Turning in Machining: 3 common types of turning machining you must know
Turning is a very popular mechanical processing method, but not everyone clearly understands this method. During the machining process, many people encounter common problems and errors such as not knowing how to fix it, tools breaking when turning quickly, or turning products that do not meet the desired quality. However, to avoid these problems, in-depth knowledge and skills in turning methods are required.

1. What is turning?
Turning is the method of producing cylindrical and circular forms using a single cutting tool with a single cutting edge. During this process, the turning tool stays still while the workpiece is rotated.
The turning process helps create arbitrary shapes and sizes of manufactured parts, playing an important role in the production of electronic devices, machinery and household appliances.
Turning can be divided into several basic applications: longitudinal turning, facing turning and profile turning. For each application, it is necessary to use the appropriate tool type, cutting mode and programming to achieve the highest efficiency.
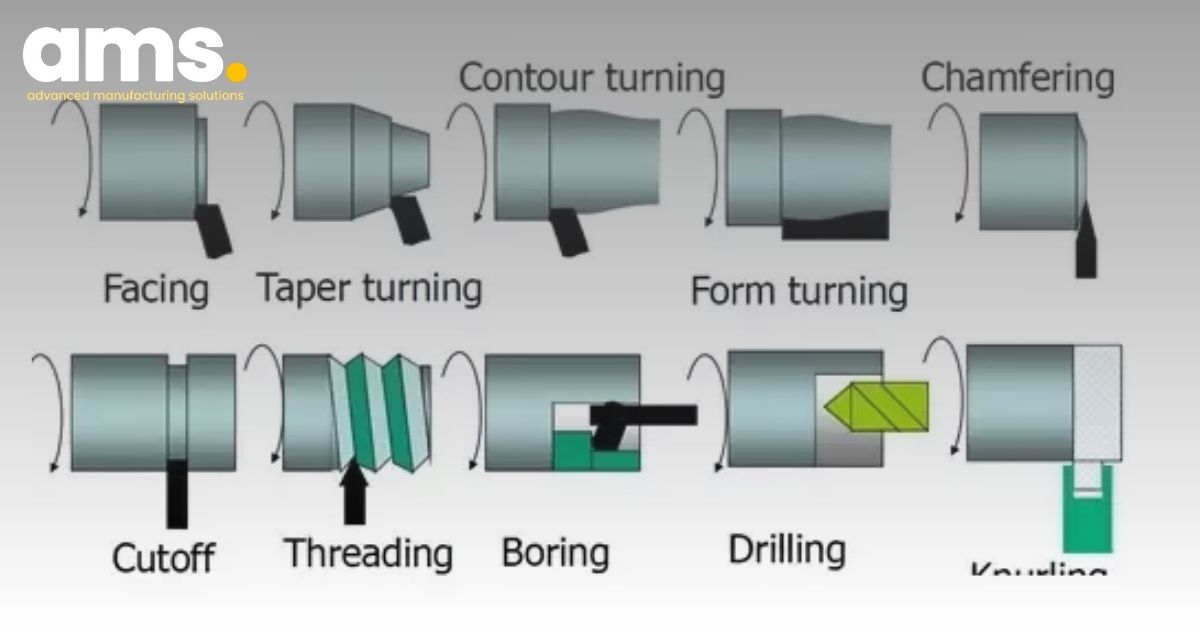
2. Characteristics of turning method
Turning is the most popular cutting and machining method, accounting for about 25% - 35% of products in the cutting and machining process in workshops.
Turning is usually performed on lathes such as: universal screw lathe, vertical lathe, truncated lathe, RW lathe, automatic lathe, CNC lathe... However, turning can also be performed on other types of machines such as drilling, milling, boring, etc.
The cutting tool used to perform turning is called a turning tool. There are many types of tools, from external turning tools, straight tips, hole turning tools, shaped turning tools to various types of turning tool pieces and turning tool handles.
