Maximizing Quality: How HEIDENHAIN Inductive Multiturn Rotary Encoders Boost Control
Owners of machinery such as machine tools, robots, and automation systems consistently seek high-performance, cost-effective solutions. To meet this demand, compact, energy-efficient drives with safety features have been developed. These drives cater to diverse applications, requiring functionally safe encoders for both high-end machine tool drives and standard uses. HEIDENHAIN has introduced the third-generation ECI/EQI 1100 series bearingless rotary encoders with inductive scanning, sized at 37 mm, to expand its range of dynamic and energy-efficient servo drives for safety-critical applications.
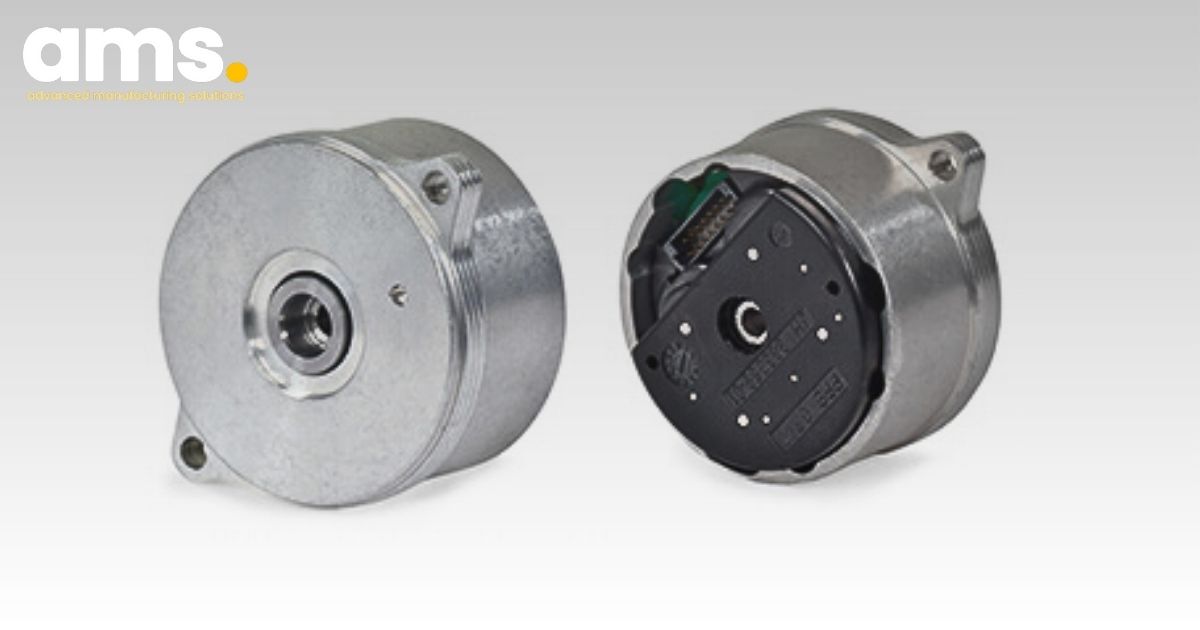
1. Compact, durable and safe in applications up to SIL 3
Using a newly designed ASIC, HEIDENHAIN has created a functionally safe inductive rotary encoder for the 37mm segment. This encoder complies with safety integrity level SIL 2, Category 3 PL d, and can potentially reach SIL 3, Category 4 PL e with additional control measures. Enhanced mechanical fault prevention ensures shaft and stator coupling integrity.
System accuracy has doubled to ± 120 angular seconds compared to previous iterations. These encoders boast contamination-resistant inductive scanning, ensuring durability. The new ECI 1119 FS (single-turn) and EQI 1131 FS (multi-turn) rotary encoders are compatible with the ECN/EQN 11xx FS series optically scanned rotary encoders with built-in bearings. This enables scalability based on application control needs while reducing motor variants.
