The Power of Safe Absolute Position Values in HEIDENHAIN Linear Encoders
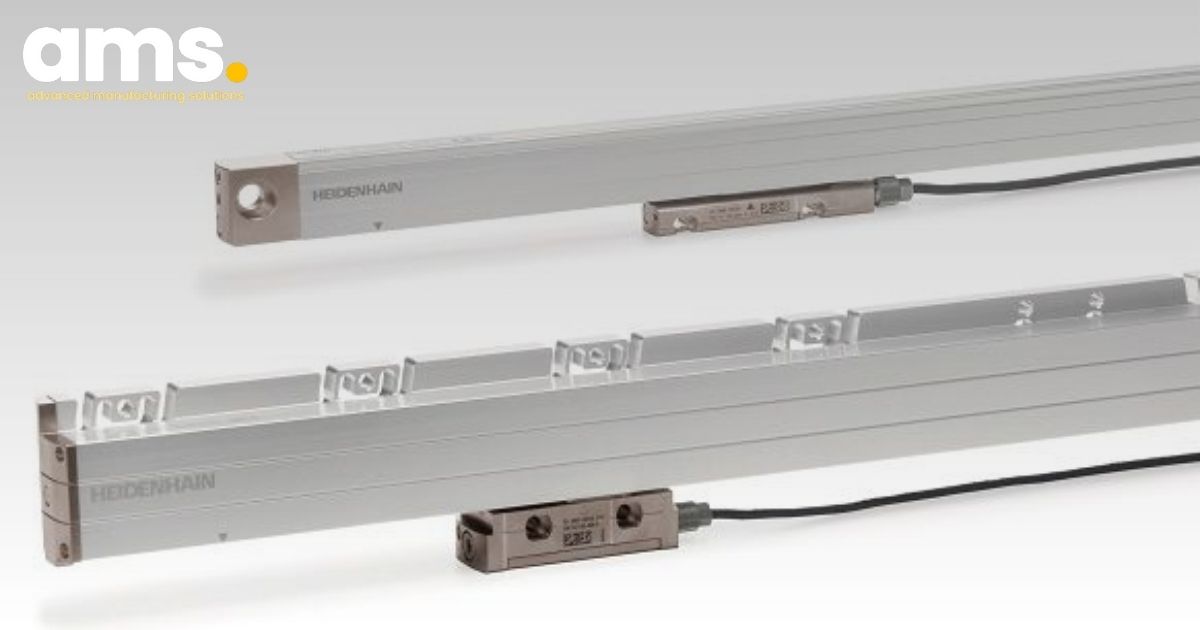
Over the years, HEIDENHAIN absolute linear and angle encoders have become the preferred choice for machine tools that demand high accuracy, reliability, and productivity. These encoders utilize the absolute measuring method, providing the position value immediately upon switch-on and enabling its retrieval at any time without the need to move the axes to find the reference position. This absolute position information is obtained from the scale graduation, which features a serial absolute code structure. Due to the inherent advantages of absolute encoders, HEIDENHAIN now prioritizes their production in larger quantities compared to the incremental versions.
The evolving technical requirements in machine and plant manufacturing, coupled with stricter safety standards at national and international levels, have led to the introduction of a new generation of sealed linear encoders in the market. At the core of these new encoders lies a groundbreaking innovation – the HEIDENHAIN OPTO-ASIC, developed based on 15 years of research and development experiences. By integrating optical elements, analog circuits, and digital signal evaluation on a single chip, the signal quality and reliability have significantly improved. Furthermore, the OPTO-ASIC incorporates functions that enable the operation of these encoders in safety-critical applications, leading to the absolute linear encoders of the LC 115 and LC 415 series achieving SIL2 in accordance with IEC 61508 and performance level d of ISO 13849 as single-encoder systems. Additionally, the necessary safe mechanical connection mandated by the standards has been effectively implemented.
With an impressively swift formation of the position value within 5 µs and a remarkable resolution down to 1 nm, these encoders offer limitless possibilities for application in machine tools. In addition to encoders for the RS 485 interfaces, such as EnDat 2.2, FANUC, and MITSUBISHI, HEIDENHAIN also offers encoders for the Ethernet-based interface from SIEMENS.
