Maximizing Metal Cutting Tool Longevity: Essential Tips for Maintenance and Optimization
Wear and tear happens when the surface of materials undergoes damage and separation due to sliding, rolling, or colliding movements.

1. What causes wear and tear of cutting tools?
Cutting tool wear occurs due to surface irregularities interacting, akin to the phenomenon of friction. The extent of wear is not contingent on the material properties but predominantly hinges on the system and operating conditions. These conditions directly influence the wear state at the common contact surface. There is a common misconception that high friction on the mating surface is the primary cause of high-speed wear.
The wear of cutting tools, including milling cutters, lathes, and other tool types, defines their performance and constrains their longevity due to wear. This wear substantially impacts the precision of the machining process, surface quality of products, and the overall cost-effectiveness of machining. Efforts in researching and developing new tool materials, as well as implementing new technological measures to enhance surface durability, are geared towards augmenting the wear resistance of tools.
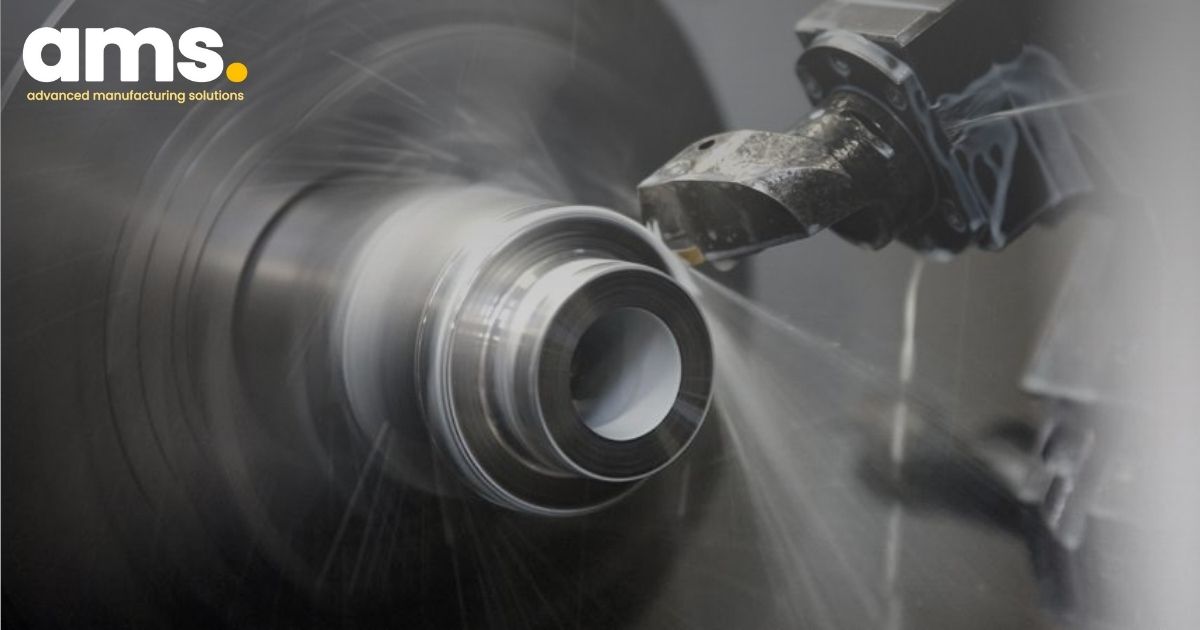
2. Wear and tear of cutting tools
During metal cutting, the cutting capability of the tool progressively diminishes over time, eventually leading to an inability to cut due to wear or complete failure.
Tool wear is the primary criterion used to assess tool performance, as it directly impacts tool lifespan and consequently influences the precision of the machining process and the overall surface quality from both technical and economic perspectives.
The advancement and exploration of new materials for metal cutting tools, combined with the utilization of innovative technological approaches to enhance wear resistance, such as the application of TiN, TiAlN surface coatings, and CBN, are all aimed at optimizing the wear resistance of metal cutting tools like alloy disc milling cutters and alloy ball milling cutters, while also enhancing the overall cutting process performance.
