Suitable drill bit system: The secret to success in mechanical processing
Drilling technique, a method of creating round holes in a variety of materials, is being widely applied in many industrial fields such as manufacturing, mechanical engineering, construction, oil and gas, mineral exploitation and carpentry.
The drill bit cuts deep into the material, creating a thin layer (in the case of wood, metal) or a layer of dust (in the case of concrete), creating a hole after machining.
The process of drilling and creating holes in machinery products is a particularly popular process. However, selecting the right drilling tool is not always easy. This requires a drill suitable for each type of material, to ensure the drilled holes meet technical requirements and bring the highest economic efficiency. Each type of drill can deliver cost savings and efficiency depending on the specific circumstances. There is no single type of drill suitable for all situations.
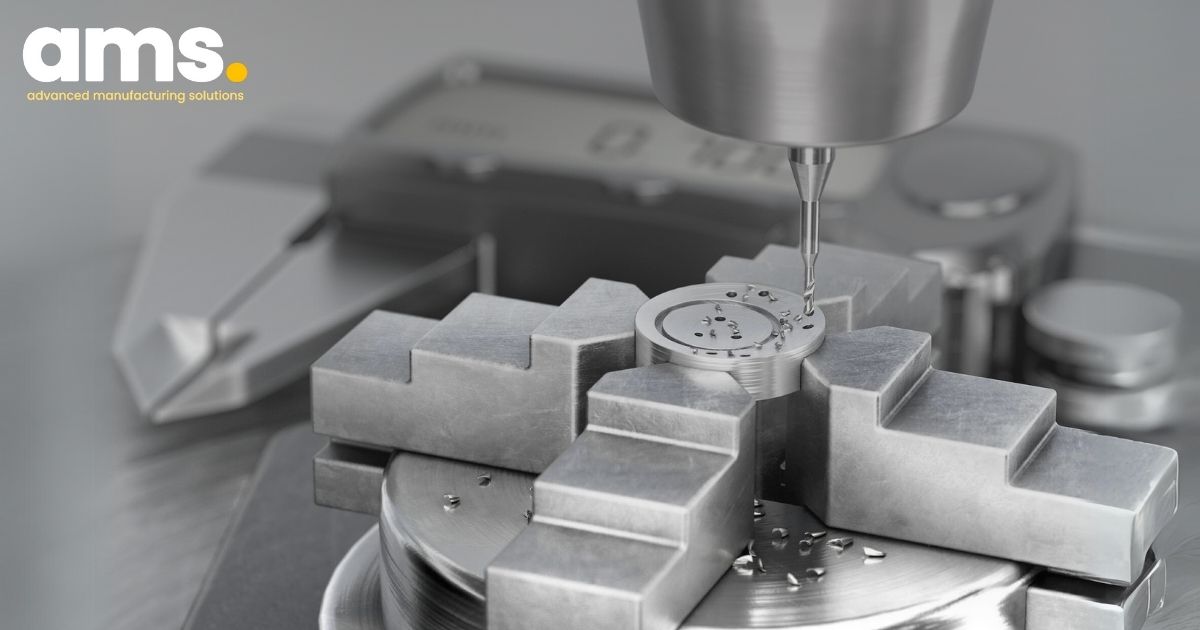
1. Classification of common drill bits and processing materials
There are two main types: monolithic drill bits, also known as solid drill, and piece-mounted drill bits, also known as indexable drill.
1.1 Monolithic drill bit
Monolithic drill bits are designed and manufactured from a single block of material from HSS or Carbide, with a choice of many different types of coatings to increase durability and extend the life of the tool.
There are a number of solid drill bit products from Sandvik Coromant that you may be interested in including:
-
CoroDrill 860: Solid drill bit designed to ensure high performance and precision during drilling.
-
CoroDrill 870: A reliable, optimized drilling technique option to enhance machining productivity and accuracy.
-
CoroDrill 880: Drill bit developed to meet the high requirements for surface quality and precision in industrial production.
