PCD vs. CBN Cutting Tools: The Differences
Nowadays, PCD and CBN turning tools are widely used on the market. Cutting tool manufacturers have developed their own technologies for the production of their PCD and CBN tool lines.
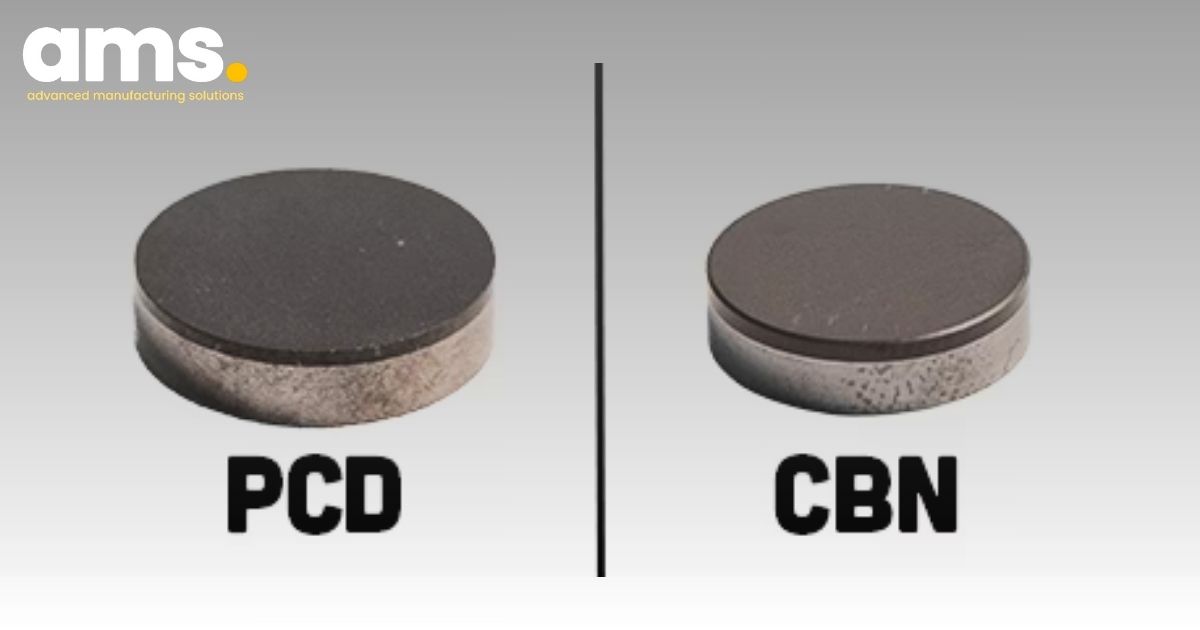
Sandvik Coromant stands as a prominent global supplier of cutting tools. They offer top-quality CBN and PCD inserts, leading the market in terms of quality and performance. The products of Sandvik Coromant are highly regarded for their exceptional quality and performance, effectively catering to the machining needs of companies and manufacturers across diverse industries. With their state-of-the-art production facilities and stringent quality standards, Sandvik Coromant continually conducts research and development to introduce new machining solutions and enhance the performance of their cutting tools, in accordance with the requirements and demands of their customers.
