Mastering Workpieces and Chips in Manufacturing and Machining: A Comprehensive Overview
The metal machining process is crucial in producing metal components with precise dimensions and surface finishes. Key machining techniques include turning, planing, drilling, milling, and grinding, each requiring the use of cutting tools such as lathes, drills, milling cutters, and grinding bits on metal cutting machines.
Furthermore, comprehending the distinction between "workpiece" and "chip" is pivotal in the manufacturing process. Primarily, the workpiece is typically regarded as the initial material, while the chips refer to the final machined product. A deeper insight into the application and benefits of each type in metal fabrication will clarify the nuanced differences between these concepts.

1. The Science Behind Efficient Chip Manufacturing for Industrial Use
1.1. What are Chips?
In mechanical engineering, the term "chip" denotes a thin segment of material that is extracted or detached from a workpiece during machining, typically utilizing cutting techniques. A chip generally comprises a portion of the metal layer that undergoes deformation and separation from the primary component. This deformation can vary based on cutting parameters, the workpiece material, and additional influencing factors.

1.2. Understanding the Process of Chip Formation and Its Impact on Machined Products
In the process of machining, a non-continuous amount of material, referred to as chips, is removed to shape and refine a part according to specific technical requirements. Research has indicated that the cutting process is a result of material particles sliding under the influence of force exerted by cutting tools.
When subjected to cutting force, the metal layer in front of the tool is compressed, then separated and compelled to rise along the tool's edge. If the tool's pressure on the material surpasses the bond force between the material particles, the compressed chip will slide along the surface and the cutting process will continue.
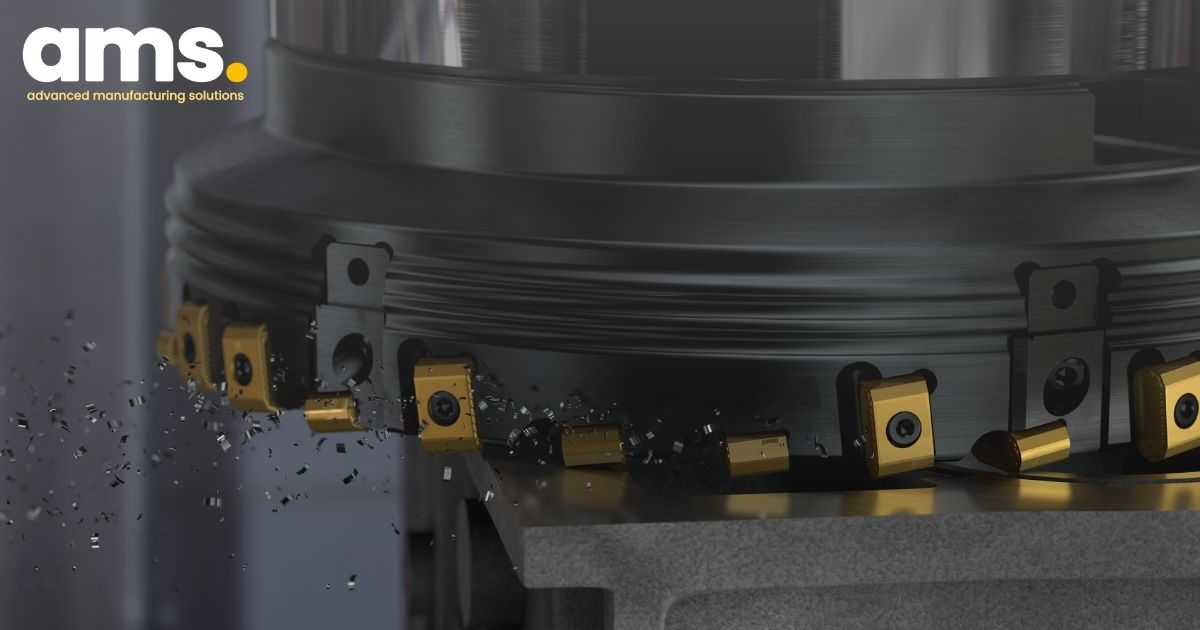
The material particles slide along the surface, forming an angle of approximately 30-40 degrees in relation to the workpiece surface. As this reduction in thickness occurs, the crystals within each material particle also undergo displacement at an angle of approximately 60-65 degrees.
Consequently, the cutting process not only induces elastic and plastic deformation in the material particles but also leads to a continual sliding of the chips.
