What is an encoder? Structure, operating principle and application
What is an Encoder? What is its Structure, Working Principle, and Application? This article provides a comprehensive overview of the technical aspects of encoders, including their structure, operating principles, and applications. It also offers insights into choosing high-quality, reliable, and authentic encoders.
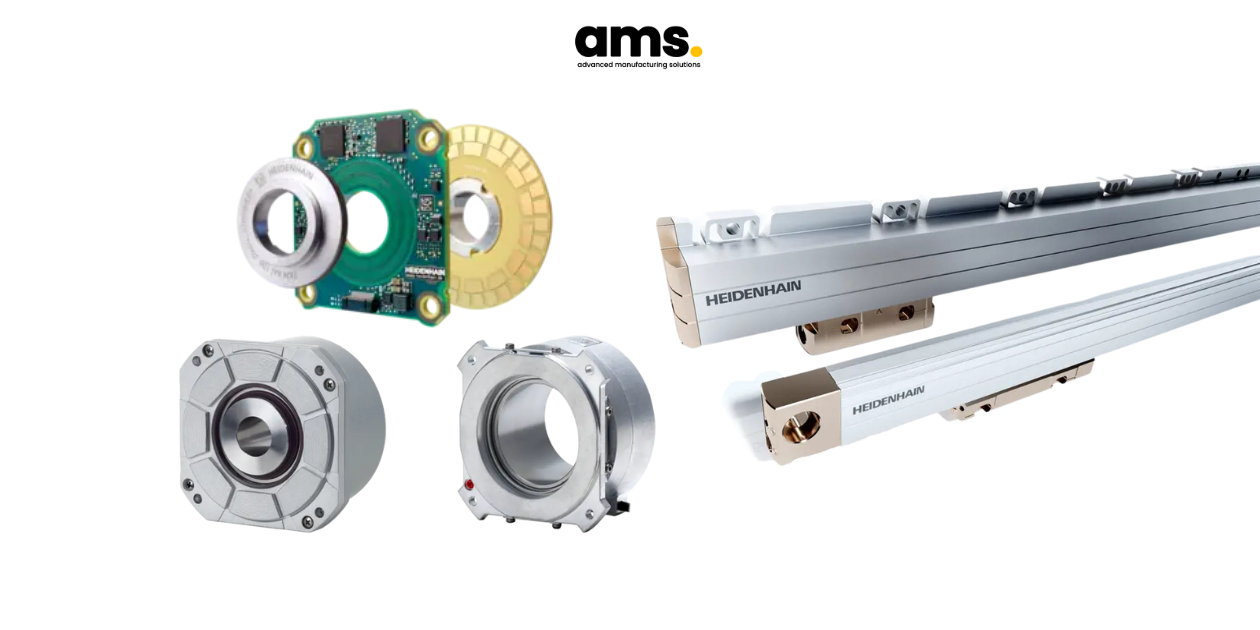
1. What is an Encoder?
What is an Encoder? This is a common question that arises in the fields of digital electronics and signal processing. An encoder is a device that converts information from one format or code to another, typically converting physical motion or position into digital signals. The conversion process carried out by an encoder is crucial and indispensable for standardization, speed, and compression across various technological applications. For technicians to precisely control and automate systems, the conversion of mechanical motion into readable electronic data is a fundamental step. Below are the types of information that encoders translate in motion control and automation systems:
-
Position: The current position of the shaft is determined by the measurement provided by the encoder, the spindle or other moving components.
-
Speed: The control system can determine the speed of movement thanks to the encoder which can analyze the rate of change of the output signal.
-
Direction: the directions will depend on the type of encoder, for rotary encoders the output will indicate clockwise or counterclockwise movement; for linear encoders the output will indicate forward or reverse.
Understanding encoders is not just about their basic functions. A technician should have a deep understanding of their inner workings, once you understand the structure and operation of an encoder, you will be better equipped to work with encoders. Besides, encoders are classified as absolute or incremental, depending on their output signals.
>> See more: Why Heidenhain Encoders Are the Top Choice in Production Lines
2. Structure of encoder
Each type of encoder will have different main components and functions, but in general there are 3 main components as follows:
-
Sensor element: This is the part that has the function of physical movement and converting it into an electrical signal.
-
Signal converter: This is the part that has the function of physically converting the detected movements into an electrical signal.
-
Output interface: This circuit processes the raw signal from the sensor and transmits that signal to the control system.