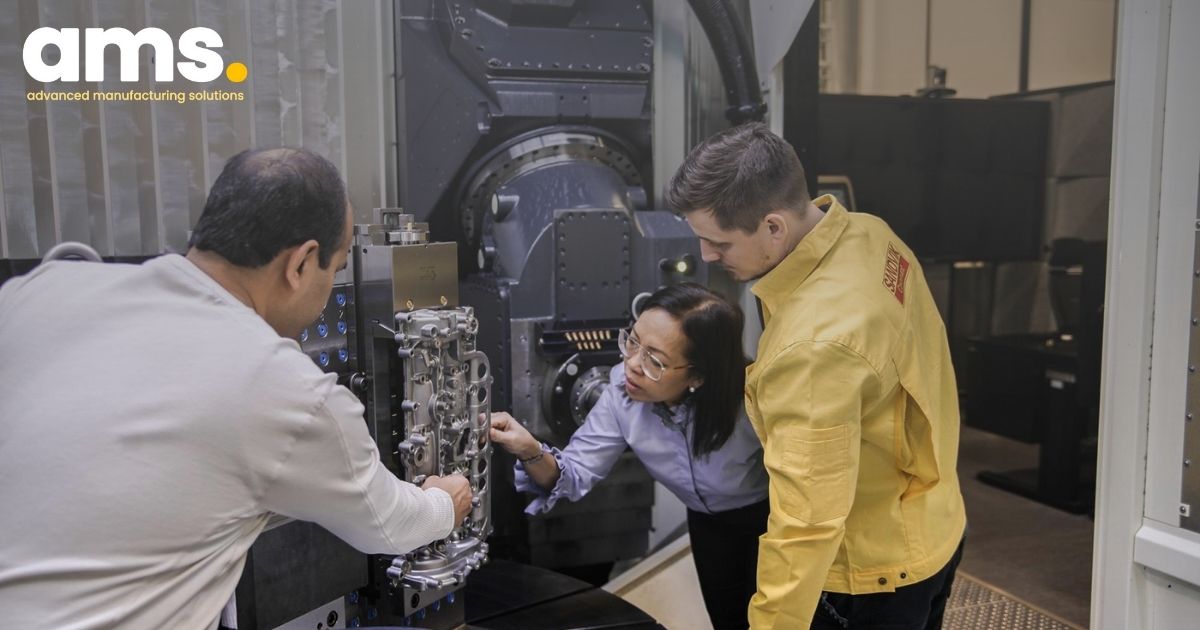
1. What is a PCD cutting tool?
PCD stands for Polycrystalline Diamond.
PCD is an advanced material created by sintering selected diamond particles at high pressure and temperature. This material can be used in many different fields such as aerospace industry, automobile manufacturing, electrical equipment, woodworking and stoneworking.
Here are some examples of Sandvik Coromant's PCD cutting tools:
-
CoroMill 600: This is a range of PCD milling cutters that are specifically crafted for the purpose of machining hard metals. With excellent hardness and exceptional heat resistance, these cutters find applications in various industries, including automotive, aerospace, and industrial sectors with a focus on metal processing.

-
CoroDrill PCD: This line of PCD drills is designed and optimized for the speedy and accurate machining of challenging materials like ceramics, carbon composites, and other rigid substances. The key strength of these tools lies in their ability to perform deep drilling tasks with utmost precision.

-
CoroTurn 107: The CoroTurn is a series of turning tools specially tailored for both external and internal machining operations. These tools are engineered to tackle demanding materials that demand high precision, such as alloy steel, cast iron, and composite materials. Offering excellent cutting performance, extended tool life, and exceptional machining accuracy, they are an ideal choice for precision machining applications.
