The Essential Guide to Mould Polishing Tools: What you need to know
1. What is mould and die?
A mould is a metallic tool utilized in shaping products through various moulding techniques. Each mould serves the purpose of shaping or extruding a specific quantity of products, can be used once or reused multiple times. The texture and size of the mould are determined by the size, shape, quality, and quantity of the desired product.
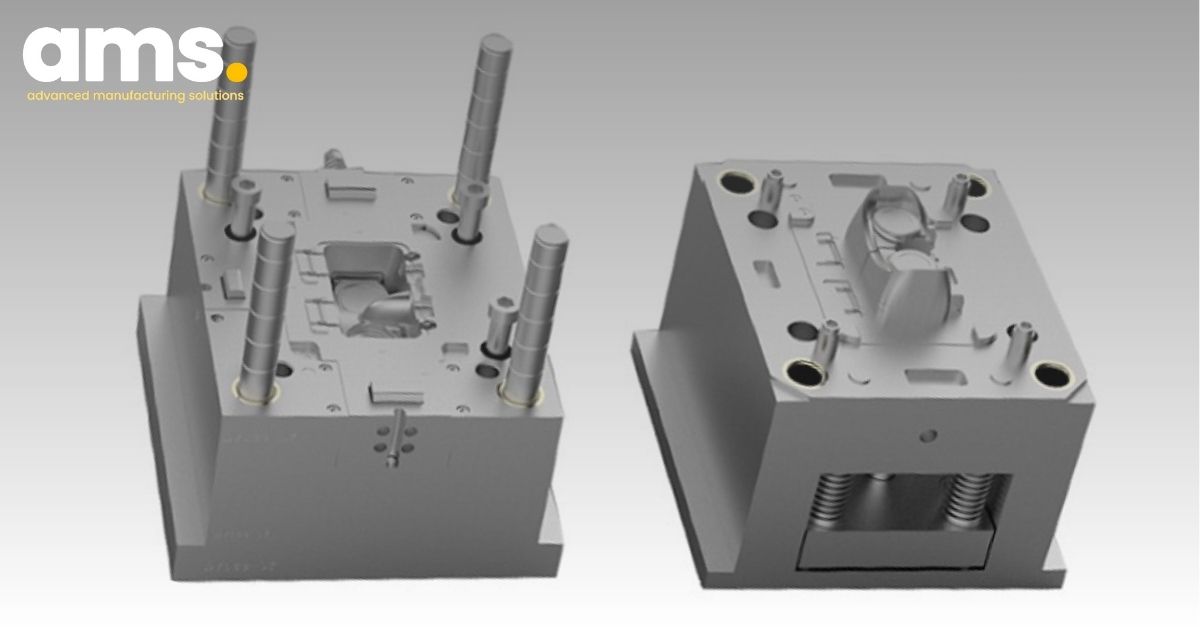
During the production of moulds and dies, manufacturers have the option to either utilize existing templates or develop new product samples based on creative designs and ideas. The moulding process helps manufacturers to create products in accordance with customer requirements. Using available moulds to support the creation of products similar to the original prototype, while still ensuring the product's features and functions without reducing efficiency.
2. Plastic injection moulds
2.1 Mould manufacturing process
The process of manufacturing moulds involves five main technological steps: sample design, CNC machining, heat treatment, testing, and assembly. Manufacturers have the flexibility to engage in one or more of these processes, as well as the overall manufacturing process, to create the final product.
