Độ Bền và Độ Hao Mòn Của Dụng Cụ Cắt Gọt Kim Loại: Bí Quyết Tối Ưu Hóa và Bảo Quản
NỘI DUNG
Hao mòn xảy ra khi bề mặt của vật liệu bị phá hủy và tách ra trong quá trình chuyển động trượt, lăn hoặc va chạm với nhau.

1. Nguyên nhân gây ra sự hao mòn của dụng cụ cắt là gì?
Hao mòn dụng cụ cắt xảy ra do tương tác giữa các nhấp nhô bề mặt, tương tự như hiện tượng ma sát. Mòn không phụ thuộc vào tính chất của vật liệu mà chủ yếu phụ thuộc vào hệ thống và các điều kiện vận hành. Các điều kiện này ảnh hưởng trực tiếp đến tình trạng mòn tại bề mặt tiếp xúc chung. Một quan điểm sai lầm phổ biến là cho rằng ma sát lớn trên bề mặt chung là nguyên nhân chính gây mòn với tốc độ cao.
Mòn dụng cụ cắt như dao phay, dao tiện, và các loại dụng cụ khác đánh giá khả năng làm việc của chúng và hạn chế tuổi thọ thông qua quá trình mòn. Mòn này ảnh hưởng đáng kể đến độ chính xác của quá trình gia công, chất lượng bề mặt sản phẩm và tổng thể tính kinh tế của quá trình gia công. Sự nghiên cứu và phát triển các vật liệu dụng cụ mới cũng như các biện pháp công nghệ mới nhằm tăng bền bề mặt được đặt ra với mục tiêu tăng khả năng chịu mòn của dụng cụ.
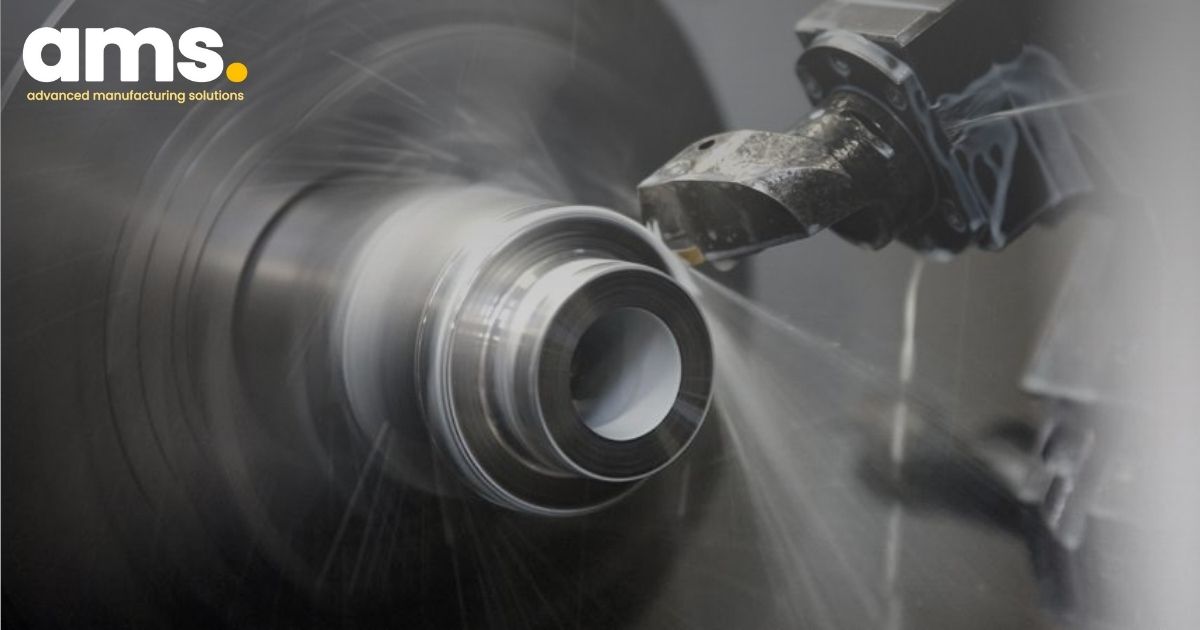
2. Mòn dụng cụ cắt gọt
Trong quá trình cắt gọt kim loại, hiệu suất cắt của dụng cụ sẽ giảm dần và cuối cùng sẽ không còn có thể cắt được do sự mòn hay hỏng hoàn toàn.