HEIDENHAIN regards ASIC design, ASIC qualification, and all modern manufacturing methods, including COB (chip on board) or flip-chip assembly, as crucial expertise that should not be outsourced. The company's high manufacturing depth and the collaboration of interdisciplinary processes involving mechanical and electronics R&D at a single location form the basis for the exceptional reliability of series production of absolute and incremental encoders.
1. Makeup of the encoders
The absolute linear encoders, available in the full-size LC 115 and slim-line LC 415 versions, feature a scale consisting of a 20 µm incremental grating and an absolute grating with a serial Pseudo Random Code (PRC).
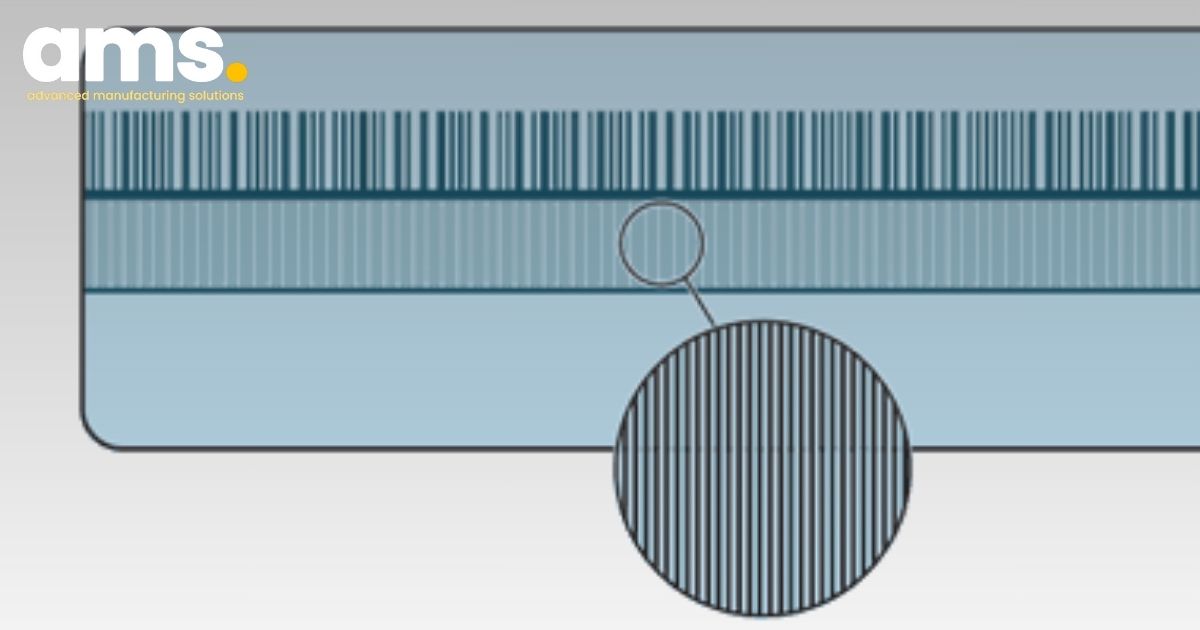
The incremental track is scanned using the well-established single-field method, which significantly differs in signal quality and reliability compared to the three- or four-field methods. The extensive scanning area across the entire width of the scale grating, along with the arrangement of multiple scanning fields in succession, renders the encoders with single-field scanning highly resistant to contamination. Rigorous contamination tests have demonstrated that even when large areas are contaminated, the encoder consistently delivers high-quality signals, maintaining the position error well below the specified accuracy grade of the encoder.