3. Types of wear for cutting tools in the mechanical industry
3.1 Worn on back
This type of wear occurs when the material layer of the tool becomes detached from the backing during machining. This wear phenomenon commonly happens during cutting with small cutting thickness (t ≤ 0.1mm) or when working with brittle materials.
3.2 Worn on the front
When cutting, the workpiece movement on the front surface generates a pressure center at a specific distance from the cutting edge, forming a crescent-shaped indentation. This indentation on the tool's front face occurs as material is peeled off with the workpiece during motion. Typically, these dents manifest alongside the cutting edge and are assessed based on their width, depth, and distance from the cutting edge to the wear mark. This type of wear is commonly observed when machining ductile materials with substantial depths of cut.

3.3 Worn on both front and back
Cutting tools, such as solid drill bits, frequently experience wear on both the front and rear sides, leading to the creation of a fresh cutting edge. This is a common scenario when processing pliable materials with cutting depths ranging from 0.1 to 0.5mm.
3.4 Blunt cutting blade
On cutting tools, wear marks frequently develop in the form of a circular arc along the cutting edge. The measurement of this arc's radius is typically taken from a plane perpendicular to the cutting edge. This wear pattern commonly manifests when machining materials with low thermal conductivity, especially when working with pliable materials. The concentration of heat at the cutting tip accelerates blade dullness in such scenarios.
4. Wear mechanisms of cutting tools
4.1 Wear caused by scratches
When operating at low speeds and temperatures, the abrasive wear mechanism becomes a significant consideration. Impurities with high hardness within the material being machined can generate parallel scratches on the tool's contact surface as a result of the scratching motion.
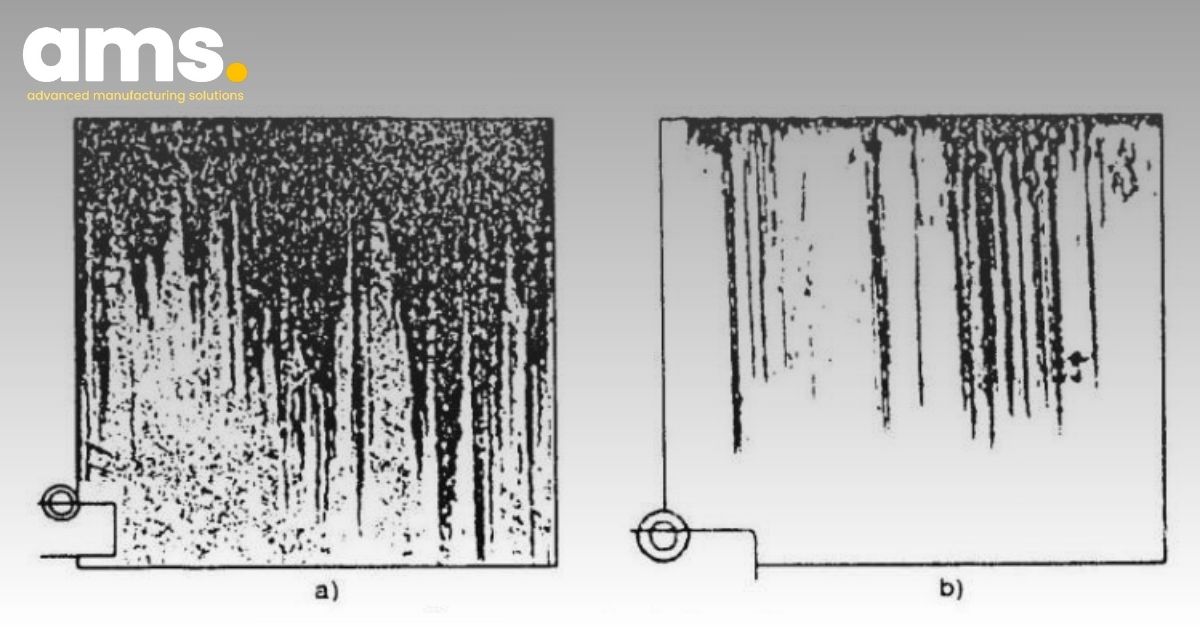
4.2 Wear due to adhesion
When two flat, solid surfaces move in relation to each other, adhesion wear occurs at the contact point on the crests due to the effect of the normal load. During the sliding process, the material in this area undergoes plastic deformation and adheres to the opposing surface or produces loose wear pieces. Some wear pieces are also generated due to fatigue wear at the tips of the protrusions. For cutting tools such as alloy grinding bits, the occurrence of adhesive wear is notably pronounced, particularly in high-temperature conditions. Adhesive regions undergo continuous shearing and cyclic reformation, even over brief shearing periods; this wear phenomenon can be labeled as adhesion.