1.3. Categorization of Chip Varieties
Based on the material's mechanical properties, which encompass its elastic and plastic deformation characteristics, various chip types are generated during the cutting process. These commonly observed chip types include discontinuous chips, continuous chips, and continuous with built-up edge chips
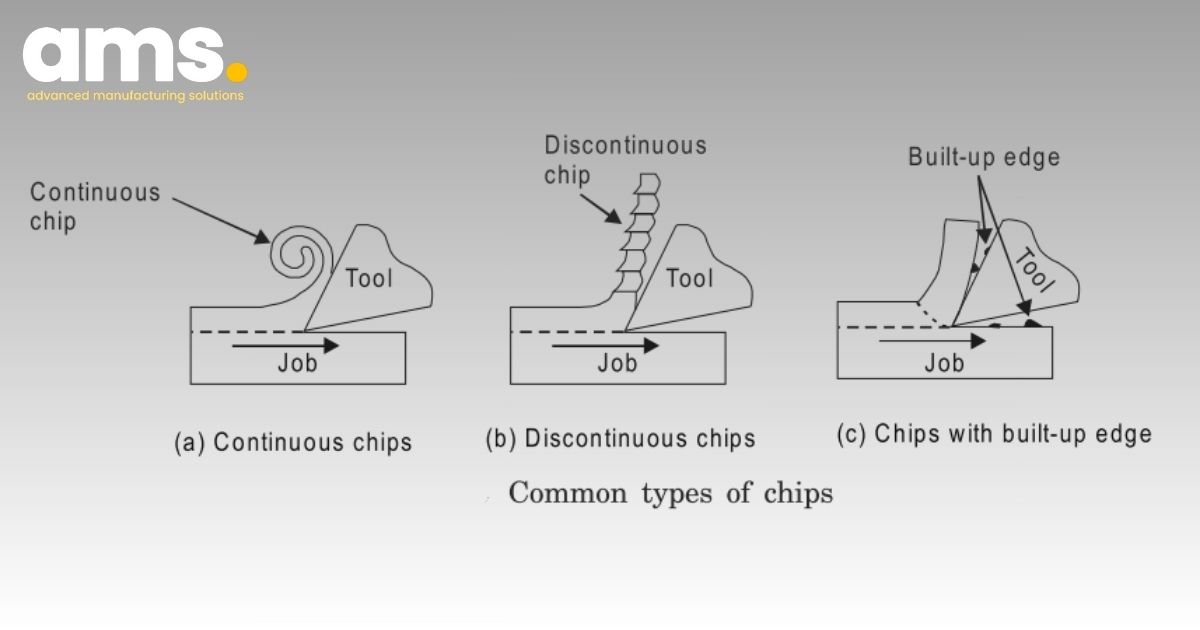
1.3.1. Discontinuous chip
When machining hard and brittle materials like cast iron, brass, stone, ceramics, and Ebonite, discontinuous chips are produced. These chips consist of distinct material pieces of varying shapes, with constituent particles that are loosely or weakly bonded together.
1.3.2. Continuous with built-up edge Chips
Continuous with built-up edge chips are generated when machining materials with consistent hardness, low ductility, and moderate cutting speeds. The chip's surface slides smoothly along the tool's edge, while the opposite side appears jagged and rough. The material particles in this type of chip are relatively firmly connected.
1.3.3. Continuous Chips
These chips form when machining materials with high ductility and low hardness using high cutting speeds. They emerge from the tool as long strings with a relatively smooth surface and minimal roughness.
It's important to note that chip types are not fixed based on material alone but can vary based on the cutting conditions. For instance, slight adjustments in depth of cut and higher cutting speeds can alter chip shapes.
Assessing chip shape provides crucial insights for determining cutting modes and the cutter's geometric parameters.
2. Understanding Workpieces and the Machining Process
2.1. What is a Workpiece?
In mechanical processing, workpieces are crucial as they serve as the foundational material for creating products based on predetermined size and design specifications outlined by the customer. The workpiece not only serves as essential raw material but also plays a pivotal role in determining the quality and characteristics of the final mechanical product.