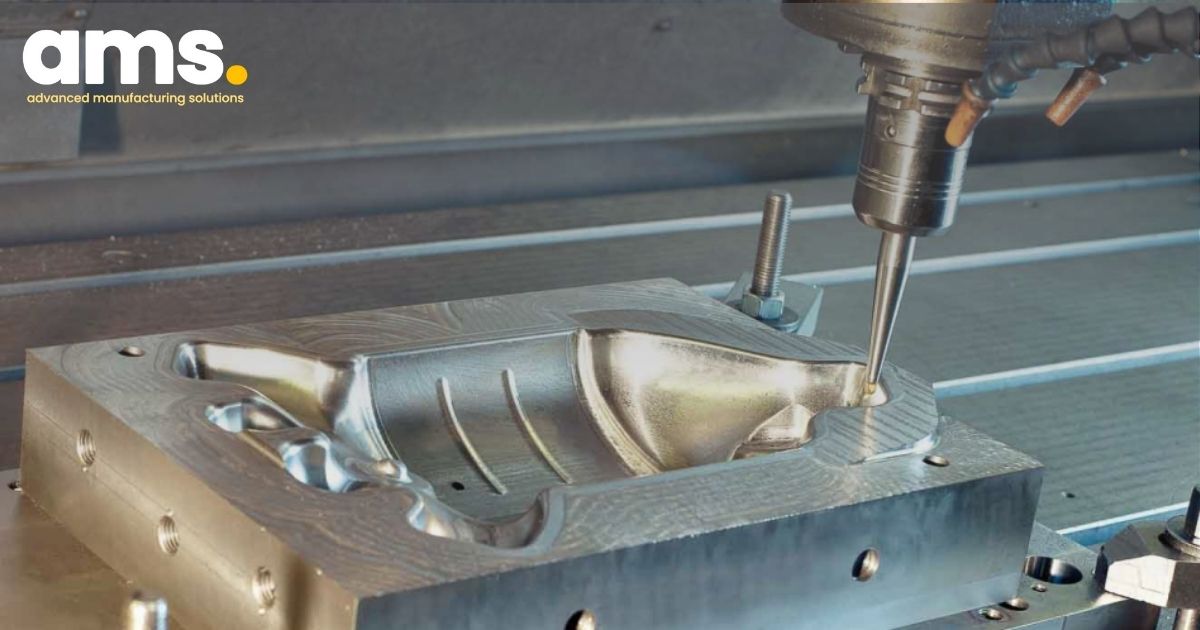
This closed process encompasses various stages, including order receipt, analysis, processing, delivery, and repair services, including the replacement of parts within the mould. Mould processing units are involved in each of these stages, and some larger manufacturing firms may handle their own design, testing, and assembly processes, even manufacturing and selling the end products themselves.
Since moulds are individually produced, the production of moulded products is not influenced by economies of scale. This presents favorable conditions for Vietnam to compete with other countries, notably China. The mould market in Vietnam and globally is experiencing rapid growth and is of significant scale. Vietnam's technological expertise in this field is not low and has the potential to progress and catch up to the global average.
2.2 Popular types of moulds
Injection moulds play a vital role in various industries for producing parts made from a range of materials, including plastic, metal, rubber, glass, and other inorganic substances. These injection moulds are used to create products such as metal and plastic components found in automobiles, aircraft, home appliances, electrical devices, electronics, consumer goods, furniture, military equipment, and medical products.
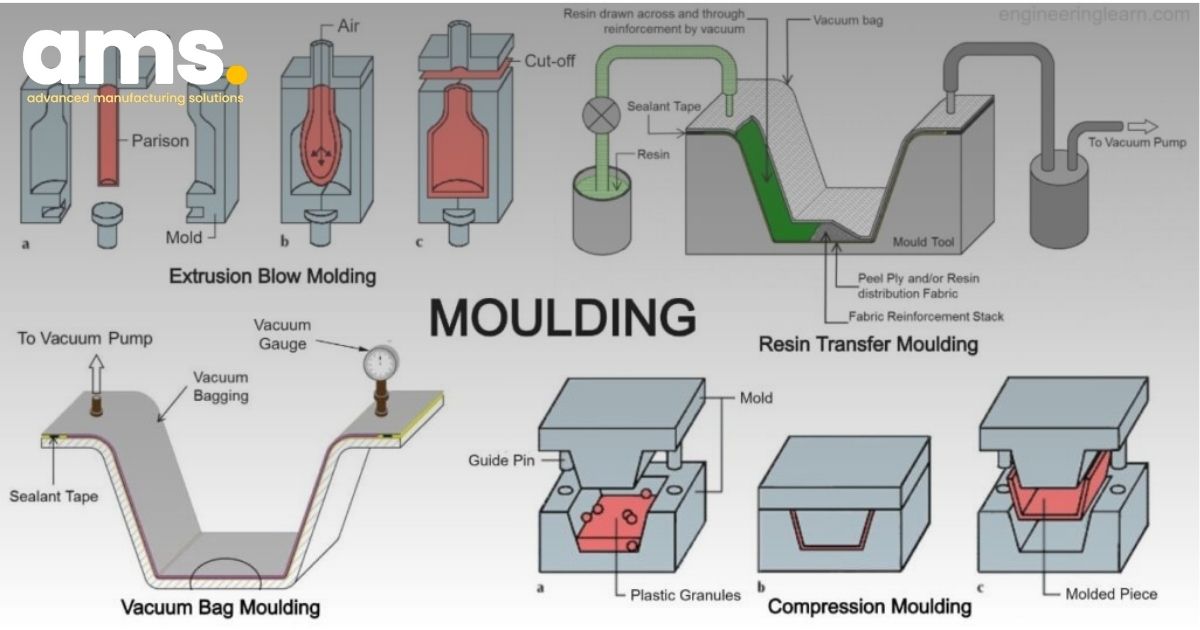
In the manufacturing process of plastic products, different types of moulds are employed, including injection moulds, compression moulds, blow moulds, punching moulds, die casting moulds, extrusion moulds, and more. Among all these, injection moulding and punching moulds are the most commonly utilized.