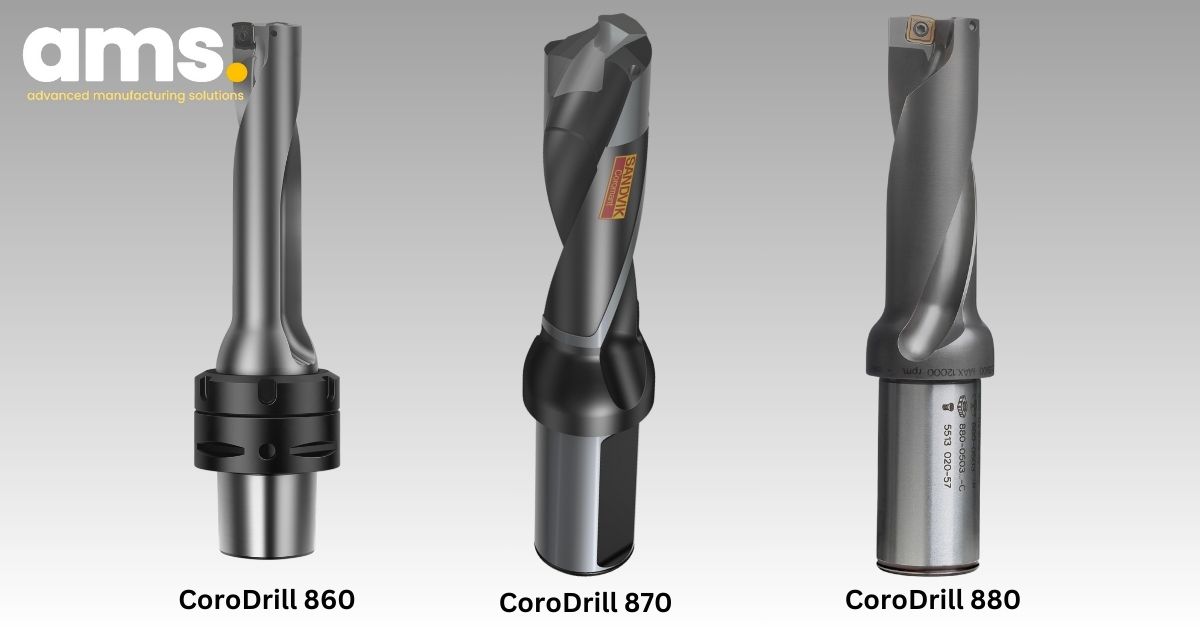
1.2 Piece-mounted drill bit
A piece-mounted drill bit is a type of drill bit structured with a tool shank and an assembled drill piece, similar to piece-mounted milling cutters or piece-mounted turning inserts.
Bit drill bit products from Sandvik Coromant that you may be interested in include:
-
CoroMill 419: Slim-mounted drill bit designed to optimize machining performance in deep, consistent drilling applications.
-
CoroDrill 434: The slim-mounted drill has been optimized to provide maximum performance and durability during acupuncture.