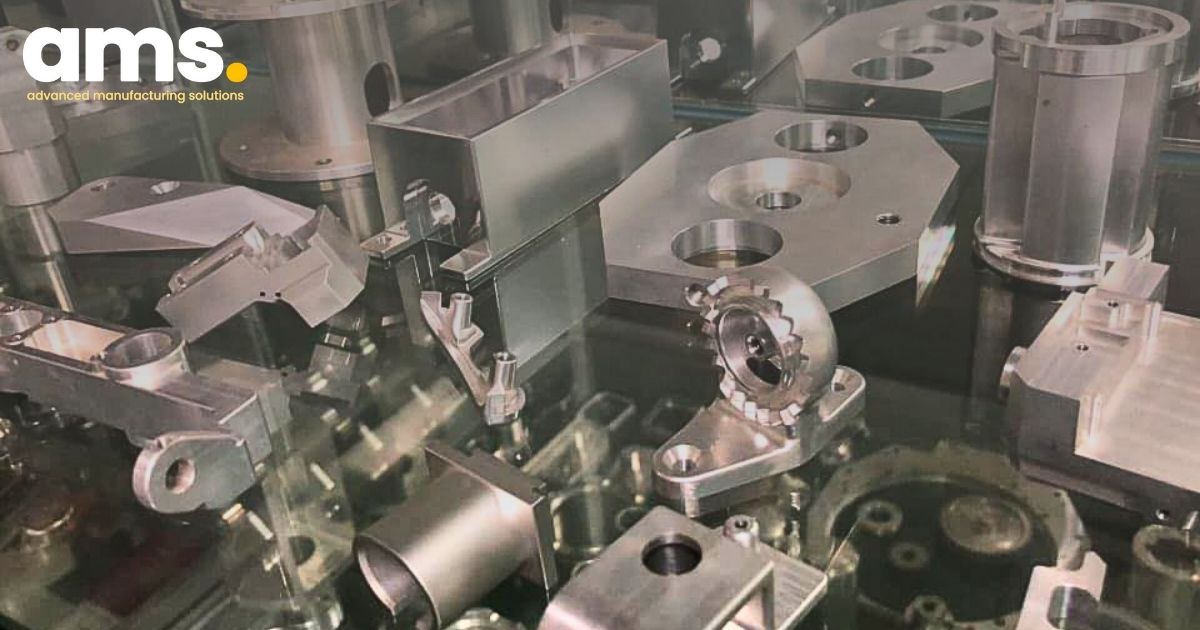
2.2. Selecting Workpiece Materials for the Machining Process
When developing a manufacturing process for a mechanical component, the choice of workpiece material and its type, along with determining the workpiece's size, holds significant importance. The size of the workpiece is determined by calculating the remaining material after the machining process, while the workpiece type is based on the technical and functional requirements of the part.
The selection of blanks must adhere to economic and technical criteria, considering cost, manufacturing feasibility, simplifying the technological process, and achieving cost-effectiveness while meeting technical demands.
This process involves determining the necessary materials, shape, technological structure, production process, workpiece manufacturing method, and the method's accuracy.
Moreover, selecting the appropriate workpiece type based on the factory's working conditions is crucial. Choosing an unsuitable workpiece type for the factory conditions can lead to economic loss and wasted time.
2.3. Overview of Workpiece Manufacturing and Processing Technologies
Mechanical processing entails harnessing the power of machines and the specialized skills of mechanics to carry out cutting, turning, milling, grinding, and planning operations.
Notably, precision mechanical processing methods are increasingly employed using automatic CNC machines, delivering near-perfect accuracy and ensuring sophistication and high aesthetics for every product detail.
The diversity and flexibility of mechanical processing methods vary depending on the type of machinery utilized. Among the popular mechanical processing methods are:
-
Mechanical lathe processing
-
Milling mechanical processing
-
Machining mechanical planning
-
Mechanical grinding processing
-
Final finishing
2.4. Common Workpiece Manufacturing and Machining Methods in Today's Industry
Various manufacturing methods are employed to transform a workpiece into a finished product. The following are some prevalent techniques utilized in the current manufacturing industry.

2.4.1. Casting Technique
In the casting process, workpieces are created by pouring molten metal into a mold and allowing it to solidify, forming details with the desired shape and size.
This casting technique enables the production of parts from a range of metals and alloys with varied compositions. It is particularly well-suited for creating parts with complex shapes and moderate loads. Moreover, this method facilitates the production of parts ranging from a few tens of grams to several tens of tons.
Due to its cost-effectiveness in producing billets, this casting method is increasingly popular in the industry.
2.4.2. Pressure Machining Technique
The pressure machining technology involves using external force to alter the metal in a crystal lattice state, according to specific directions, to produce details with various sizes and shapes as needed.
Throughout this process, the mass and chemical composition of the material remain unchanged when applying machining pressure, while enhancing the material's mechanical properties. The outcomes encompass precise sizing, shape, and surface quality of the workpiece, leading to time savings compared to cutting processes and minimizing material wastage.
