Expert Insights: Unraveling 6 Effective Mould Polishing Techniques
If you're in the manufacturing industry, you know how crucial it is to achieve smooth and flawless surfaces on your moulds. A well-polished mould not only enhances the aesthetics of your final product but also ensures optimal performance and durability. In this article, we will explore six different techniques for mould polishing that professionals in the field widely use. Whether you prefer traditional hand or cutting-edge diamond polishing, we've got you covered!
1. Traditional Mould Polishing Methods
1.1 Hand polishing
Hand polishing is one of the most traditional and commonly used methods for mould polishing. It involves using manual tools, such as sandpaper, files, and polishing stones, to remove imperfections on the surface of the mould. This method requires skill and precision from the polisher.
The process begins by assessing the condition of the mould and identifying areas that need improvement. Then, different grits of sandpaper are used to gradually smooth out rough spots and scratches. Next, finer abrasives are applied to achieve a higher level of polish.

Hand polishing allows for complete control over the pressure and angle at which each stroke is made, resulting in a more customized finish. It also provides flexibility in reaching difficult-to-access areas. However, it can be time-consuming compared to other methods.
Despite its labour-intensive nature, hand polishing ensures excellent surface quality without compromising intricate details or sharp edges on the mould.
1.2 Abrasive polishing
Abrasive polishing is a widely used method for achieving a smooth and shiny surface on moulds. This technique involves using abrasive materials to remove imperfections, scratches, and other surface irregularities. It is an effective way to improve the overall quality of the mould and enhance its performance.

One of the commonly used abrasive materials in this process is sandpaper. Different grit sizes are available, ranging from coarse to fine, allowing for gradual refinement of the surface texture. The choice of abrasive material depends on the specific requirements of the mould and desired finish.
During abrasive polishing, operators apply pressure in circular or back-and-forth motions to ensure even removal of material. This process requires patience and precision as it can be time-consuming depending on the size and complexity of the mould.
Abrasive polishing can be done manually or with the help of automated tools such as rotary polishers or grinding machines. These tools offer greater efficiency by reducing human effort and ensuring consistent results.
Regular maintenance plays a crucial role in achieving optimal results through abrasive polishing. By regularly inspecting and addressing any wear or damage to abrasives, operators can maintain their effectiveness over time.
Abrasive polishing is a versatile method that offers excellent control over surface finishing. Whether you are working with metal molds or plastic molds, this technique can help achieve high-quality finishes that meet your specific requirements without compromising accuracy or functionality.
1.3 Electrolyte polishing
Electrolyte polishing is a method used for mould polishing that involves the use of an electrolytic solution to remove material from the surface of the mould. This process is often preferred for complex shapes and hard-to-reach areas, as it allows for precise control over the amount of material removed.
In electrolyte polishing, the mould is immersed in an electrolytic bath containing a conductive solution. A direct current is then applied between the mould and a cathode, causing metal ions to dissolve from the surface of the mould and deposit onto the cathode.
One advantage of electrolyte polishing is its ability to achieve uniform removal across large surfaces. By adjusting parameters such as current density and bath composition, operators can control both material removal rate and surface finish quality.
Furthermore, electrolyte polishing can be used on various materials including steel, aluminum, copper, and even hardened tool steels. This versatility makes it suitable for a wide range of applications in industries such as automotive manufacturing, aerospace engineering, and consumer electronics.

However, it's worth noting that electrolyte polishing requires careful monitoring to prevent over-polishing or under-polishing. Proper training and expertise are essential to ensure consistent results without damaging or distorting the mold structure.
In conclusion, electrolyte polishing offers precision and versatility in achieving high-quality finishes on complex molds. Its ability to remove material uniformly makes it a valuable option for industries where aesthetics play a significant role in product performance. With proper technique application by skilled professionals ensures optimal results with minimal damage risk to delicate mold structures.
2. Advanced Mould Polishing Methods
2.1 Diamond polishing
Diamond polishing is a highly effective method used to achieve a superior finish on moulds. It involves the use of diamond abrasives, which are incredibly hard and durable, making them ideal for removing imperfections and creating a smooth surface.