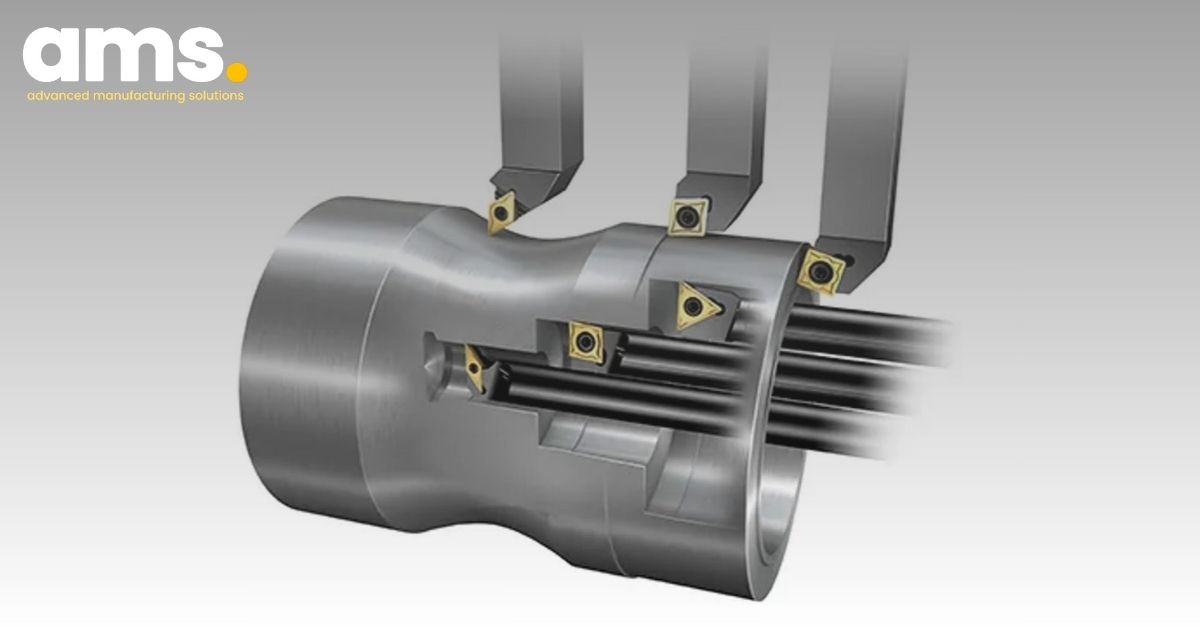
3. Common types of turning
Finish turning, rough turning and semi-finishing methods are commonly used methods in turning machining because they provide good performance and produce accurate machine part shapes and surfaces.
3.1 Rough turning
In the turning process, the first step that needs to be performed is destructive machining. The purpose of destructive machining is to eliminate external defects of the workpiece such as pitting, sand adhesion, hardening and excessive deviations.

To perform rough turning on the exterior, cutting methods can be used layer by layer, section by section, or a combination of both methods.
- Cutting in layers allows for high precision but low productivity due to the large total travel distance of the knife.
- Cut in sections, using multiple cuts per section to ensure the residual amount and cutting force are not too large, but the hardness and stability are low.
Thus, combining the above two methods (coordinated cutting) will be able to solve the disadvantages of each method, ensuring high accuracy and good productivity.
Besides, for rough turning, CNC machines need to have high rigidity and large capacity to achieve high productivity. However, the accuracy does not need to be too high. In cases where the workload is small, demolition work can be assigned to old machines in the workshop.
To achieve high efficiency in rough turning, choosing the right type of turning tool is extremely important and requires attention and caution on the part of the machinist. In this article, AMS would like to introduce some rough turning tools from Sandvik Coromant that you can consider:
- CoroTurn 107: This is a tangentiál turning tool designed for quick and efficient turning of a variety of materials.
- CoroTurn 200: This turning tool is used for machining carbon steel and alloy steel materials. It has a flexible design and is suitable for many machining applications.
- CoroTurn Prime: This is an advanced turning tool line, optimized to achieve the highest turning speed and long tool life. It helps reduce machining time and provides good surface quality.
- CoroTurn XS: This is a compact turning tool, used for machining small or hard-to-reach parts. It ensures high precision during machining.
Sandvik Coromant is one of the best options when it comes to turning tools available on the market. With its quality and product variety, this company is worth considering and testing in your rough turning process. To choose the right turning tool, please research carefully or contact AMS for detailed advice.
3.2 Semi-finish turning
Semi-finishing turning is an important step in the turning process, performed before using the finishing turning method.
