Distinguish CNC Lathe Machining Techniques on Common Materials
In the field of Precision Mechanical engineering, there are six primary material groups denoted by the symbols P - M - K - N - S - H, each possessing distinctive properties. As a result, specific machining techniques and conditions are essential when employing CNC turning to ensure the best possible performance.

1. Machining steel materials on lathes

1.1. Machining of non-alloy steel materials - Material classification: P1.1
Processing low carbon content steels, characterized by carbon content up to 0.55%, presents specific challenges. Steels with even lower carbon content (less than 0.25%) require careful handling due to difficulties related to chip breaking and build-up edge.
To effectively manage cutting materials and control chips, it is crucial to optimize the machining process by utilizing the highest feasible feed rate. When working with this material, it is strongly advised to employ Wiper angle cutting tools.
Opting for a high cutting speed is essential to prevent the formation of build-up edge on the cutter. However, it's important to consider that excessively high cutting speeds can have a detrimental impact on the surface finish of the end product. Selecting cutters with sharp cutting angles and an optimal geometric design will reduce the formation of build-up edges and protect the cutting edges from wear.
1.2. Machining low alloy steel materials - Material classification: P2.x
The machinability of low-alloy steels is directly linked to their alloy content and heat treatment, which determines their hardness. Within this material group, the primary types of wear observed are Crater wear on the Insert face and Flank Wear on the cut corner flanks of the Insert.
Additionally, in the case of hard materials, plastic deformation due to the generated machining temperature is a common wear mechanism.
When dealing with low alloy steels in their unhardened state, the optimal approach is to utilize Inserts specifically designed with geometry and coatings tailored for machining these steels. Conversely, for harder materials, the preference leans towards Grades and coatings with higher hardness (including specialized coatings for cast iron processing, Ceramic, and CBN coatings).
1.3. Machining high alloy steel materials - Material classification: P3.x
High alloy steel encompasses carbon steels with a combined alloy content surpassing 5%, blending both soft and hard materials. According to experts, machining efficiency gradually diminishes with increased alloy content and hardness.
Similarly to low-alloy steels, utilizing Inserts with geometry and coatings tailored for steel machining is imperative.
For steels with alloy content surpassing 5% and a hardness exceeding 450 HB, particular emphasis is placed on resistance to plastic deformation and edge strength. Accordingly, prioritizing Grades and coatings with higher hardness (including specialized coatings for cast iron processing, Ceramic, and CBN coatings) is crucial.
2. Turning stainless steel materials
Stainless steel is divided into three primary types: ferritic/martensitic, austenitic, and duplex (austenitic/ferritic). Each type necessitates distinct machining procedures to optimize efficiency during turning.

2.1. Turning Ferritic and Martensitic stainless steel - Material classification: P5.1
Stainless steel, commonly referred to as Inox, is categorized as a steel material falling under the P5.x material classification. To optimize the processing of this material, industry experts frequently recommend selecting specialized grades for stainless steel and customizing the application geometry during the stainless steel processing procedure.
When machining hardened Martensitic Steel, the demand for the insert's resistance to plastic deformation escalates. Therefore, opting for CBN types with a hardness of HRC = 55 or higher is a prudent choice.
Similarly, when processing hardened Martensitic stainless steel, the importance of the insert's ability to withstand plastic deformation becomes more significant. Users may contemplate leveraging specialized CBN insert types for machining hardnesses of 55HRC or higher.
2.2. Turning austenitic stainless steel - Material classification: M1.x and M2.x
Austenitic stainless steel stands as one of the most widely used stainless steel types, which encompasses Super Austenitic stainless steel featuring a Nickel content surpassing 20%.
When dealing with this material, it is advisable to prioritize the selection of CVD, PVD grade, and geometric designs tailored specifically for stainless steel processing.
In situations where parts necessitate discontinuous cuts, or chip crushing and jamming are the primary wear mechanisms, considering the use of PVD Inserts holds significant importance.
Furthermore, it is recommended to consistently utilize coolant to mitigate Crater Wear and plastic deformation, as well as to opt for the largest possible tool tip radius. Emphasizing the use of rounded Inserts or small feed angles to minimize Notch Wear is also crucial. Leveraging inserts with sharp edges or positive rake face geometry serves to optimize the machining process.
2.3. Turning Duplex stainless steel (Austenitic/Ferritic) - Material classification: M3.4
When working with Duplex stainless steel or higher alloy steels boasting substantial mechanical strength, the machining process becomes notably intricate, particularly in managing heat generation, cutting forces, and chip control.
In such scenarios, it is advisable to opt for CVD, PVD grades, and specialized geometric designs tailored for stainless steel.
Furthermore, it is essential to incorporate coolant to enhance chip control and prevent plastic deformation. Employing cutting tools with internal coolant designs and integrating small feed angles to mitigate Notch Wear and Burr formation are also critical aspects to highlight.
3. Turning cast iron materials