3. Die (manufacturing)
3.1 Product design (CAD)
CAD software is computer design software widely used in many industries. It allows designers to create product models in the form of 2D or 3D drawings.
Highly complex plastic moulds or punching moulds will be simplified by CAD software. This is greatly beneficial for completing the prototype quickly and accurately.
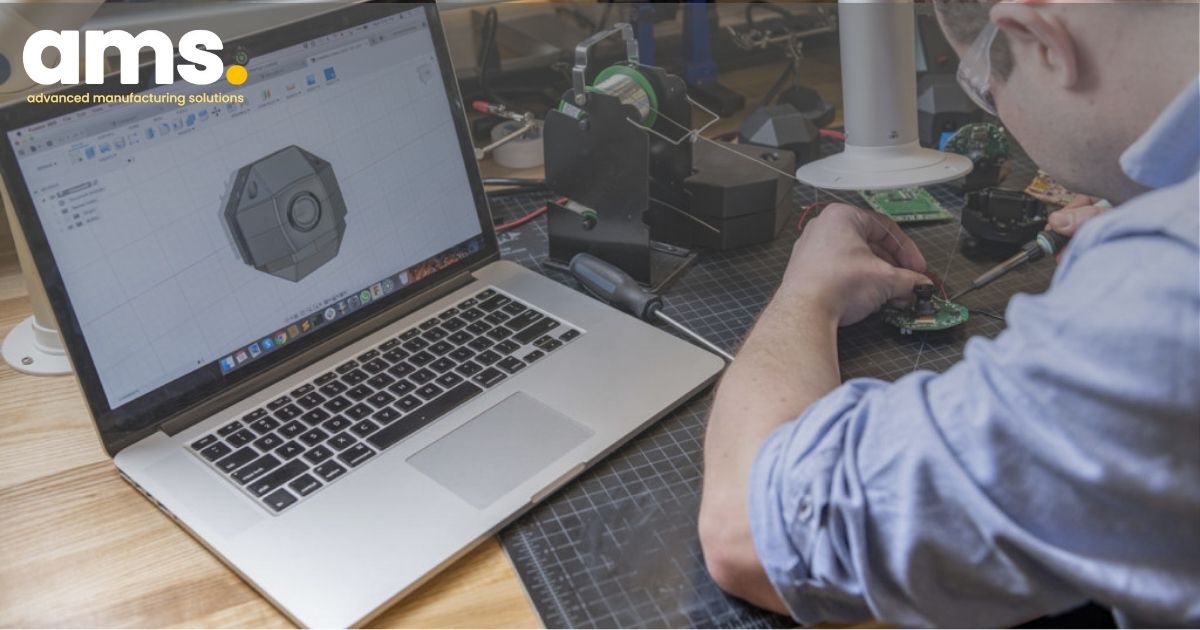
Completing the prototype quickly and accurately during the mould manufacturing process is important. CAD software allows you to design product models efficiently and accurately. This saves time during the design and editing process, while ensuring consistency and quality of the final mould product. Completing prototypes quickly and accurately helps optimize the production process and minimize errors.
