Why Heidenhain Encoders Are the Top Choice in Production Lines
Encoders are products used in industrial production, bringing high efficiency to the line. Encoder products from the Heidenhain brand always receive the attention of many customers because of their high applicability, efficiency and durability over time. Let's find out why Heidenhain Encoders are always the top choice.
1. What is an Encoder?
To start, let's find out what an Encoder is? Encoders are known as mechanical motion sensors that creates digital signals that respond to physical movements. Encoders have the function of converting motion signals into digital signals, transmitting them to the system's electronic processor.
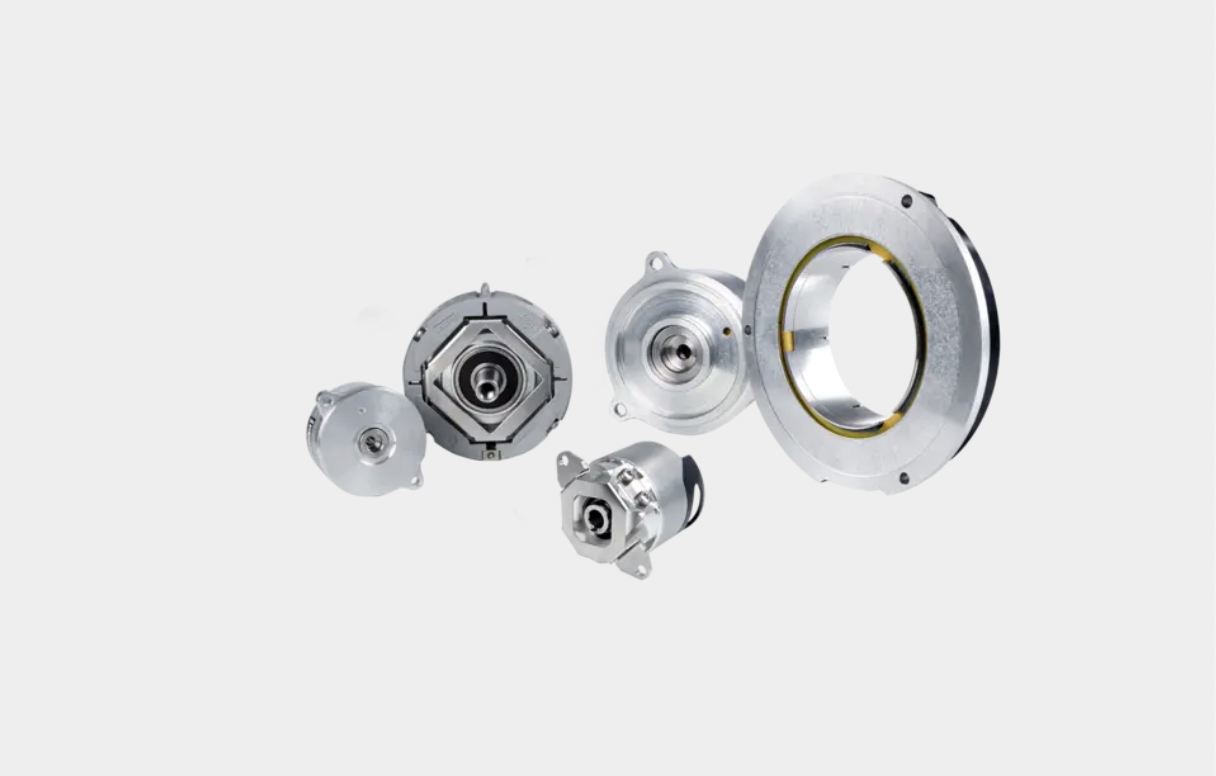
Encoders are important parts of CNC machines, with the task of measuring the parameters and working speed of the machine, counting the number of products produced. Therefore, in the CNC industry, fully automated operations are achieved by integrating encoders.
In addition to applications in CNC machines, Encoders are also applied in the following industries:
-
Speed display application: reflects the flow rate of liquid and transmits signals to the inverter to operate the pump.
