Những Lưu Ý Quan Trọng Khi Chọn Mua Insert và Chip Tiện Hợp Kim cho Mảnh Dao Tiện
NỘI DUNG
1. Thông tin cơ bản về Mảnh dao tiện, Insert và Chip tiện hợp kim
Mảnh dao tiện, công cụ không thể thiếu trong quy trình gia công tiện, đóng vai trò quan trọng trong tạo hình các chi tiết trên máy tiện (tiện CNC). Mang đến sự đa dạng về hình dáng và kích thước, mảnh dao tiện được chế tạo từ hợp kim, thể hiện sự sắc nét và tính chính xác trong quá trình cắt gọt vật liệu. Qua việc gắn vào dao, mảnh dao tiện nâng cao độ sắc bén và chính xác của dao, giúp người gia công dễ dàng làm việc với nhiều loại vật liệu có độ cứng khác nhau.
Vật liệu chế tạo mảnh dao tiện đa dạng, từ thép hợp kim, thép cacbon, thép gió, kim loại gốm đến hợp kim cứng. Đối với mỗi loại vật liệu, yêu cầu về độ chịu nhiệt, độ cứng, độ bền và khả năng chống mài mòn đều được đặt ra và phải đáp ứng một cách hoàn hảo.
Quy trình lựa chọn vật liệu chế tạo dao tiện phụ thuộc vào tốc độ tiện. Vật liệu cần phải đạt được độ cứng và khả năng chống mài mòn tốt nếu sử dụng cho tốc độ tiện thấp. Trong khi đó, tốc độ tiện cao đòi hỏi vật liệu có khả năng chịu nhiệt và độ cứng cao cùng độ bền ưu việt. Qua đó, quá trình lựa chọn vật liệu chế tạo dao tiện đóng vai trò quyết định trong hiệu suất và chất lượng của quá trình gia công tiện.
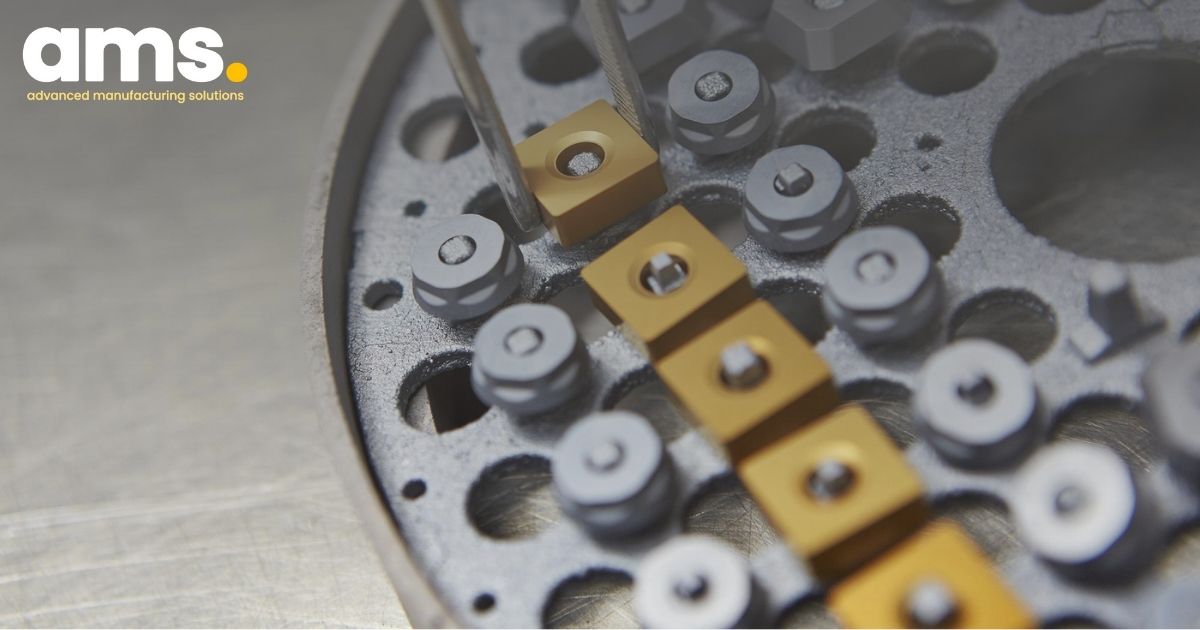
2. Phân loại mảnh dao tiện
2.1 Mảnh dao tiện hàn cố định
Mảnh dao tiện hợp kim được kết cấu hàn cố định với độ chắc chắn vô cùng cao, mang đến sự tin tưởng khi sử dụng. Người dùng chọn lựa mảnh dao phù hợp và thực hiện quá trình hàn cố định vào cán dao theo những yêu cầu kỹ thuật nghiêm ngặt, tạo nên sự bền bỉ vượt trội trong quá trình sử dụng