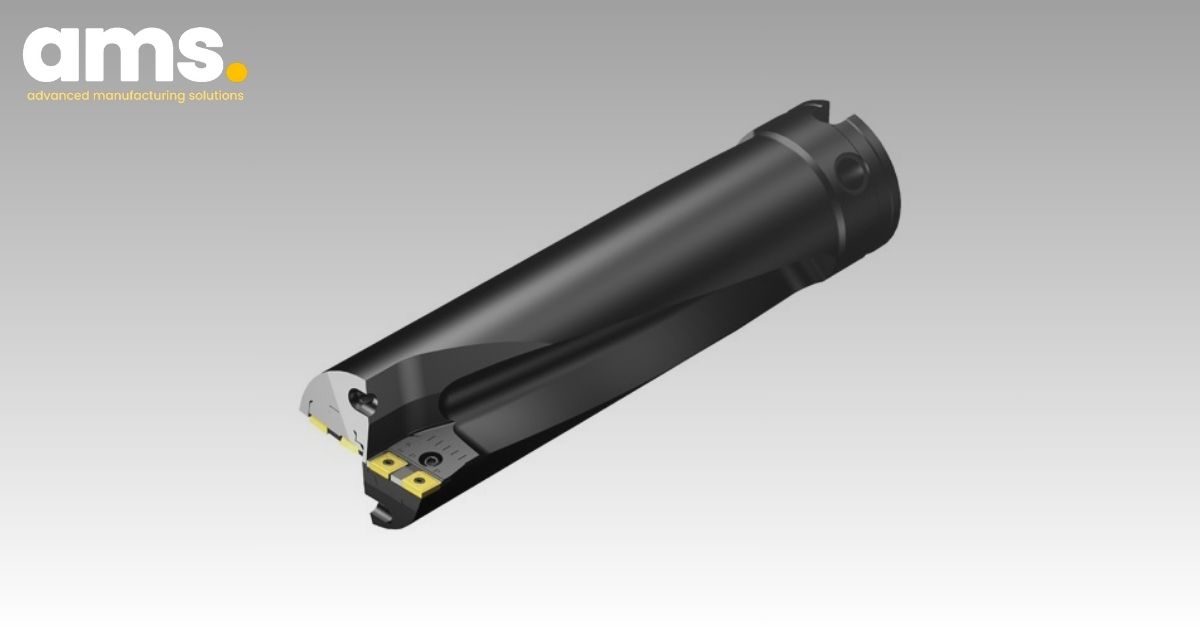
2. Issues to consider when choosing the right type of drill bit
2.1 Determine the machining period for the next drilling part in your contract
-
If your project involves the production of large diameters (8mm or more) in long-term or repeat orders, a practical option is to consider investing in insert drills (also known as indexable drills) which are capable of replacing cutting edges. These tools are specifically engineered to allow machine operators to swiftly replace cutting edges, thereby contributing to a reduction in the overall cost per hole. Despite the initial cost of the drill holder, the investment can be quickly recouped through decreased cycle time and lower drill insert replacement expenses compared to the use of solid carbide drills. The simplicity, variable speed, and reduced long-term production costs make replaceable insert drills the optimal choice for extended production tasks.
-
However, if your project involves a prototype or short-run order with small hole diameters (8mm or less), solid carbide drills may be a more suitable choice due to their lower initial cost. Typically, replaceable insert drills are not manufactured in small diameters.
-
Lastly, if the machining requirement primarily involves refining the hole surface, shallow hole depths, and small quantities in the experimental phase without specific cycle time constraints, a viable option would be high-speed steel drill bits (HSS Drills) which carry the lowest initial cost.
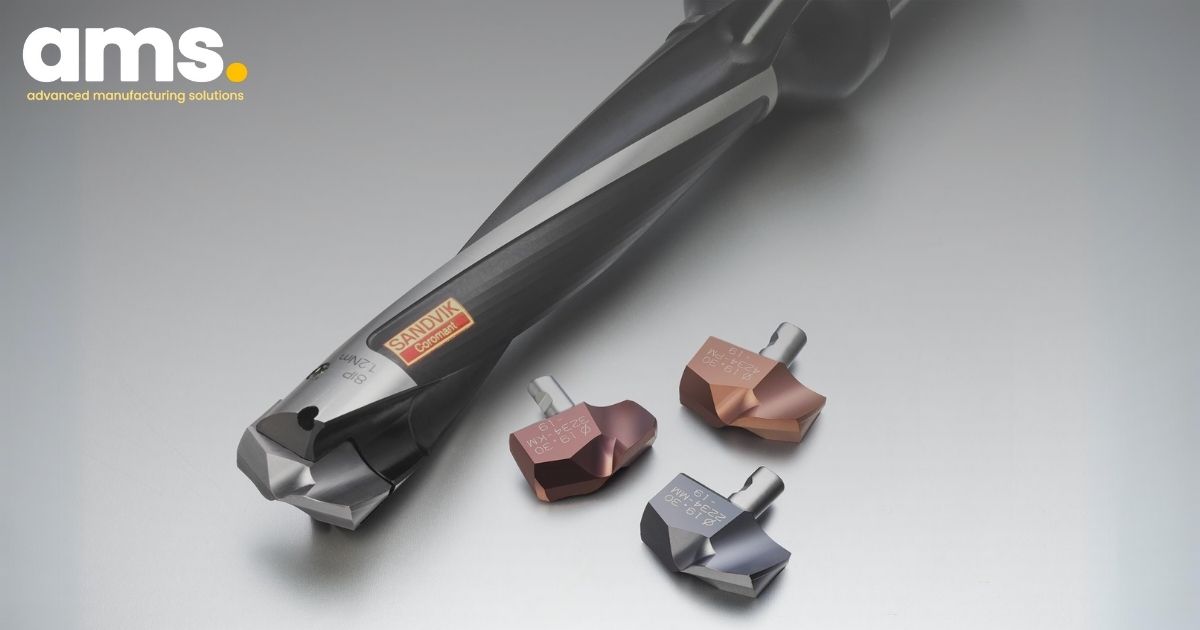
2.2 Consider the level of stability required for the drill bit
-
When comparing solid carbide drills to replacing a worn cutting edge with a new blade in insert drills, it's essential to factor in dimensional stability. Repeated sharpening of the cutting edge of solid carbide drills can result in shrinkage of the tool diameter and a decrease in length, causing it to deviate from the original size. Consequently, this may lead to insufficient length to complete drilling to the desired depth. In such cases, a drill bit with a small diameter and short length is only suitable for roughing. The process of re-grinding solid carbide drills adds an extra step to the production process, leading to an increased cost per hole.