Significant improvements in mechanical tolerance have been made, with, for instance, a twofold increase in allowable axial movement. For easy installation verification, the encoder provides mating dimension values read by the servo inverter through the EnDat interface. The new inductive rotary encoders feature temperature monitoring for both the encoder and motor through integrated and external temperature sensors, respectively. This data is digitally accessible via the EnDat 2.2 interface without disrupting the control cycle.
2. Control quality compared with optically scanned encoders
In the upcoming illustration, we use an actual motor as a case study to contrast the latest inductive rotary encoders with earlier versions and an optically scanned EQN 1135 encoder. We selected a model with exceptionally low cogging torque for the measurements to minimize potential motor effects. An ultra-precise angle encoder, boasting a measuring accuracy of better than ± 1 angular second, was affixed to the motor's output shaft to evaluate the drive system's accuracy and rotational speed stability.
3. System accuracy
The precision of a system plays a vital role in determining its appropriateness for particular uses. Figure 2 displays the accuracy data of the three encoders. The latest EQI 1131 inductive rotary encoder exhibits significantly lower short-range measurement errors compared to the EQI 1130. Unsurprisingly, the optically scanned EQN 1135 encoder delivered the most accurate results.
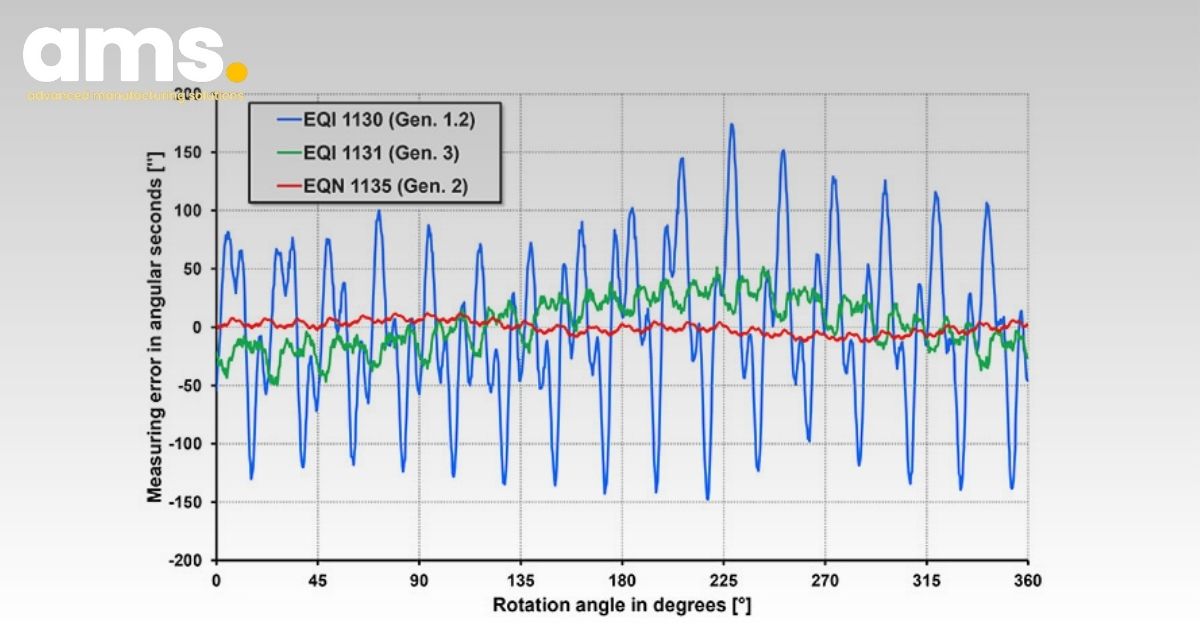
4. Dynamic behavior in the control loop
The dynamic characteristics of the control loop were examined using a cascading control structure encompassing motor currents, speed, and position. To ensure a fair comparison, identical control parameters were implemented across all tested encoders (control cycle time of 100 µs, speed controller proportionality gain set at 1400 1/s). Figure 3 illustrates the amplitude frequency response of the closed speed control loop for the three encoders (Bode plot), showcasing a control bandwidth of around 600 Hz for all. Notably, no resonance points were detected, indicating that the achievable dynamics are predominantly determined by the controller parameters. HEIDENHAIN rotary encoders offer a wide bandwidth, allowing for high-performance systems where the encoders do not constrain the overall dynamics but instead the intricate control paths.