-
Dimension measurement application: encoders are installed on aluminum plate conveyors, used to determine the position with high precision, and measure the length of the material plate to be cut.
-
Application of encoders in quantity counting: encoders are installed on product conveyors to count the number of products passing through.
-
Application of encoders in industries: application to control car speed; application in office equipment such as scanners, printers; applications in medical scanners, positioning in telescope equipment, etc.
2. Encoder structure
In terms of structure, the Encoder has a fairly simple structure with the following 5 parts:
-
1 round disc with small holes machined with equivalent sizes and at a specified position with the same radius. The round disc can rotate around a fixed axis at a constant speed.
-
1 LED light is arranged near the rotating disc
-
1 light sensor is arranged in the opposite position
-
Encoder housing
-
Digital signal transmission wire
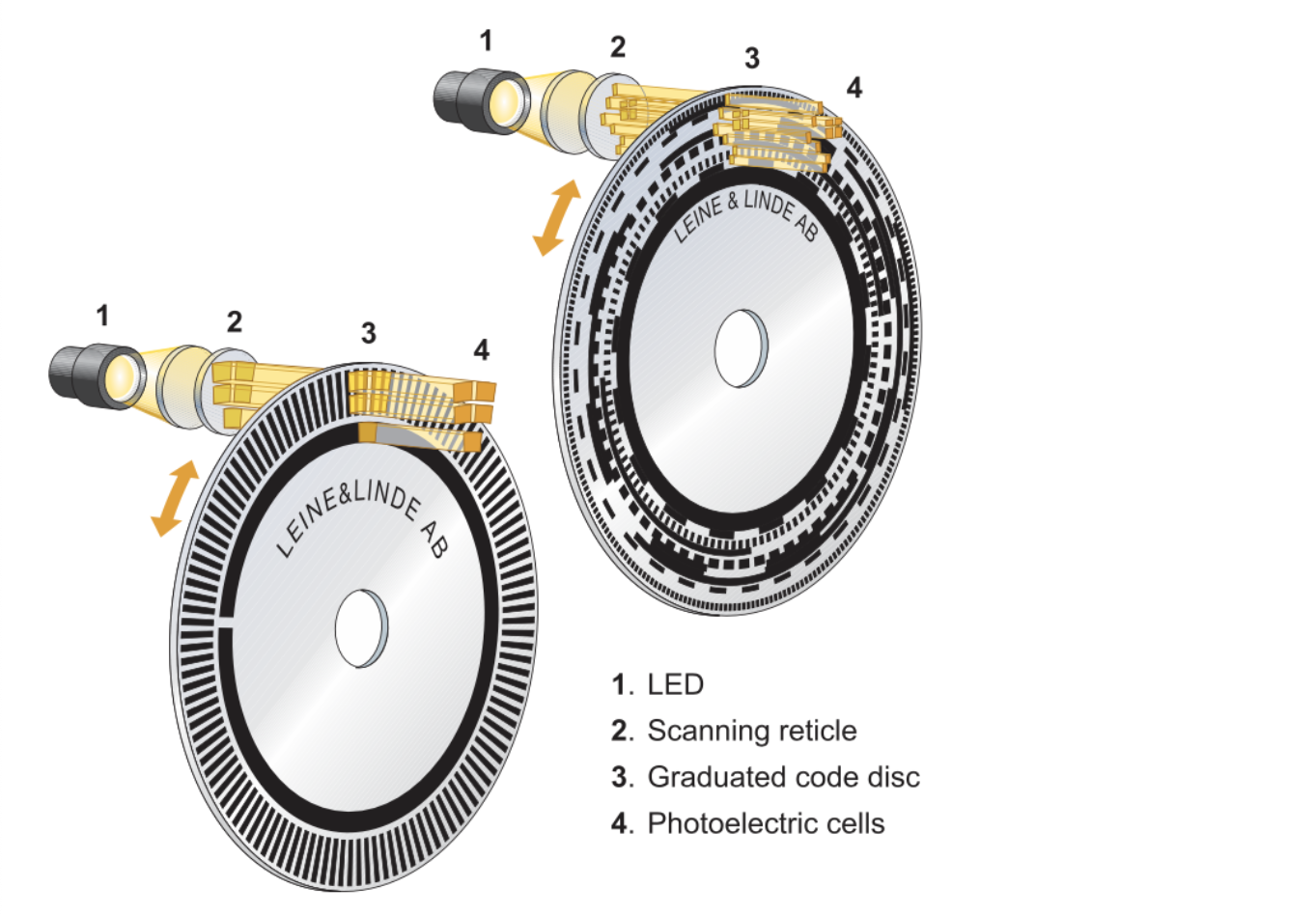
3. Encoder operating principle
The Encoder operating principle is based on optical signals. On the round disc there are holes for LED light to pass through and holes for no light to pass through. From there, the signal will be transmitted to the light sensor. The number counted will be determined by the number of times the light is cut. The light sensor operates to generate square pulses, convert them into digital signals, and transmit them to the central processor. From there, the computer will determine the speed of the motor.
