Optimizing with Diamond Paste: The Ultimate Selection Guide (Part 1)
Kemet Diamond Paste and Kemet Diamond Compound come in various sizes, including 5g, 10g, 20g, 50g, 100g, and 1kg containers. The specially designed AppliKator ensures precise dispensing of the diamond compound, preventing any leakage from syringes. Moreover, diamond paste is applicable in Metallography processes. For convenient application, Diamond Compound Applikator Sticks are crafted from Monocrystalline or Polycrystalline materials, eliminating the necessity for spatulas or manual application. These products are produced in compliance with ISO 9001:2015 Quality Assurance standards.
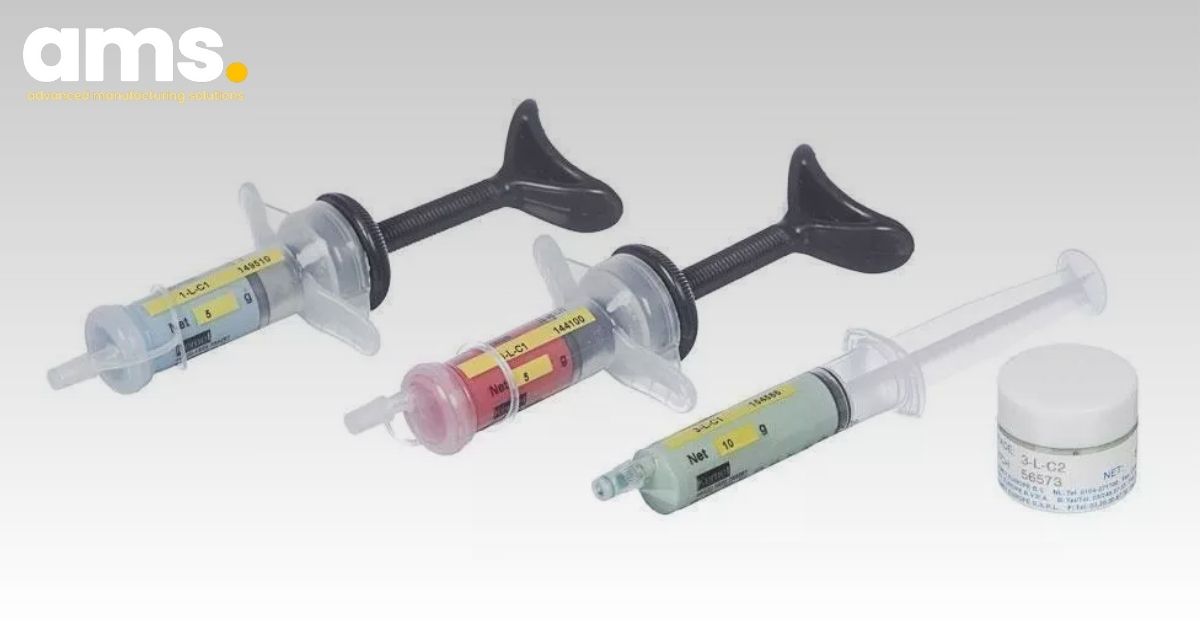
1. What is the best polishing paste for your particular application requirements?
When aiming to achieve the desired surface finish on tools, a particular level of roughness is often necessary, ranging from technically smooth to a deep high gloss. The choice of appropriate tools is paramount in this process.
Now, let's explore the various types of available diamond paste. Each Kemet diamond paste comprises a blend of diamond powder, characterized by its specific grade and concentration, and a chemical carrier. These pastes contain either mono or polycrystalline diamonds, meticulously sorted based on their grain size using a specialized vision system. By ensuring uniform dimensions of all diamond grains in the paste, Kemet diamond pastes ensure consistent performance throughout their usage. The chemical carriers used in these pastes are precisely formulated to address specific applications, resulting in a diverse range of products tailored to various materials and application methods.

1.1 Manual polishing
When manually polishing, the speed of the polishing tool is typically kept low. However, if you seek efficient and swift results, a high cutting force is essential. This is where the water-based KD diamond paste proves invaluable, tailored to meet these demands across a variety of metals. The KD paste presents varying diamond concentrations, suitable for a wide range of metal polishing applications. For rapid material removal, the 90 µm KD paste excels, swiftly and effectively eliminating material, expediting the polishing process. Progressing through the polishing stages involves transitioning to finer diamond paste grits. The 0.1 µm paste delivers a super smooth and flawless finish.