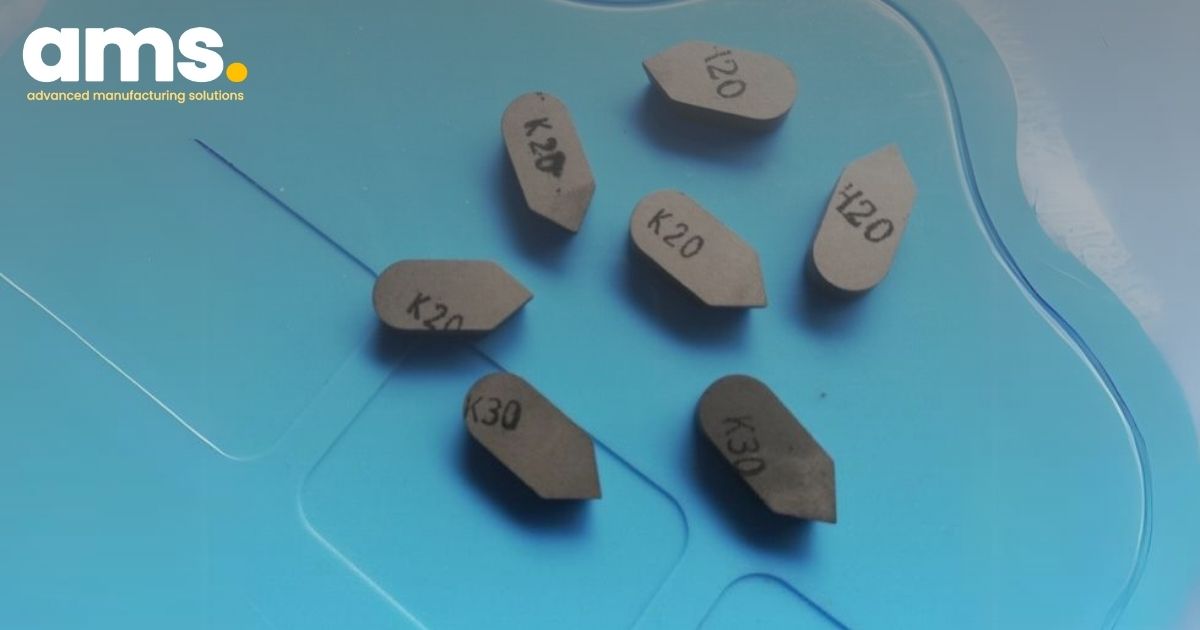
2.2. Mảnh dao tiện bắt vít
Mảnh dao tiện hợp kim bắt vít là loại được giữ cố định thông qua việc sử dụng bắt vít, mở ra khả năng linh hoạt cho người dùng khi có thể thay đổi mảnh dao một cách nhanh chóng. Điều này đem lại lợi ích đặc biệt, đặc biệt khi cần thay thế mảnh dao bị mòn do cắt nhiều vật liệu cứng trong thời gian dài. Chỉ cần mài lại và lắp vào, mảnh dao tiện sẽ có thể tiếp tục được sử dụng một cách hiệu quả.
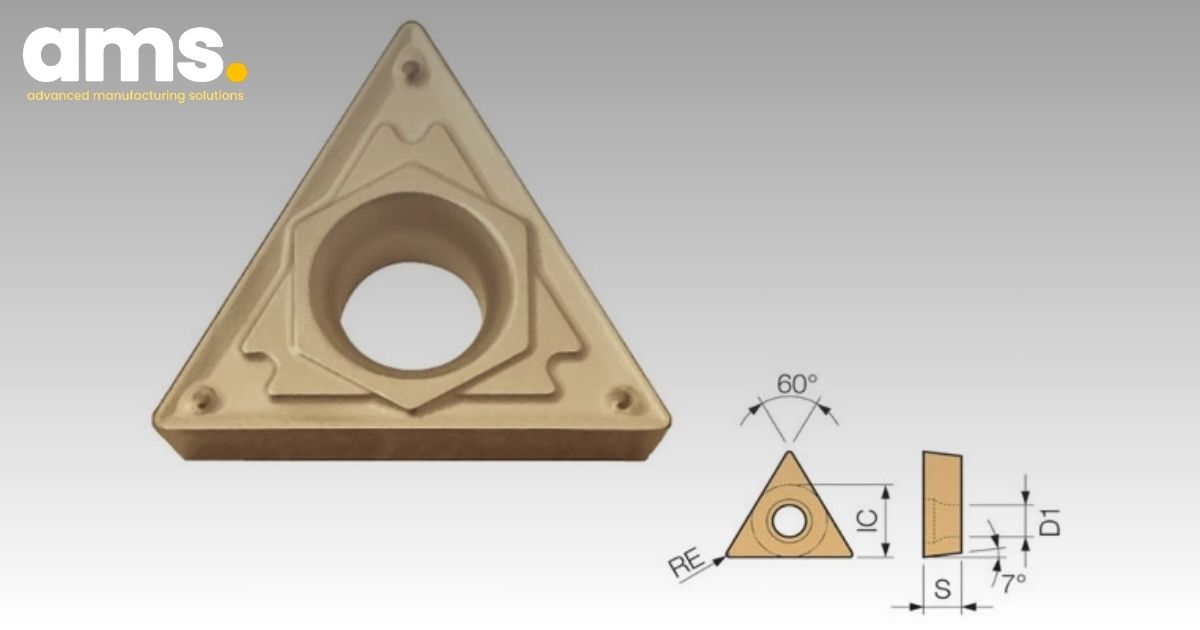
2.3. Mảnh dao tiện 1 mặt và 2 mặt
Mọi dụng cụ cắt gọt đều được trang bị Positive Insert (Dao tiện 1 mặt) và Negative Insert (Dao tiện 2 mặt), cung cấp sự linh hoạt và đa dạng trong quá trình gia công ứng dụng phay, tiện, khoan trong ngành cơ khí chính xác.
2.3.1. Dao tiện 1 mặt và 2 mặt (Positive Insert / Negative Insert) là gì?
Trong ngành gia công kim loại, dao cụ cắt gọt đóng vai trò quan trọng trong quá trình tiện, móc lỗ, khoan và các hoạt động cắt gọt khác. Việc sử dụng Insert (chip) ngày nay được phân thành các loại (type), lớp phủ (grade) và hình dạng hình học (shape) khác nhau.
Một điểm quan trọng mà nhiều người đều quan tâm đó là góc thoát phoi (clearance angle) của insert (dao tiện). Sự khác biệt lớn nhất giữa insert một mặt (positive insert) và insert hai mặt (negative) có thể thấy qua góc thoát phoi, với insert một mặt có góc thoát phoi dao động từ 1° đến 90°, trong khi đó, insert hai mặt thì cố định không có góc thoát phoi hoặc góc thoát phoi bằng 0°.
Một cách để nhận biết insert một mặt và hai mặt khác nhau là chú ý đến kí tự thứ 2 trong mã sản phẩm insert. Nếu là chữ N, đó sẽ là Insert hai mặt, còn nếu không phải là chữ N, thì đó đều là Insert một mặt.

