Explore the Power of HEIDENHAIN Exposed Linear Encoders for Direct Drives
Linear motors have penetrated dynamic applications like manufacturing and measuring equipment in the semiconductor industry, PCB assembly machines, textile machines, and automation. For open and closed-loop control in direct drives, accurate real-time position information for the slide is essential. The precision, effectiveness, and dependability of the individual axes rely on the linear measuring devices. These days, compact and contact-free measuring devices, known as exposed linear encoders, primarily fulfill this task in conjunction with linear motors.
Direct drive technology provides a crucial advantage with its tightly coupled drive to the feed component without additional mechanical transfer elements. This allows for a much higher gain in the control loop compared to conventional drives. The efficiency of a linear motor is significantly affected by the choice of the position encoder. High-quality position signals from the encoder are essential to achieve a high control-loop gain. Even slight disturbances in the encoder output signal can cause significant issues in drive performance due to the high gain required in the control loops. Improved position information quality noticeably enhances velocity control and positioning, resulting in quiet motor operation and minimal heat generation.
1. Velocity measurement on direct drives
In direct drives, there's no separate encoder for measuring speed. The position encoder, such as linear encoders for linear motors or angle encoders for rotating motors, is responsible for measuring both position and speed. Since there's no mechanical link between the speed encoder and the feed unit, the position encoder needs a very high resolution to enable precise velocity control, especially at slow speeds. The velocity is calculated as the distance traveled per unit of time, a method also used for conventional axes, but it can amplify periodic disturbances or noise in the signal.
Direct drives have significantly higher control loop gain, meaning the quality of the signal has a big impact on drive performance. To ensure direct drives function effectively, it's crucial to use linear encoders that produce high-quality position signals with minimal interpolation error. Encoders using photoelectric scanning are well-suited for this task, as they can utilize very fine graduations as measuring standards. These encoders enhance positioning, speed stability, and thermal behavior of a direct drive.
Previously, exposed linear encoders didn't provide immediate absolute position value calculation after switch-on without axis movement. Sealed absolute linear encoders, though beneficial, weren't often used on direct drives due to their compact dimensions. Exposed encoders, lacking an enclosure and thus having small dimensions and low weight, were typically only available in incremental versions. However, HEIDENHAIN now offers the LIC 4100 exposed linear encoder, providing absolute position calculation and using the EnDat 2.2 serial interface for direct drives.
2. The graduation carrier—a METALLUR scale tape
HEIDENHAIN encoders that use optical scanning feature periodic structures called graduations as their measuring standards. These graduations are known for their sharp edges and consistent quality, which are essential for minimizing interpolation errors and ensuring smooth operation and high control loop gain.
The quasi-planar graduation structure, implemented through the METALLUR process, is highly resistant to contamination, significantly boosting the reliability of the encoder.

In the LIC 4100 series, featuring absolute graduation, the encoder provides the position value right after the machine is switched on, eliminating the need to move the axes over reference marks to establish the reference position. The absolute position data is obtained from the scale graduation, which consists of a pseudo-random-coded track (PRC) and a separate incremental track. The position data is determined using a newly developed scanning method that evaluates both the PRC track and the incremental track. This is made possible by a highly integrated opto-ASIC, leading to a new level of accuracy and reliability in position information.