The purpose of semi-finishing turning is to remove rough edges on the surface of the part (cutting depth is about 2-4mm) to prepare for later finishing turning. To perform semi-finishing turning, it is necessary to choose the cutting depth so as not to affect the quality and accuracy of each machined part.
However, you should not choose a cutting depth that is too small to avoid over-slip and vibration during machining. To achieve best performance, alloy steel knives should be used at moderate speeds. Choosing the right turning tool not only affects the quality of the final product, but also has a significant impact on the performance and productivity of the machining process.
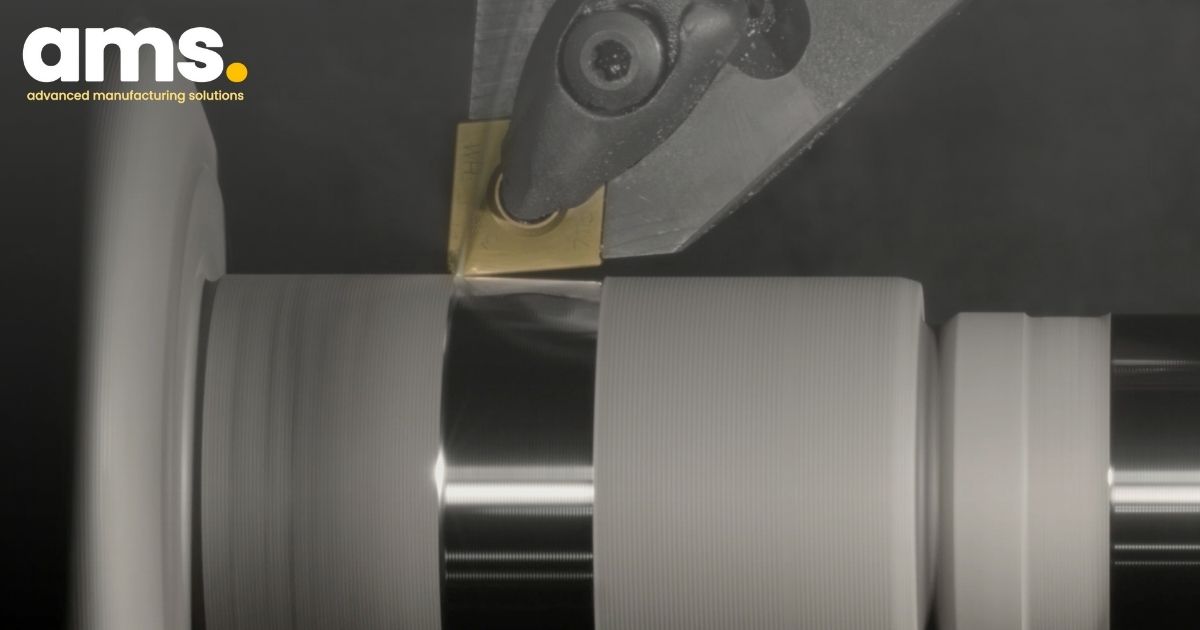
During the semi-finishing turning process, choosing the right turning tool can be affected by many important factors. First, the quality and hardness of the turning tool need to match the type of material being turned. Different materials require turning tools with corresponding hardness and sharpness to ensure good grinding.
Second, the design of the turning tool is also important to meet each specific machining requirement. Characteristics such as tooltip shape, cutting angle, bounce pattern, and turning direction can influence cutting properties, producing accurate dimensions and smooth surfaces.
Here are suggestions for 4 other turning tool lines from Sandvik Coromant for the semi-finishing turning process:
- CoroTurn 300: This turning tool is designed for precision machining on materials such as stainless steel and cast iron.
- CoroTurn Prime A: This series of turning tools is especially suitable for semi-finishing turning on aluminum and other lightweight materials.
- CoroTurn XS U: This compact turning tool is optimized for machining small, hard-to-reach parts in materials such as hardened steel and alloys.
- CoroTurn TR: This line of turning tools is designed for threading on various materials, helping to create precise threads and smooth surfaces.
3.3 Finish turning
To have a shiny surface, we can use thin turning with an alloy knife or diamond knife. You should be extra careful in this stage because grinding of the blade is important to ensure straightness and a smooth surface.
The cutting mode when finishing thin turning has a small feed rate and depth of cut, while the cutting speed is quite high. For example, when machining aluminum alloys, the cutting speed usually ranges from 1000 to 1500m/min; copper alloy, knife V=300 to 450m/min; and other metals, the knife V=200 to 250m/min.