Sự mòn của dụng cụ được coi là tiêu chí chính để đánh giá hiệu suất làm việc của dụng cụ, do nó ảnh hưởng đến tuổi thọ của dụng cụ và trực tiếp tác động đến độ chính xác của quá trình gia công, chất lượng bề mặt và các khía cạnh kinh tế kỹ thuật nói chung.
Việc phát triển và tìm kiếm các loại vật liệu mới cho dụng cụ cắt gọt kim loại cùng với việc áp dụng các phương pháp công nghệ mới nhằm tăng cường khả năng chịu mài mòn, chẳng hạn như sử dụng lớp phủ bề mặt TiN, TiAlN, CBN, đều nhằm mục tiêu tối ưu hóa sức mạnh chống mài mòn của dụng cụ cắt gọt kim loại như dao phay đĩa hợp kim, dao phay cầu hợp kim, và cải thiện hiệu suất của quá trình cắt gọt.
3. Các loại hiện tượng mài mòn cho dụng cụ cắt trong ngành công nghiệp cơ khí
3.1 Mòn mặt sau
Dạng mòn này xảy ra khi lớp vật liệu dụng cụ bị tách ra khỏi mặt sau trong quá trình gia công. Hiện tượng mòn thường diễn ra khi cắt với chiều dày cắt nhỏ (t ≤ 0.1mm) hoặc khi gia công vật liệu có tính chất giòn.
3.2 Mòn mặt trước
Trong quá trình cắt, do phôi trượt trên mặt trước, tạo ra một trung tâm áp lực cách lưỡi cắt một khoảng nhất định có dạng lưỡi liềm. Vết lõm hình dạng lưỡi liềm trên mặt trước là kết quả của việc vật liệu dụng cụ bị bóc theo phôi trong quá trình chuyển động. Vết lõm thường xuất hiện dọc theo lưỡi cắt, và được đánh giá dựa trên chiều rộng, chiều sâu và khoảng cách từ lưỡi cắt đến vết mòn. Sự mòn này xảy ra khi gia công vật liệu dẻo với chiều sâu cắt lớn.

3.3 Mòn đồng thời mặt trước và mặt sau
Dụng cụ cắt gọt, bao gồm cả mũi khoan nguyên khối, thường trải qua quá trình mòn ở cả mặt trước và mặt sau, dẫn đến việc tạo thành lưỡi cắt mới. Tình trạng này thường xảy ra khi thực hiện gia công vật liệu dẻo với độ dày cắt trong khoảng từ 0,1 đến 0,5mm.
3.4 Cùn lưỡi cắt
Trên dụng cụ cắt, vết mòn thường hình thành một cung tròn theo lưỡi cắt. Để đo bán kính của cung này, ta đo từ mặt phẳng vuông góc với lưỡi cắt. Hiện tượng mòn này thường xảy ra khi gia công các vật liệu dẫn nhiệt kém, đặc biệt là trong quá trình gia công chất liệu dẻo. Do nhiệt tập trung tại mũi cắt, lưỡi dao sẽ trở nên cùn nhanh chóng.
4. Các cơ chế mòn của dụng cụ cắt gọt
4.1 Mòn do cào xước
Khi thực hiện cắt ở tốc độ thấp và nhiệt độ cắt thấp, cơ chế mài mòn hạt mài trở thành yếu tố quan trọng. Các tạp chất có độ cứng cao trong vật liệu chịu gia công sẽ tạo ra các vết cào xước song song trên bề mặt tiếp xúc của dụng cụ do quá trình chuyển động cào xước.