4. How Heidenhain Encoder is applied in precision measurement in machine tools
As mentioned above, the Encoder has the function of distinguishing and transmitting position and speed through two main methods, mainly based on the interaction between the fixed disk or scale and the disk moving according to the load. Based on the operating principle of the encoder, it can be divided into two main types: Relative encoder and Absolute encoder.
The classification is based on the light interaction mechanism in the case of Optical Encoder, while Magnetic Encoder uses magnetization patterns, in which changes in resistance are signaled to the controller. Optical Encoder usually uses glass scales, in contrast to the application of steel in Magnetic Encoder. These differences are essential to understand the modes, through which Heidenhain Encoder easily recognizes position and speed in machine tool operations.
4.1. Heidenhain relative encoder
Relative encoders generate signals incrementally or periodically. Relative encoders have a maximum of 3 turns of the disc. The advantage is that they are cheap and the signal returns quickly, but because they are relative signals, they do not guarantee absolute accuracy and are limited by the information provided, so additional reference devices are required to calculate the movement. Many types of Heidenhain encoders incorporate reference marks that are encoded at different distances according to a mathematical algorithm. By passing through two consecutive reference marks, the electronics can determine the absolute reference marks, which is consistent with the performance of the Heidenhain encoder.
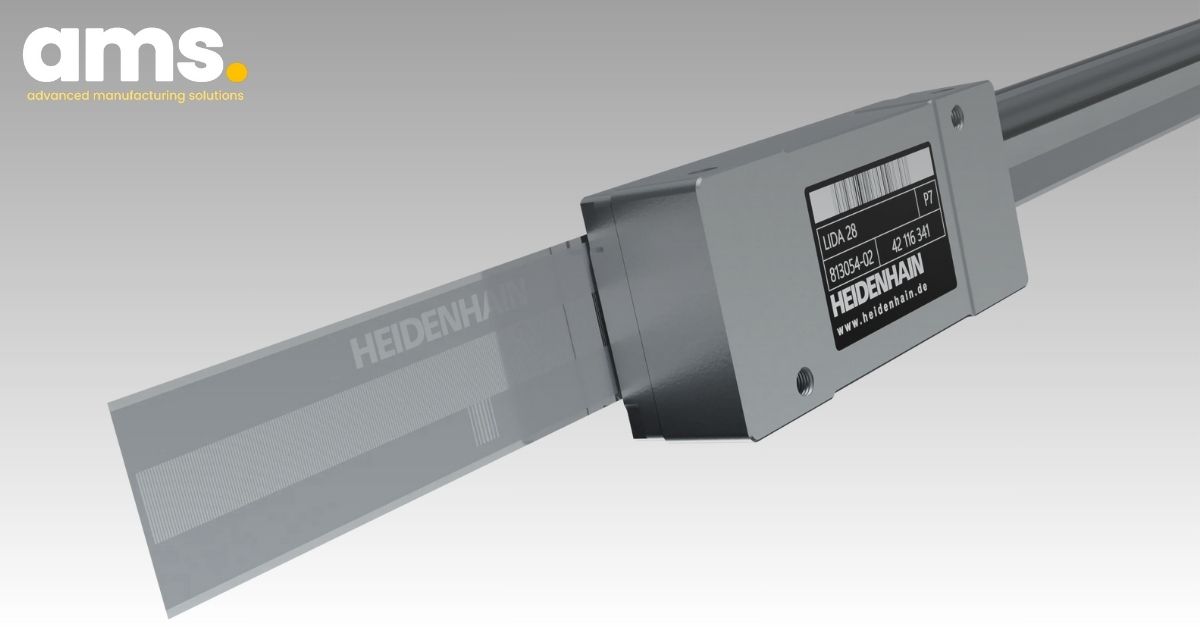
Relative encoders use more uniform gratings to relay relative positions. Positions are established through the use of reference marks scattered throughout the sample. Therefore, machine parts using this type of encoder all need to set the zero point before starting work. They provide us with excellent speed and distance feedback. Because there are few sensors involved, the structure is quite simple and saves costs for users. This is also a type of Encoder that is quite commonly used in the Vietnamese market.
4.2. Heidenhain Absolute Encoder
Absolute Encoder uses a gray code binary disk, made from transparent material with concentric circular holes. The ability to return signals with high accuracy so users do not need to process steps like with Relative Encoder. However, the manufacturing of Absolute Encoder is complicated and expensive.
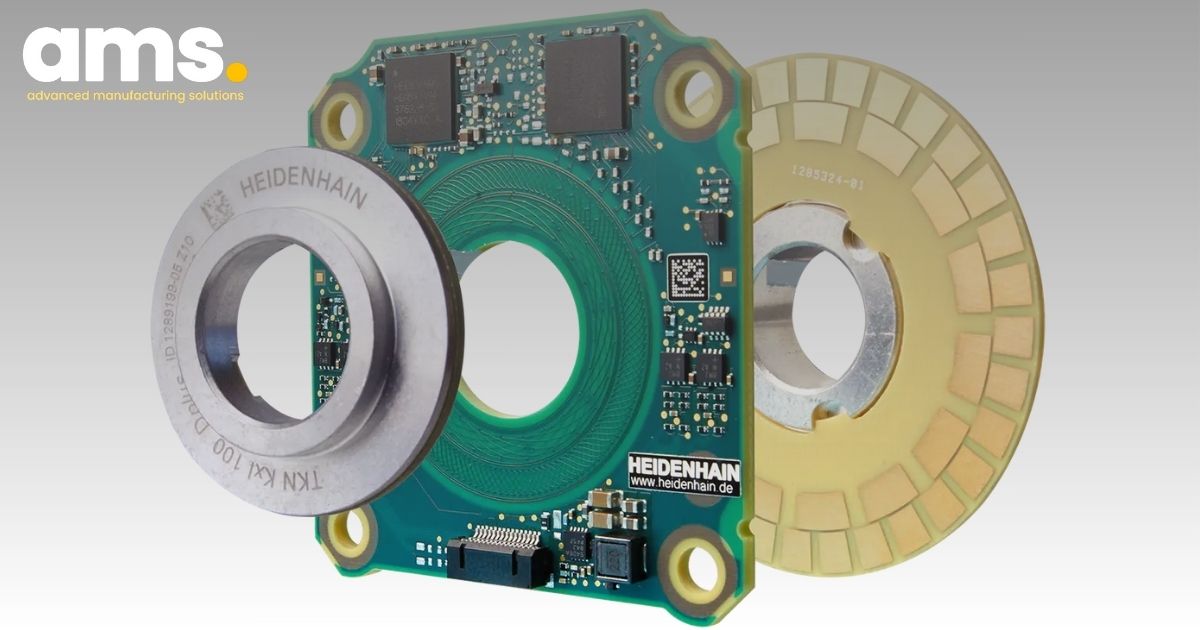
Absolute Encoder works by outputting a digital word of bit as the shaft rotates. There are two disks, both with concentric rings with offset markers. One disk is fixed to the central shaft, the other disk is free to move. As the disk rotates, the markers along the encoder track change position on the fixed disk. Each profile along the disk of the absolute rotary encoder represents a unique binary code. Looking at the binary code in the rotary encoder will determine the absolute position of the object.