For non-ferrous metals, thin grinding is the best choice. The special thing about this material is that it cannot be sharpened, because the area of grinding chips adheres tightly to the working surface of the grinding wheel.
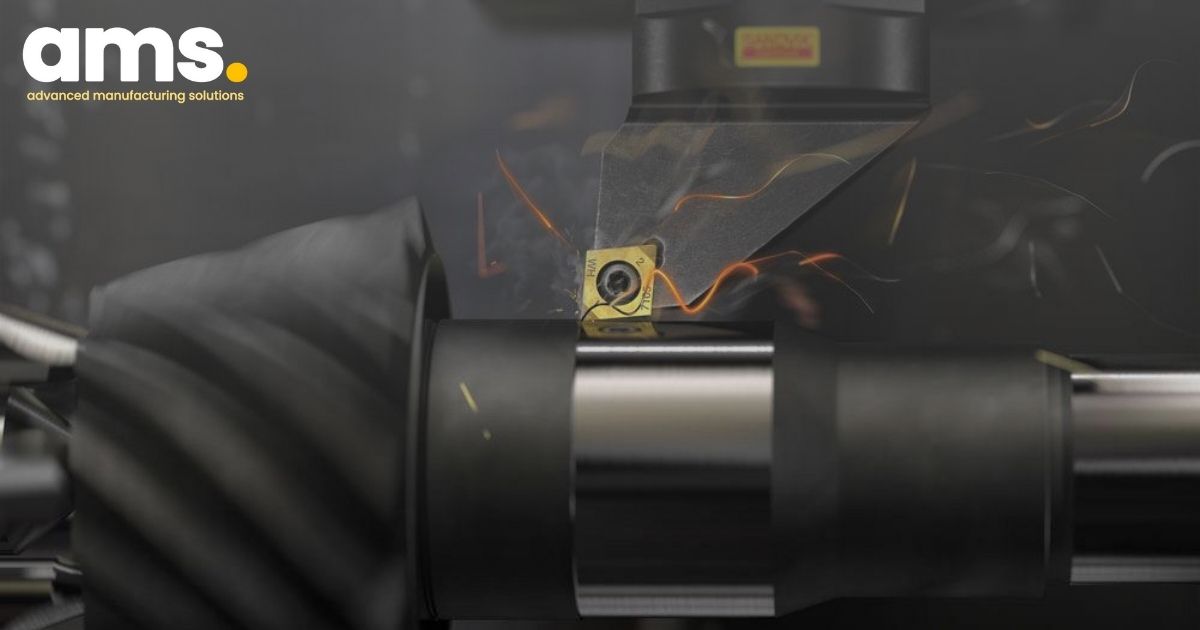
In short, the finishing method with an alloy knife or diamond knife is the best choice for machining non-ferrous metals and achieving a shiny and smooth surface.
Some turning tool products for finish turning you should consider include:
- CoroTurn® 107: This turning tool line is renowned for its excellent performance in finishing turning. Helps provide high precision and good surface finish, suitable for a variety of materials.
- CoroTurn® HP: This tool line is designed for high precision turning applications. They provide good chip control and high tool life, helping to improve productivity and component quality.
- CoroTurn® Prime: This series of turning tools is specially developed for fine-tuning machining processes on various materials. Features a unique design that reduces cutting forces and increases tool life, helping to increase productivity and surface finish.
- CoroTurn® XS: This line of cutting tools is designed for small parts machining, including fine-tuning operations. Helps provide high precision and stability, suitable for complex parts and high precision requirements.
- CoroTurn® SL: The SL turning tool series features tool tips and tool holders specifically designed for fine-tuning operations. They provide good surface finish and high precision.
4. Turning capabilities and technology
4.1 Shaping ability
Turning can process many different types of circular surfaces such as: external turning, hole turning, face turning, cutting off turning, external thread turning, internal thread turning, external turning, internal taper turning, shaping turning, etc.