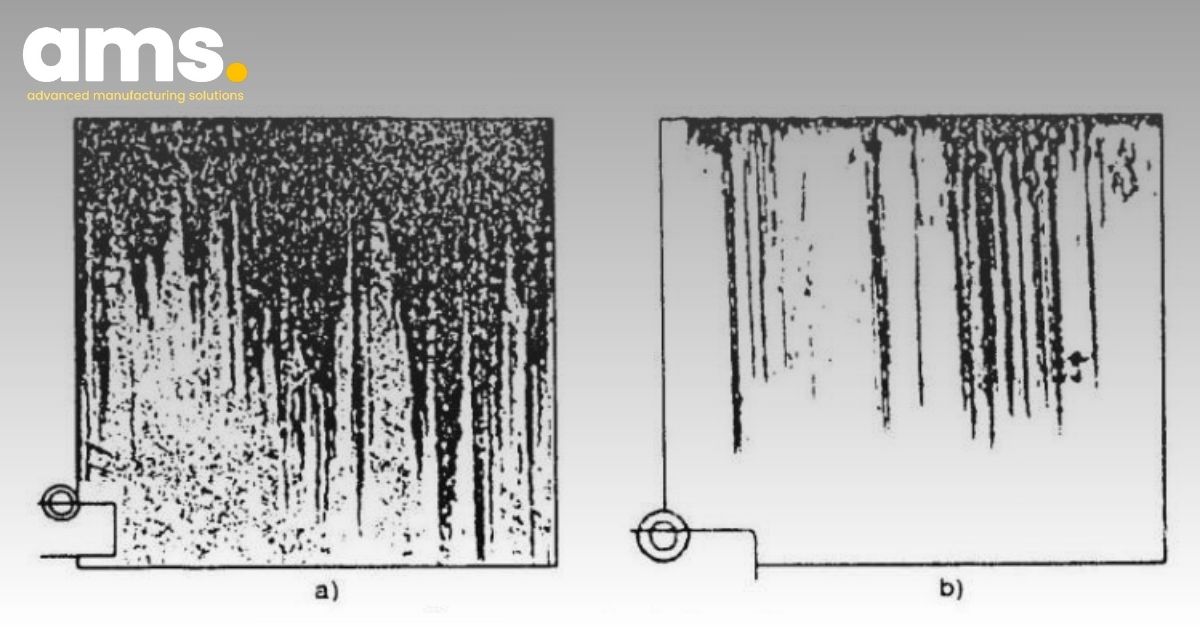
4.2 Mòn do dính
Khi hai bề mặt rắn, phẳng trượt so với nhau bị mòn do dính xảy ra tại điểm tiếp xúc ở đỉnh các nhấp nhô do tác động của tải trọng theo pháp tuyến. Khi sự trượt xảy ra, vật liệu ở vùng này bị trượt (biến dạng dẻo) dính vào bề mặt đối diện hoặc tạo thành các mảnh mòn rời, một số mảnh mòn còn được tạo ra do quá trình mòn do mỏi ở đỉnh các nhấp nhô. Đối với dụng cụ cắt gọt (mũi mài hợp kim,...), hiện tượng mòn do dính phát triển mạnh đặc biệt trong điều kiện nhiệt độ cao. Các vùng dính bị trượt cắt và tái tạo liên tục theo chu kỳ thậm chí trong khoảng thời gian cắt ngắn, hiện tượng mòn này có thể được gọi là dính mòi.
4.3 Mòn do hạt mài
Trong nhiều trường hợp, quá trình mòn bắt đầu do hiện tượng dính tạo ra các hạt mòn ở vùng tiếp xúc, sau đó các hạt mòn này trở nên cứng và tích tụ do quá trình ôxy hóa, gây ra hiện tượng mòn hạt cứng ba vật. Thậm chí, trong một số trường hợp, các hạt cứng này có thể được tạo ra và nhập vào hệ thống trượt từ môi trường xung quanh.