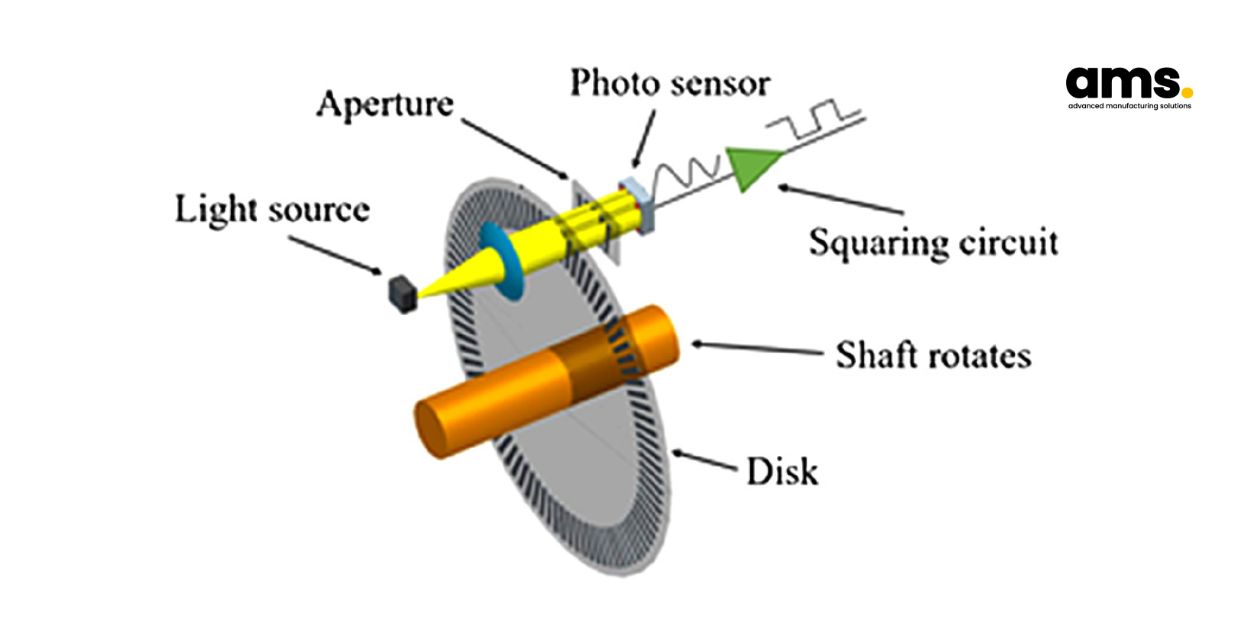
3. Working Principle of an Encoder
The working principle of an encoder is to convert physical motion into a readable format. For example, in a rotary encoder, the rotational movement of the shaft is detected by the sensor element, which then generates a corresponding electrical signal. Specifically, this signal is produced as the sensor detects a light source turning on and off continuously, creating square wave pulses. The encoder records the number and speed of these pulses. This signal is transmitted to a central processor (such as a microcontroller, PLC, etc.), where it is converted into a digital format to enable precise monitoring and control of mechanical motion. Connectors are used to transmit the electrical signals between the encoder and the control device, while couplings isolate the encoder from the impact of machine shocks and vibrations.
4. Applications of Encoders
Some prominent practical applications of encoders include:
-
Speed Indication: Inverters installed in a pump used to transfer liquid into a storage tank require a specific flow rate. Here, the encoder connects to the inverter and provides feedback on the actual flow rate of the liquid.
-
Measurement: In the manufacturing industry, companies using CNC machines for metal cutting and machining often employ encoders mounted on conveyor belts. These encoders can detect materials as they pass by and measure the product length.
5. Types of encoders
5.1. Rotary Encoders
Rotary encoders, also known as shaft encoders, are responsible for measuring the rotational position or angular movement of an object. Fields that commonly use rotary encoders include motor feedback, robotics, and automation.
Rotary encoders are categorized into two types: incremental and absolute. Incremental encoders provide relative angular position information by generating a series of pulses as the shaft rotates, while absolute encoders offer a unique position value for each shaft position, ensuring precise and repeatable measurements.
5.2. Linear Encoders
Linear encoders are designed to measure position along a straight line and are frequently used in CNC machines, precision measuring instruments, and automated assembly lines. Linear encoders can be optical or magnetic. Optical linear encoders provide high resolution and accuracy, whereas magnetic linear encoders are known for their durability in harsh environments.
5.3. Optical Encoders
To detect positional changes with high resolution and accuracy, optical encoders use light as a key element in their operation. They are widely used in semiconductor manufacturing and laboratory equipment. Optical encoders can be either rotary or linear, depending on the application.
5.4. Magnetic Encoders
Magnetic encoders determine position using a magnetic field, allowing them to operate effectively in harsh environments with dust, dirt, and moisture. Magnetic encoders are commonly used in automotive, heavy machinery, and outdoor equipment applications.
The table below compares the differences between these types of encoders:
Type | Resolution | Accuracy | Typical Applications | Output Signal | Suitable Environment | Suggestions |
Rotary Encoder | High (up to 10,000 CPR) | High | Motor feedback, Robotics, Automation | Digital pulses, Similar signals | Indoors, Controlled environment | ERN 1387, ECN 413, RON 287, RCN 2391F, ERN 120 |
Linear Encoder | High (up to 1 µm) | High | CNC Machines, Precision measuring tools | Digital pulses, Similar signals | Indoors, Controlled environment | LS 487, LB 302C, LC 483, LC 185, LC 193M |
Optical Encoder | Very high (up to 20,000 CPR) | Very high | Semiconductor manufacturing, Laboratory equipment | Digital pulses, Similar signals | Clean, Controlled environment | |
Magnetic Encoder | Medium (up to 1,024 CPR) | Medium to high | Automotive, Heavy machinery | Digital pulses, Analog signals | Harsh, Outdoor environment |
6. Technical Specifications to Consider When Purchasing an Encoder
After distinguishing and understanding the characteristics of each encoder type, you need to pay attention to several technical specifications to select the appropriate encoder for your needs.