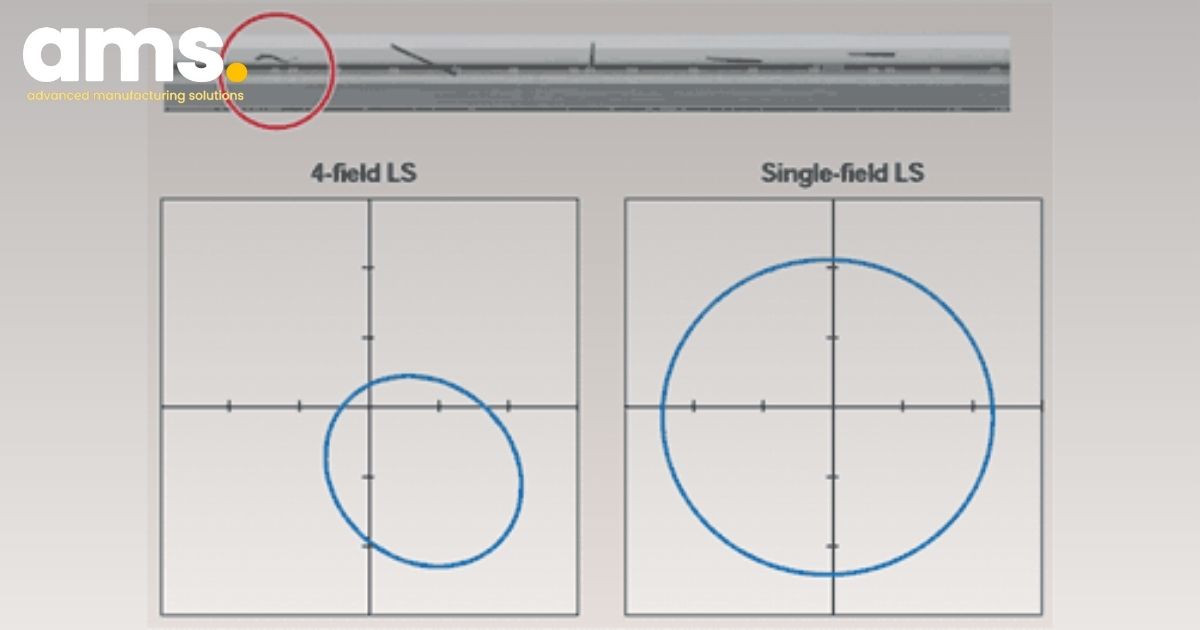
Left: four-field scanning, right: single-field scanning
An established technique from absolute rotary encoders, previously unused in linear encoders, was adopted to generate the absolute encoder signals. The individual PRC bits are scanned differentially, with each bit comprising a dark and a light field. Similar to the differential data transfer of an RS 485 interface, disturbances affect both fields and minimally impact signal processing. The fusion of these technologies ensures the attainment of exceptional signal quality and reliability.
2. Functional safety
Safety is increasingly crucial in machine and plant construction, evidenced by new legislation and the heightened safety requirements of national and international standards. These stringent requirements are primarily aimed at protecting humans, while also giving more consideration to material assets and the environment.
To meet the elevated demands on measuring technology set by the new standards, HEIDENHAIN and TÜV-Süd collaborated to subject HEIDENHAIN's safety concept to type examination. The certification covers the entire system – from the formation of the position value through data transmission to evaluation in the subsequent electronics. The assurance of mechanical elements remaining securely in place represents the final aspect of this consideration. The new absolute linear encoders of the LC 115/415 series are the first linear encoders capable of providing the OEM with a PFH value for consideration of the complete system. The range of encoders available with functional safety will gradually expand, with plans for certification of the RCN series of angle encoders in 2012.
In cases where a machine tool builder has developed a distinct safety concept, HEIDENHAIN can provide assistance with MTTF values and a fault table specifically tailored for the encoder. However, it is imperative that details in both cases are always aligned with the machine tool builder.