4.4 Mòn do khuếch tán
Trong quá trình cắt, việc nhiệt độ tăng lên đặc biệt là trên mặt trước dụng cụ làm tạo điều kiện thuận lợi cho hiện tượng khuếch tán giữa vật liệu dụng cụ và vật liệu gia công. Tốc độ mòn tăng đột ngột tại nhiệt độ 930°C khi cắt bằng dao hợp kim cứng (bao gồm dao phay ngón hợp kim và dao phay rảnh) là một dạng mòn quan trọng ở tốc độ cắt cao. Cấu trúc tế vi của các lớp dưới của phôi thép cắt bằng dao hợp kim cứng chứa nhiều carbon hơn so với phôi, cho thấy sự kết hợp hoặc khuếch tán của carbon từ chỉ thị volfram và phôi, làm tăng thành phần carbon của các lớp này.
4.5 Mòn do ôxy hoá
Dưới tác động của tải trọng nhỏ, vết mòn trên bề mặt kim loại trở nên trơn bóng và màu sắc sáng hơn. Quá trình mòn diễn ra với tốc độ chậm và tạo ra các hạt mòn oxit nhỏ. Cơ chế mòn này xuất phát từ sự bong ra của các lớp oxit. Khi các lớp oxit bị bong ra, các lớp mới được tạo ra liên tục theo một quá trình tiếp nối. Tuy nhiên, lớp oxit tạo ra tương tác hóa học với môi trường bề mặt có khả năng ngăn chặn hiện tượng dính. Trong điều kiện làm việc trong môi trường chân không, mòn do dính xảy ra mạnh do lớp oxit không thể hình thành được.
4.6 Mòn do nhiệt
Khi vật liệu được cắt bằng lưỡi cắt, thể tích vật liệu ở vị trí cắt rất nhỏ, dẫn đến tập trung nhiệt độ cao ở vị trí này. Hiện tượng này có thể gây ra quá nhiệt và dẫn đến sự phá hủy của lưỡi cắt do nhiệt.

4.7 Mòn của dụng cụ cắt gọt do lớp phủ bay hơi
Trên dụng cụ cắt có lớp phủ, hai cơ chế mòn chính xảy ra khi thao tác cắt bao gồm nứt vỡ và bong tróc của lớp phủ, cũng như làm mòn vật liệu nền. Sự gãy vỡ của lớp phủ trên mặt trước được gây ra bởi sự phát triển của nhiệt độ cao, dẫn đến việc giảm độ cứng của vật liệu nền. Quá trình gãy vỡ này được thúc đẩy bởi ma sát giữa phoi và lớp phủ, tạo ra nhiệt độ và truyền nhiệt đến dụng cụ cắt. Dưới áp lực và nhiệt độ cao tạo ra dưới lớp phủ, vật liệu nền trở nên dẻo, gây nứt vỡ và bong tróc phần lớp phủ, làm lộ vật liệu nền ra ngoài. Sự gia tăng của ma sát và nhiệt độ trong vùng này tiếp tục làm mòn mặt trước, dẫn đến sự suy giảm khả năng cắt gọt của dụng cụ cắt.
5. Các yếu tố dẫn đến độ bền của dụng cụ cắt gọt kim loại
Tuổi thọ của dụng cụ cắt gọt trong gia công cơ khí được định nghĩa là thời gian hoạt động liên tục giữa hai lần mài sắc, hay nói cách khác, tuổi thọ của dụng cụ cắt là thời gian làm việc liên tục cho đến khi bị mòn đến mức mòn giới hạn.
Đây là một yếu tố quan trọng ảnh hưởng đáng kể đến năng suất và tính kinh tế trong quá trình gia công cắt. Tuổi thọ của dụng cụ phụ thuộc chủ yếu vào yêu cầu kỹ thuật của chi tiết gia công. Do đó, việc dự đoán tuổi thọ cơ bản có ý nghĩa quan trọng để thực hiện các so sánh.