2.3.2. Ứng dụng của Insert tiện 1 mặt và 2 mặt
Mỗi loại Insert dù hai mặt hay một mặt đều phù hợp với 1 ứng dụng gia công nhất định
Positive Insert (Insert 1 mặt) | Negative Insert (Insert 2 mặt) |
---|---|
Gia công lực cắt thấp | Gia công lực cắt lớn |
Có góc thoát phoi | Không có góc thoát phoi |
Phù hợp gia công móc lỗ hoặc tiện ngoài các chi tiết nhỏ | Lựa chọn đầu tiên khi bạn gia công tiện ngoài |
Sử dụng số góc cắt x 1 mặt | Sử dụng nhiều góc cắt (số góc cắt x 2 mặt) |
Phù hợp sử dụng trong điều kiện gia công tinh | Phù hợp sử dụng trong điều kiện gia công nặng như phá thô |
3. Những bước cần thiết để chọn được insert tiện hợp kim phù hợp
Trong quá trình chọn lựa chip insert, có nhiều yếu tố quyết định đến chất lượng sản phẩm gia công. Do đó, việc cẩn trọng lựa chọn thiết kế hình học, lớp nền, hình dạng, kích thước insert, góc lưỡi dao và góc tiếp xúc của insert là rất quan trọng để đạt được sự kiểm soát phoi tốt nhất trong quá trình gia công.
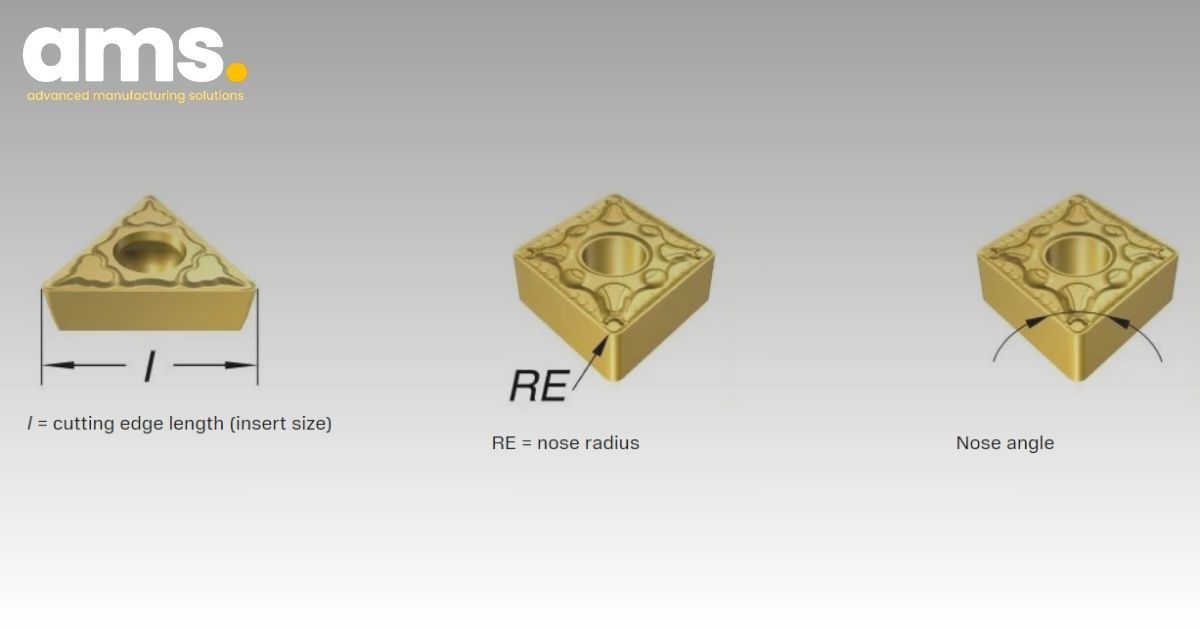
3.1. Thiết kế hình học Insert
Theo thiết kế, insert có thể được phân chia ra thành ba loại cơ bản tương ứng với các ứng dụng khác nhau:
1. Tiện phá thô: Sử dụng cho quy trình cắt với độ sâu lớn (D.O.C) và bước tiến (feed rate) cao, yêu cầu insert có thiết kế góc cắt cứng cáp nhất.