-
On the other hand, using insert drills with the option to replace worn inserts with a new blade ensures stability in diameter and depth. The replacement procedure is swift and does not alter the drill length, preserving the original dimensions and tolerances.
-
As for high-speed steel drills (HSS drills), they are unsuitable for processing materials with high hardness, resulting in machined holes that lack straightness, large hole diameters, and high roughness. Their cutting edges wear out quickly, necessitating more frequent tool changes, particularly when used at very low machining speeds. Nevertheless, the primary advantage of high-speed steel drill bits lies in their durability and good impact resistance.
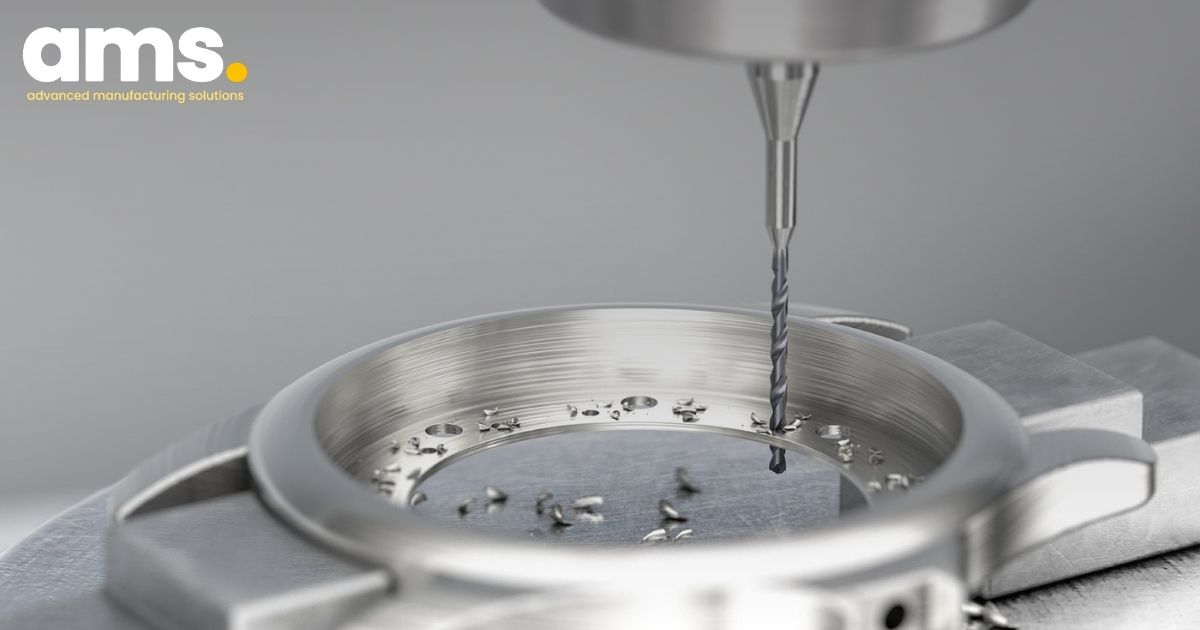
2.3 Take inventory needs into account when making your decision
-
Tool float refers to the overall number of tools needed in a production setting to prevent machine downtime. It's crucial to maintain a consistent inventory of tools to ensure continuous production. This involves ensuring an adequate supply of tools at each machine, having enough spares in the tool cabinet, and even having a reserve of tools ready for use.
-
Furthermore, tool inventory significantly contributes to the total production costs, making it essential to thoughtfully consider an inventory strategy for various types of drill bits.
2.4 The impact of performance on drill bit selection
-
During machine operation, it is widely recognized that solid carbide drills can operate at higher speeds compared to insert drills of the same diameter. The robust composition of solid carbide drills, owing to their absence of joints, enables them to resist damage over time. However, some machinists may opt for uncoated solid carbide drills to save time, eliminating the need for customers to wait for coated tools. Nonetheless, utilizing uncoated tools may decrease the cutting speeds and superior feed capabilities of coated solid carbide drills. In such cases, the performance gap between solid carbide drills and insert drills becomes insignificant, making the choice between these two types of drills dependent on specific circumstances.
-