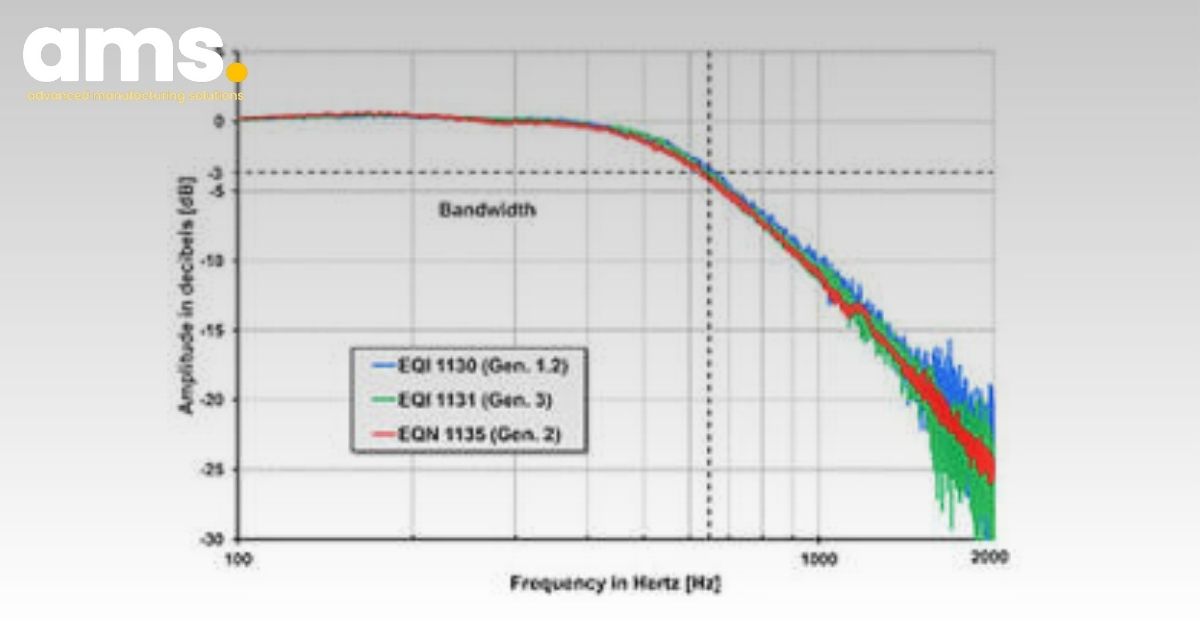
The elevated speed controller gain effectively minimizes mechanical disturbances on the motor shaft but also intensifies measurement errors in the rotary encoder. Consequently, especially with high-performance servo motors, the encoder's influence, rather than mechanical factors like cogging torque, significantly impacts speed stability. In Figure 4, the speed stability of the controlled motor at various speeds is displayed. The new inductive rotary encoder exhibits comparable speed stability to its optical counterpart, owing to its resilient scanning and enhanced vibration resistance (stator: ≤ 400 m/s², rotor: ≤ 600 m/s²), making it well-suited for industrial machinery. The improved speed consistency in the new inductive encoder primarily results from reduced short-range position errors.