3.2 CNC machining programming (CAM)
CAM is a mechanical processing software installed on a computer, similar to CAD. CAM acts as an operating system for computerized devices and machines.

CAM software has the ability to receive and analyze data from detailed CAD, then calculate the necessary parameters and control the operation of CNC machines during CNC machining programming.
Using CAM software helps to successfully manufacture mould products and limit the tolerance of each mould to the maximum level. This ensures the accuracy and reliability of the machining process and meets the quality requirements of the mould product.
3.3 Machining on CNC machines
CNC (Controlled-Numeral Computers) are modern technological machines with high precision. CNC machines include cutting machines, lathes, milling machines, laser punching machines and many other industrial machines in the new generation.

CNC machinery systems operate automatically through programming on CAM software. The product is manufactured using reliable and precision CNC according to high world standards, its quality and precision is undisputable.
CNC machines are designed and manufactured with the goal of achieving high precision during the machining process. Thanks to modern technology, CNC machines are capable of operating with very high precision, often achieving strict quality and accuracy standards. This helps ensure that CNC machined products have high precision, thereby bringing good performance and quality to the manufacturing process. However, to take full advantage of the precision of CNC machines, attention must be paid to other factors such as model design, programming, and effective machine settings.
4. Why is mould polishing necessary?
A set of moulds with a good surface finish will make it easier to remove the product from the mould. The mould polishing process usually includes many different stages, each stage will use its own specialized mould polishing tools. Learn about each stage of the polishing process and choose the right tools for your needs.
5. Mould polishing tools
Depending on the requirements of the mould, the production process, the workmanship of the workers and the actual experience, each mould manufacturer will use different polishing processes and materials. However, there are some common materials, tools and machines used in the mould polishing field.
5.1 Diamond File
Basic tools are used for rough sanding or polishing. Metal files or diamond files need to come in a variety of shapes and sizes to get access to the microscopic, hard-to-reach details.
Features: Hardness and smoothness can be adjusted to avoid mould damage.
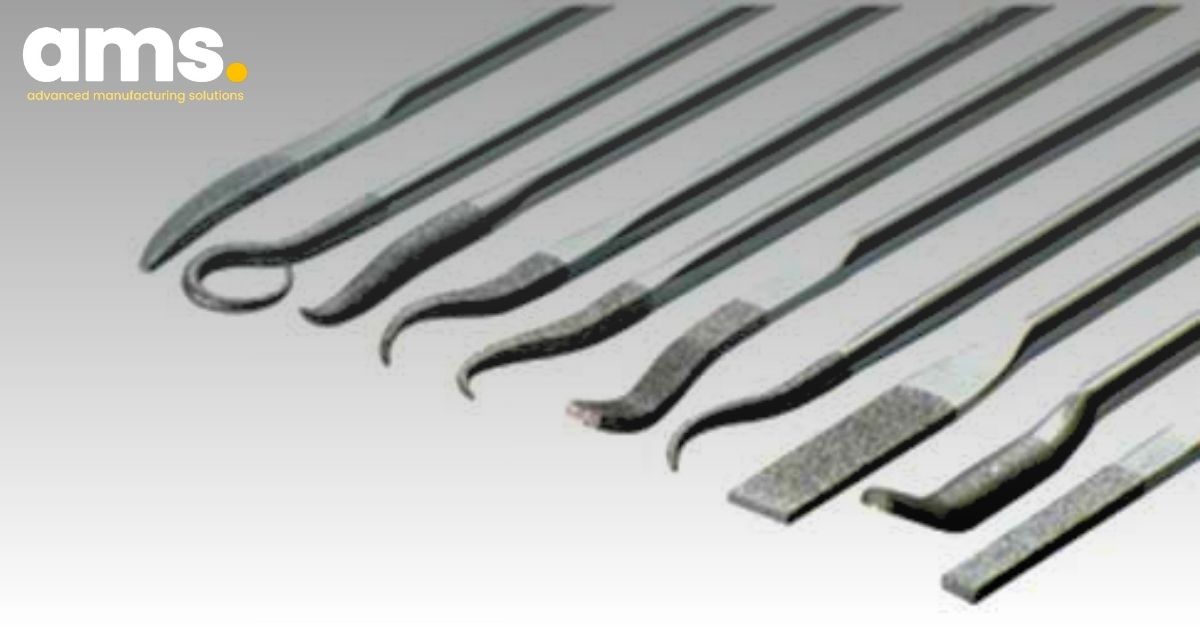
5.2 Bar grinding stone, oil grinding stone
For example, materials such as Xebec, Giesswein are used to polish moulds in hard-to-reach positions due to their hardness and durability.