The versatile KD Diamond Paste serves dual purposes of stock removal and achieving a fine surface finish. Its unique solubility in both oil and water adds flexibility in selecting the preferred medium for polishing tasks. Especially recommended for Toolroom and Precision Engineering applications, this diamond compound's consistent performance makes it a top choice among industry professionals. Moreover, the KD Diamond Paste is offered in various concentrations for each micron size, allowing customization based on specific polishing needs. Concentrations range from C1 (lowest) to C4 (highest), providing flexibility to achieve optimal outcomes depending on material characteristics and desired results.
1.1.1 Type KD Diamond Paste
TYPE KD - Oil / Water soluble | |||||
Diamond Grade | Color | 5g AppliKator | 10g Syringe | 20g Syringe | 10g Stick |
Code | Code | Code | Code | ||
1/10-KD-C2 | gray | 111002 | 111126 | 111095 | - |
1/4-KD-C2 | 111004 | 111128 | 111097 | - | |
1-KD-C1 | blue | 111005 | 111129 | 111098 | 113189 |
1-KD-C2 | 111006 | 111130 | 111099 | ||
1-KD-C3 | 111007 | 111131 | 111100 | ||
3-KD-C1 | Green | 111008 | 111132 | 111101 | 113190 |
3-KD-C2 | 111009 | 111133 | 111102 | ||
3-KD-C3 | 111010 | 111134 | 111103 | ||
3-KD-C4 | 111011 | 111135 | 111104 | ||
6-KD-C1 | Yellow | 111012 | 111136 | 111105 | 113191 |
6-KD-C2 | 111013 | 111137 | 111106 | ||
6-KD-C3 | 111014 | 111138 | 111107 | ||
8-KD-C1 | Red | 111015 | 111139 | 111108 | 113192 |
8-KD-C2 | 111016 | 111140 | 111109 | ||
8-KD-C3 | 111017 | 111141 | 111110 | ||
8-KD-C4 | 111018 | 111142 | 111111 | ||
14-KD-C1 | Brown | 111019 | 111143 | 111112 | 113193 |
14-KD-C2 | 111020 | 111144 | 111113 | ||
14-KD-C3 | 111021 | 111145 | 111114 | ||
25-KD-C1 | Mahogany | 111022 | 111146 | 111115 | 113194 |
25-KD-C2 | 111023 | 111147 | 111116 | ||
25-KD-C3 | 111024 | 111148 | 111117 | ||
45-KD-C1 | Purple | 111025 | 111149 | 111118 | 113195 |
45-KD-C2 | 111026 | 111150 | 111119 | ||
45-KD-C3 | 111027 | 111151 | 111120 | ||
60-KD-C1 | Orange | 111028 | 111152 | 111121 | 113196 |
60-KD-C2 | 111029 | 111153 | 111122 | ||
90-KD-C1 | White | 111030 | 111154 | 111123 | - |
90-KD-C2 | 111031 | 111155 | 111124 |
1.2 Machine polishing of molds
Machine polishing of molds involves utilizing a variety of tools, such as electric or compressed air powered hand motors, and even ultrasonic equipment. These tools operate at higher speeds, generating increased heat during the polishing process. To combat this, the use of the L oil-based diamond paste is highly advised, given its exceptional heat resistance, rendering it suitable for direct application on injection molds. A notable property of the L diamond paste is its slight stickiness, facilitating adherence to the polishing tool, enabling precise and accurate polishing with minimal diamond paste. Additionally, Type L diamond paste is highly concentrated, ensuring effective performance. In case dilution is necessary, adding oil maintains its suspension properties, keeping the paste well-mixed and ready for use.