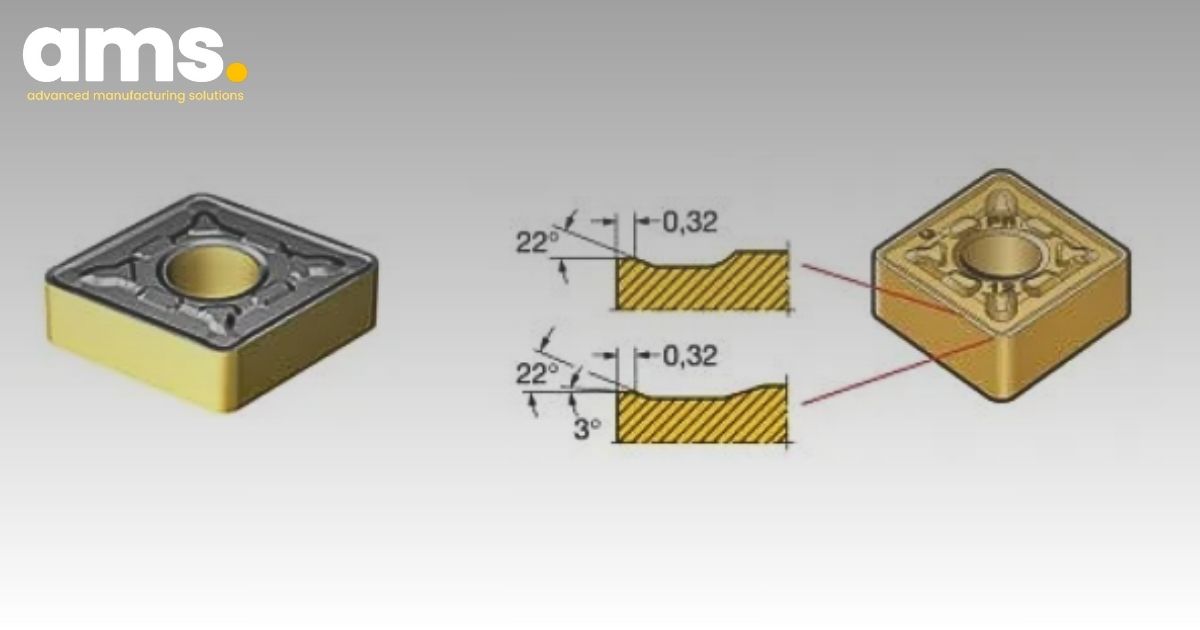
2. Tiện bán tinh: Sử dụng trong quy trình cắt với mức độ sâu và bước tiến trung bình.
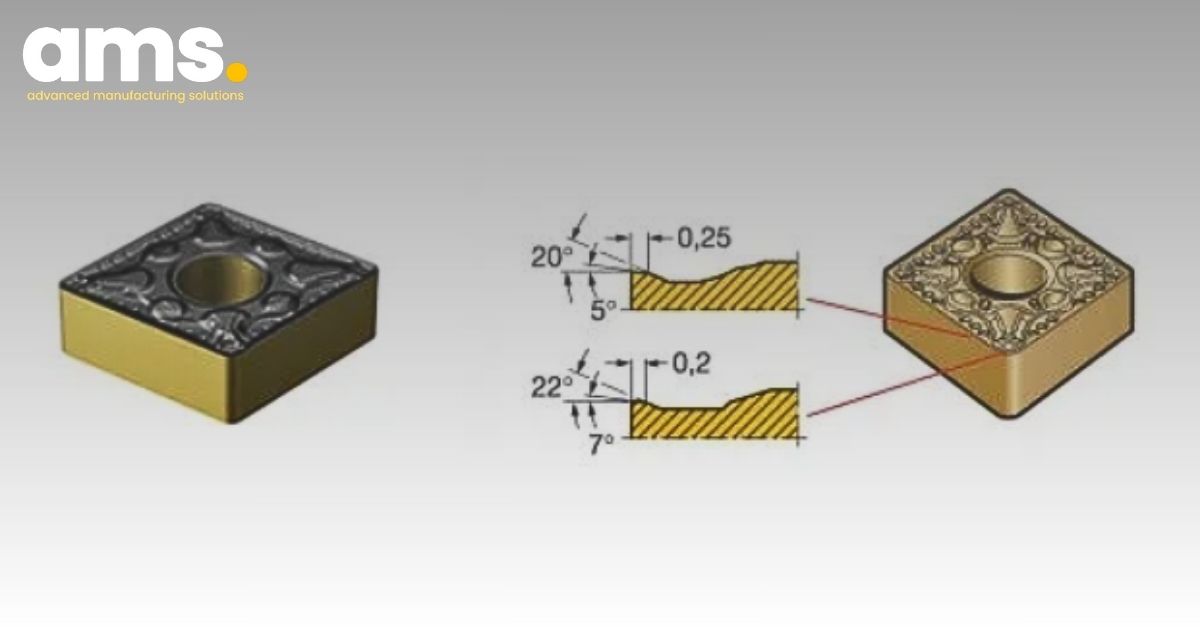
3. Tiện tinh: Sử dụng cho quy trình cắt với D.O.C và bước tiến thấp nhất, đồng thời yêu cầu lực cắt tối thiểu.
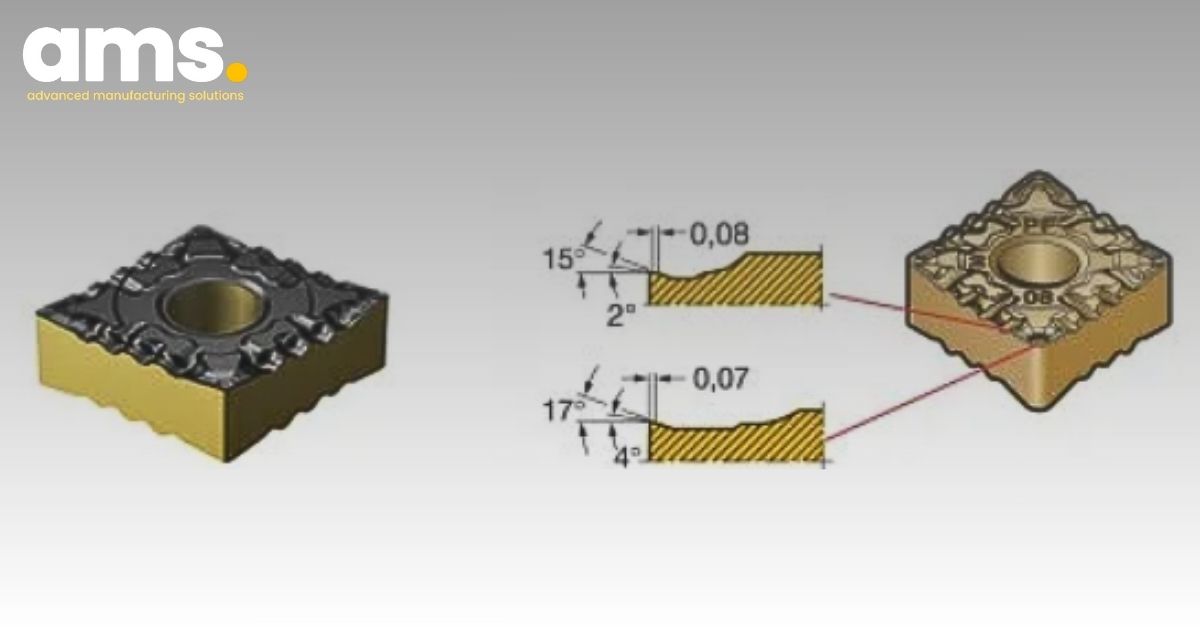
3.2. Lớp nền Insert tiện
Các yếu tố quan trọng trong quá trình gia công kim loại bao gồm các thành phần gia công như ISO P, M, K, N, S, H, ứng dụng gia công (tính, bán tinh, phá thô), và điều kiện gia công (tốt, trung bình, khó). Bên cạnh đó, thiết kế hình học và lớp nền của insert cũng đóng vai trò quan trọng, với khả năng bù đắp lẫn nhau. Chẳng hạn, các lớp nền cứng có thể cải thiện sự thiếu vững chắc của thiết kế hình học của insert.