5. How Heidenhain Encoders are applied in precision measurement in CNC machines
CNC machine tools rely heavily on a harmonious combination of speed, accuracy and repeatability. And the Encoder plays a key role in combining the above factors by providing position feedback to the controller. Heidenhain Encoders always do these tasks well, providing accurate position feedback to the controller and the operator can clearly grasp the information.
Heidenhain Encoders include Linear Encoders, Rotary Encoders and Angular Encoders that control the tasks of providing feedback to the CNC machine system. Each type of Encoder has the function of monitoring specific aspects of the machine's motion, taking into account factors such as the required accuracy and flexibility. The performance of CNC machine tools depends heavily on these various Encoder mechanisms, while providing accurate and consistent feedback readings.
5.1. Heidenhain Angle Encoder
Angle encoders are used to precisely measure the alignment between two components, typically with an accuracy of better than ±10" (arcseconds). Heidenhain offers angle encoders that can achieve an exceptional accuracy of ±0.04" (arcseconds). This extraordinary accuracy makes angle encoders indispensable in the development of multi-axis centers. Whether these components move simultaneously or independently, the design of the rotary table and rotary head often incorporates this type of encoder.
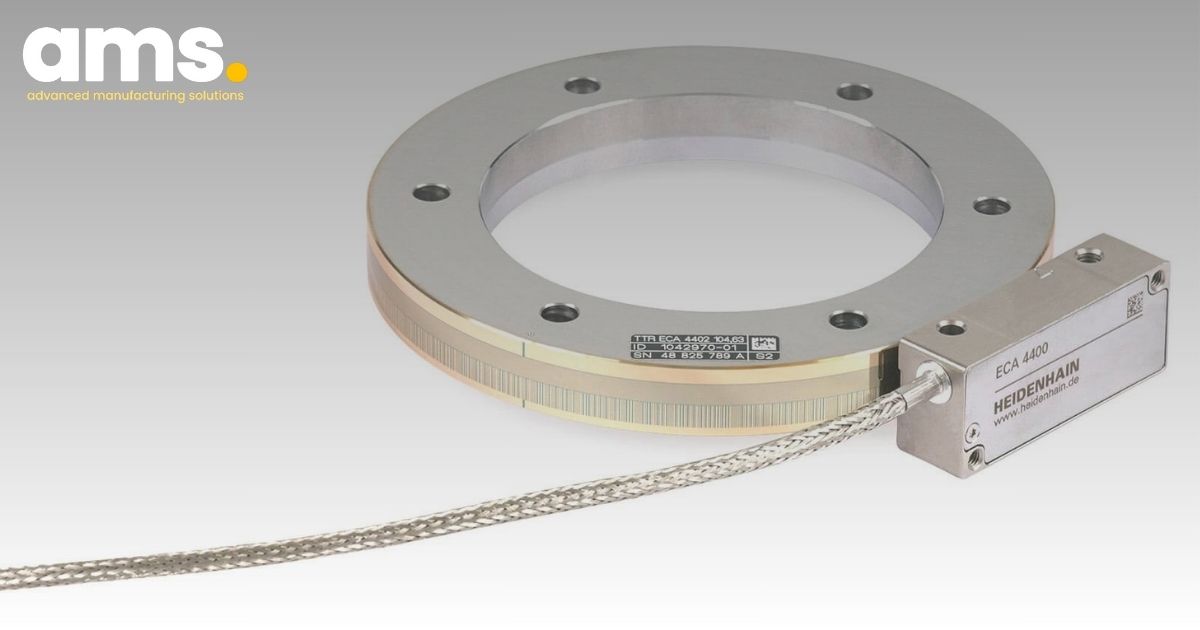
Angle encoders are commonly used in machine tool rotary tables and rotary heads, indexing heads, high-precision angle measuring tables, precision devices for angle measurement, antennas and telescopes.
