Angle Measurement with HEIDENHAIN Rotary Encoder
1. Angle Encoders
HEIDENHAIN angle encoders are characterized by high accuracy values in the range of angular seconds and better.
These devices are used in applications such as rotary tables and swivel heads of machine tools, indexing heads, high precision angle measuring tables, precision devices in angular metrology, antennas and telescopes.
- Line counts: typically 9000 to 180000
- Accuracy: from ±5" to ±0.4"
- Measuring steps: as fine as 0.00001° or 0.036" (incremental) or 29 bits, i.e., approx. 536 million positions per revolution (absolute)
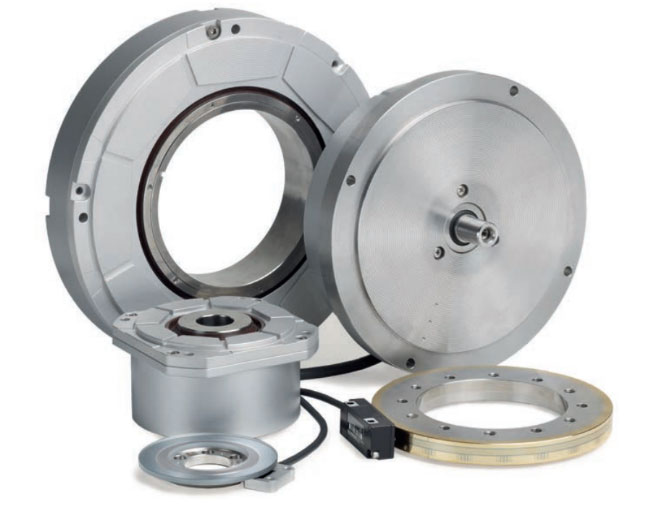
2. Rotary Encoders
Rotary encoders from HEIDENHAIN serve as measuring sensors for rotary motion, angular velocity and, when used in conjunction with mechanical measuring standards such as lead screws, for linear motion. Application areas include electrical motors, machine tools, printing machines, woodworking machines, textile machines, robots, elevators and handling devices, as well as various types of measuring, testing and inspection devices.
- Line counts: typically 16 to 5000
- Accuracy grades: to ±10" (depending on the line count, corresponding to ±1/20 of the grating period)
- Measuring steps: as fine as 0.00001°
Particularly for photoelectric rotary encoders, the high quality of the sinusoidal incremental signals permits high interpolation factors for digital speed control.
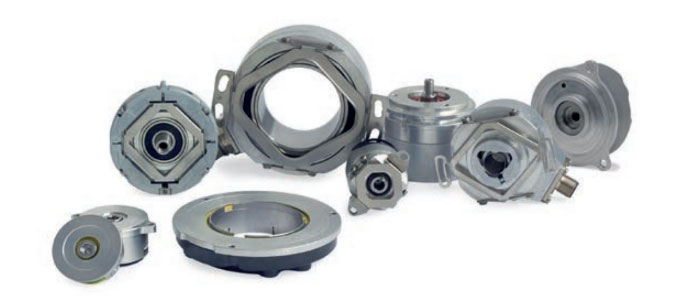
3. Mounting Variants
In angle encoders and rotary encoders with integral bearing and stator coupling, the graduated disk of the encoder is connected directly to the shaft to be measured. The scanning unit is guided on the shaft via ball bearings, supported by the stator coupling.
As a result, during angular acceleration of the shaft, the stator coupling must absorb only that torque resulting from friction in the bearing. These angle encoders therefore provide excellent dynamic performance. Thanks to the stator coupling, the system accuracy includes the error of the shaft coupling.
Other benefits of the stator coupling are:
- Simple mounting
- Short overall length
- High natural frequency of the coupling
- Hollow through shaft is possible

Angle encoders and rotary encoders with integral bearings for a separate shaft coupling are designed with a solid shaft. The recommended coupling to the measured shaft compensates radial and axial tolerances. Angle encoders for separate shaft couplings permit higher shaft speeds.
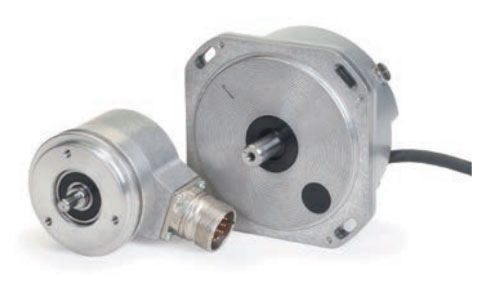
Angle encoders and rotary encoders without integral bearing operate without friction. The two components—the scanning head and the scale disk, drum, or tape—are adjusted to each other during assembly. The benefits are:
- Little space required
- Large hollow-shaft diameters
- High shaft speeds possible
- No additional starting torque
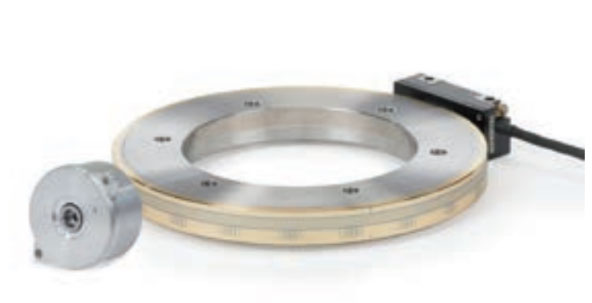
4. Classification: Incremental and Absolute
Absolute angle encoders and rotary encoders require no previous traverse to provide the current position value.