Trong thực tế, tuổi thọ của dụng cụ cắt gọt (như mũi khoan và mũi taro) thường bị ảnh hưởng bởi các yếu tố sau đây:
-
Sự biến đổi về độ cứng, cấu trúc tế bào, thành phần hóa học và các đặc tính bề mặt của phôi.
-
Thay đổi vật liệu dụng cụ, thông số hình học và phương pháp mài.
-
Sự dao động của hệ thống máy móc, dao cụ và công nghệ.
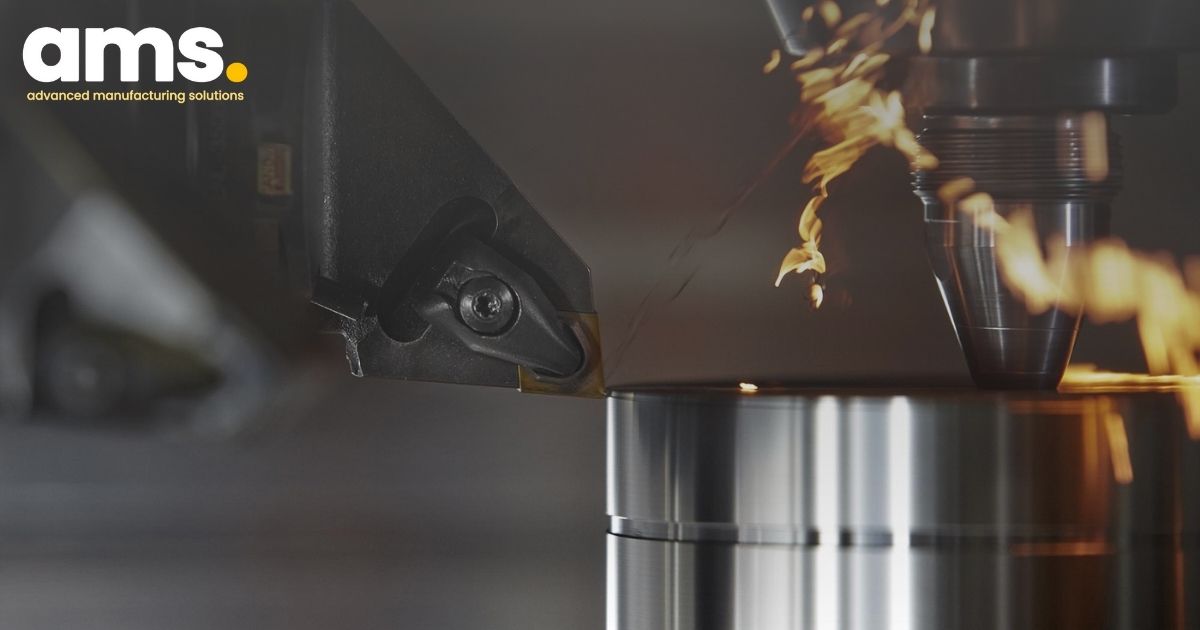
6. Phân tích tác động của chế độ cắt tới tuổi thọ của dụng cụ cắt gọt
Chế độ cắt đặc biệt ảnh hưởng mạnh nhất đến tuổi thọ bề mặt cắt thông qua vận tốc cắt và lượng chạy dao.
-
Đối với bề mặt cắt phía trước, quy luật mòn tương đối đơn giản, mòn diễn ra chậm cho đến một giới hạn vận tốc cắt, khi mà tốc độ mòn tăng mạnh. Lượng chạy dao càng lớn thì giới hạn vận tốc cắt càng nhỏ.
-
Ở mặt sau, tốc độ mòn tăng nhanh từ vận tốc cắt và lượng chạy dao giới hạn, tương tự như mặt trước do các cơ chế mòn phụ thuộc nhiệt độ quyết định tuổi thọ. Tuy nhiên, dưới một dải tốc độ cắt, tốc độ mòn mặt sau tăng trên một khoảng nhất định trước khi giảm liên tục, vì các cơ chế mòn ở đây không phụ thuộc vào nhiệt độ.