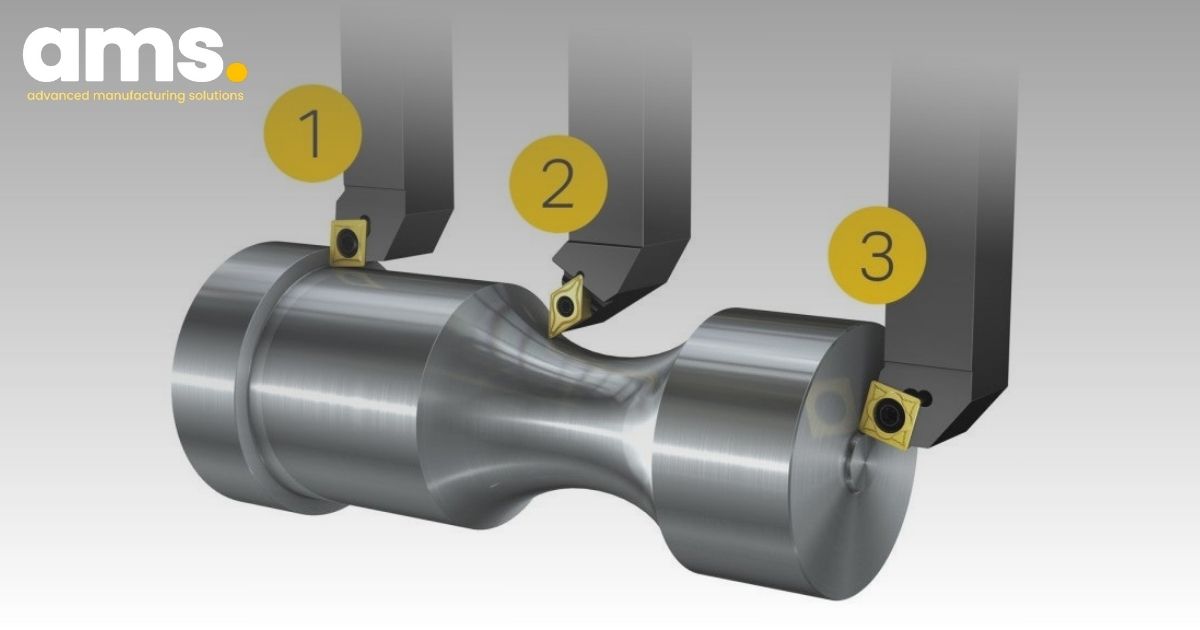
4.2 Ability to achieve high accuracy
The accuracy of the turning process depends on the following factors:
- Machine accuracy: Including knife countermeasure, parallelism between slider and main shaft, coaxiality of moving parts and main shaft.
- Status of turning tool. The skill level of workers is also an important factor.
- When machining on a CNC lathe, the quality of the turning process depends less on the skills and techniques of the worker compared to turning on a conventional mechanical lathe.
For example, machining accuracy and relative positional accuracy such as coaxiality between shaft parts, coaxiality between inner and outer surfaces depend on the method of mounting the workpiece, the accuracy of the machine can reach 0.01 mm. When turning threads, the accuracy can reach level 7 and parameters Ra = 2.5 - 1.25 micrometers.
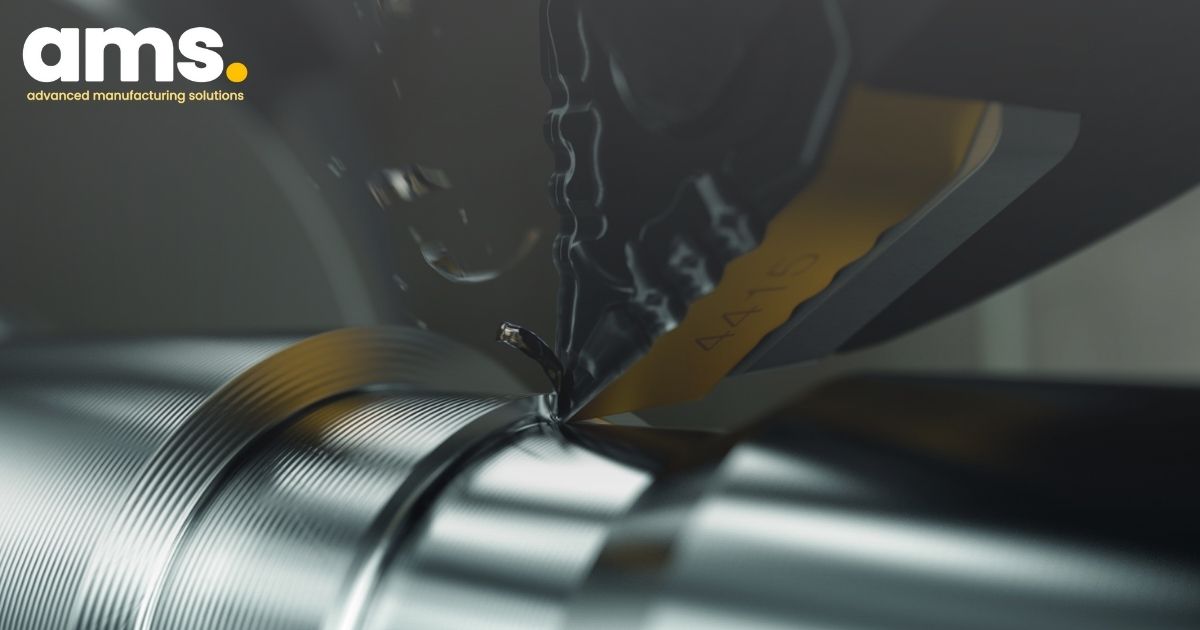
5. Correct turning technique
5.1 Correct turning process
When performing machining on a CNC lathe, the following factors should be considered to ensure a successful process:
- Prepare and set up the CNC machine: Before starting turning, make sure the CNC machine is properly prepared and set up to achieve the best accuracy and performance during the machining process.
- Choose the right cutting tool: Choosing the right cutting tool for each machine part will help machining faster and more accurately, while minimizing the wear of the cutting tool.
- Setting machining parameters: Setting machining parameters, including rotation speed, cutting pressure and cutting depth, is important to ensure product quality meets requirements.
- Monitoring the machining process: Monitoring the machining process and checking machine operations will help detect possible problems early and provide timely solutions.
- Check the results after turning: After completing the machining of machine parts, it is necessary to check the results and ensure that they meet the customer's requirements.
With the above factors, the CNC lathe machining process will become efficient and ensure the quality of the final product.

5.2 How to attach workpiece to lathe
To attach the workpiece to the CNC machine for turning, you can do the following steps:
- Determine the size of the workpiece: Before starting, know the exact size of the workpiece, including diameter, length and precision, to choose the appropriate clamping face.