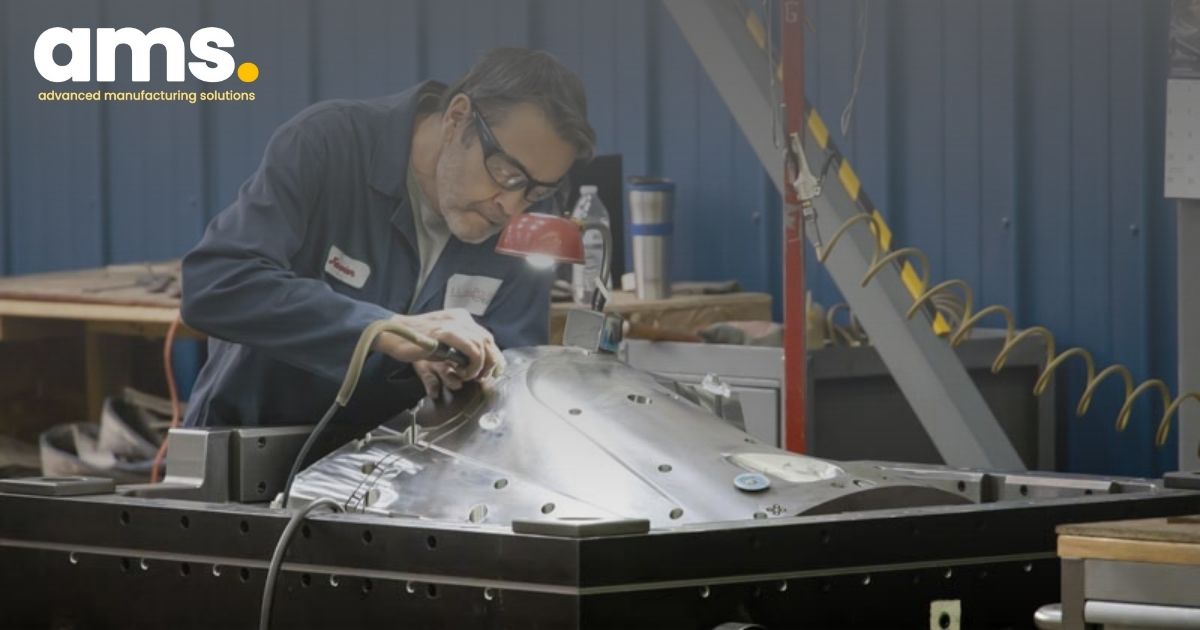
Specifically developed for hard materials such as Tungsten Carbide, Hardened Steels, and Ceramics, Type L diamond paste is an oil-soluble compound tailored to deliver exceptional results. Its carrier demonstrates high thermal stability, enabling the diamond compound to withstand the frictional heat generated during polishing. This stability ensures that the Kemet Diamond Compound maintains its integrity and suspension properties even under demanding operating conditions. Given its superior characteristics, Type L diamond paste is especially recommended for Toolroom and General Production applications, where precision and quality are paramount. Through the use of this specialized diamond compound, professionals can achieve outstanding results in polishing and refining molds, ensuring optimal performance and longevity of the finished products.
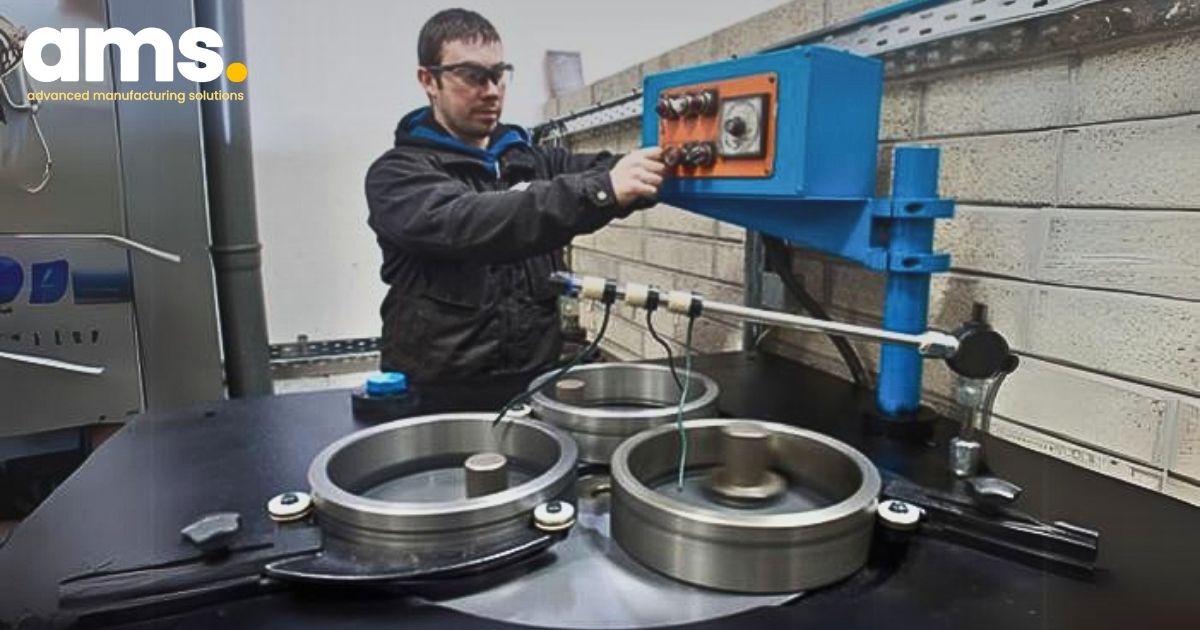
1.2.1 Type L Diamond Paste
TYPE L - Oil soluble | |||||
Diamond Grade | Color | 5g AppliKator | 10g Syringe | 20g Syringe | |
Code | Code | Code | |||
1-L-C1 | Blue | 112001 | 112069 | 112052 | |
1-L-C2 | 112002 | 112070 | 112053 | ||
3-L-C1 | Green | 112003 | 112071 | 112054 | |
3-L-C2 | 112004 | 112072 | 112055 | ||
6-L-C1 | Yellow | 112005 | 112073 | 112143 | |
6-L-C2 | 112006 | 112074 | 112138 | ||
8-L-C1 | Red | 112007 | 112075 | 112058 | |
8-L-C2 | 112008 | 112076 | 112059 | ||
14-L-C1 | Brown | 112009 | 112077 | 112060 | |
14-L-C2 | 112010 | 112078 | 112061 | ||
25-L-C1 | Mahogany | 112011 | 112079 | 112062 | |
25-L-C2 | 112012 | 112080 | 112063 | ||
45-L-C1 | Purple | 112013 | 112081 | 112064 | |
45-L-C2 | 112014 | 112082 | 112065 | ||
45-L-C3 | 112015 | 112086 | 112066 | ||
60-L-C1 | Orange | 112016 | 112085 | 112067 | |
90-L-C1 | White | 112017 | 112084 | 112068 |
1.3 How to use Diamond Paste

-
Prepare the Substrate: Ensure the substrate is clean and free from dirt, debris, or prior coatings. Clean the surface with a mild detergent or solvent and rinse with clean water. Ensure the substrate is completely dry before proceeding.
-
Apply Diamond Paste: Use a small quantity of highly concentrated diamond paste and apply it onto the lapping plate or flat surface.
-
Spread Evenly: Spread the diamond paste evenly across the lapping plate or flat surface, ensuring uniform distribution without any clumps or gaps.
-
Determine Amount Needed: The amount of diamond paste required depends on the substrate's size and the desired level of abrasiveness. Generally, a small pea-sized amount is adequate for most applications.
-
Place the Substrate: Position the substrate onto the lapping plate or flat surface, ensuring proper contact between the diamond paste and the substrate.
-
Apply Pressure and Motion: Depending on the hardness of the substrate, apply gentle and even pressure while moving the substrate in circular, figure-eight, or back-and-forth motions. Avoid applying excessive pressure to prevent uneven results or substrate damage.