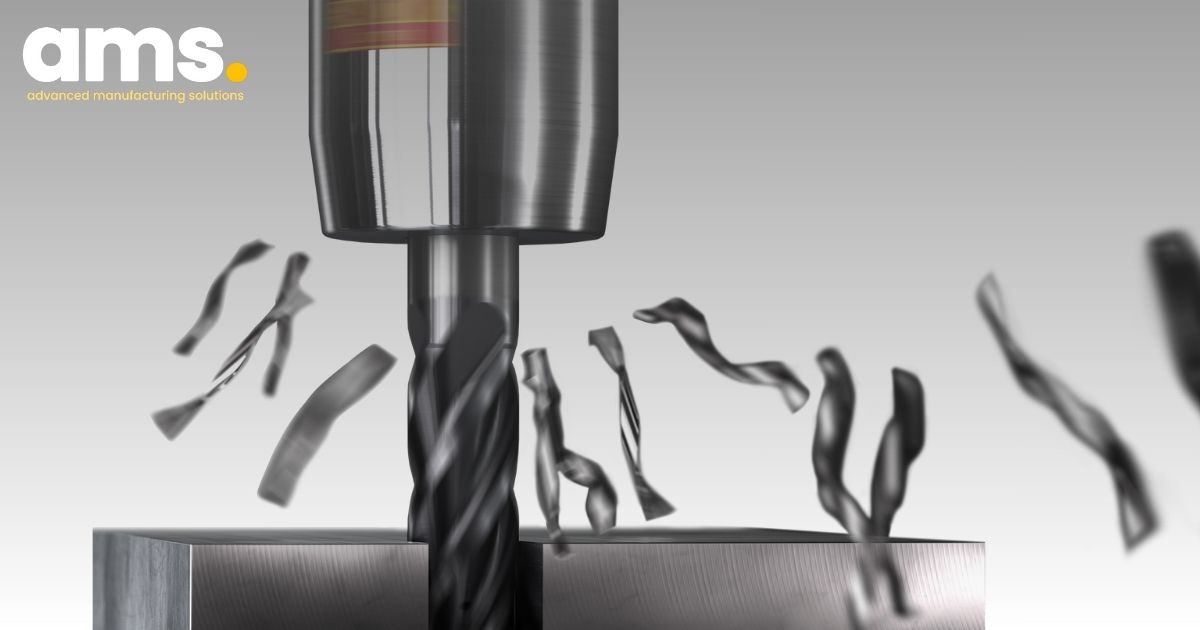
7. Xác định tầm quan trọng của lớp phủ cứng trong việc gia tăng độ bền của dụng cụ cắt
Lớp phủ cứng đóng vai trò quan trọng trong việc giảm ma sát trên bề mặt dụng cụ, hạn chế nhiệt độ cực đại và sự phát triển của trường nhiệt độ bên trong dụng cụ, từ đó giảm thiểu mòn do nhiệt và gia tăng tuổi thọ của dụng cụ. Lớp phủ cứng còn tạo ra một lớp phân cách giữa phôi và dao, có khả năng chống dính và chống cào xước mạnh mẽ do tính trơ hoá học và độ cứng cao, từ đó cũng ảnh hưởng tích cực đến sự giảm mòn và tăng tuổi thọ của dụng cụ. Ngoài ra, tính chất nhiệt đặc biệt của lớp phủ cứng cũng giảm tỷ lệ truyền nhiệt vào phôi và dao, là yếu tố quan trọng đóng vai trò trong việc gia tăng tuổi thọ của dụng cụ phủ khi cắt với chế độ cắt cao.