Additionally, this method fosters high productivity by streamlining steps in the technological process and facilitating mechanization and automation.
2.4.3. Forging Technique
Forging, a popular hot metal processing method, presents numerous notable advantages. This method provides high flexibility and is applicable across a wide range of applications. Forged materials demonstrate the ability to withstand heavy loads and offer cost savings due to the use of simple equipment. In comparison to the casting method, forged billets commonly exhibit superior mechanical properties and are well-suited for mass production, leading to time savings and enhanced productivity.
2.4.4. Lathe Machining
The turning machining method, a workpiece cutting and shaping technology, utilizes the rotational motion of the workpiece in conjunction with the forward movement of the blade. This process involves both vertical and horizontal movement of the workpiece and blade to execute the cutting and shaping of the workpiece. The lathe mechanical processing method is suitable for manufacturing machine parts, screws, bolts, and other precision mechanical products.
2.4.5. Milling Machining
Milling machining employs milling cutters with multiple cutting edges, utilizing circular motions combined with tool movement in vertical, horizontal, and lateral directions to cut and shape the workpiece. This method is frequently applied in the production of transmissions, gearbox covers, aluminum disc covers, and other components for the automotive industry. Additionally, it is utilized in the manufacturing of gears and supporting parts for industrial machinery.
2.4.6. Planing Machining
Planing machining entails creating a flat, smooth surface on a material, typically achieved through precise movement between the cutting tool and the workpiece. Presently, planing machining commonly employs two primary methods: rough machining and finishing machining, suitable for manufacturing parts with narrow width but considerable length, such as V-grooves and similar structures.
2.4.7. Grinding Processing
Grinding machining involves manufacturing metal by utilizing grinding stones to abrade and generate a smooth, glossy surface on the workpiece. This method enhances the workpiece's surface smoothness and shine, making it suitable for creating sleek and lustrous surfaces for parts requiring specific thinness, a challenge for other machining methods.
2.4.8. Drilling, Boring, Tapping
The drilling-boring-boring-tapping processing method plays a vital role in creating holes in metal workpieces. Machinists customize the methods used, including drilling, boring, and tapping, based on the specific characteristics of the workpiece. This technology finds widespread application in manufacturing racks, pinions, gear shafts, gearboxes, and various other mechanical products.
2.4.9. Broaching Machining
Broaching technology not only creates holes in materials but can also produce round holes, shaped holes, straight holes, keyholes, or even spiral grooves. Sometimes, the movement of the broaching tool is precisely adjusted statically to ensure the precision and accuracy of the machining process, exemplifying the versatility and diversity of this method in creating holes in materials.
2.4.10. Final Finishing
The final refining stage encompasses methods such as grinding, honing, super-fine grinding, polishing, and scraping, representing a critical and indispensable process in manufacturing mechanically processed products. Through this stage, the product attains the highest level of perfection, achieving sophistication and optimal quality.
3. Introducing Sandvik Coromant: Elevating Manufacturing Excellence
Sandvik Coromant, a renowned leader in cutting tool solutions, plays a pivotal role in enhancing manufacturing processes worldwide. With a rich history of groundbreaking innovations, Sandvik Coromant continues to revolutionize the industry by providing cutting-edge tools and expertise to optimize chip and workpiece manufacturing. Their extensive range of products includes indexable inserts, drills, milling cutters, and tool holders, designed to deliver precision and efficiency in metalworking and machining operations.
Sandvik Coromant's product line meets a broad spectrum of manufacturing needs. For instance, their milling cutters, such as the CoroMill® 390, are adept at producing high-quality surfaces and complex 3D shapes, essential for workpiece manufacturing. Additionally, their range of drills, including the CoroDrill® 860, stands out in delivering precision and productivity, addressing diverse hole-making requirements in chip manufacturing. These examples underscore the diverse and high-quality solutions that Sandvik Coromant offers, catering to a wide array of manufacturing applications.

AMS Company Limited, the distinguished distributor of Sandvik Coromant in Vietnam for over 20 years, has consistently provided top-tier cutting tools and solutions to meet the diverse needs of the manufacturing sector. As a valued partner, AMS offers unparalleled expertise and support to industries seeking to elevate their production processes. Contact AMS today to benefit from their comprehensive knowledge and experience in Sandvik Coromant products, ensuring that you are equipped with the best solutions for your manufacturing requirements.
AMS Company, Ltd.243/9/10D To Hien Thanh, Ward 13, District 10
Hot line: 028.3868 3738/3903 - Fax: 028.3868 3797