-
Number of lines: typically 9000 to 180000
-
Accuracy: ±5" to ±0.4"
-
Measurement steps: as small as 0.00001° or 0.036” (incremental) or 29 bits, i.e., approx. 536 million positions per revolution (absolute)
5.2. Heidenhain Rotary Encoders
Rotary encoders are designed to measure rotational angles, although with relatively lower accuracy, typically providing accuracies of over ±10” (arcseconds). While angle encoders specialize in precision positioning, rotary encoders are often preferred for speed control applications. In the machine tool industry, they are particularly valuable for monitoring spindle revolutions per minute (RPM), a key metric for understanding and improving critical metrics such as speed, tool wear, and energy consumption.
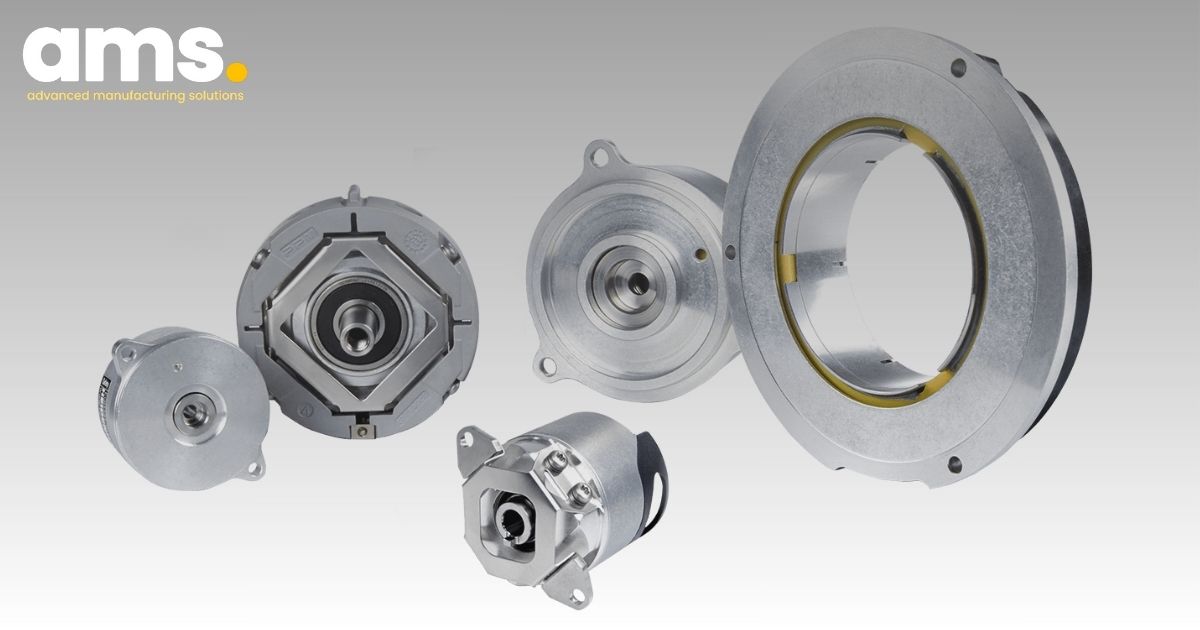
Rotary encoders are commonly used in a wide range of applications, including electric motors, machine tools, printing machines, woodworking machines, textile machines, robots, elevators and handling equipment, as well as various types of measuring, testing and inspection equipment.