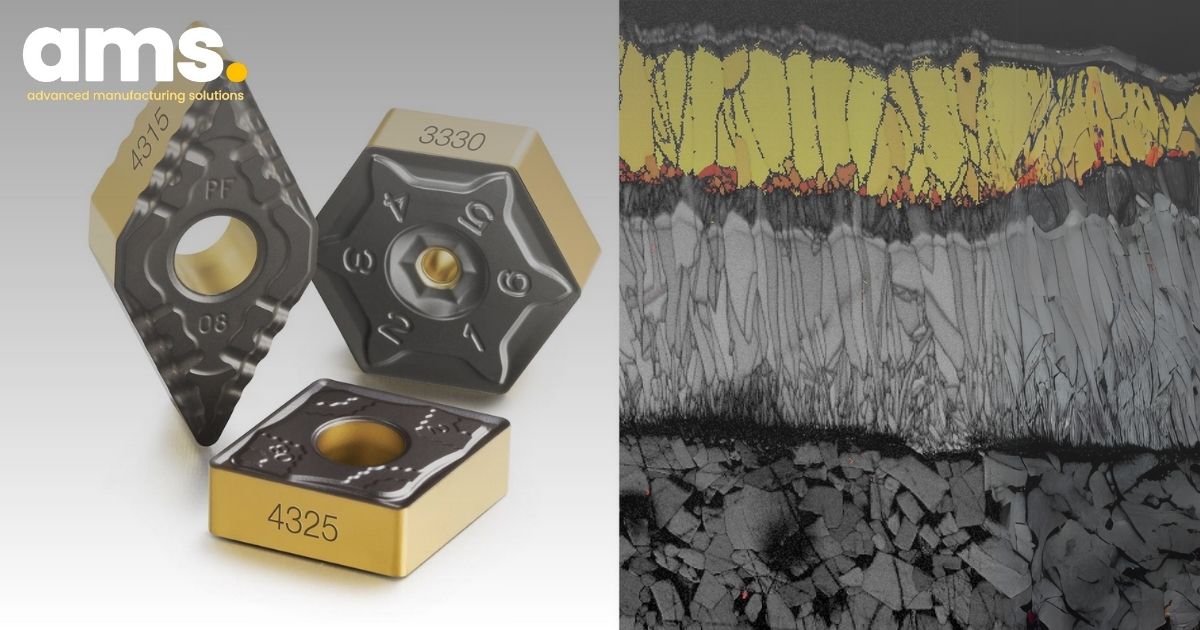
8. Sandvik Coromant: Đứng Đầu trong Công Nghệ Dụng Cụ Cắt Gọt
Sandvik Coromant, một cái tên không còn xa lạ trong lĩnh vực công nghệ cắt kim loại, nổi bật với sự tiên phong trong đổi mới và chính xác. Với những giải pháp tiên tiến, Sandvik Coromant đã đánh dấu sự cách mạng trong ngành công nghiệp, thiết lập các tiêu chuẩn mới về độ bền, hiệu suất và hiệu quả. Sự cam kết không ngừng trong nghiên cứu và phát triển giúp Sandvik Coromant dẫn đầu trong việc tiến bộ về vật liệu dụng cụ cắt, hình học và lớp phủ, từ đó giúp các nhà sản xuất tối ưu hóa quy trình sản xuất và đạt được kết quả vượt trội.