- Check the status and clean the workpiece: Before loading the workpiece into the machine, check the workpiece surface and make sure it is not warped, eccentric, or has thick or thin errors. Also, clean the workpiece to remove dirt.
- Choose and install suitable clamps: Based on the size and shape of the workpiece, select suitable clamps and install them on the CNC machine. There are many different types of clamps you can use.
- Clean the clamp and table top: Before loading the workpiece into the clamp, clean the table surface and bottom of the clamp using a brush or cloth. This helps prevent the workpiece from tilting or slipping due to grease or dirt.
- Pick and clamp the workpiece into the machine: Place the workpiece on the clamp surface and ensure that the bottom of the workpiece is in full contact with the clamping surface. You need to correctly set the position and operation of the clamp in the control computer to achieve stable results.
- Grip the workpiece tightly: Use the clamping arm or power assist to clamp the workpiece into the clamp. Tighten so that the workpiece is not eccentric, tilted or rotated. If necessary, recheck the position of the workpiece before proceeding with machining.
Note: During the process of assembling and picking up workpieces into the CNC machine, fully comply with labor safety regulations and ensure you have received proper training to avoid causing machine damage or accidents to yourself.

6. Conclusion
Turning is a mechanical machining process that uses lathes to cut from the surface of the workpiece to create precise sizes and shapes.
The turning process is often performed on CNC machines with high precision. It plays an important role in the mechanical industry, providing precision parts and components for many different industries, from machinery and equipment manufacturing to vehicle manufacturing.
Make the right choice for your turning applications by selecting the correct turning tool. If you are unsure or need assistance, AMS is here to help. As an experienced player in the precision industry for two decades, we have extensive expertise working with diverse applications and supplying top-notch Sandvik Coromant products. Our team at AMS is dedicated to providing you with free, trustworthy consultation. Contact us today to benefit from our wide knowledge and understanding.
AMS Company, Ltd.243/9/10D To Hien Thanh, Ward 13, District 10
Hot line: 028.3868 3738/3903 - Fax: 028.3868 3797