Achieving Precision and Productivity with Sandvik Coromant Milling Cutters: End Milling vs. Face Milling
When it comes to machining, selecting the right cutting tool is crucial in achieving optimal results. Among the different types of cutting tools, milling cutters are widely used in the manufacturing industry. Sandvik Coromant, a leading specialist in cutting tools for various applications, offers a wide range of milling cutters designed to deliver precision and productivity in machining operations.
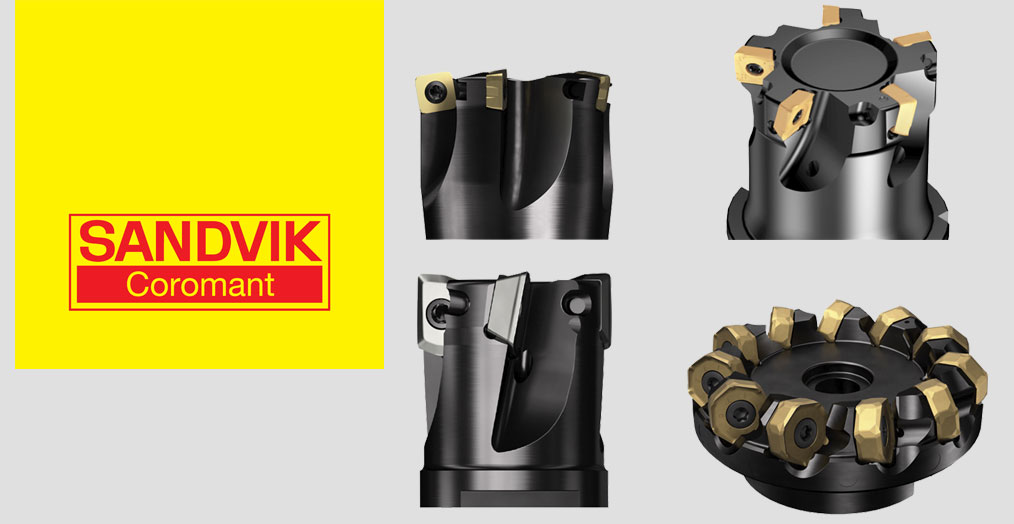
AMS Company Limited is the official distributor of Sandvik Coromant products in Vietnam, offering you access to state-of-the-art milling cutters that can enhance your productivity and efficiency.
In this article, we will highlight the differences between two popular types of milling operations: end milling and face milling. Understanding these differences can help you choose the right tool for the job.
One essential consideration when selecting milling cutters is the type of milling operation required. Two primary types of milling operations are end milling and face milling. The main difference between these two is the direction of the cutting forces. In end milling, the cutting forces are predominantly radial to the rotation of the tool. On the other hand, in face milling, the cutting forces are axial.
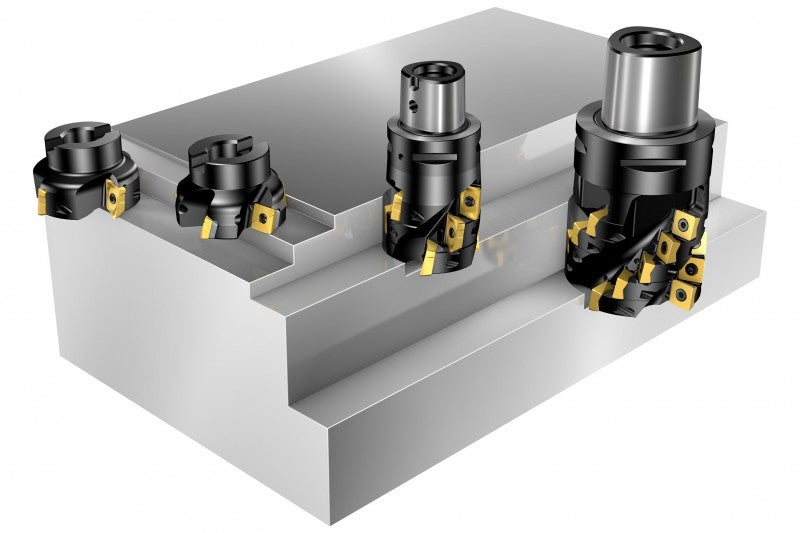
1. End Milling
End milling is suitable for producing slots, pockets, and other similar features. Sandvik Coromant's Solid Carbide End Mills, for instance, are designed to deliver excellent surface finish and accuracy in applications such as profiling, ramping, and plunging. These end mills come in various geometries, coatings, and sizes to suit different materials and machining requirements.