4.3 Wear due to abrasive particles
In numerous instances, the wear process commences with adhesion, resulting in the formation of wear particles within the contact region. Subsequently, these wear particles harden and accumulate due to oxidation, leading to severe wear on the object. Occasionally, these tough particles can even be produced and introduced into the sliding system from the nearby surroundings.
4.4 Wear due to diffusion
When cutting, the rise in temperature, particularly at the tool's cutting edge, fosters conducive circumstances for material exchange between the tool and the workpiece. The abrupt surge in wear rate at 930°C during high-speed cutting operations using hard alloy tools (such as alloy end mills and free milling cutters) is a significant form of wear. The microstructure of the underlying steel blank cut with a hard alloy tool reveals a higher carbon content compared to the original blank, signifying the assimilation or diffusion of carbon from the tungsten indicator and the blank, consequently elevating the carbon composition of the layers.
4.5 Wear due to oxidation
When subjected to light loads, the metal surface exhibits smoother wear marks and a brighter appearance. The wear process transpires at a gradual pace, yielding minute oxide wear particles. This wear mechanism ensues from the shedding of oxide layers. As these layers peel off, new layers are consistently formed in a sequential manner. However, the oxide layer fosters a chemical interaction with the surface environment, effectively inhibiting adhesion. In a vacuum environment, adhesive wear becomes pronounced as the oxide layer is unable to form.
4.6 Wear due to heat
When a blade cuts through material, the small volume of material at the cutting location results in concentrated high temperatures. This can cause overheating, potentially leading to thermal damage of the blade.

4.7 Wear of cutting tools due to coating evaporation
In the case of coated cutting tools, two primary wear mechanisms occur during cutting operations: the cracking and peeling of the coating, and wear of the base material. High temperatures during the cutting process lead to a reduction in the hardness of the substrate material, causing the coating on the front surface to fracture. Friction between the chip and the coating generates heat, transferring it to the cutting tool, resulting in a fracture process. Under the high pressure and temperature beneath the coating, the base material becomes flexible, leading to the cracking and peeling of the coating, exposing the base material. The escalating friction and temperature in this area lead to further wear on the front face, consequently reducing the cutting ability of the cutting tool.
5. Factors influencing the longevity of metal cutting tools
The longevity of a cutting tool in mechanical machining refers to the duration of continuous operation between two sharpenings, or simply put, the time of uninterrupted operation until it reaches the limit of wear.
This is a crucial aspect that significantly impacts productivity and the economics of the cutting process. The lifespan of a tool is primarily contingent on the technical specifications of the workpiece. Thus, accurately predicting the baseline life expectancy is essential for comparative purposes.
In practice, the lifespan of cutting tools (such as drill bits and taps) is frequently influenced by the following factors:
-
Variations in the hardness, cellular structure, chemical composition, and surface properties of the workpiece material.
-
Changes in tool materials, geometric parameters, and grinding methods.
-
Fluctuations in machinery, tools, and technological systems.