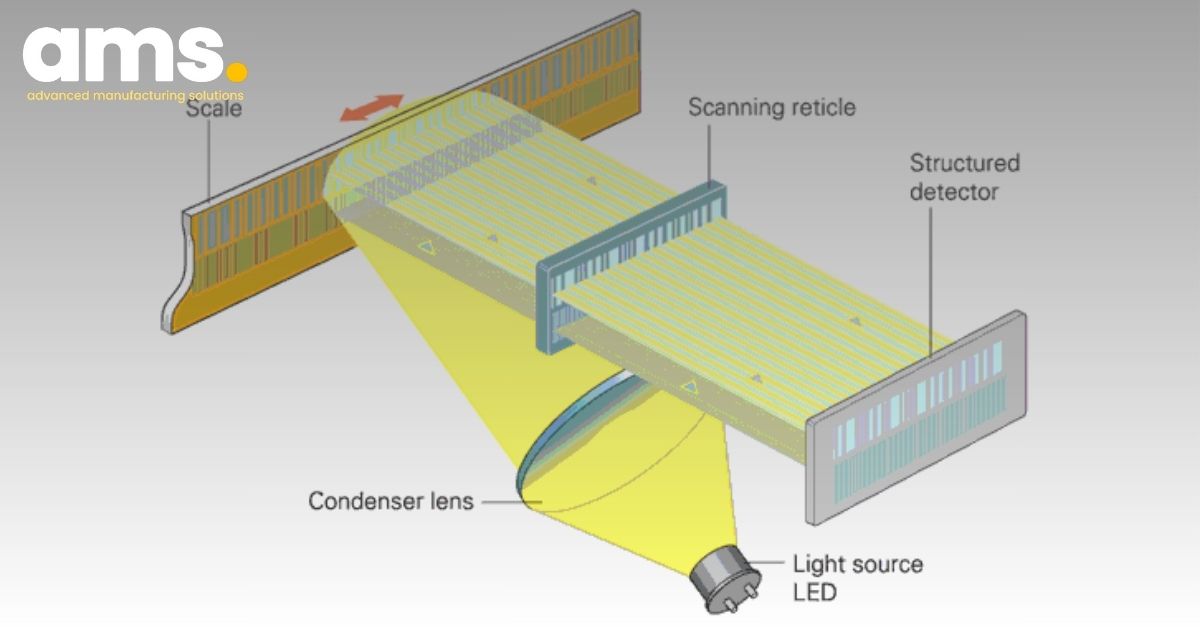
The precision of measurement and high reliability are key factors in ensuring machine safety. The innovative scanning method, relying on the high-quality graduation, delivers absolute position values with an interpolation error of less than ± 40 nm. Exposed linear encoders from the LIC 4100 series are specifically designed for use in fast, precise machines. Despite their exposed design, these encoders exhibit exceptional tolerance to contamination, significantly enhancing machine uptime in various applications.
Extensive laboratory testing has demonstrated the encoder's resilience to everyday contaminants such as small amounts of oil, dust, fingerprints, hair, and tiny metal objects, with minimal impact on operational reliability. Furthermore, the measuring accuracy of the LIC 4100 remains largely unaffected by the tested forms of contamination.
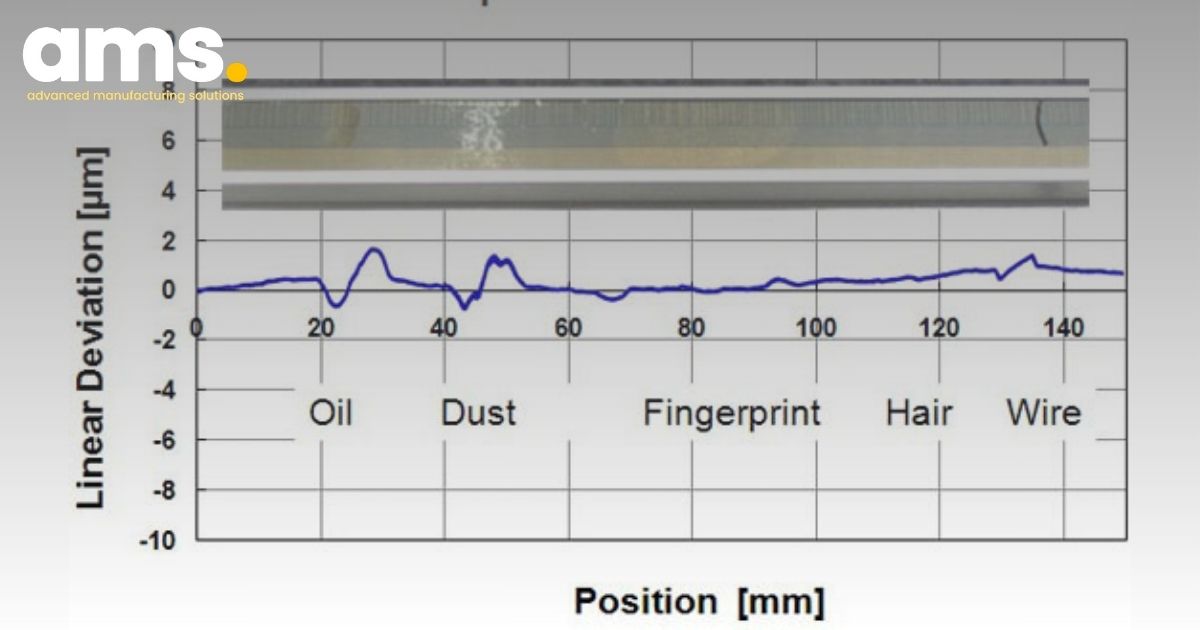
3. Benefits of serial position transmission with EnDat 2.2
The scanning signals in the LIC 4100 series are digitized directly within the scanning head and converted into a high-resolution position value. This removes the previous method of transmitting analog signals from the scanning head for drive control. By utilizing digital position transmission through EnDat 2.2, the benefits of the new absolute scanning process in terms of accuracy and resolution can be fully realized without any loss during transmission.