Oil grinding wheels are manufactured in a variety of sizes and roughnesses.
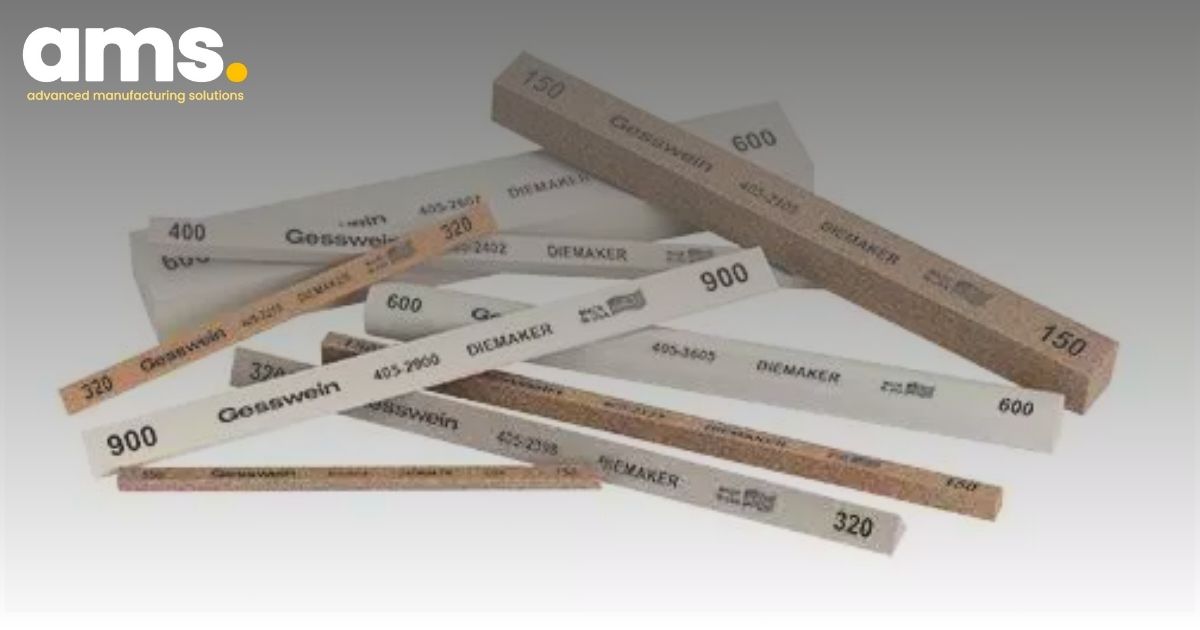
5.3 Wood and felt polishing head
Wood rods are divided into two types: softwood bars for fine polishing and hardwood bars for rough grinding or polishing. These wooden slats have different shapes such as rectangular blocks, thin plates and have different inclined angle designs, catering for many different types of moulds.