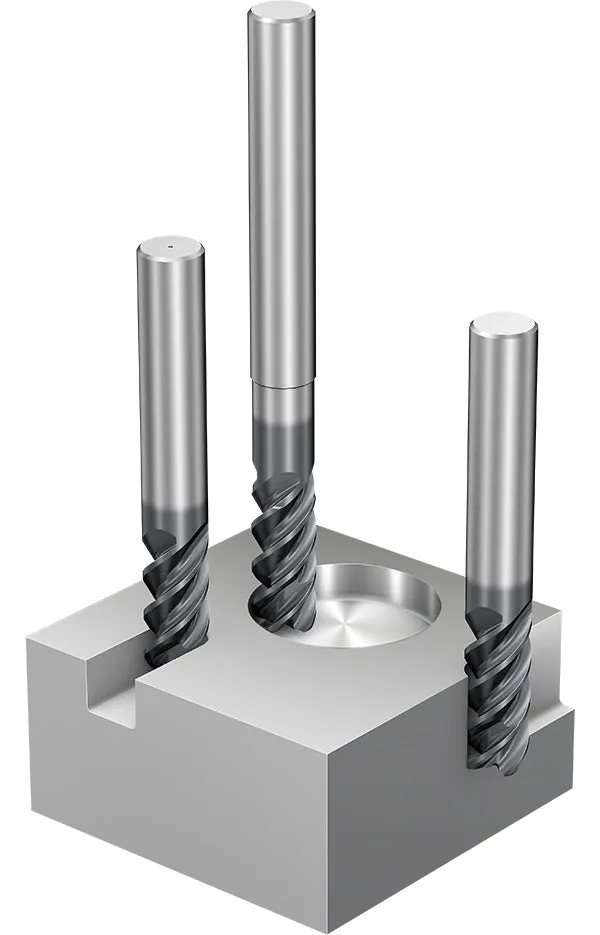
The Sandvik Coromant CoroMill Plura and CoroMill 316 milling cutters are excellent tools for end milling. These cutters feature a high-performance coating that provides improved wear resistance and a longer tool life. The geometries of these cutters are optimized to reduce vibrations and enhance chip evacuation, leading to a more efficient milling process.
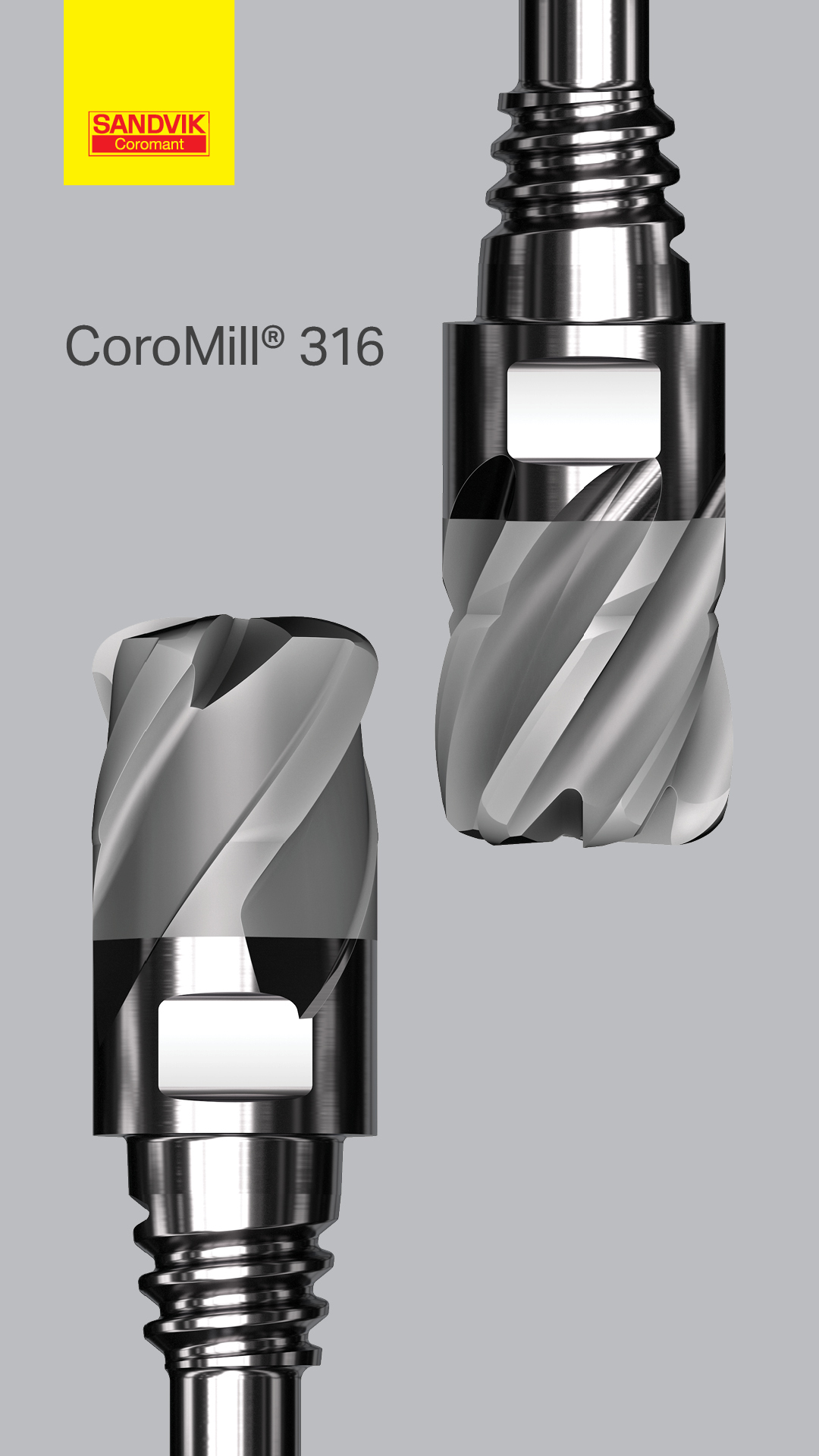
2. Face Milling
Face milling, on the other hand, is ideal for machining large flat surfaces and creating square edges. Sandvik Coromant's Face Milling Cutters, such as the CoroMill 200, are designed to maximize metal removal rate while ensuring high accuracy and smooth finishes. These cutters come in different types, including high-feed, plunge, and profile cutters, to match a wide range of applications.
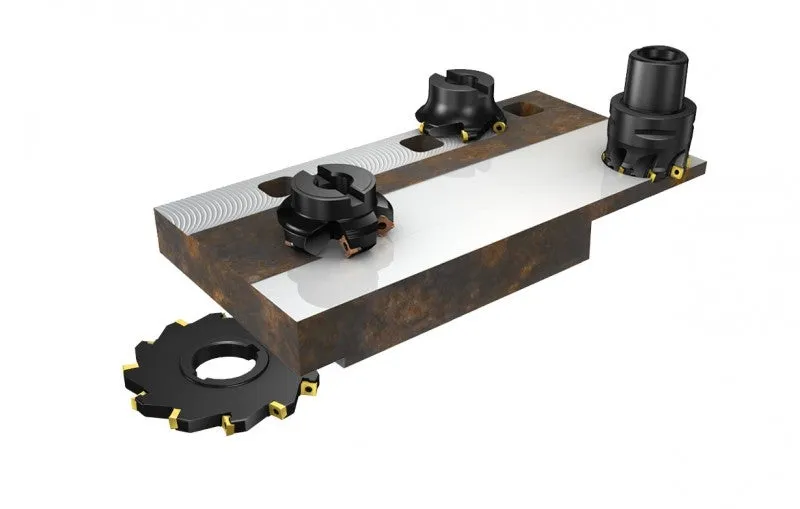
The Sandvik Coromant CoroMill 360 and CoroMill 419 milling cutters are excellent tools for face milling. These cutters feature a unique insert design that allows for a more precise and stable machining process. They also have a high metal removal rate, which results in faster and more efficient machining.

3. Factors to consider when selecting milling cutters
Apart from the cutting operation, other factors to consider when selecting milling cutters include the type of material to be machined, the machine tool, and the operating parameters. Sandvik Coromant provides comprehensive technical support and machining expertise to help clients optimize their machining processes and achieve their productivity and quality objectives.
In conclusion, choosing the right milling cutter and the appropriate milling operation is crucial in achieving optimal machining results. With Sandvik Coromant's wide range of high-performance milling cutters and machining solutions, clients can maximize their productivity, profitability, and competitiveness in various industries. Explore our website to learn more about our milling cutters and other cutting-edge tools for metal cutting and beyond.
Contact us today to learn more about how Sandvik Coromant milling cutters can enhance your machining process.
AMS Company, Ltd.243/9/10D To Hien Thanh, Ward 13, District 10
Hot line: 028.3868 3738/3903 - Fax: 028.3868 3797