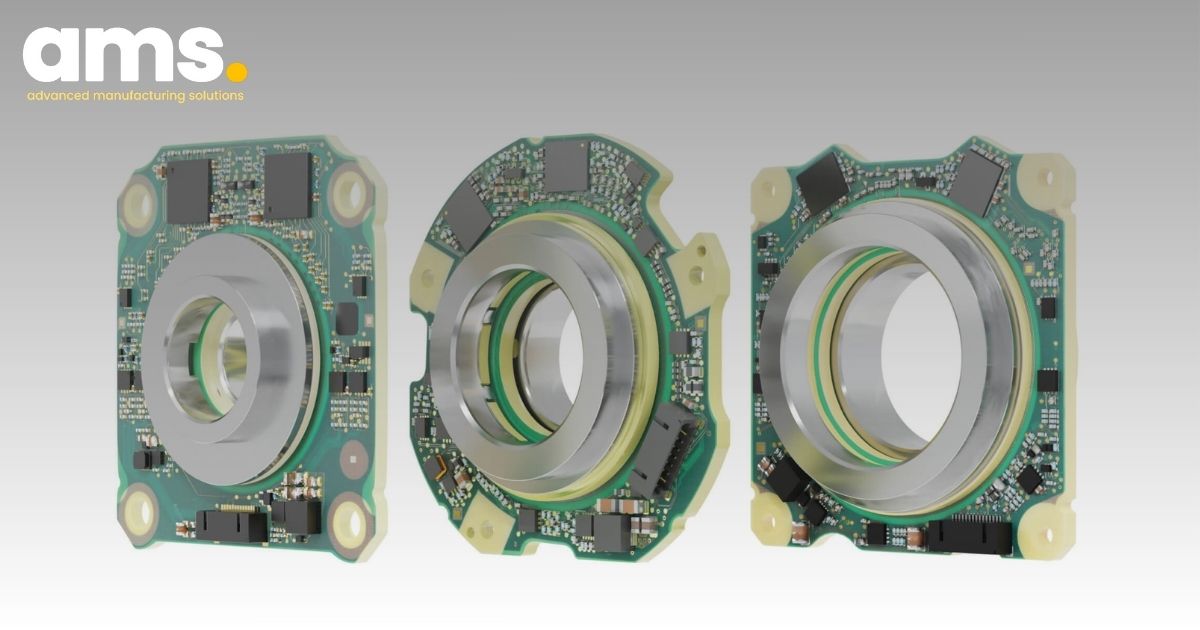
Dual encoders like HEIDENHAIN’s KCI 120 Dplus offer exceptional precision by concurrently assessing the rotational position and speed of a shared shaft. While one encoder determines the shaft’s absolute position, the other gauges its relative position or angular displacement. This simultaneous tracking of two distinct axes of rotation delivers enhanced feedback, consequently enabling finer positioning and speed control.
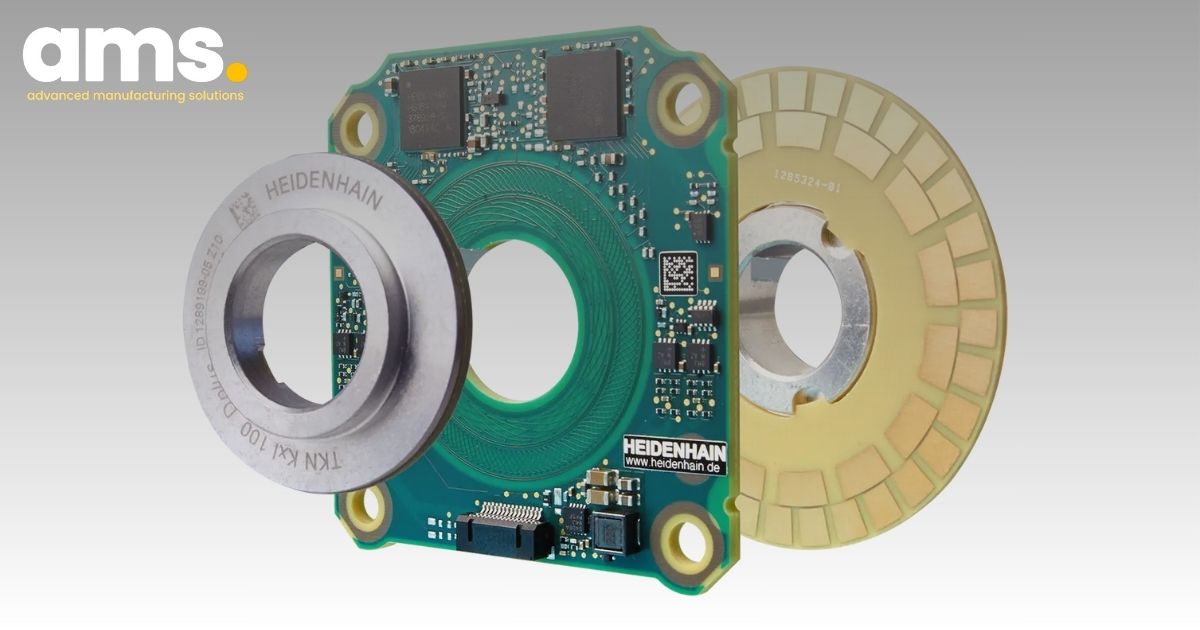
3. General Criteria for Robotics
When selecting an encoder, it's crucial to first consider certain overarching factors before delving into performance-related aspects:
3.1. Needs
What is the primary purpose of this robot? Whether it's assembling aircraft fuselages or executing precise cuts on large components, it's important to take into account the specific requirements of your robot when selecting an encoder.
