Insight into Tapping tools: Understanding the Structure and Classifications for Mechanical Applications
In the field of mechanical engineering, the terms "tapping" and "tap" are widely recognized. However, distinguishing between these concepts often leads to confusion.

Tapping refers to the process of creating threads and is commonly used for this purpose. Currently, taps are utilized for producing external threads or creating internal hole threads. Therefore, a tap is considered a tool, while tapping is categorized as an operation within the context of the technological process.
1. Tapping Tool Classification
Various methods are used to categorize tapping tools, with the most common approach being based on the following criteria:

1.1 Based on the Processing Method
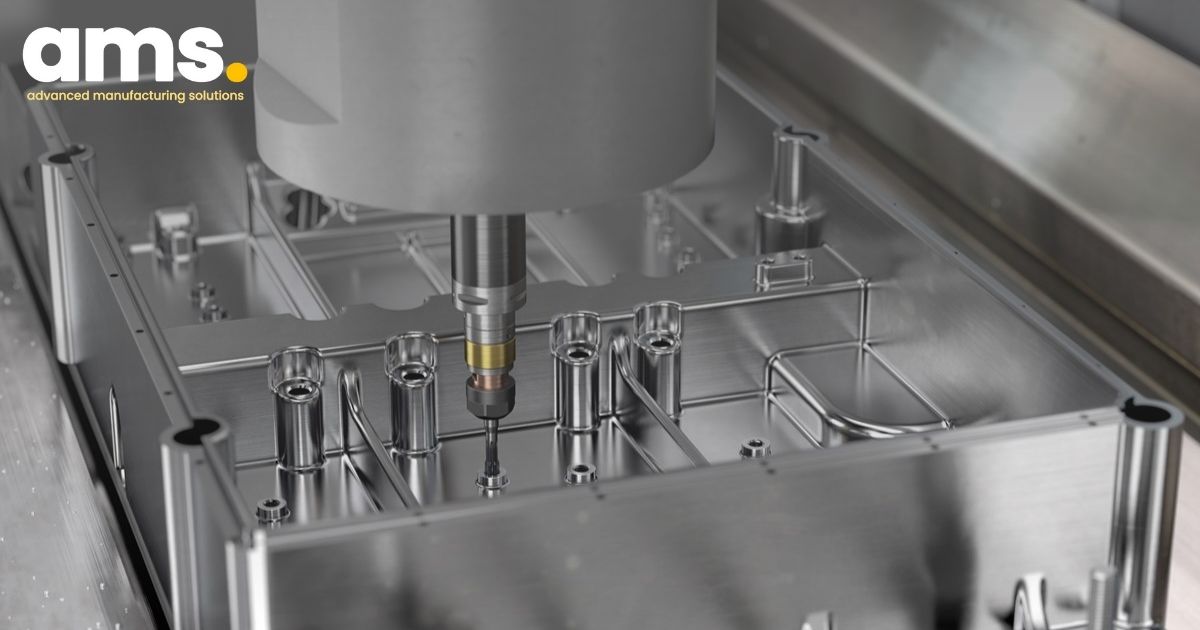
Tapping tools can be classified into two main types based on the processing method: machine taps and hand taps.
Machine tapping involves the use of machine tools such as CNC milling machines, CNC lathes, milling machines, tapping drilling machines, and similar equipment. This category exclusively employs straight taps or spiral taps. Straight taps are utilized for machining through holes, while spiral taps are employed for machining blind holes.
On the other hand, hand taps are manually operated and often paired with a tap wrench. Formerly, hand taps were available in three variations (coarse, semi-finished, and fine), but advancements in materials and geometric designs have led to the necessity for only one type of hand tap. The advantages of using a single hand tap include speed and compatibility with running machines when required, particularly for managing cut material chips. Hand tapping generates fine chips, making it suitable for tapping blind or through holes.