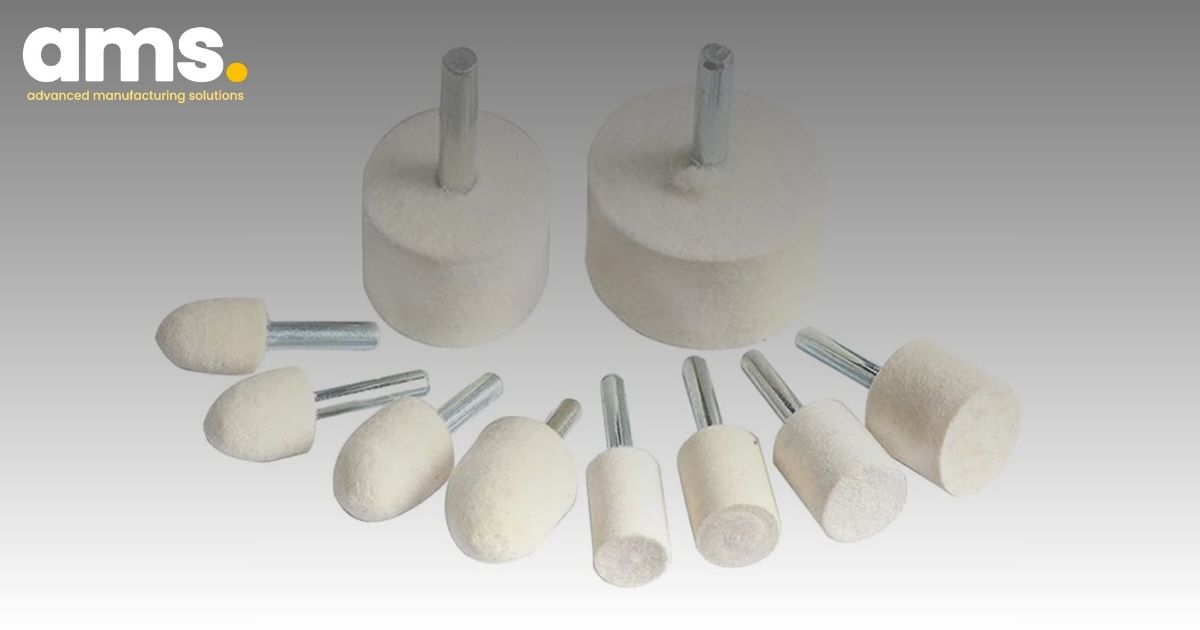
5.4 Mould polishing brush – mould polishing wood
In addition, other materials such as soft paper, abrasive stone, cotton, cotton wool and polishing cloth are used in the polishing process of the mould.
- Soft paper is often used to roughen the surface, smooth or remove small scratches on the mould.
- The grinding wheel is used to remove sharp edges from the surface of the mould, creating a finely polished and smooth finish.
- Cotton and cotton wool are commonly used to apply buffing and polishing agents to the surface of the mould, creating a glossy and smooth finish.
- Polishing rollers are used for rough grinding and polishing, and the hardness can be adjusted to suit the specific requirements of the polishing process.


6. Types of polishing supplies
6.1 Polished Diamond Powder
Diamond powder is the highest quality mould polishing powder available nowadays. With the greatest hardness and cutting ability, diamond powder can polish all other materials, surpassing the polishing ability of many other types of polishing products.
Diamond powder is designed in the form of a cylinder, making it easier to use and store.
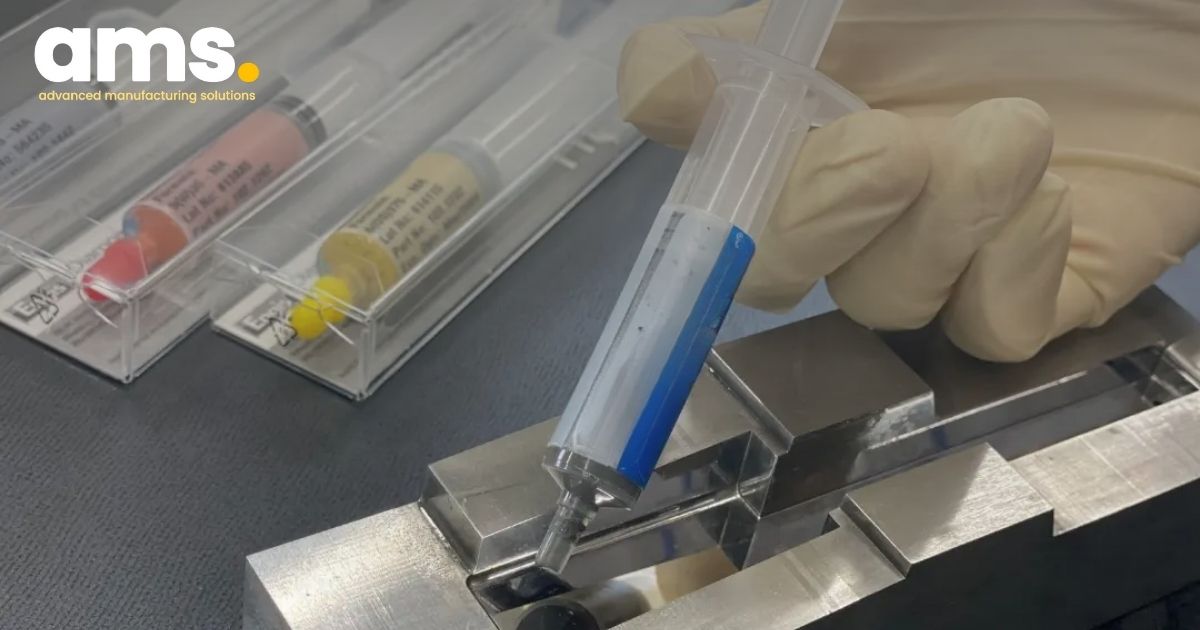
6.2 Mould polishing paste
Diamond powder used for mould polishing is produced according to strict requirements for stability and standard dimensions.