3.2. Cost
Manufacturers need to carefully evaluate the initial cost of an encoder and determine if it will provide long-term value. Although an encoder may entail a higher upfront investment, it could lead to overall cost savings in the design process. Furthermore, high-cost encoders can provide robotics manufacturers with a competitive advantage due to enhanced functional safety, greater accuracy, and reduced long-term expenses.
3.3. Operating Environment
The operational environment of the robot is crucial in determining the necessary durability and optimal type of sensor. In addition to the forces and vibrations encountered during operation, factors such as dust, temperature, and humidity must be considered. Will the encoder require protective housing? If the vibration exceeds 30-40 Gs, a magnetic scanner may be necessary. Alternatively, a highly clean environment may favor the use of a more precise optical scanner. It's important to recognize that what suits one environment perfectly may not be suitable for another.
3.4. Footprint
Robots typically have restricted space, especially when a secondary encoder is required. What appears to be an ideal fit for a manufacturer's requirements might end up being too large, which is where rotary encoders like the KCI/KBI 1300 series, with their compact profiles and absence of bearing, can prove to be crucial.
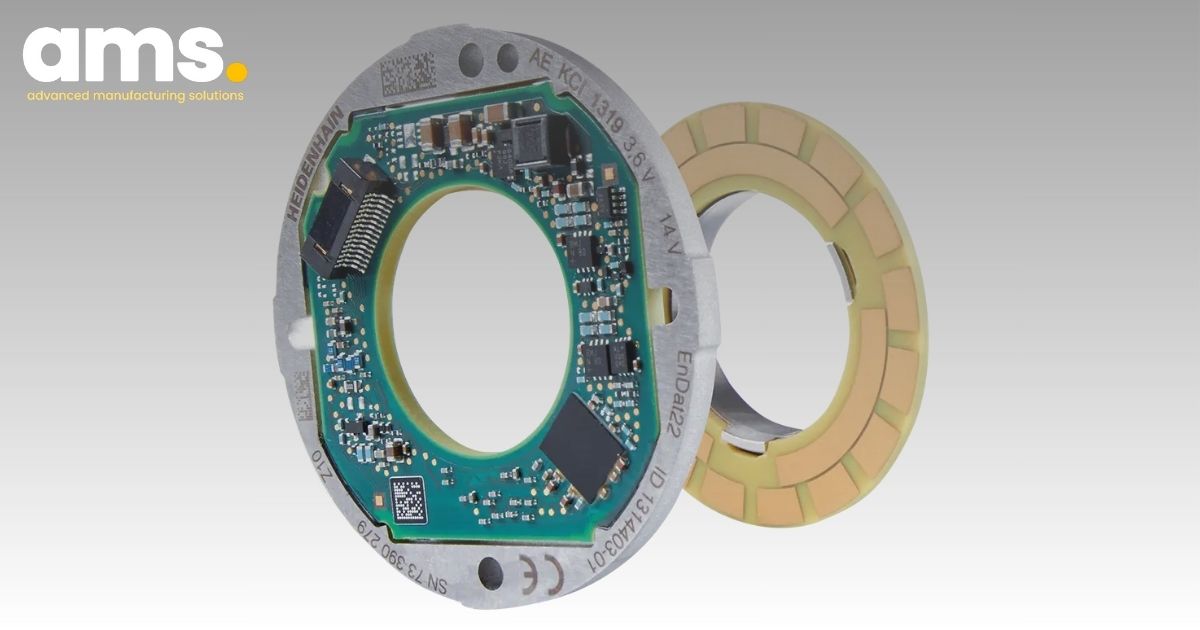
3.5. Flexibility
Furthermore, it's important to take into account the different iterations offered. Each component in a robot may introduce geometric limitations. Therefore, it's advantageous to utilize rotary encoders that are flexible enough to accommodate these restrictions or have customizable variations. Additionally, modular models or self-assembled kits could be considered. While these options may necessitate more expertise during setup, they can be highly advantageous in customizing a robot to exact specifications.