1.2 Based on Thread Characteristics
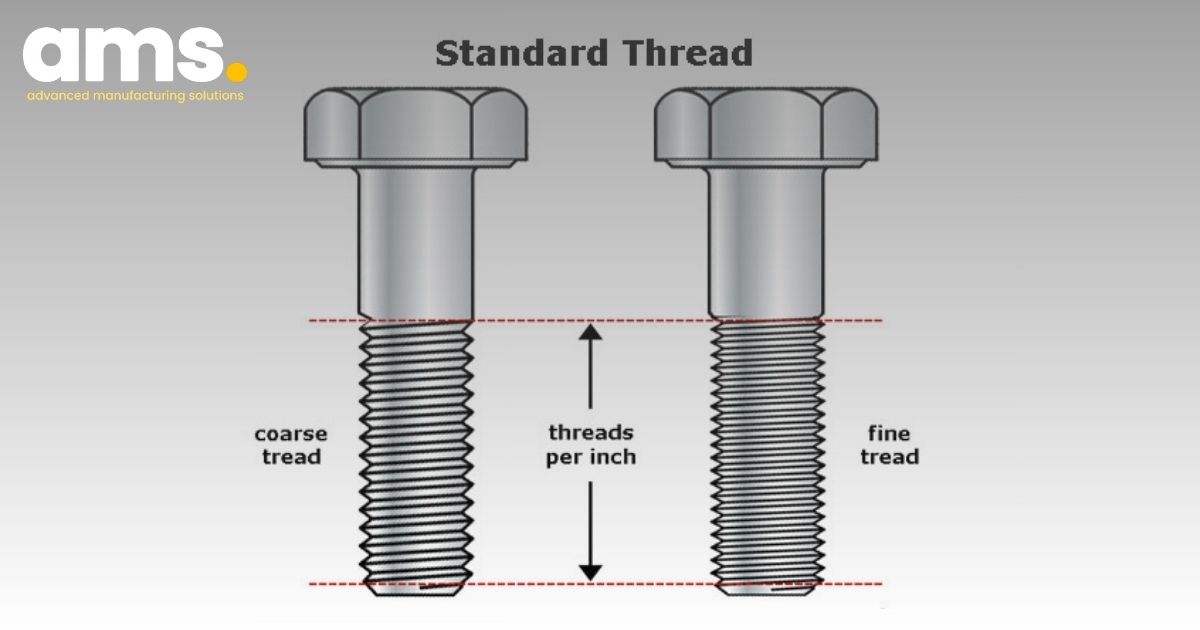
Taps are commonly classified based on the thread pitch into standard pitch taps and fine pitch taps, also known as fine thread taps.
Standard pitch taps, such as M10x1.5 and M8x1.25, are widely used.
Fine pitch taps, like M10x1.25 and M8x1, have a smaller pitch compared to the standard pitch taps.
Both types of taps find extensive application in threading gas and water lines, as well as in the food industry to ensure secure threaded joints and prevent leaks.
1.3 Based on Thread Direction
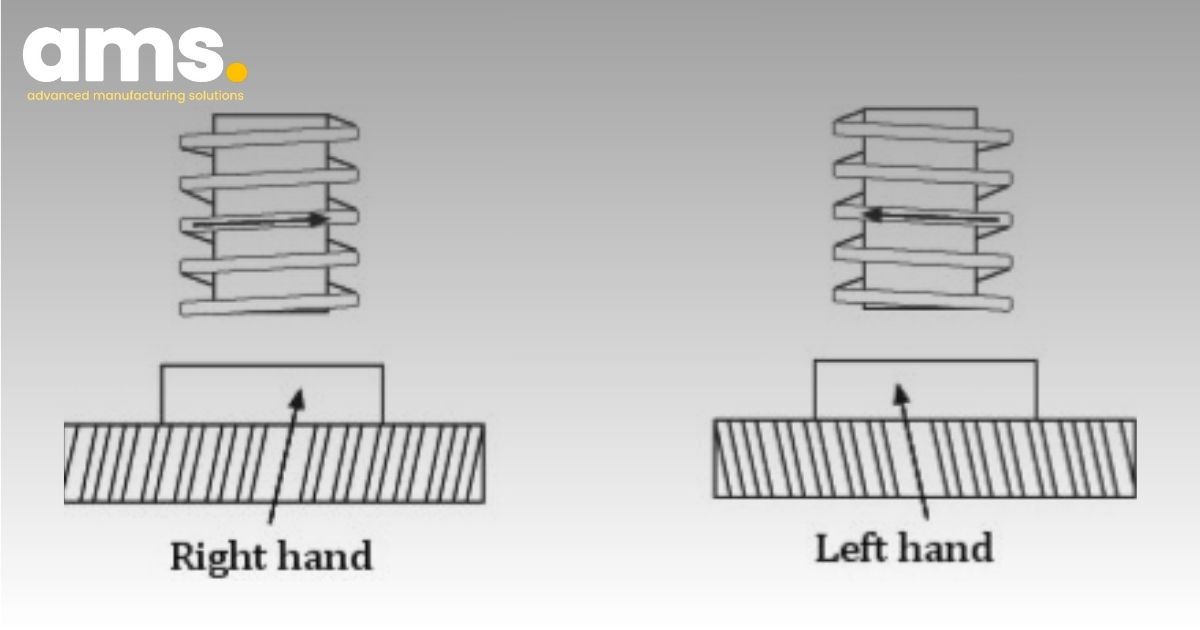
Taps can also be categorized based on thread direction into right-thread taps and left-thread taps. The right-threaded tap features a clockwise thread and is commonly utilized. Conversely, the left-threaded tap has a counter-clockwise thread and is often employed in copper transfer thread joints, such as rotor threads or glass joints in motorcycles.
1.4 Based on Material Processing

Depending on the type of processing material, taps are manufactured from distinct billet types such as scrap billet or wire billet, each possessing varying hardness characteristics.