-
Shaft Diameter: Shaft diameters range from 5 to 50 mm.
-
Shaft Type: The shaft can be either recessed (negative) or protruding (positive).
-
Resolution (Pulses): This corresponds to the number of encoder signals that can be counted in one full rotation. The typical pulse count for elevators is usually 1024 pulses/revolution, while for machine manufacturing, it can be around 360 or 1000 pulses/revolution. Additionally, there are encoders that can provide up to 6000 pulses/revolution or more.
-
Voltage: Choose the correct power supply to prevent burning out the encoder during installation, which would require replacing the entire unit. If the encoder has a voltage range of 5-24V, it is quite easy. However, for larger shaft encoders (30-40 mm), it is common to encounter specific voltage requirements of 5V, 12V, or 15V.
7. Which Brand of Encoder Should You Purchase?
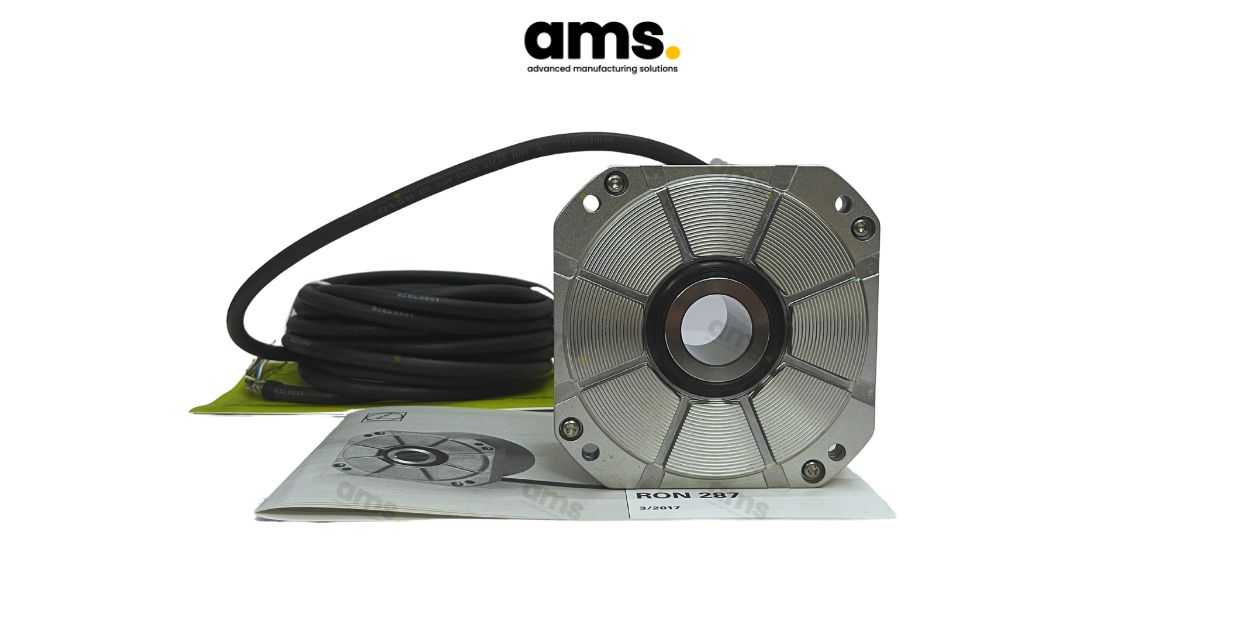
Encoders from the Heidenhain brand are AMS's top recommended choice for you. We understand that there are many distributors offering various encoder product lines today. However, there are valid reasons why we suggest this brand's products to our partners and customers:
Heidenhain is a reputable, long-established brand from Germany, the "home" of the best machinery and industrial equipment manufacturing companies in Europe, with a record sales figure of 260 billion euros in 2021. Situated in the promising cradle of a manufacturing and high-tech boom, Heidenhain has a history spanning several decades, producing sustainable, high-quality products that reflect its brand prestige, especially in rotary encoders and linear encoders.
AMS takes pride in being the exclusive distributor for Heidenhain in Vietnam, committed to providing advanced manufacturing solutions for our partners and customers. In addition to understanding our partners' desire for high-quality products, AMS excels in offering tailored advice for specific technical issues, purchasing policies, delivery, and customer care.
Contact AMS today for detailed consultation on Encoder product information!
>> Learn more: AMS distributes a wide range of Heidenhain products
8. Conclusion
Encoders have become familiar components in the precision engineering industry. Through this article, AMS hopes that our partners and customers will find useful and valuable information that contains what you are looking for. Stay tuned with us to keep updated on the latest news and useful technical knowledge in the precision engineering field to support stronger manufacturing development!
AMS Company, Ltd.243/9/10D To Hien Thanh, Ward 13, District 10
Hot line: 028.3868 3738/3903 - Fax: 028.3868 3797