This advancement significantly enhances the speed stability and precision of linear direct drives using the LIC 4100. High-performance drives powered by position signals from the LIC 4100, even with very high proportional gain in the velocity controller, operate quietly. The high control loop gain achieved would not have been feasible without the EnDat interface's high clock frequency and the resulting short read-out times. EnDat 2.2 presently stands as the fastest purely serial interface for position encoders based on RS-485 transmission characteristics.
4. Simple installation with diagnostic capabilities
The absolute encoders in the LIC 4100 series are straightforward to install. Through EnDat 2.2, the valuation numbers for the absolute and incremental tracks, as well as the position value calculation, provide a real-time status report on the encoder's condition. Proven mounting tolerances combined with valuation numbers enable reliable installation without sacrificing safety margins in practical applications. During motor operation, the valuation numbers can be accessed via EnDat 2.2 without compromising servo control performance. The diagnostic system generates error messages and warnings, significantly contributing to ensuring the overall system's availability.
5. Enhancing precision and performance: The revolutionary LIC 4100 absolute encoder
Direct drive applications have specific demands on control and measurement technology. The encoders used for position and drive velocity need to deliver high-quality signals. In direct-driven feed axes, errors in the position measuring signal can lead to positioning errors, speed variations, increased noise, and additional heat generation. Encoders employing optical scanning with small signal periods have proven to be highly effective in enabling machines to operate with exceptional accuracy and resolution.
The LIC 4100 compact exposed linear encoder now offers an absolute encoder with a resolution as fine as one nanometer (1 nm). This encoder utilizes the reliable EnDat 2.2 serial interface for fast data transfer. In addition to position data, the EnDat protocol allows for the transfer of various data useful for system diagnostics. This exposed absolute encoder is poised to significantly enhance the accuracy, performance, and reliability of individual axes across various demanding applications such as semiconductor manufacturing, metrology, medical technology, automation, and textile machinery. This advancement provides machine tool builders and plant manufacturers with a key asset for current and future generations of machinery.
6. AMS Company Limited - Your Exclusive Distributor for HEIDENHAIN Exposed Linear Encoders
HEIDENHAIN is renowned for its cutting-edge solutions in precision measurement and motion control. Their line of exposed linear encoders has been a game-changer for industries relying on direct drives. With high-resolution position feedback and EnDat 2.2 interface, these encoders have set a new standard for accuracy and performance.

In Vietnam, AMS is the exclusive distributor for HEIDENHAIN products. AMS has a stellar reputation for providing exceptional technical expertise and support. If you're considering integrating HEIDENHAIN's exposed linear encoders into your systems, don't hesitate to reach out to AMS for professional guidance and assistance. Their team of experts can offer insights into the advantages of HEIDENHAIN's products and how they can elevate the performance of your machinery.

Contact AMS now to explore how HEIDENHAIN's innovative solutions can benefit your operations.
AMS Company, Ltd.243/9/10D To Hien Thanh, Ward 13, District 10
Hot line: 028.3868 3738/3903 - Fax: 028.3868 3797