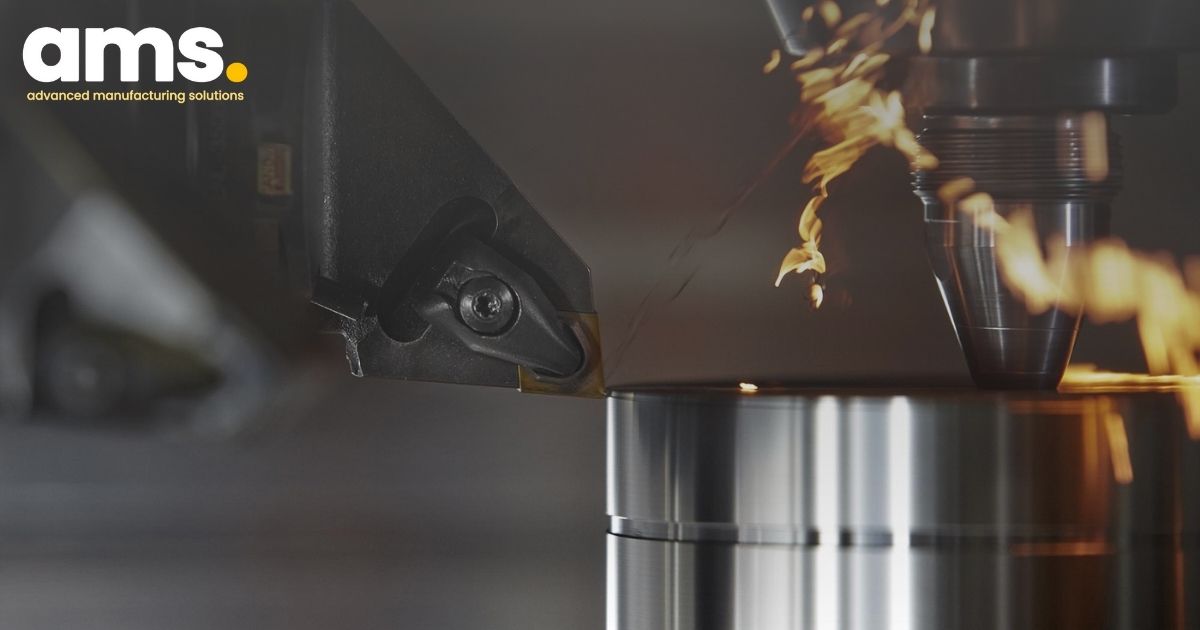
6. Examine the effect of cutting methods on the longevity of cutting tools
Specific cutting methods possess the most substantial impact on the lifespan of cutting surfaces, primarily through cutting speed and feed rate.
-
On the front cutting surface, wear progresses slowly until reaching a critical cutting speed limit, after which the wear rate sharply escalates. Additionally, a greater feed rate leads to a lower cutting speed limit.
-
On the reverse side, the wear rate undergoes a rapid increase beyond the critical cutting speed and limited feed rate, mirroring the behavior of the front side due to wear mechanisms influenced by temperature, which dictate the lifespan. Nevertheless, within a certain range of cutting speeds, the wear rate on the rear side rises before steadily decreasing, as the wear mechanisms in this area are unaffected by temperature.
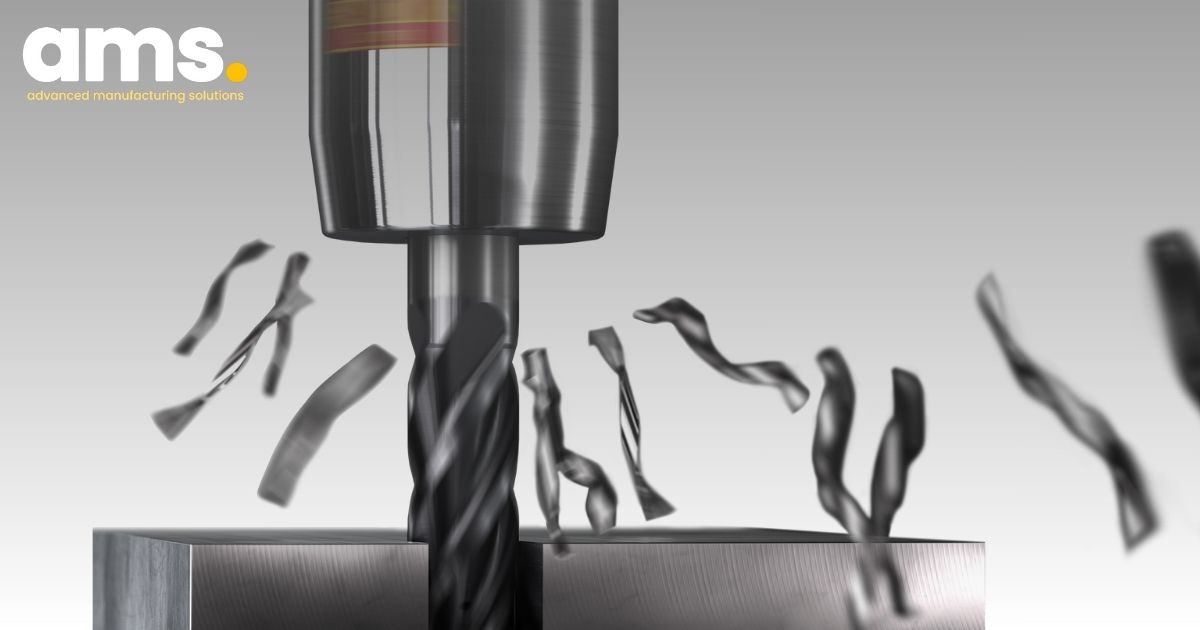
7. Understand the significance of hard coatings in enhancing the durability of cutting tools
Hard coatings are pivotal in diminishing surface friction on the tool, restraining temperature peaks, and curbing the formation of temperature fields within the tool. Consequently, this minimizes thermal