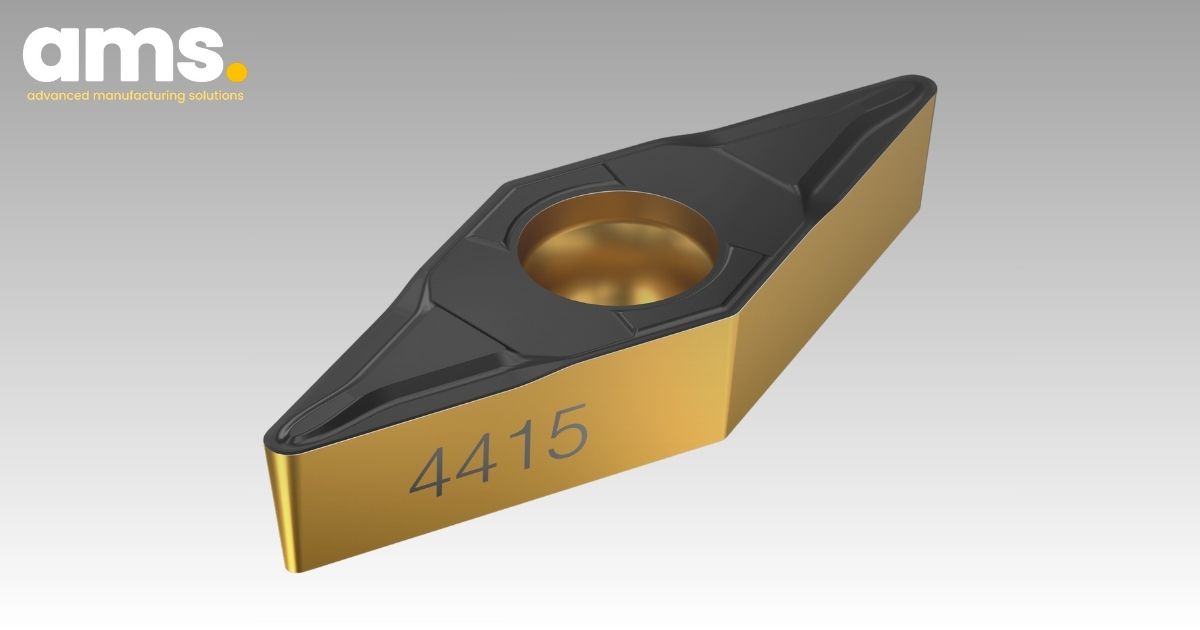
2. Advantages of PCD (Polycrystalline Diamond)
-
PCD knives exhibit exceptional hardness and wear resistance, resulting in extended tool life and cost reduction.
-
They are meticulously machined to deliver superior surface finishes, exemplifying high quality and a polished appearance.
-
These knives facilitate efficient processing, optimizing time usage.
-
The diamond coating enhances productivity by boasting remarkable resistance to wear.
-
Moreover, utilizing PCD knives allows for gentler pressure to be applied to the product.
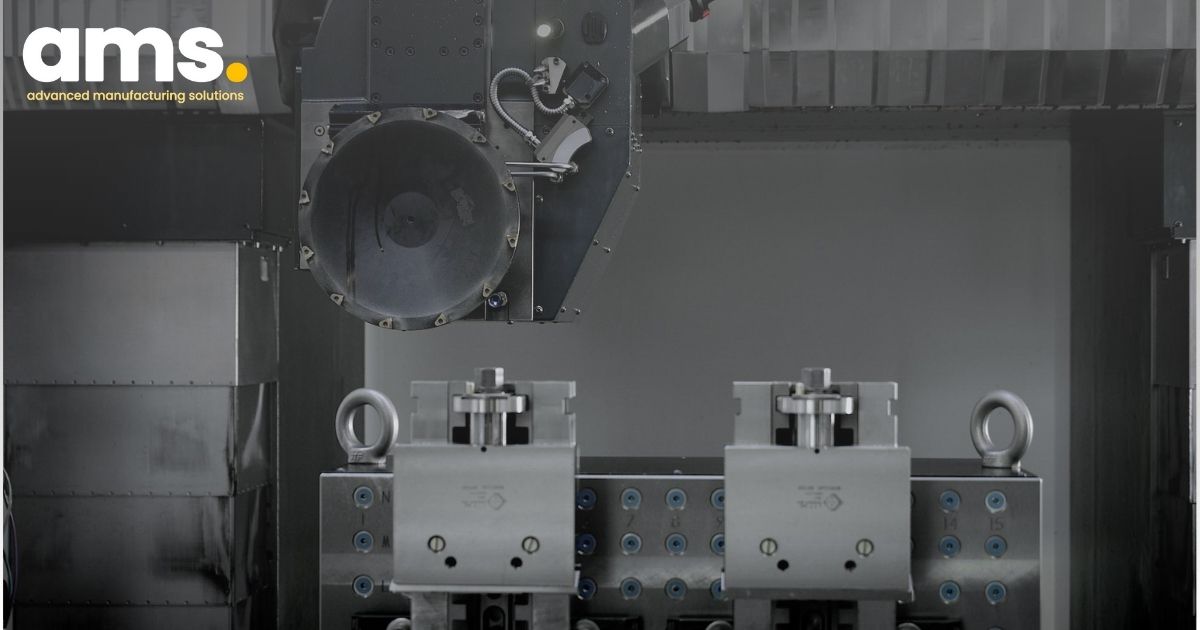
PCD (Polycrystalline Diamond) cutting tools find applicability across diverse operations such as CNC milling, grooving, CNC turning, CNC boring, and more. PCD inserts are particularly suited for non-ferrous materials such as aluminum, aluminum alloys, copper, brass, copper alloys, as well as gold, silver, tungsten carbide, titanium, ceramics, carbon fiber polymers, graphite, glass resins, and wood.