In contrast, HSS drills typically operate at lower drilling speeds. To enhance their performance, some manufacturers have applied coatings to HSS drills to augment cutting speeds. While the coating has improved cutting speeds, there are still drawbacks such as a lack of enhanced cutting action and a less robust design, leading to vibration and hole warping during machining. Consequently, HSS drills do not meet the criteria for machining hard materials, resulting in lower performance compared to solid carbide drills and insert drills. It is crucial to carefully consider these factors when making your selection.
2.5 Calculate the overall cost per drilled hole in the drill selection process
-
Evaluating data on tool lifespan and production expenses plays a crucial role in determining the appropriate drill bit. Factors such as job size, initial tool cost, downtime for tool changes, time spent on tool resharpening and repairs, and the number of process steps all have a significant impact on production costs. For short orders, solid carbide drills pose as a practical option due to their lower initial costs.
-
Utilizing slim insert drills with replaceable cutting edges helps reduce the total cost of ownership during long-term contracts and high-production operations. This cost-saving approach is particularly beneficial when there's no need to purchase an entirely new tool, only the insert piece (also referred to as the blade) when necessary.
-
Furthermore, the time saved or utilized during cutting tool changes is another cost-saving variable. While the diameter and length of the drilled hole remain unaffected when insert drills are replaced, solid carbide drills necessitate replacement when worn out, and reinserting the tool also consumes time. Even though this timeframe may be minimal, it still impacts production efficiency.
-
Lastly, the number of steps in the hole making process also influences production costs. Insert drills can often accomplish the entire hole making process in a single step, saving time and costs. However, the process of resharpening drills can add to the costs and time required to complete the manufacturing process.
-
In conclusion, selecting the appropriate drill bit is not solely based on initial cost, but also requires consideration of total operating costs and long-term production efficiency.