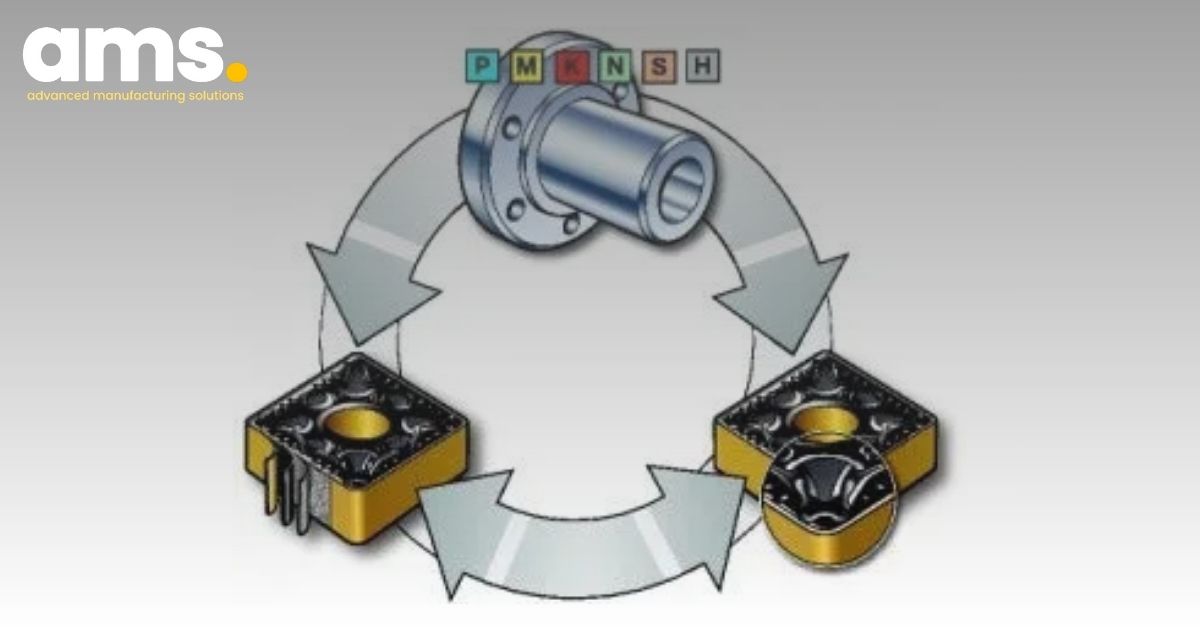
3.3. Hình dạng Insert
Việc lựa chọn hình dạng của insert liên quan đến khả năng tiếp cận góc cắt theo yêu cầu của công cụ gia công. Đối với việc này, việc chọn góc mũi lớn nhất có thể đảm bảo độ bền và tin cậy của đầu cắt. Tuy nhiên, việc này cần được cân nhắc kỹ lưỡng theo yêu cầu cụ thể của quá trình gia công, và không phải lúc nào cũng là lựa chọn tối ưu.
Sử dụng insert có góc mũi lớn đòi hỏi sự hỗ trợ từ các thiết bị công suất lớn hơn và có thể tăng độ rung khi so sánh với việc sử dụng insert có góc mũi nhỏ hơn. Insert có góc mũi nhỏ có thể yếu hơn và có góc cắt nhỏ, điều này làm tăng khả năng bị ảnh hưởng bởi nhiệt độ trong quá trình gia công.
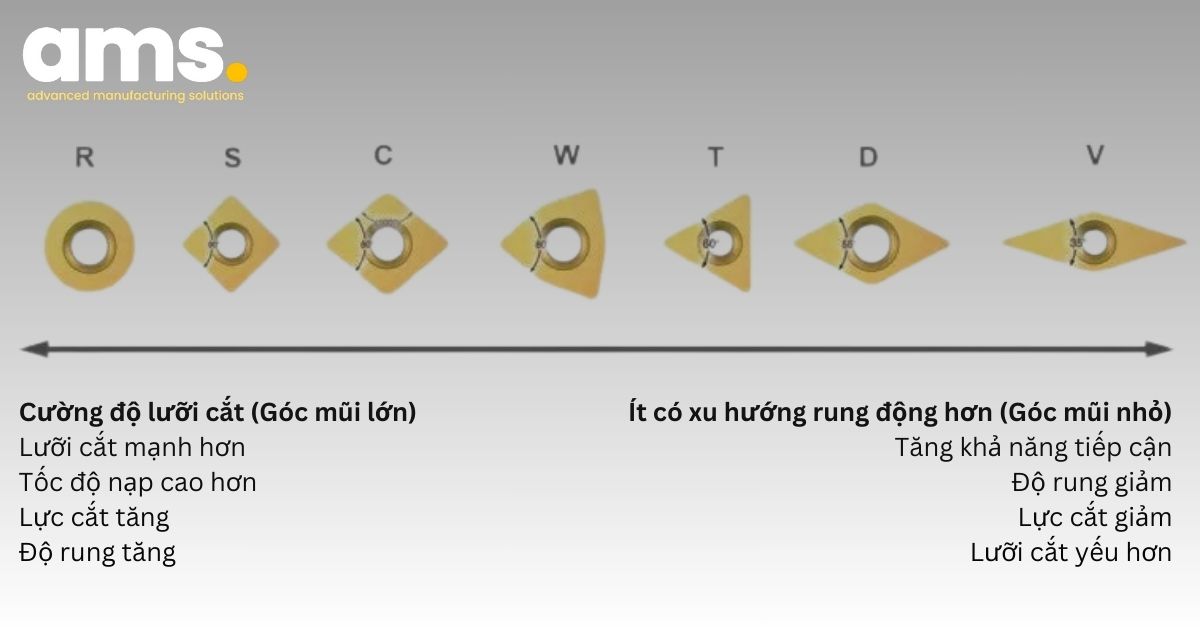
3.4. Kích thước Insert
Quá trình lựa chọn kích thước của insert phụ thuộc vào nhu cầu cụ thể của ứng dụng và yêu cầu không gian dành cho công cụ cắt trong quá trình sử dụng. Việc sử dụng kích thước insert lớn hơn có thể mang lại sự ổn định tốt hơn trong quá trình gia công. Đối với các ứng dụng gia công nặng như phá thô, kích thước insert thường cao hơn IC 25 mm (1 inch). Ngược lại, khi tiện tinh, việc giảm kích thước của insert trong nhiều trường hợp có thể được áp dụng để đáp ứng yêu cầu cụ thể của quá trình gia công.