3.6. Assembly
About 70 percent of production expenses arise during the design phase, prior to the robot becoming operational. Modifying the design or processes after operations have begun incurs even greater costs. Therefore, encoders that are easy to mount can result in significant time and cost savings. A straightforward setup reduces the number of work steps and training hours required to construct and install each robot.
3.7. Safety
Regardless of the task at hand, it is crucial to minimize risk to human operators and robots. Seek out a dual encoder that is certified in compliance with Safety Integrity Levels (SIL) and Performance Levels (PL). Employing an interface like EnDat facilitates the simpler implementation of a comprehensive system, reducing design time and minimizing delays caused by errors.
4. Performance Characteristics to Consider
Once you move beyond the fundamental aspects, the physical mechanics and performance attributes of the encoder become significant considerations:
4.1. Quality Assurance
Quality assurance can often be a protracted procedure, but certain encoders can substantially expedite this process. Some encoders obviate the need for a calibration run and can begin operating immediately upon mounting—akin to "plug and play" functionality. There are bearingless encoders equipped with electronic mounting diagnostics that carry out immediate safety checks to verify correct installation.
Additionally, some models incorporate electronic ID labels accessible through the interface and have the capability to store their own data, facilitating automated setup.
4.2. Maintenance Posture
Manufacturers require machinery capable of providing extensive real-time data through a dependable interface. Every encoder should offer consistent, accurate measurements and supply comprehensive condition data, including error messages or warnings based on assessment values. This diagnostic information can then be analyzed to predict necessary maintenance or swiftly troubleshoot issues. For superior performance, consider utilizing an encoder equipped with the EnDat 3 interface, enabling faster data transfer, reducing cable requirements, and monitoring temperatures across various components, from the robot arm to the inside of the cabinet.

4.3. Wide Tolerances
Robotics inherently carry numerous risks such as zero point errors in joints, reversal errors in gearboxes, or load bearing issues stemming from material elasticity, collectively known as hysteresis. These factors can lead to significant complications during manufacturing, along with the influence of temperature fluctuations and aging components. A suitable encoder can effectively counteract these effects.
As automation and robotics continue to expand their presence across various industries, the choice of encoder can substantially elevate the quality of your robotics designs in the continuously evolving and increasingly demanding automation market. It's essential to thoroughly consider all available options and gain the expertise to select the most appropriate one. Your operators and your bottom line will undoubtedly benefit from this informed decision-making.
5. AMS Company Limited - Exclusive Distributor of HEIDENHAIN in Vietnam
AMS Company Limited proudly serves as the exclusive distributor of HEIDENHAIN products in Vietnam. Recognized as a premier provider of precision measurement and control equipment, HEIDENHAIN is esteemed for the excellence and dependability of its products. Collaboration with us grants access to a diverse array of HEIDENHAIN encoders suitable for various industrial applications.

Consult with AMS today for expert guidance in selecting the appropriate HEIDENHAIN encoder tailored to meet your specific business needs. Our team of experienced professionals is committed to comprehending your requirements and recommending optimal solutions to enhance your operational workflows. Whether your industry focus is automotive, aerospace, medical, or general manufacturing, we possess the proficiency to assist you in the selection of the perfect HEIDENHAIN encoder for your applications.
By procuring HEIDENHAIN products through AMS, you also benefit from HEIDENHAIN's comprehensive warranty and maintenance policy. This ensures that the products we provide are eligible for coverage under HEIDENHAIN's warranty, delivering added confidence concerning the longevity and performance of your investment. Conversely, products acquired from other sources may lack the assurance of coverage under HEIDENHAIN's warranty and maintenance policy. In the event of malfunctions or unforeseen issues, this disparity could result in additional expenses and disruptions to your operations.
Rely on AMS Company Limited as your exclusive partner in Vietnam to secure genuine HEIDENHAIN products bolstered by reliable warranty and maintenance support. Reach out to us today to explore our range of HEIDENHAIN encoders and benefit from the peace of mind that comes with collaborating with the region's foremost distributor.
AMS Company, Ltd.243/9/10D To Hien Thanh, Ward 13, District 10
Hot line: 028.3868 3738/3903 - Fax: 028.3868 3797