In the field of mould polishing, diamond powder is commonly used with particle sizes ranging from 1 micron to 160 microns. At a particle size of 1-3 microns, other materials can achieve a mirror-like gloss or can even surpass it.
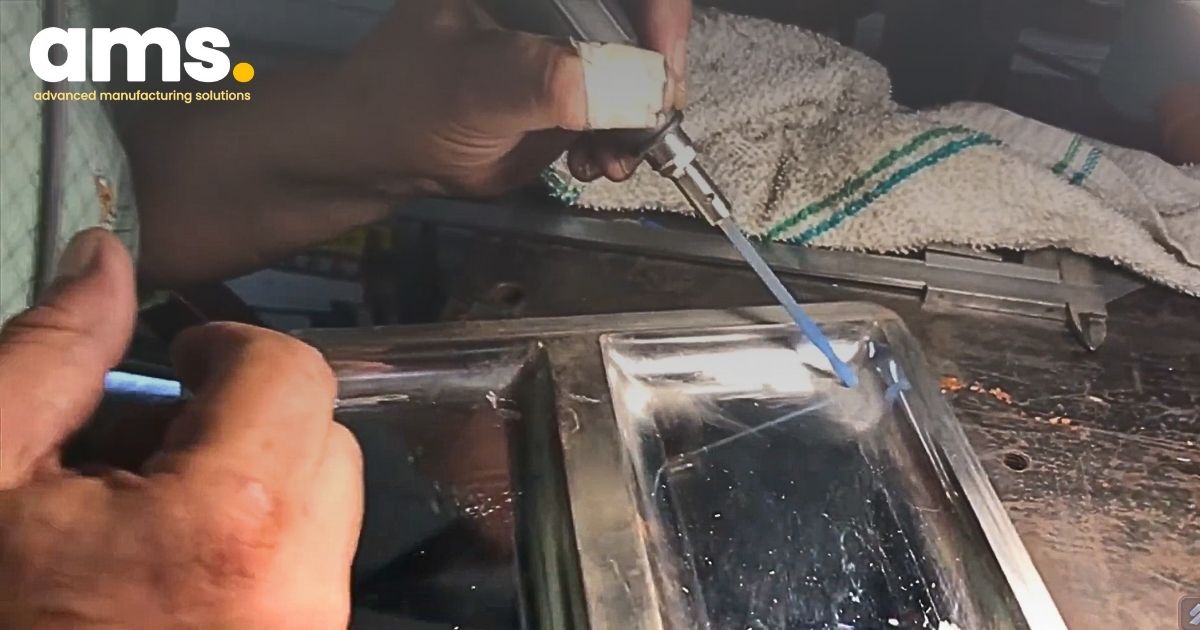
6.3 Auxiliary fluid in the polishing process
In principle, if only diamond powder is used to polish the mould, that will suffice. However, the sole use of diamond powder will increase costs significantly. That is why the process of polishing moulds with diamond powder is often accompanied by the use of a support solution. This can help to save cost and resource as diamond powder, improves cutting ability and ensures hygiene of the mould. In fact, polishing moulds with diamond powder is sometimes even more cost-effective than using other types of powder.
7. Types of machinery supporting mould polishing
Mould polishing machines are usually designed with vibration, capable of connecting with different types of mould polishing tools such as wood, cloth, file, etc. This makes polishing faster to save costs and labor.