wear and prolongs the lifespan of the tool. The hard coating also establishes a protective layer between the workpiece and the cutting edge, exhibiting strong anti-adhesive and anti-abrasion properties due to its chemical inertness and high hardness. As a result, this positively impacts wear reduction and enhances the tool's longevity.
Moreover, the distinctive thermal properties of hard coatings also alleviate the heat transfer rate to the workpiece and tool. This is a critical factor contributing to the extended lifespan of coated tools during high-speed cutting operations.
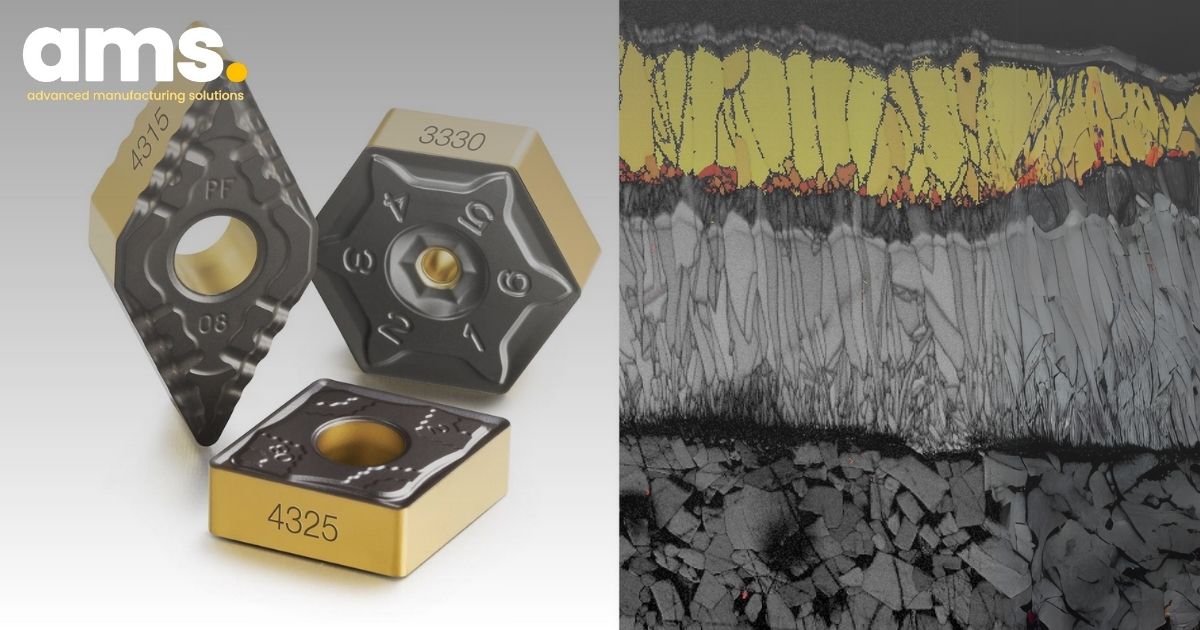
8. Sandvik Coromant: Pioneering the Future of Cutting Tool Technology
When it comes to cutting tools, one company stands at the forefront of innovation and precision: Sandvik Coromant. As a global leader in metal cutting technology, Sandvik Coromant's cutting-edge solutions have revolutionized the industry, setting new standards for durability, performance, and efficiency. With a relentless commitment to research and development, Sandvik Coromant continues to spearhead advancements in cutting tool materials, geometries, and coatings, empowering manufacturers to optimize their processes and achieve superior results.