Single Turn encoders provide the current angular position value within one revolution, while multiturn encoders can additionally distinguish between revolutions. The position values are output, for example, over the purely serial, bidirectional EnDat interface. It enables automatic configuration of the higher-level electronics and provides monitoring and diagnostic functions.
Under the designation functional safety, HEIDENHAIN offers encoders with purely serial data transmission as single-encoder systems for safety-related machines and systems. The two measured values are already formed independently of each other in the encoder, and are transmitted to the safe control via the data interface.
With incremental angle encoders and rotary encoders, the current position is determined by starting at a reference point and counting measuring steps, or by subdividing and counting signal periods. Incremental encoders from HEIDENHAIN feature reference marks to reestablish the reference point.
Incremental rotary encoders with commutation signals provide the angular shaft position value—without requiring previous traverse—with sufficient accuracy to correctly control the phases of the rotating field of a permanent-magnet three-phase motor.
Sealed angle encoders | Series | |
---|---|---|
With integral bearing and integrated stator coupling | Absolute (singleturn)/Incremental | RCN, RON, RPN |
With integral bearing | Absolute (singleturn)/Incremental | ROC, ROD, RON |
Angle encoder modules | With precision bearings | MRP, SRP |
Modular angle encoders | ||
Without integral bearing, with optical scanning | Absolute (singleturn)/Incremental | ECA, ERA, ERO, ERP |
Without integral bearing, with magnetic scanning | Absolute (singleturn)/Incremental | ECM, ERM |
Rotary encoders | ||
With integral bearing, for mounting via stator coupling | Absolute (singleturn/multiturn) Incremental |
ECN, EQN ERN |
With integral bearing, for separate shaft coupling | Absolute (singleturn/multiturn) Incremental |
ROC, ROQ ROD |
Without integral bearin | Absolute (singleturn/multiturn) Incremental |
ECI, EQI, EBI ERO |
AMS Company LimitedHEIDENHAIN's Exclusive Distributor in Vietnam
With over 20 years of experience in mechanical engineering, AMS Co., Ltd is proud to be the official exclusive distributor of HEIDENHAIN in Vietnam. We distribute all HEIDENHAIN products and provide after-sales service directly from the experts affiliated with HEIDENHAIN.
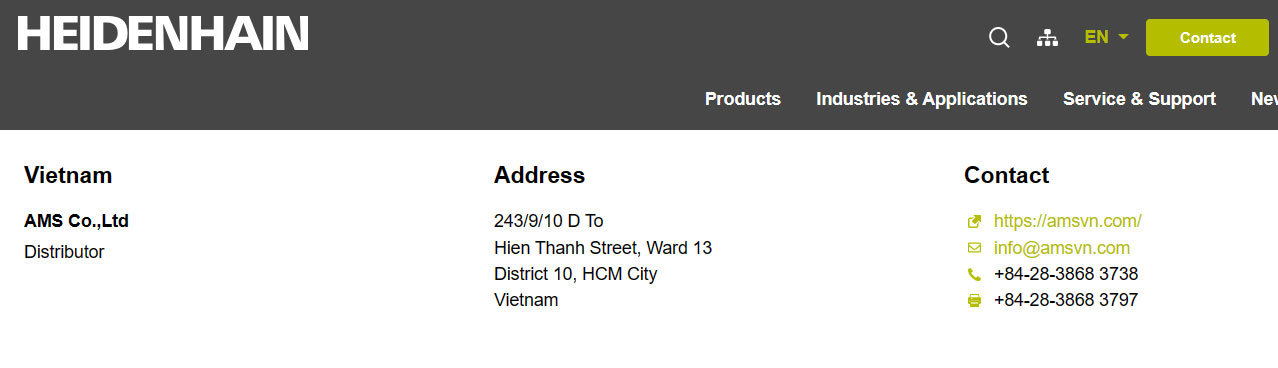
Contact us now for the best prices on the market.
AMS Company, Ltd.243/9/10D To Hien Thanh, Ward 13, District 10
Hot line: 028.3868 3738/3903 - Fax: 028.3868 3797