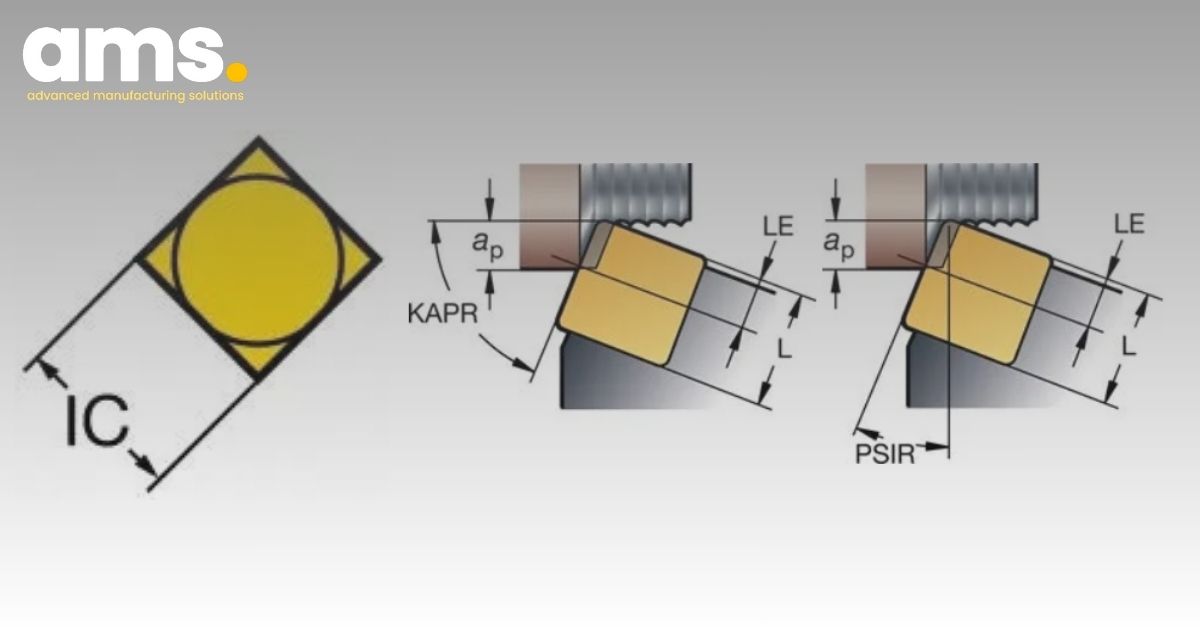
3.5. Bán kính góc dao, lưỡi cắt
Bán kính góc dao RE đóng vai trò quan trọng trong quá trình hoạt động của máy tiện. Việc lựa chọn các kích thước bán kính mũi như 0.2 – 0.4 – 0.8 trong insert là một yếu tố quan trọng, và quyết định phụ thuộc vào nhiều yếu tố như độ sâu cắt (D.O.C), bước tiến (feed), bề mặt hoàn thiện sau gia công, khả năng chịu lực bẻ và độ cứng của insert.
3.5.1. Góc RE nhỏ
-
Lựa chọn lý tưởng và phù hợp với áp suất cắt thấp
-
Giảm độ rung trong quá trình gia công
-
Góc cắt mạnh mẽ
3.5.2. Góc RE lớn
-
Gia công với áp suất cao
-
Tốc độ bước tiến lớn (high feed rate)
-
Góc cắt mạnh mẽ
-
Lực cắt tập trung gia tăng theo hướng tâm
3.6. D.O.C và lực cắt
Mối liên hệ giữa bán kính mũi dao và độ sâu cắt D.O.C có ảnh hưởng đáng kể đến tình trạng rung khi gia công. Các lực tác động theo hướng tâm có thể đẩy insert ra khỏi bề mặt cắt và gây ra áp lực theo hướng trục khi độ sâu cắt tăng lên.
Việc tối ưu hóa lực tác động theo hướng dọc trục hơn là áp dụng lực hướng tâm sẽ giúp giảm thiểu các hiện tượng rung động và cải thiện chất lượng bề mặt sau quá trình gia công.
Theo nguyên tắc tổng quát, việc lựa chọn bán kính mũi RE bằng hoặc nhỏ hơn độ sâu cắt Ap sẽ đem lại hiệu quả tối ưu trong quá trình gia công.