The process of diamond polishing starts with the selection of the appropriate grit size for the desired level of polish. Coarser grits are used initially to remove any roughness or scratches from the mould surface. As the polishing progresses, finer grits are employed to achieve a mirror-like finish.

During diamond polishing, water is often used as a coolant and lubricant to prevent overheating and ensure optimal results. The diamonds are typically applied using rotary tools or hand-held devices, allowing for precision and control over the polishing process.
One advantage of diamond polishing is its ability to produce consistent results across different types of materials, including steel, aluminium, and plastic. This versatility makes it an excellent choice for moulds made from various materials.
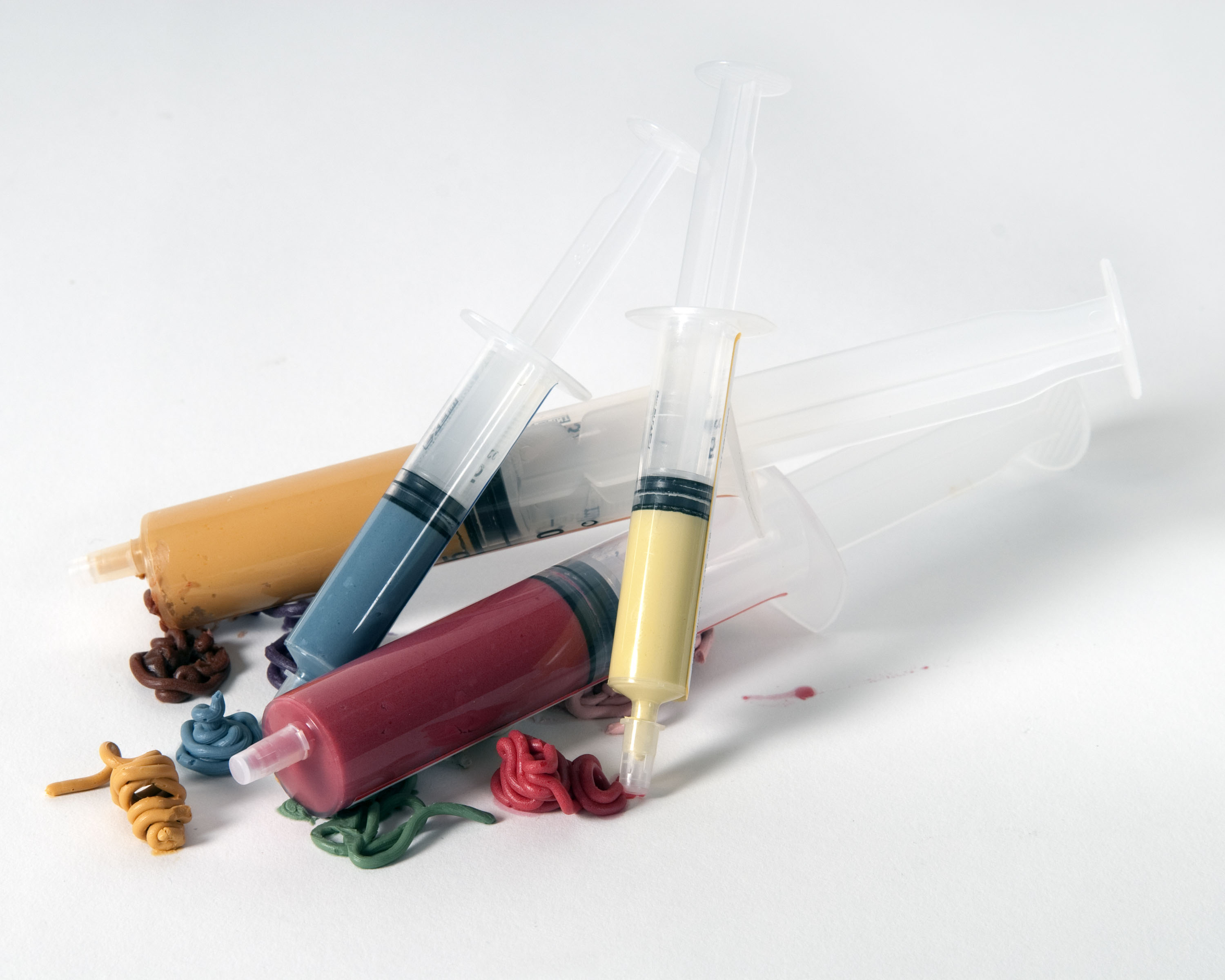
In addition to delivering exceptional gloss and shine, diamond polishing can also help extend the lifespan of moulds by reducing wear and tear that occurs during production.