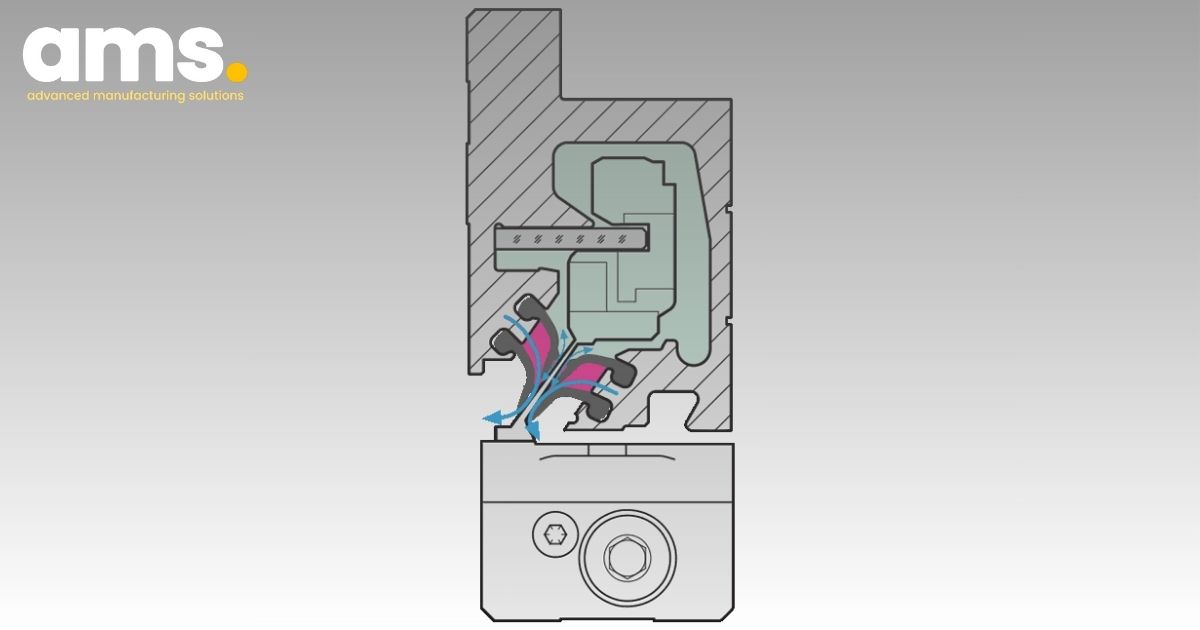
3. Reliability
The efficiency of a machine tool relies on its accuracy (ability to safely produce the required part quality), dynamics (time taken), and availability. The new LC encoders set new benchmarks in all three aspects. The achievable accuracy has been previously discussed. In terms of dynamics, the permissible traversing speed of 3 m/s and a maximum acceleration in the measuring direction of 10 g should not limit linear motion.
Utilizing filtered compressed air alongside linear encoders ensures maximum reliability by creating an overpressure in the encoder, preventing the entry of dirt and liquids.
Considering that surges of condensed liquids might occur in compressed air supplies, the LC 115 incorporates a design feature to minimize the impact of such contamination. The compressed air is channeled into a "chamber" between the inner and outer pairs of sealing lips, creating a primary flow from the encoder and a much smaller secondary flow of compressed air into the encoder interior. This effectively prevents direct contamination entry into the encoder, thereby ensuring that temporarily contaminated sealing air no longer affects reliability.
4. HEIDENHAIN LC 211—absolute even over lengths up to 28 meters
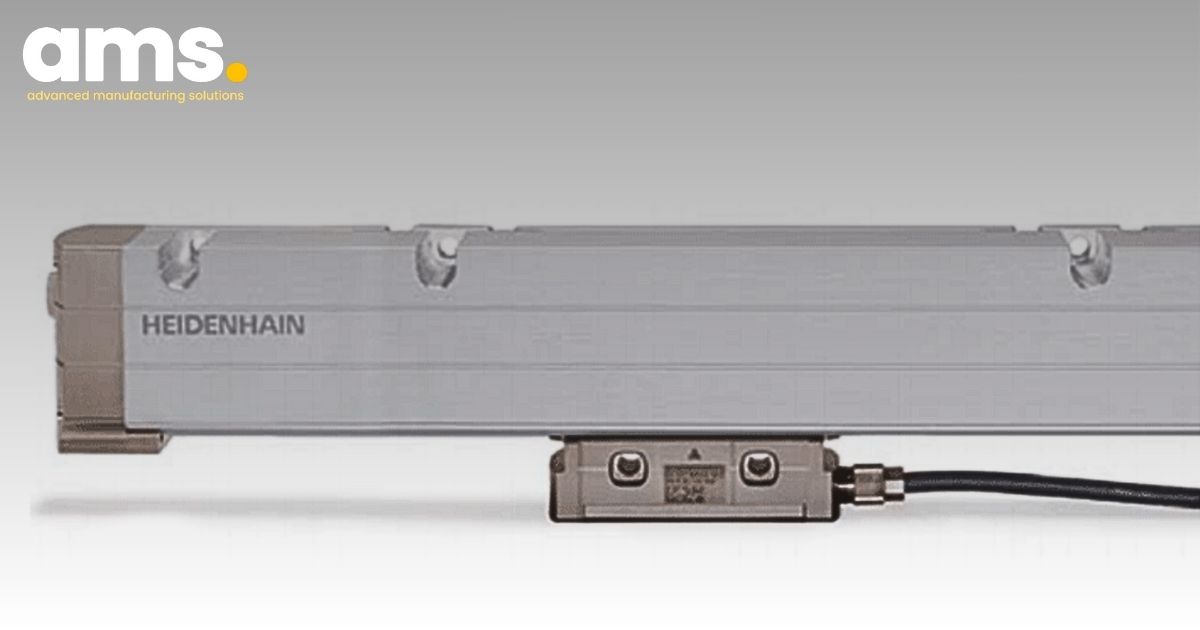
The LC 211 represents a significant advancement in linear measurement for long machine-tool axes. As the successor to the well-established multi-section LB 382 linear encoder, it now offers the benefits of absolute position acquisition for measuring lengths of up to 28 meters. The LC 211 utilizes the previously described new OPTO-ASIC, albeit with a modified beam path, as it employs a steel tape rather than glass as the measuring standard. This METALLUR steel tape graduation, also featured in the LB 382, comprises a 40 µm incremental track and a PRC track, incorporating a highly reflective gold layer and light-absorbent grating lines. The scanning process delivers unique absolute position values across the entire measuring length with a resolution as fine as 10 nm.