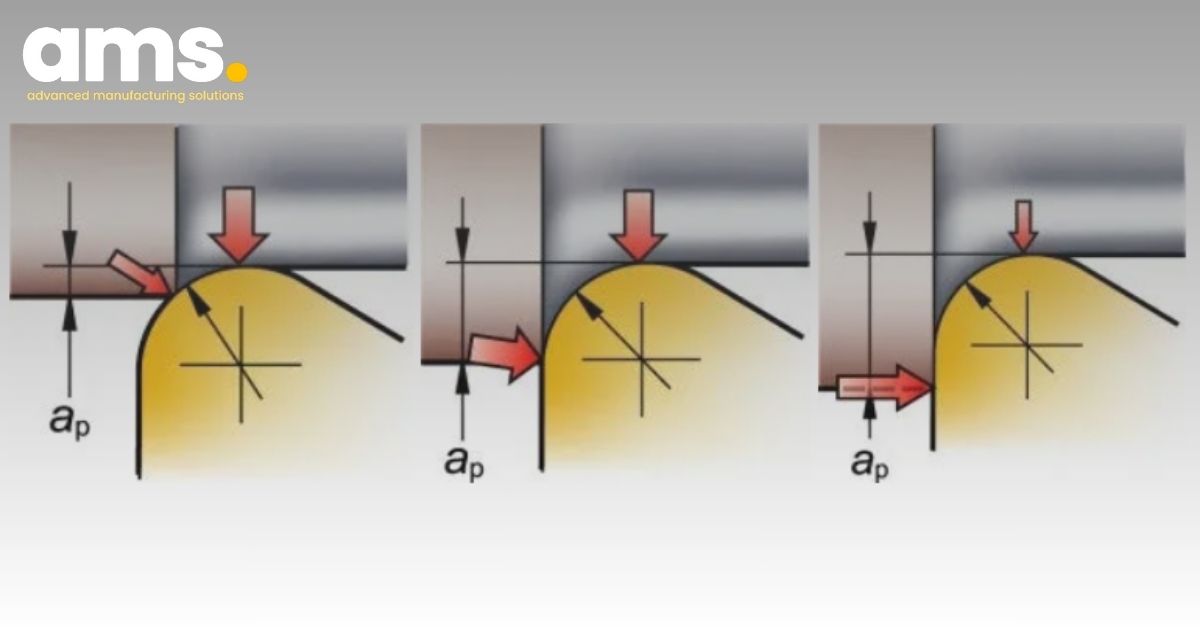
3.7. Insert một mặt hay hai mặt
Insert hai mặt (Negative Insert) được thiết kế với góc thoát phoi bằng 0°, trong khi đó, Insert một mặt (Positive Insert) có góc thoát phoi nhỏ hơn 90°. Hình minh họa của các loại Positive Insert và Negative Insert sẽ trực quan hóa cách mà chúng được lắp ráp vào cán dao và góc nghiêng khi tiếp xúc với phôi.
3.8. Góc tiếp xúc
Góc tiếp xúc KAPR (hoặc góc dẫn Lead PISR) là góc mà cạnh cắt tạo với hướng bước nạp. Việc lựa chọn góc vào/dẫn chính xác đóng vai trò quan trọng trong việc đảm bảo sự thành công của quy trình gia công. Các góc tiếp xúc KAPR và góc dẫn PISR sẽ ảnh hưởng đến hình dạng của phôi, hướng lực cắt, và chiều dài của cạnh cắt trong quá trình gia công.
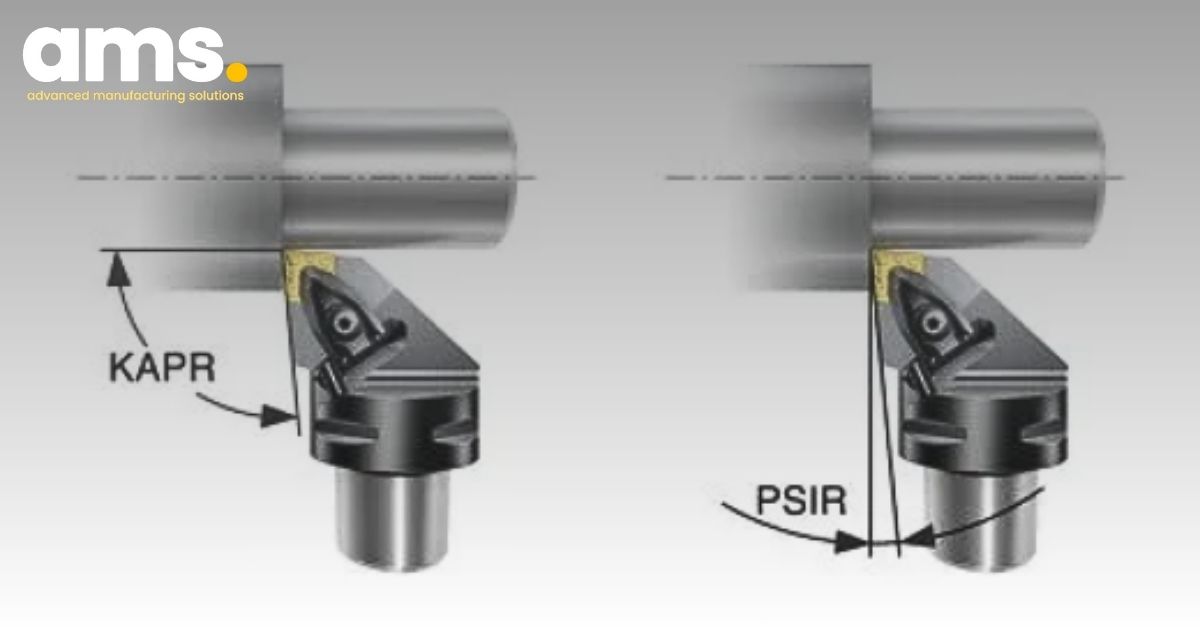
3.8.1. Góc tiếp xúc lớn (góc dẫn nhỏ)
Lực cắt được tập trung hướng về phía kẹp phôi, giảm thiểu xu hướng rung động và gia tăng khả năng tiện vai. Điều này cũng đi kèm với lực cắt tăng cao và đồng thời dễ bị mài mòn trong quá trình gia công các loại phôi như heat-resistant supper alloy và thép sau nhiệt.
3.8.2. Góc tiếp xúc nhỏ (góc dẫn lớn)
Các lực cắt tăng tỷ lệ theo hướng tâm khi tiếp xúc với phôi có thể gây ra hiện tượng rung và đồng thời giảm lực cắt chính. Để gia công các loại phôi mỏng và dẻo, có thể điều chỉnh tốc độ nạp cao hơn để giảm thiểu hiện tượng bẻ phoi, cũng như giảm mài mòn dao cụ. Tuy nhiên, không thể tiện vai với góc 90° trong trường hợp này.