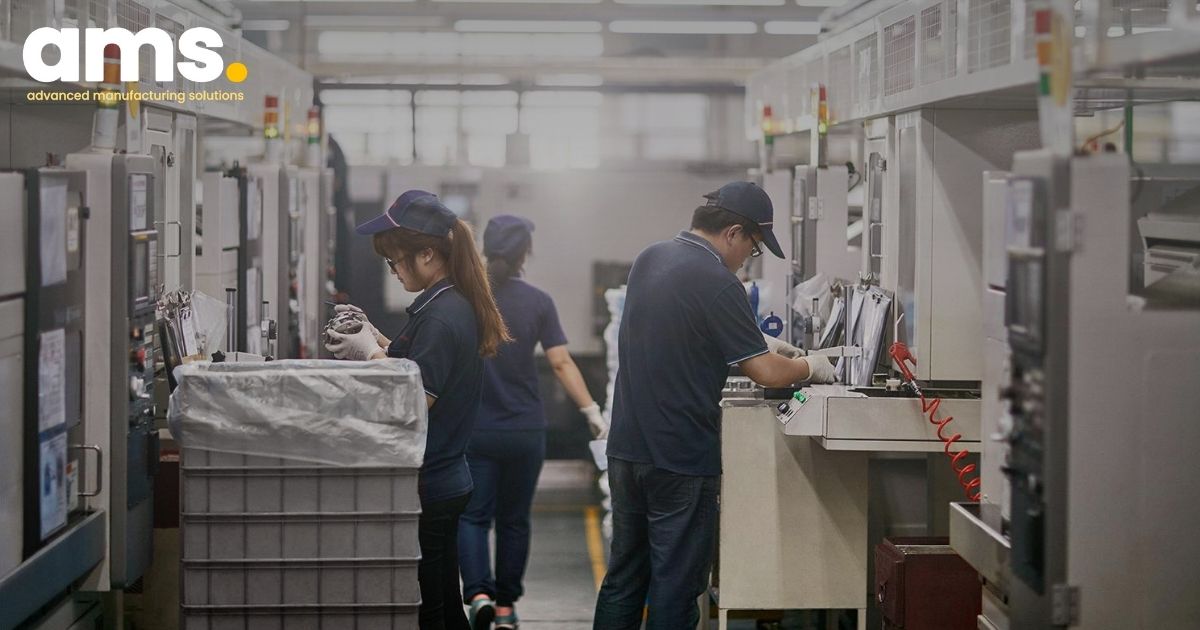
Ở Việt Nam, Công ty TNHH Thương mại và Dịch vụ Kỹ thuật AMS tự hào là nhà phân phối chính thức của Sandvik Coromant, đứng đầu trong lĩnh vực công nghệ dụng cụ cắt gọt. Với hơn hai thập kỷ kinh nghiệm, AMS đã xác lập mình là đối tác đáng tin cậy cung cấp các giải pháp sản xuất cho doanh nghiệp, không ngừng nâng cao hiệu quả vận hành và năng suất trong nhiều ngành công nghiệp khác nhau trên toàn quốc. Là đối tác phân phối ủy quyền của Sandvik Coromant, AMS đồng hành cùng khách hàng tiếp cận các đổi mới và giải pháp công nghệ tiên tiến nhất, giúp các doanh nghiệp nâng cao quy trình sản xuất và đạt được kết quả tối ưu nhất.
Trong hơn 20 năm qua, AMS đã là đối tác kiên định trong việc thúc đẩy xuất sắc sản xuất ngành cơ khí chính xác và khuôn mẫu. Cho dù đó là dụng cụ chính xác, chiến lược gia công tối ưu, hay giải pháp dụng cụ cắt gọt hiện đại, AMS luôn cam kết mang đến các sản phẩm và dịch vụ hàng đầu để đáp ứng nhu cầu đặc biệt của doanh nghiệp tại Việt Nam.
Nếu Quý khách đang tìm cách tích hợp các sản phẩm đổi mới của Sandvik Coromant vào quy trình sản xuất, AMS hân hạnh được là đối tác đáng tin cậy của Quý khách. Hãy liên hệ với chúng tôi ngay hôm nay để tìm hiểu cách AMS có thể cung cấp sự chuyên môn và hỗ trợ cần thiết để giúp doanh nghiệp của bạn phát triển với những giải pháp tiên tiến được cung cấp bởi Sandvik Coromant.
Công ty TNHH Thương mại và Dịch vụ Kỹ thuật A.M.S243/9/10D Tô Hiến Thành, phường 13, quận 10
Hot line: 028.3868 3738/3903 - Fax: 028.3868 3797