Diamond polishing offers precise control over the finishing process while providing outstanding results in terms of aesthetics and durability. Whether you're working with intricate details or larger surfaces on your moulds, this method can help you achieve impeccable quality every time!
2.2 Ultrasonic polishing
Ultrasonic polishing is a highly effective method used for mould polishing. It utilizes the power of ultrasonic vibrations to achieve precision and smoothness on the surface of the mould.
In this process, a mixture of abrasive particles and liquid is applied to the surface, and then high-frequency sound waves are passed through it. These sound waves create microscopic bubbles that implode with tremendous force upon contact with the mould surface, effectively removing any imperfections or roughness.
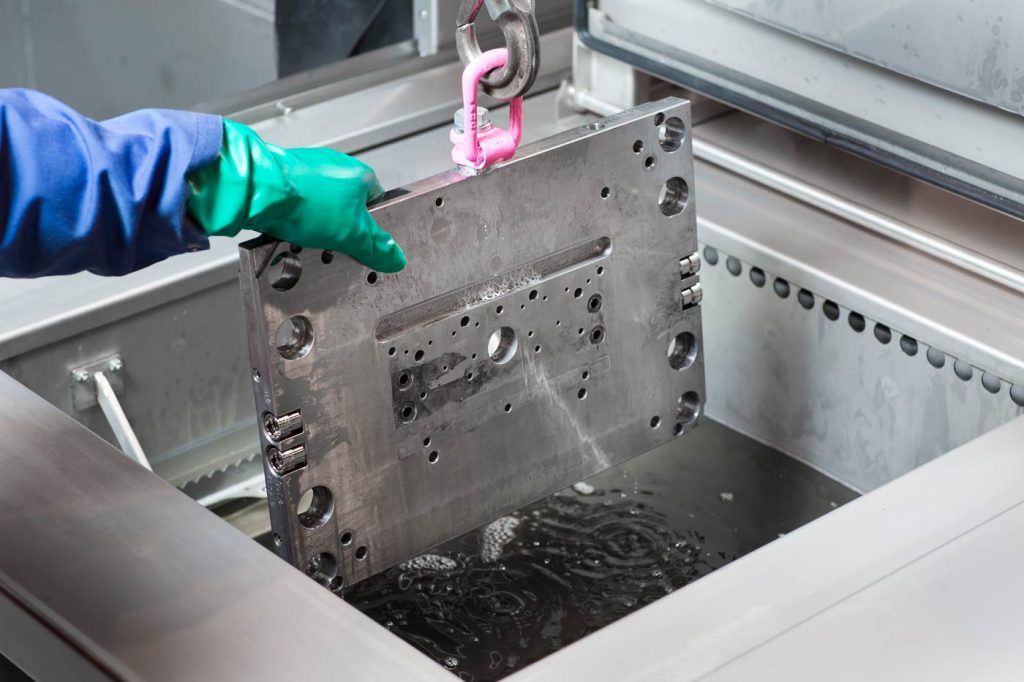
The advantages of using ultrasonic polishing are numerous. It allows for precise control over the level of polish desired, ensuring consistency across all parts of the mould. It can reach into complex geometries and hard-to-reach areas that may be difficult to access by other methods.
Additionally, ultrasonic polishing reduces manual effort and saves time compared to traditional hand polishing techniques. It also minimizes operator fatigue as there is less physical exertion required.