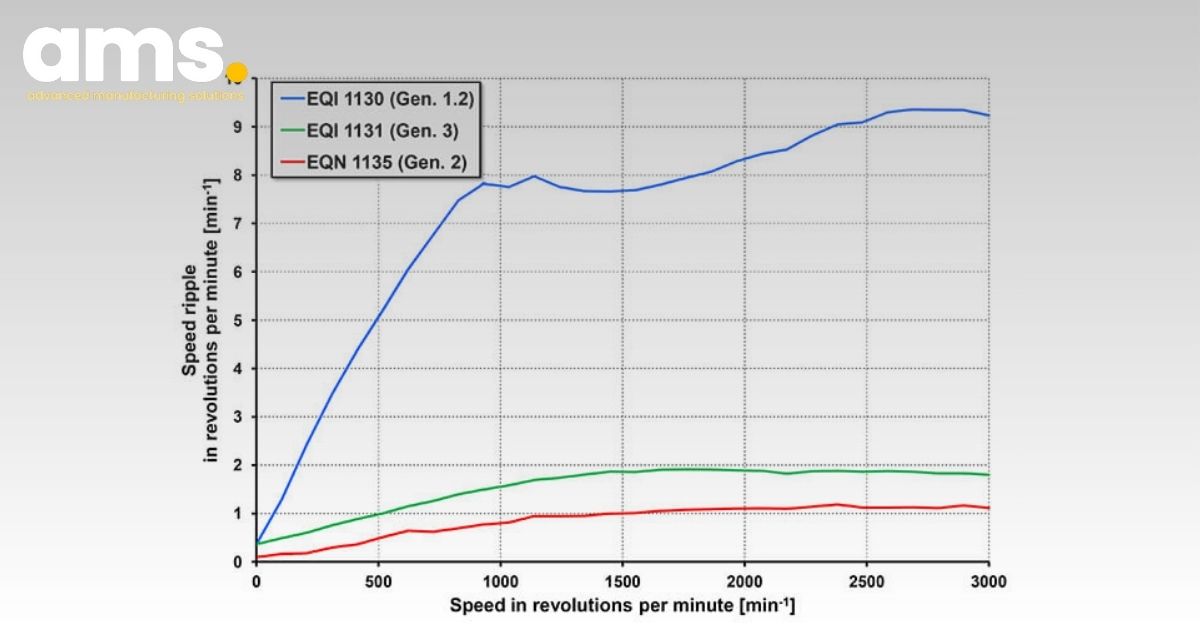
In drive systems, limited resolution manifests as quantization noise in measured speed. This noise is most pronounced at high frequencies due to the calculation of speed from the (quantized) position derivative. The high-frequency noise is introduced into the current control loop via the speed control loop, leading to motor forces and torques that can excite mechanical frequencies and manifest as noise emission. Moreover, this process contributes to increased motor losses, negatively impacting energy efficiency. Hence, high position resolution is imperative for highly responsive drives.
5. Position error in the position control loop
The accuracy and/or reproducibility of the rotary encoder are crucial for positioning precision, depending on the task at hand. Position errors around the nominal position result from noise sources within the drive system and the quantization of measured quantities (position, speed, and current). Achieving swift positioning necessitates high loop gains in both the speed and position controllers, which also introduces errors from the actual value acquisition into the control loop. For optimal performance in positioning mode, encoders offering the highest signal quality, such as those from HEIDENHAIN, are essential.
Encoder signal noise becomes significant when maintaining a specific motor shaft position. Both the inherent noise in the encoder pre-digitization and the quantization noise from finite position resolution result in actual value deviations in the control loop. As seen in Figure 5, the closed-loop control compensates for these deviations by generating torques that induce minor motor movements around the desired position. Notably, the optically scanned encoder outperforms the others, largely due to its superior effective resolution.