3. Why Sandvik Coromant is the Ideal Partner for Precision Mechanical Applications
-
Sandvik Coromant stands out as a leading global provider of precision metal cutting and machining technology. Boasting over 150 years of expertise, the company has continuously invested in research and development, delivering top-notch, reliable products that cater to the worldwide precision engineering industry.
-
When choosing Sandvik Coromant as your drill bit supplier, you are choosing reliability and quality. Advanced technology and commitment to providing solutions that optimize productivity and costs make Sandvik Coromant a trusted partner in the precision engineering industry. At the same time, Sandvik Coromant also provides professional and dedicated technical support services, helping customers achieve success in metal production and processing.
-
With a solid reputation and reputation in the industry, Sandvik Coromant not only provides high-quality drill bit products, but also accompanies customers in improving productivity and efficiency in the production process.

As the official distributor of Sandvik Coromant products in Vietnam, AMS Company Limited brings over 20 years of experience in the precision mechanical industry. With a track record of supporting manufacturers in various sectors, including footwear, stationery, automotive, electronics, medical, dental, and more, AMS Company is well-equipped to offer tailored consultation and support for your manufacturing business, regardless of your product's industry.
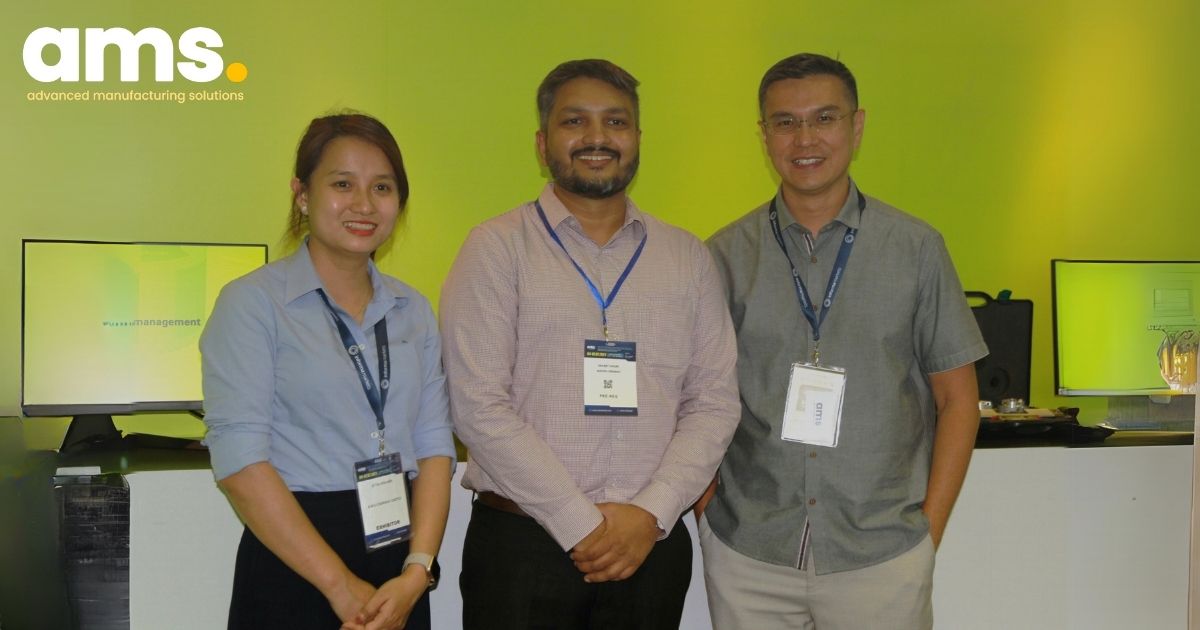
Reach out to AMS Company Limited today for complimentary consultation and dedicated support for your production requirements. Count on us to collaborate with you in optimizing the manufacturing and precision mechanical processing process.
AMS Company, Ltd.243/9/10D To Hien Thanh, Ward 13, District 10
Hot line: 028.3868 3738/3903 - Fax: 028.3868 3797