Ultrasonic polishing is a valuable tool in achieving high-quality finishes on moulds. Its ability to provide precise control, accessibility in intricate areas, and efficiency make it a preferred choice among manufacturers seeking top-notch results in their products' production processes.
2.3 Chemical polishing
Chemical polishing is another method commonly used for mould polishing. It involves the use of chemical solutions to remove surface imperfections and enhance the overall appearance of the mould.
In this process, a mixture of chemicals is applied to the surface of the mould, which helps in dissolving any unwanted material or rough spots. The chemicals work by selectively attacking certain areas on the surface, resulting in a smooth and polished finish.
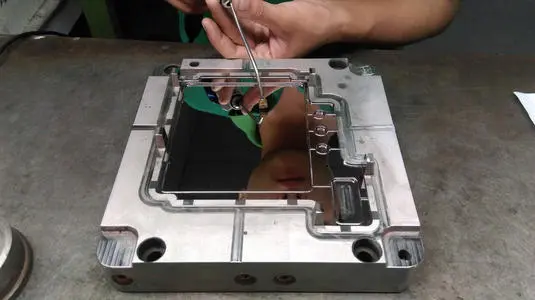
One advantage of chemical polishing is that it can be used on various types of materials, including metals like stainless steel and aluminium. This makes it a versatile option for different types of moulds.
However, it's important to note that chemical polishing may not be suitable for all types of materials or surfaces. Some materials may react differently with the chemicals, leading to undesired results. Therefore, proper care must be taken when using this method.
Chemical polishing offers an effective solution for achieving high-quality finishes on moulds. It can help improve both aesthetics and functionality by removing imperfections and creating a smooth surface texture.
3. Comparison of mould polishing methods
When it comes to mould polishing, there are several methods that can be used to achieve excellent results. Each method has its own advantages and considerations, making it important to choose the right technique for your specific needs.
Hand polishing is a traditional method that relies on skilled craftsmen using various tools and abrasives to manually polish the mould surface. While this method allows for precise control, it can be time-consuming and may not always produce consistent results.
Abrasive polishing involves using abrasive compounds or materials such as sandpaper or grinding stones to remove imperfections from the mould surface. This method is effective in removing scratches and achieving a smooth finish but requires careful handling to avoid damaging the mould.
Electrolyte polishing utilizes an electrolytic process where metal ions are selectively removed from the mould surface, resulting in a polished finish. This method offers great precision and efficiency but may require specialized equipment and expertise.
Diamond polishing employs diamond particles embedded in a matrix material to grind away imperfections on the mold surface. It is highly effective in achieving a mirror-like finish with tight tolerances but can be costly due to the use of diamond materials.
Ultrasonic polishing uses high-frequency vibrations combined with abrasive slurry or paste for efficient removal of burrs, scratches, and other imperfections. It offers fast results while minimizing damage risks but may not be suitable for all types of moulds.
Chemical polishing involves immersing the mould in a chemical solution that selectively dissolves material from its surface, resulting in a smooth finish. Although this technique is less common than others mentioned above, it can provide excellent results when applied correctly.
4. Conclusion
While each technique has its strengths, it's important to consider factors such as material type, desired finish quality, the complexity of the mould design, and available resources before selecting a specific method.
Finding the right mould polishing approach will depend on your unique requirements and constraints. Consulting with experts in the field can help you make an informed decision based on your specific needs.
Remember that proper maintenance and regular inspection are vital in ensuring optimal performance and longevity of moulds regardless of which polishing technique you choose.
Still unsure of which mold polishing technique is suitable for your application? Look no further! Contact AMS Company Limited today for a consultation on choosing the right technique and polishing product. We have every product line available for any polishing technique, ensuring that you have access to the best tools for your needs. With over 20 years of experience in the field of polishing, our trained professionals will guide you in making an informed decision. Don't hesitate, reach out to us now!
AMS Company, Ltd.243/9/10D To Hien Thanh, Ward 13, District 10
Hot line: 028.3868 3738/3903 - Fax: 028.3868 3797