The die vibrating polishing machine has adjustable speed and is available in various designs to cater for different types of moulds. Please contact us for further advice.
Mould Welding Machine: When a mould is used for a long period of time, the appearance of cracks, scratches, on moulds are inevitable.
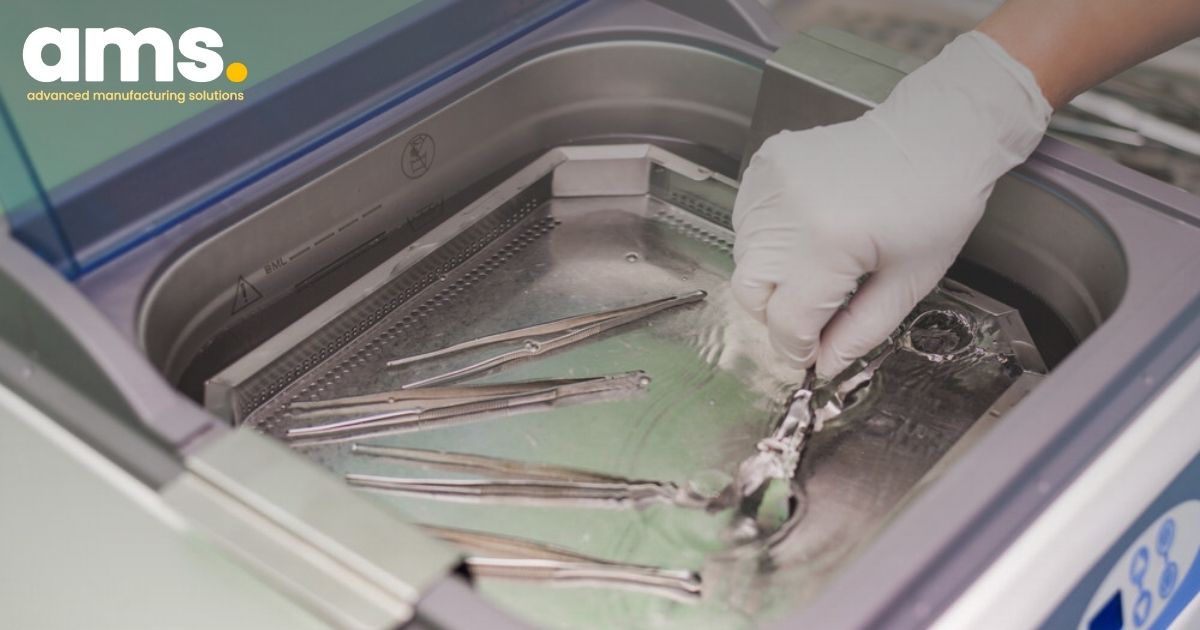
8. Advices on mould polishing
- Mould polishing should be done in a dust-free and isolated environment: dust and sand particles on the surface of the mould can cause unwanted scratches.
- Specialized polishing tools need to be used specifically for each diamond grain size. For example, polishing felt tips used with 3-micron diamond particles should not be used to polish powders of other sizes, because particles of different sizes will affect the mould surface and waste time.
- Mould polishing tools should be stored in a separate place.
- When grinding by hand, set the sharpening algorithm on the tool. When machine polishing, place abrasive grit on the part.
- The force needs to be adjusted to suit the hardness of the tool.
- For large scratches, large sized diamond powder should be chosen.
- It is recommended to start polishing the mould from areas with angular shapes.
9. Conclusion
Polishing in the manufacturing industry comes with its fair share of challenges and problems. To learn more about the issues commonly associated with polishing, you can refer to our previous article 5 Common Mistakes with Diamond Compound and How to Fix Them
At AMS, we understand these challenges and are dedicated to providing the highest quality polishing products for the precision manufacturing industry. If you find yourself unsure about which product and tool to use in order to achieve the best results and minimize costs, we encourage you to contact us. With our 20 years of expertise in polishing, our team is ready to provide you with expert consultation and guidance. Don't hesitate to reach out to us now.
AMS Company, Ltd.243/9/10D To Hien Thanh, Ward 13, District 10
Hot line: 028.3868 3738/3903 - Fax: 028.3868 3797