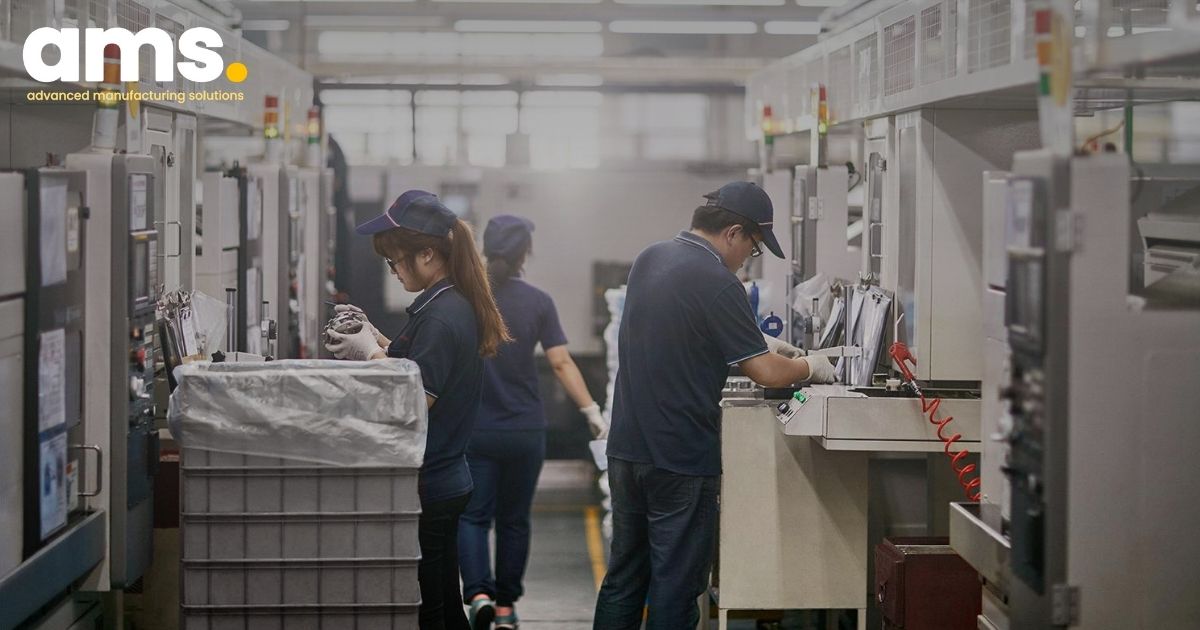
In Vietnam, AMS Company Limited holds the distinction of being the official distributor of Sandvik Coromant, the trailblazer in cutting tool technology. With over two decades of experience, AMS has been a trusted provider of manufacturing solutions to businesses, consistently enhancing operational efficiency and productivity in various industries across Vietnam. As an authorized distributor of Sandvik Coromant, AMS offers access to the latest innovations and advanced technological solutions, empowering businesses to elevate their manufacturing processes and achieve unparalleled results.
For over 20 years, AMS Company Limited has been a steadfast partner in driving manufacturing excellence. Whether it's precision tooling, optimized machining strategies, or state-of-the-art cutting tool solutions, AMS has demonstrated a commitment to delivering top-tier products and services to meet the unique needs of businesses in Vietnam.
If you're looking to integrate Sandvik Coromant's innovative products into your manufacturing processes, AMS Company Limited is your reliable ally. Contact us today to explore how AMS can provide the necessary expertise and support to help your business flourish with the pioneering solutions offered by Sandvik Coromant.
AMS Company, Ltd.243/9/10D To Hien Thanh, Ward 13, District 10
Hot line: 028.3868 3738/3903 - Fax: 028.3868 3797