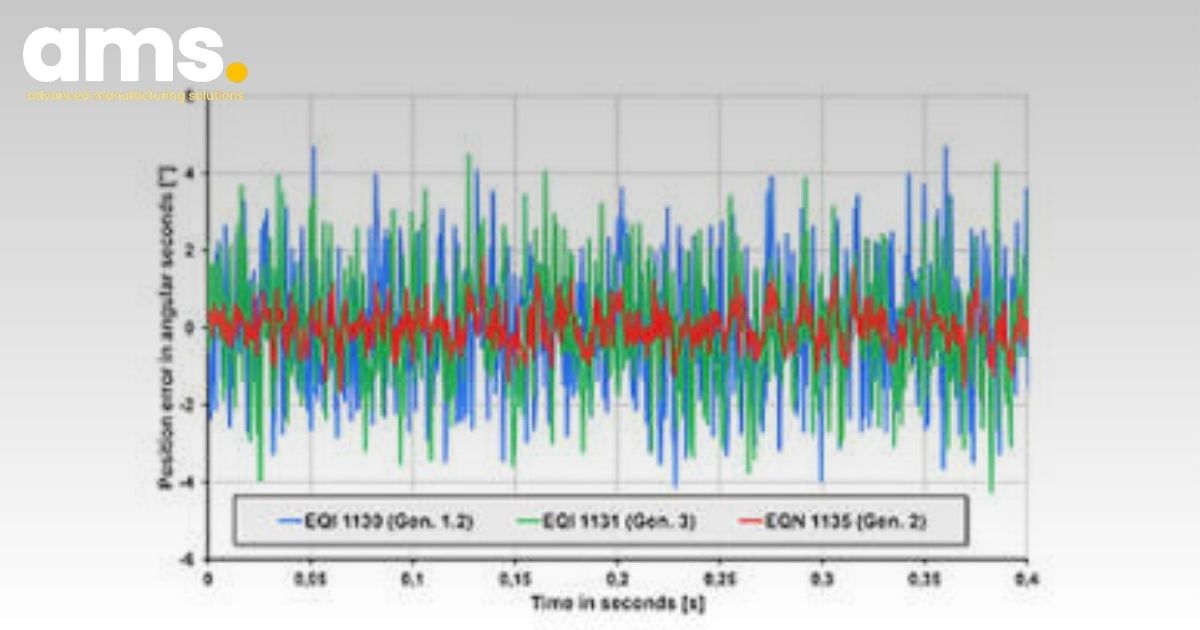
6. Summary and outlook
The third-generation ExI 11xx inductive multiturn rotary encoders offer the capability to integrate functionally safe systems up to SIL 3 using a single device. Their mechanical (installation) and electrical (EnDat 2.2 interface) compatibility with the ExN 11xx optically scanned rotary encoders allows for broad application coverage. Users can expect excellent control features, encompassing high accuracy, dynamic performance, efficiency, robust construction, compactness, and ample mounting tolerances, benefitting all users across diverse applications.
6.1 EQI 1130 Generation 1.2
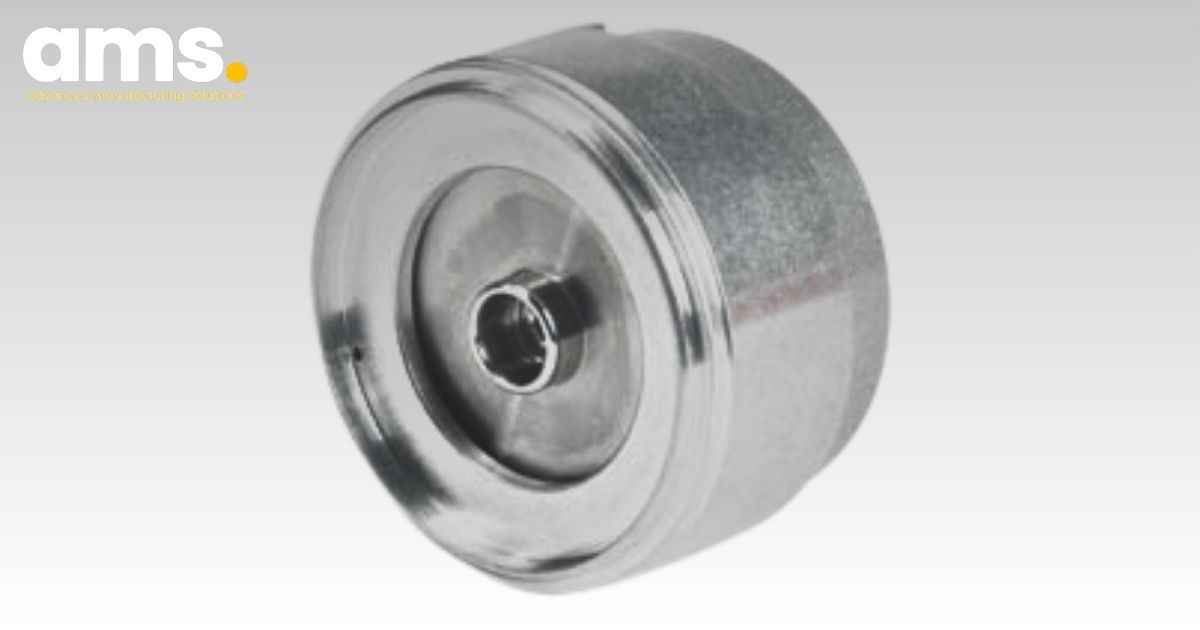
-
EnDat 2.1 (18-bit singleturn, 12-bit multiturn), ≤ 2 MHz clock
-
No analog signals (purely serial)
-
Without integral bearing
-
Without support for temperature evaluation
-
System accuracy ±280”
-
Permissible axial motion of the drive shaft ±0.2 mm
-
Vibration resistance in compliance with EN 60068-2-6:
-
Stator ≤ 300 m/s²
-
Rotor ≤ 300 m/s²
-
For applications with moderate requirements for control quality and accuracy
6.2 EQI 1131 Generation 3
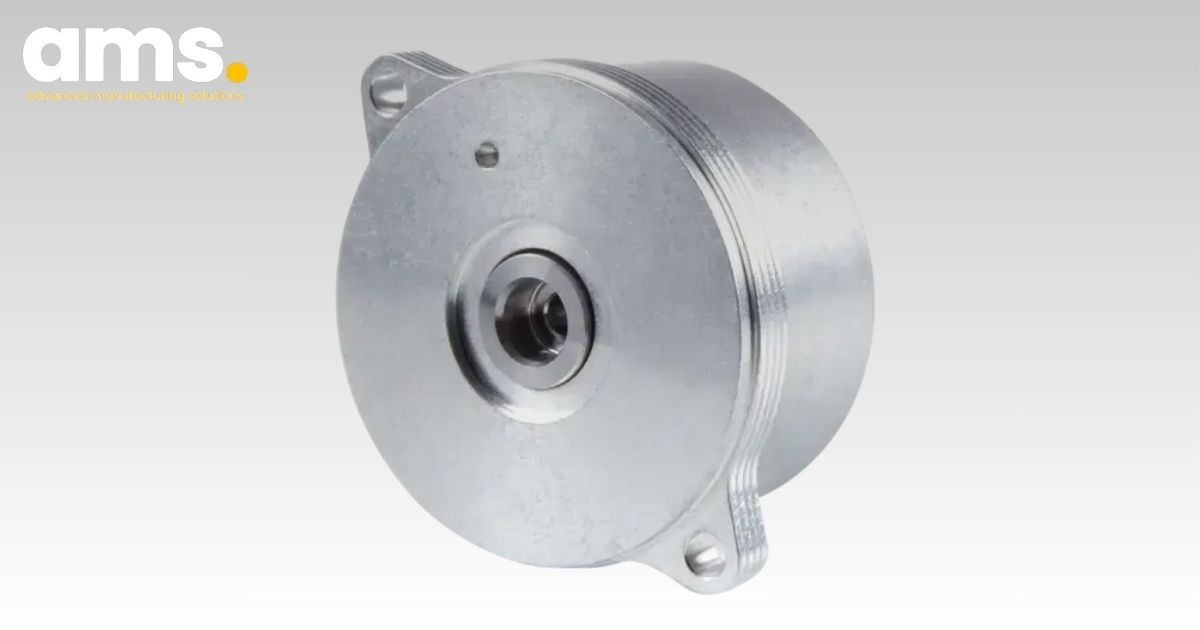
-