Common classifications encompass regular steel taps, hardened steel taps, stainless steel taps, aluminum + copper taps, and cast iron taps.
When engaging in large-scale and batch machining, selecting the appropriate tap suited for the material is crucial to ensure tap longevity, product quality, and machining productivity.
1.5 Based on Thread Standards

Different standards for thread usage are applied within each region or country.
While commonly referred to as MET and INCH tap taps, the reality is more nuanced. The MET tap tap is prevalent in Asia and is a popular tap type in Vietnam, typically denoted by the letter M. Conversely, the INCH tap tap is utilized in Europe, America, and Australia. However, each region and country has specific standards pertaining to tap and thread selection.
1.6 Based on Chip Classification
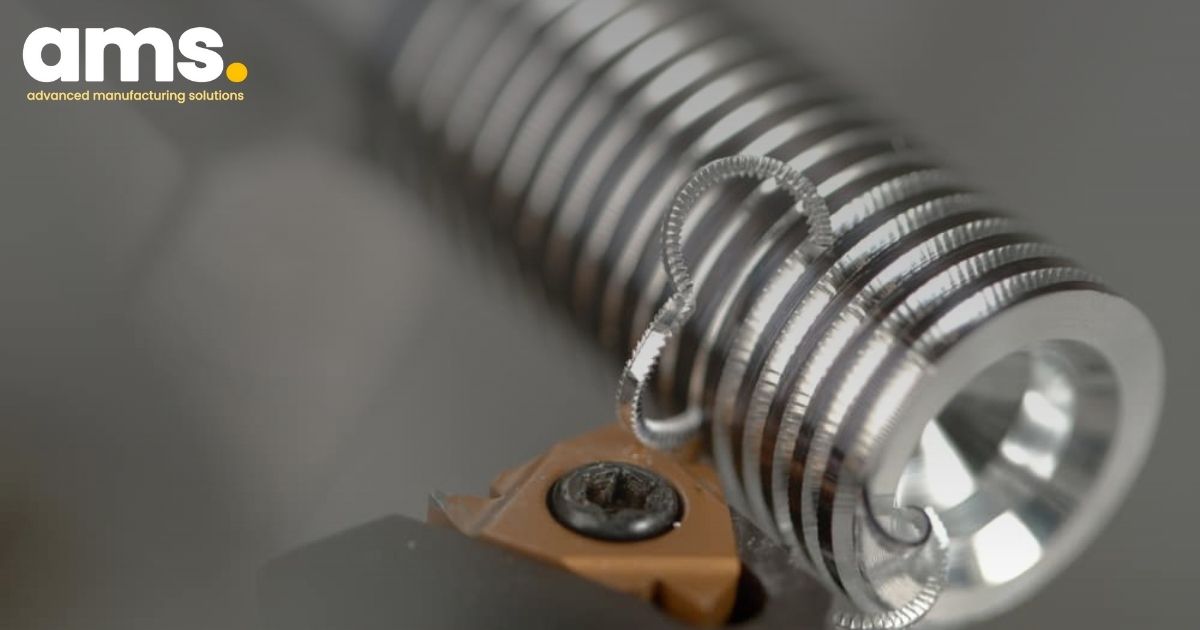
Taps can be categorized into cutting taps and forming taps based on the processing method. A cutting tap is employed to create chips, whereas a forming tap doesn't produce chips but instead compresses them.