Given the extensive measuring lengths of up to 28 m, the use of long cables becomes unavoidable. Serial data transmission is particularly advantageous for such applications as signals from a 1 VPP interface experience a significantly diminished usable component due to the extended cable lengths. In contrast, the serial interface ensures data transmission without loss, irrespective of the cable length. Similar to the LC 100 and LC 400, the LC 200 will support protocols for the EnDat, FANUC, and MITSUBISHI interfaces.
To simplify the mounting of such a long encoder, a new mounting technique has been devised for the LC 211. The seals are pre-assembled on sections, which can reach up to 2 meters in length, offering a tolerance of up to 2 mm in the measuring direction during mounting. It is critical to maintain the mounting tolerance for the overall measuring length to ensure the proper functioning of the clamping mechanism. This new mounting strategy significantly reduces the time required for installation while concurrently enhancing the quality and reliability.
5. Summary
The new sealed LC 115/415 linear encoders represent a significant advancement, offering enhanced accuracy, reliability, and safety. The integration of single-field scanning and digital signal processing ensures the provision of highly precise absolute position values. Additionally, the inclusion of double sealing lips enhances the encoders' resistance to temporarily contaminated compressed air. With certification from TÜV, a single-encoder system can provide secure, purely digital absolute position values. The LC 211 extends the product line with large measuring lengths of up to 28 m. All LC encoders are compatible with EnDat, FANUC, and MITSUBISHI controls, and the LC 1×5/4×5 series can even be directly connected to the SolutionLine control from SIEMENS.
6. AMS Company Limited - Exclusive Distributor of HEIDENHAIN in Vietnam
AMS Company Limited is the sole distributor of HEIDENHAIN products in Vietnam. HEIDENHAIN, a reputable provider of precision measurement and control equipment, is renowned for the quality and reliability of its offerings. By partnering with us, you gain access to a wide range of HEIDENHAIN encoders suitable for various industrial applications.

For expert guidance in selecting the ideal HEIDENHAIN encoder tailored to your specific business needs, consult AMS Company Limited. Our experienced team is committed to understanding your requirements and proposing optimal solutions to streamline your operations. Whether your industry specialization is automotive, aerospace, medical, or general manufacturing, we are well-equipped to assist you in choosing the perfect HEIDENHAIN encoder for your specific applications.
When you procure HEIDENHAIN products through AMS, you benefit from HEIDENHAIN's comprehensive warranty and maintenance policy. This ensures that the products we deliver are covered under HEIDENHAIN's warranty, providing reassurance regarding the durability and performance of your investment. In contrast, purchasing from other sources may not offer the same level of protection under HEIDENHAIN's warranty and maintenance policy. Without this coverage, any malfunctions or unexpected issues could result in additional costs and disruptions to your operations.
Rely on AMS Company Limited as your exclusive partner in Vietnam to obtain authentic HEIDENHAIN products supported by reliable warranty and maintenance services. Reach out today to explore our selection of HEIDENHAIN encoders and benefit from the peace of mind that comes with working with the leading distributor in the region.
AMS Company, Ltd.243/9/10D To Hien Thanh, Ward 13, District 10
Hot line: 028.3868 3738/3903 - Fax: 028.3868 3797