EnDat 2.2 (19-bit singleturn, 12-bit multiturn), ≤ 16 MHz clock
-
No analog signals (purely serial)
-
Without integral bearing
-
Evaluation of an integral and an external temperature sensor
-
System accuracy ±120”
-
Permissible axial motion of the drive shaft ±0.4 mm
-
Vibration resistance in compliance with EN 60068-2-6:
-
Stator ≤ 400 m/s²
-
Rotor ≤ 600 m/s²
-
Optimum for modern production machines with functional safety
6.3 EQN 1135 Generation 2

-
EnDat 2.2 (23-bit singleturn, 12-bit multiturn), ≤ 8 MHz clock
-
No analog signals (purely serial)
-
With integral bearing
-
Evaluation of an integral and an external temperature sensor
-
System accuracy ±60”
-
Permissible axial motion of the drive shaft ±0.5 mm
-
Vibration resistance in compliance with EN 60068-2-6: ≤ 300 m/s²
For high-end drives for machine tools with functional safety, for example
7. AMS Company Limited as Vietnam HEIDENHAIN exclusive distributor
AMS Company Limited is the exclusive distributor of HEIDENHAIN products in Vietnam, committed to ensuring the availability of authentic HEIDENHAIN products with uncompromising quality. These products not only come with the renowned HEIDENHAIN warranty but are also supported by a comprehensive maintenance policy.