-
Number of lines: typically from 16 to 5000
-
Accuracy level: up to ±10” (depending on the number of lines, corresponding to ±1/20 of the grating period)
-
Measurement steps: as small as 0.00001°
5.3. Heidenhain linear encoder
Linear encoders measure distances in a straight line. One difference lies in the choice between an encoder without any protective structure and an encoder with a protective structure. However, the latter option is considered the only option in the harsh working conditions of the machining industry. The enclosed Encoder unit is mounted on a small carriage directly connected to the machine slide, moving with the table to protect the sensors and scanning devices from the workpiece and coolant, while providing precise position information to the controller.
The enclosed linear encoder provides optimal protection against dust, debris and splashes of water. They are particularly ideal for use in both manually operated and numerically controlled machine tools.
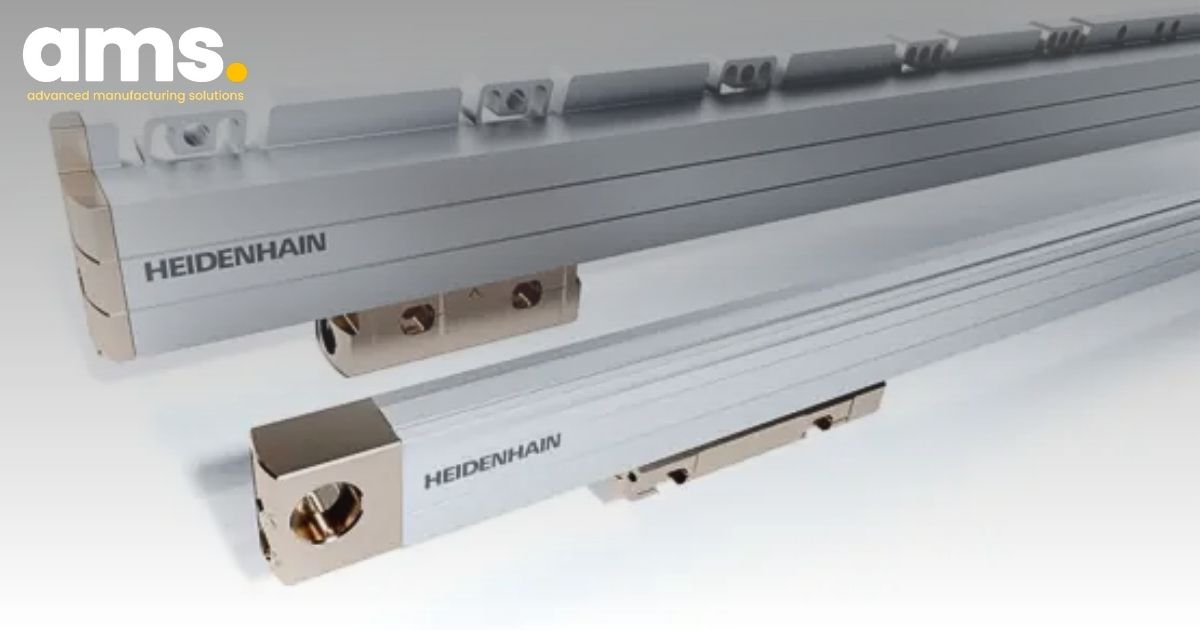
6. AMS Company Ltd - Exclusive Distributor of Heidenhain in Vietnam
AMS is honored to be the exclusive distributor of Heidenhain products in the Vietnamese market. With a reputation as a leading supplier of precision measuring and control equipment, we are committed to providing quality and reliable Heidenhain products that have been affirmed in the market.
Please contact AMS immediately to receive professional advice on choosing the Heidenhain encoder that suits your specific business needs. Our dedicated team of experts is always willing to learn and propose the most optimal solutions for you.
AMS Company, Ltd.243/9/10D To Hien Thanh, Ward 13, District 10
Hotline: 028.3868 3738/3903 - Fax: 028.3868 3797