PCD knives are employed across multiple industries, capable of achieving high cutting speeds. In specific applications, their lifespan can outlast that of alloy cutting tools by 10 to 50 times. Additionally, PCD inserts offer numerous advantages comparable to natural diamonds in certain industrial sectors.

3. What is a CBN cutting tool?
CBN is an abbreviation for Cubic Boron Nitride, a crystalline nitrogen compound with a unique four-membered structure.

To create CBN material, submicron-sized CBN particles are melted together at high temperatures and pressures without the need for adhesives. This process enhances the material's hardness, thermal conductivity, and the advantages of titanium and cobalt chromium.
CBN is incredibly hard, nearly twice as hard as Al2O3, and can withstand temperatures up to 1,371 degrees Celsius before breaking. It has excellent cutting capabilities on steel and outperforms diamond in many applications.
CBN is commonly used for the production of highly hardness materials, especially those that exhibit a hardness of approximately 48-72 HRC after heating. However, materials with a lower hardness are not suitable for CBN machining as it may cause rapid wear.
CBN is a synthetic material known for its exceptional hardness, second only to diamond. Unlike diamond, CBN is particularly well-suited for machining hard metals under high-temperature and dry cutting conditions.
Among Sandvik Coromant's CBN cutting tool lines are:
-
CoroTurn CBN series: This popular line of CBN turning tools is specifically designed for machining hard metals. With high hardness and excellent wear resistance, these knives increase tool life and improve machining efficiency.
-
CoroMill CBN series: These CBN milling cutters are optimized for machining high-hardness materials such as alloy steel and gray cast iron. They possess powerful cutting capabilities and high precision, resulting in shiny and precise machined surfaces.
-
CoroDrill CBN series: These CBN drill tools are suitable for precise and efficient drilling in hard materials. Designed with high hardness and durability, this line of knives enhances productivity and reduces machining time.

4. Advantages of CBN (Cubic boron nitride)
-
Offers exceptional resistance to impact and abrasion, ensuring extended tool life.
-
Enables the achievement of a polished surface comparable to that obtained through grinding.
-
Delivers excellent surface finish and dimensional control for high precision machining.
-
Provides impressive torsion and bending resistance.
-
Suitable for continuous or high-impact machining applications.
-
Ideal for both roughing and finishing operations.
-
Highly effective in machining steels with high carbon content or those that have undergone heat treatment.
-
Offers excellent cost performance, with CBN inserts lasting over 10 times longer than carbide inserts, resulting in cutting tool cost reductions of 30%-50%.
-
Longer intervals between insert replacements reduce machine downtime caused by tool changes.
-
CBN tools have expanded their utility beyond grinding to turning, drilling, milling, and grinding hard materials.
-
Enhances processing efficiency, increasing equipment capacity and reducing investment requirements.
-
Capable of both dry and wet machining.

CBN tools are widely used in turning, drilling, milling, and grinding of hard materials, which were previously limited to grinding methods. The exceptional hardness of CBN grinding wheels allows for precise machining with minimal adjustments and the ability to sustain consistent performance without frequent sharpening.
The utilization of CBN tools has successfully resolved numerous challenges encountered in machining. CBN is commonly applied in the processing of heat-treated steels, carbon tool steels, mold steels, high-speed steels, forged steels, cast iron, gray cast iron, and more.