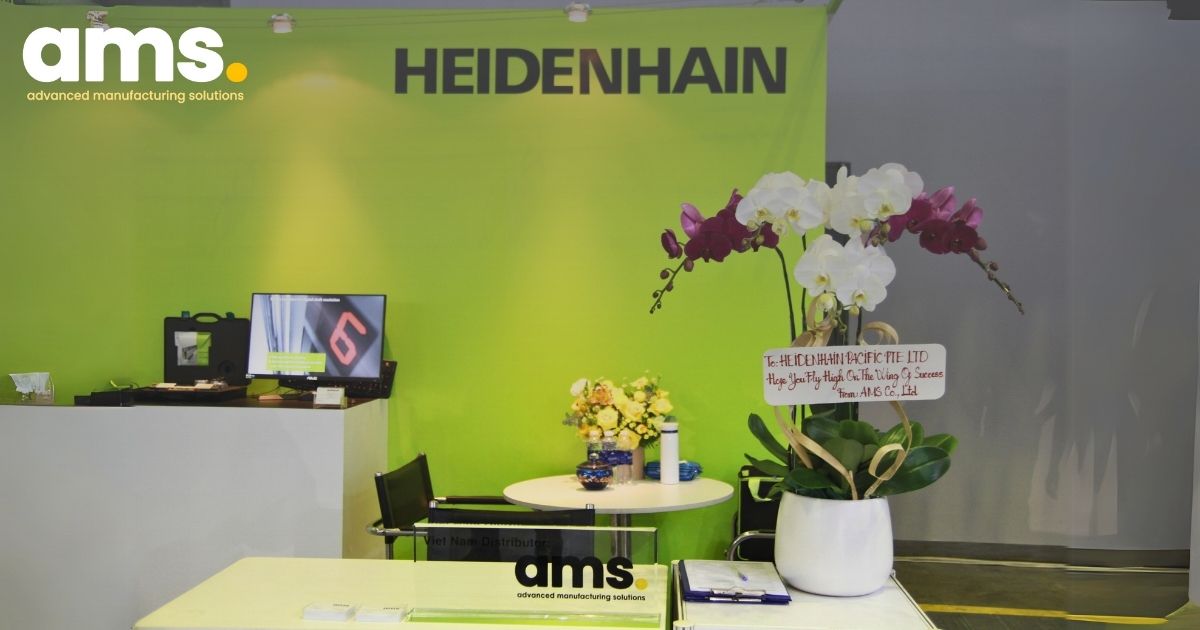
7.1 Benefits of Choosing AMS for HEIDENHAIN Products
Genuine Warranty and Maintenance: Acquiring HEIDENHAIN products from sources other than AMS may lead to ineligibility for the full benefits of HEIDENHAIN's warranty and maintenance policy. Therefore, customers could face disruptions and additional costs in the event of any product issues.
7.2 Safeguarding Your Investment
To safeguard your investment and access the complete benefits associated with authentic HEIDENHAIN products, we encourage readers and customers to connect with AMS for their motion control and precision measurement requirements. Selecting AMS as your supplier guarantees the reception of genuine components and comprehensive support, thus maximizing the value and performance of your manufacturing process.
AMS Company, Ltd.243/9/10D To Hien Thanh, Ward 13, District 10
Hot line: 028.3868 3738/3903 - Fax: 028.3868 3797