4. Mũi Dao Cắt Hợp Kim Sandvik Coromant: Sự Kết Hợp Tối Ưu Cho Hiệu Suất Gia Công Vượt Trội
Các mũi dao cắt của Sandvik Coromant, bao gồm cả mũi dao cắt hợp kim, nổi tiếng với cấu trúc hàn chắc chắn, mang lại độ tin cậy và sự tự tin đặc biệt khi sử dụng. Những mũi dao này được thiết kế tỉ mỉ để phục vụ cho nhiều ứng dụng gia công khác nhau như tiện thô, tiện bán thành phẩm và tiện hoàn thiện. Thiết kế chắc chắn và cấu trúc chất lượng cao của những mũi dao này khiến chúng rất phù hợp cho nhiều nhiệm vụ cắt kim loại.
Chọn bán kính mũi dao và độ sâu cắt phù hợp có tác động đáng kể đến hiệu suất gia công. Chuyên môn của Sandvik Coromant trong lĩnh vực này đảm bảo rằng mối quan hệ giữa bán kính mũi dao và độ sâu cắt được tối ưu hóa để giảm thiểu hiện tượng rung và cải thiện chất lượng bề mặt sau gia công. Được thiết kế với độ chính xác cao, những mũi dao này giúp giảm thiểu hiện tượng rung và cải thiện chất lượng bề mặt sau khi gia công.
Ngoài ra, Sandvik Coromant cung cấp nhiều loại mũi dao khác nhau, bao gồm mũi dao hai mặt (âm) và mũi dao một mặt (dương). Mỗi loại mũi dao có góc nhả chip và cấu hình lắp ráp cụ thể, thể hiện cam kết của công ty về độ chính xác và tính linh hoạt trong các ứng dụng cắt kim loại.
Việc hiểu rõ về góc tiếp xúc và góc dẫn trong gia công là rất quan trọng để đạt được kết quả tối ưu. Hạt dao của Sandvik Coromant được thiết kế để giải quyết những vấn đề phức tạp liên quan đến góc tiếp xúc và góc dẫn, đảm bảo rằng hình dạng phôi, lực cắt và tuổi thọ dụng cụ đều được xem xét và tối ưu hóa cẩn thận để mang lại kết quả gia công vượt trội.
Các mũi dao của Sandvik Coromant cũng được thiết kế đặc biệt để tập trung lực cắt về phía kẹp phôi, giảm xu hướng rung và cải thiện khả năng gia công. Tuy nhiên, chúng cũng giải quyết các thách thức khi gia công các loại phôi như siêu hợp kim chịu nhiệt và thép sau khi được xử lý nhiệt, đem đến giải pháp giảm thiểu mài mòn dụng cụ và nâng cao năng suất tổng thể.
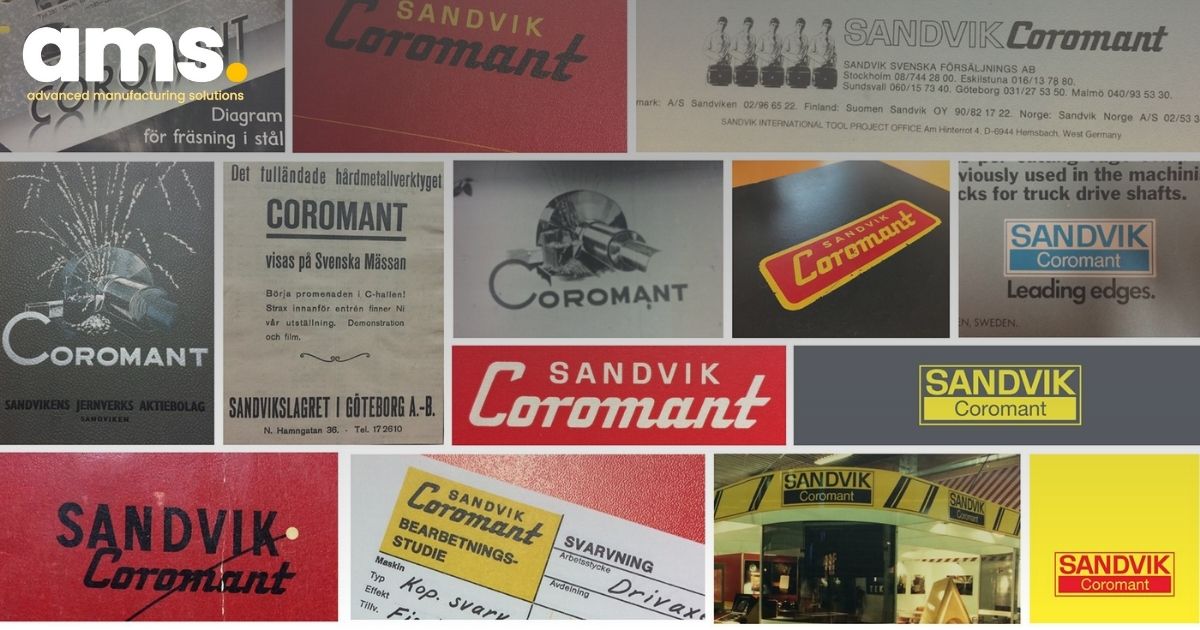
Trong suốt hơn 20 năm qua, Công ty TNHH Thương mại và Dịch vụ Kỹ thuật AMS đã là đơn vị phân phối tin cậy của các sản phẩm của Sandvik Coromant tại Việt Nam, phục vụ những nhu cầu chính xác của ngành cơ khí. Với sự giàu kinh nghiệm và cam kết với chất lượng, Công ty AMS là nguồn cung cấp hàng đầu để tiếp cận toàn bộ loạt sản phẩm công cụ cắt chính xác và mảnh dao của Sandvik Coromant. Cho dù bạn đang tìm kiếm các giải pháp tiên tiến cho hoạt động gia công của mình hay tư vấn chuyên sâu về lựa chọn công cụ, Công ty AMS sẽ là đối tác đáng tin cậy của bạn, mang đến những giải pháp xuất sắc trong các ứng dụng cơ khí chính xác.
Công ty TNHH Thương mại và Dịch vụ Kỹ thuật A.M.S243/9/10D Tô Hiến Thành, phường 13, quận 10
Hot line: 028.3868 3738/3903 - Fax: 028.3868 3797