5. CBN classification based on composition
-
50% CBN composition: Ideal for materials with a hardness range of 50-60 HRC. This CBN blade is well-suited for high-speed machining procedures involving light cuts and no interruptions.
-
60% CBN composition: Specifically developed for materials with a hardness range of 50-60 HRC, this CBN tool performs admirably in both roughing and finishing applications, even tolerating occasional interruptions in continuous machining.
-
65% CBN composition: Demonstrates excellent performance in materials with a hardness range of 60-65 HRC. This CBN tool excels in tougher applications and can handle a higher frequency of interruptions.
-
75% CBN composition: Tailored for the most challenging applications, this form of CBN tool is highly resistant to impact and excels in heavily interrupted cuts.
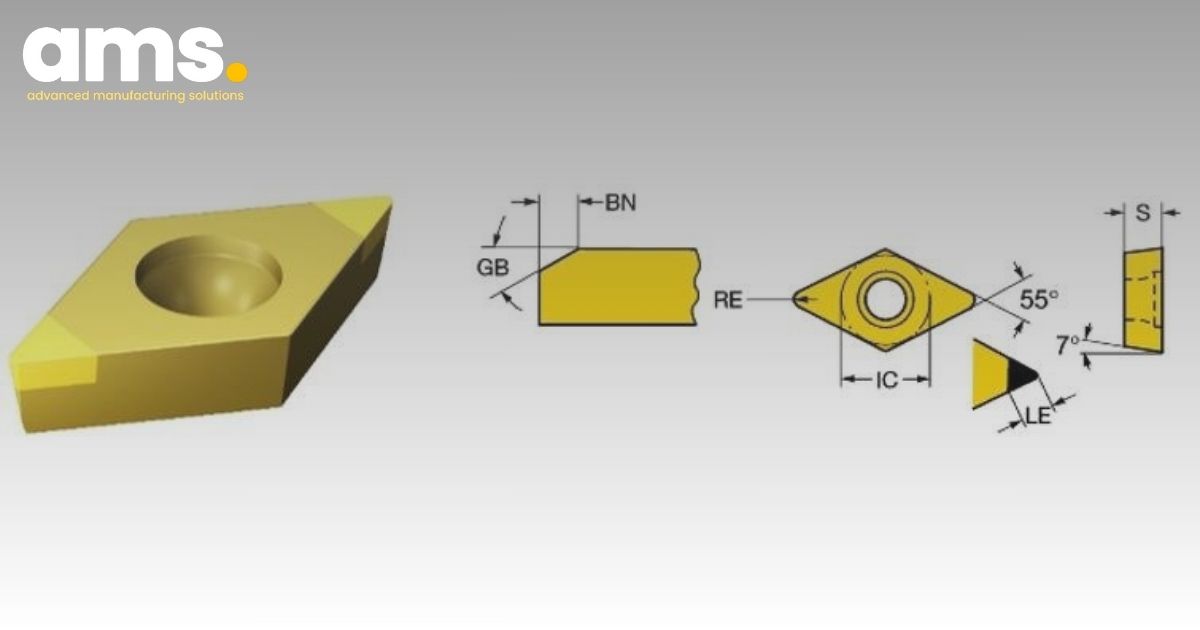
PCD tools and CBN tools each have their own unique applications and advantages. It is advisable to consult with the manufacturer to ensure the suitability of the cutting tools for each specific application.
AMS Company Limited, the authorized distributor specializing in providing authentic Sandvik Coromant products in Vietnam, is your go-to source. If you're uncertain about which tool type to select for your application, please feel free to contact AMS for a complimentary consultation. With over 20 years of experience in delivering precision mechanical products, AMS takes pride in being a leading provider and possesses the enthusiasm and expertise to guide and support you.
AMS Company, Ltd.243/9/10D To Hien Thanh, Ward 13, District 10
Hot line: 028.3868 3738/3903 - Fax: 028.3868 3797