The current market offers a diverse range of taps with varying sizes, applications, and specifications to cater to the diverse processing requirements of consumers.
2. Introducing Sandvik Coromant Tapping Tools

As the official distributor of Sandvik Coromant in Vietnam, AMS Company Limited brings over 20 years of invaluable experience in the precision mechanical industry to the forefront. Sandvik Coromant, a global leader in cutting tools and tooling systems, offers a comprehensive range of tappets designed to meet the demands of various machining applications. With a focus on precision, efficiency, and innovation, Sandvik Coromant has established itself as a trusted brand in the realm of metal cutting and machining solutions.
Understanding the significance of selecting the right tap for specific applications,AMS Company Limited takes pride in its ability to provide expert advice and consultation to customers seeking the most suitable tappets for their machining needs. Whether it's threading, hole-making, or other machining processes, Sandvik Coromant tappets are engineered to deliver high performance, reliability, and productivity.
2.1 Sandvik Coromant CoroTap Product Lines
Sandvik Coromant offers a diverse range of tappet product lines, each tailored to address specific machining requirements. Some notable tappet product lines from Sandvik Coromant include:
-
CoroTap: Designed for a wide range of materials and applications, the CoroTap series delivers exceptional performance, thread quality, and process security. These tappets are engineered to optimize chip evacuation and enhance tool life, making them suitable for various threading operations.
-
CoroTap 300: With a focus on versatility and versatility, the CoroTap 300 series offers reliable threading solutions for both internal and external threading applications. Featuring high precision and cutting-edge technology, these tappets are designed to meet the demands of modern machining environments.
-
CoroTap 400: Engineered for high productivity and performance, the CoroTap 400 series is equipped with advanced features to ensure efficient chip control, reduced cutting forces, and superior thread quality. These tappets are ideal for high-speed tapping operations and demanding machining tasks.
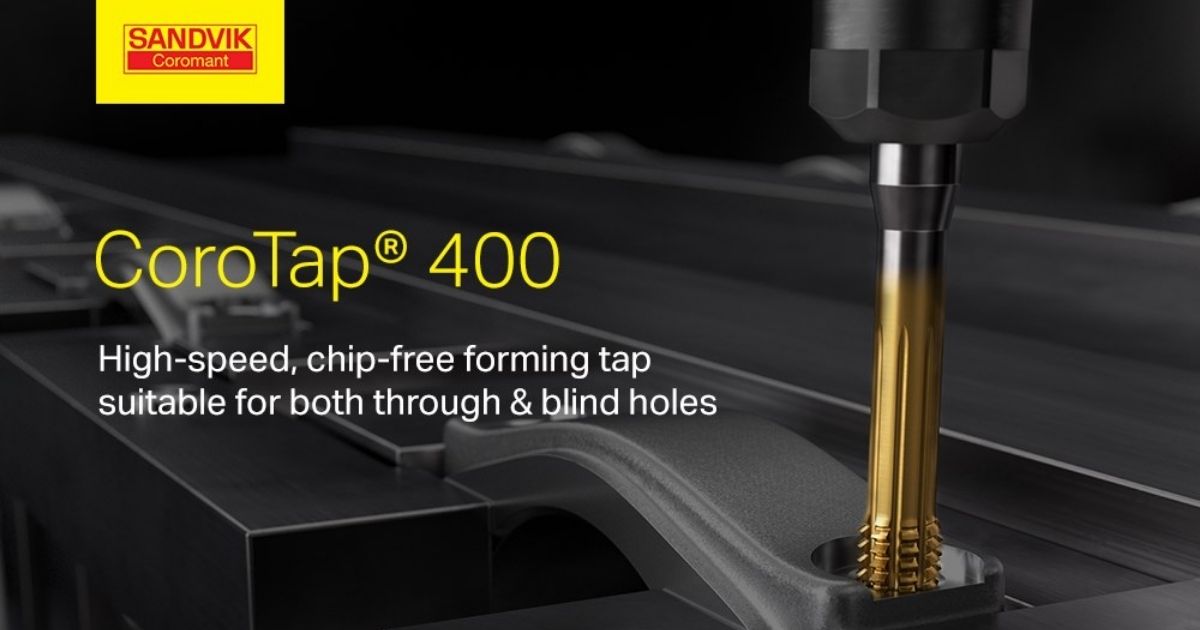
2.2 Get in touch with AMS Company Limited today - Sandvik Coromant official distributor in Vietnam
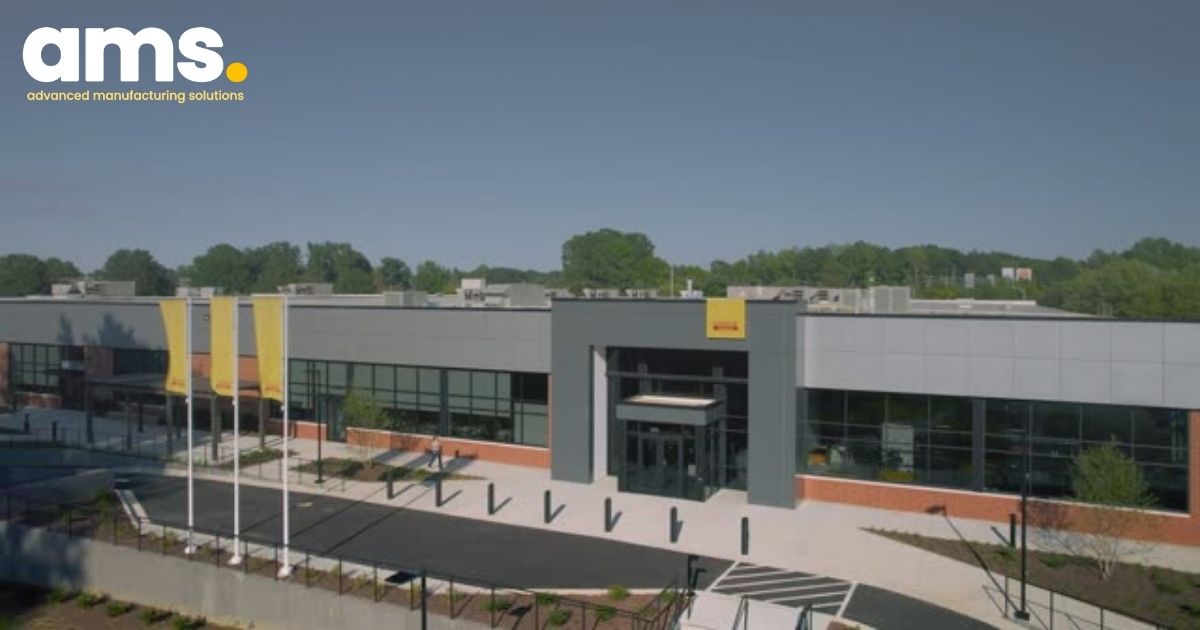
For expert guidance on selecting the right tappets from Sandvik Coromant and to explore pricings, customers are encouraged to contact AMS Company Limited today. With a team of experienced professionals and a strong commitment to customer satisfaction, AMS is dedicated to providing tailored solutions that drive success in machining operations. Contact AMS for a comprehensive consultation and discover the optimal tappet solutions for your machining needs.
AMS Company, Ltd.243/9/10D To Hien Thanh, Ward 13, District 10
Hot line: 028.3868 3738/3903 - Fax: 028.3868 3797