-
Maintain Consistency: Maintain consistent pressure and motion throughout the polishing process to ensure consistent material removal and even distribution of the diamond particles.
-
Periodic Inspection: Pause periodically during polishing to inspect the substrate's surface. Rotate the substrate by 90 degrees to maintain parallelism and check for visible scratches, imperfections, or the desired levels of shine.
-
Clean the Substrate: After each polishing stage, thoroughly clean the substrate to remove any residue or excess diamond paste. Inspect the surface for any remaining imperfections or scratches before proceeding to the next step.
-
Final Cleaning: Once the desired level of polishing is achieved, ensure thorough cleaning of the substrate to eliminate any traces of diamond paste residue. Using an ultrasonic cleaner is highly recommended for this final cleaning step.
2. AMS Company Limited: Your Premier Partner for Polishing Products in Vietnam's Mold and Die Industry
At AMS Company Limited, we take pride in being the leading trading company for polishing products in Vietnam's dynamic mold and die industry. With our wealth of experience, unwavering dedication to innovation, and a commitment to exceeding customer expectations, we are positioned to provide an extensive and diverse range of solutions to manufacturers.
2.1 Meeting Industry-Specific Needs
We recognize the distinct challenges encountered by mold and die manufacturers, and our team of seasoned experts is fully equipped to guide you in selecting the optimal polishing products tailored to your precise requirements. Whether your needs call for standard items or custom solutions, our depth of knowledge and technical proficiency enables us to deliver unparalleled outcomes.
2.2 Tailored Solutions for You
At AMS Company Limited, we are devoted to ensuring that every client receives personalized attention and comprehensive support. Our goal is to assist you in securing the best-suited polishing products, empowering your operations with efficiency and precision. We understand that no two manufacturers are alike, and as such, we are committed to offering tailored solutions that enhance your productivity and product quality.
2.3 Reach Out to AMS
Should you require any support with your polishing requisites, AMS Company Limited stands ready to offer expert assistance. Our dedicated customer service team is available to address any queries you may have and to provide individualized recommendations to propel your manufacturing processes to new heights.
Contact AMS Company Limited today and allow us to be your partner in elevating your polishing capabilities.
AMS Company, Ltd.243/9/10D To Hien Thanh, Ward 13, District 10
Hot line: 028.3868 3738/3903 - Fax: 028.3868 3797