There are five primary classifications of cast iron materials:
-
Grey Cast Iron (GCI)
-
Nodular Cast Iron (NCI)
-
Malleable Cast Iron (MCI)
-
Compacted Graphite Iron (CGI)
-
Austempered Ductile Iron (ADI)
Cast iron is composed of iron (Fe) and silicon (Si) with a carbon (C) content typically exceeding 2%. This material tends to produce short chips and demonstrates good chip control across various machining conditions.
When processing cast iron materials, it is crucial to select inserts with grades and geometrical designs tailored specifically for cast iron processing. In the case of gray cast iron, the utilization of Ceramic and CBN inserts is advisable, especially when higher cutting speeds are required.
4. Turning heat-resistant super alloy materials (HRSA)
The super alloy material is distinguished by its exceptional mechanical strength and resistance to Creep (the slow deformation or sliding under stress) at high temperatures. Moreover, it exhibits good resistance to corrosion and oxidation. HRSA materials are commonly categorized into four main groups for research and application:
-
Nickel-based (eg Inconel)
-
Iron-based
-
Cobalt-based
-
Titanium alloys
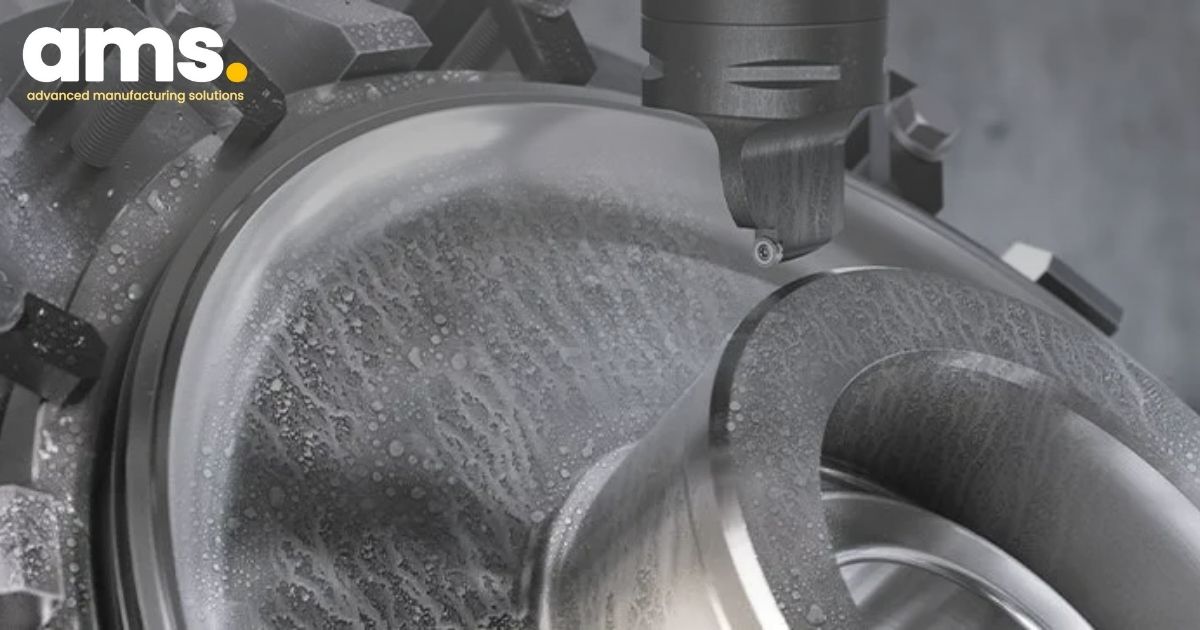
Both HRSA materials and titanium present machining challenges, particularly in extended machining conditions necessitating the high precision and performance of cutting tools. The utilization of tools with sharp cutting edges is crucial in preventing wear and the formation of coatings with varying hardness and pressure.
For HRSA materials, employing PVD and Ceramic grades is recommended to facilitate efficient processing. Additionally, the selection of cutting tools with optimized geometric designs tailored for HRSA materials is essential.
In the case of titanium alloys, the use of uncoated Inserts and PVD grades is a popular choice. Simultaneously, employing Inserts with an optimal geometric design for processing HRSA material also plays a significant role in the material's processing.
A common wear pattern observed in both titanium and HRSA is Notch Wear. To achieve optimal performance, following these principles is recommended:
-
Use Inserts with an entry angle below 45°.
-
Program machining with precise correlations between insert size, tool tip radius, and depth of cut.
-
When ramping or conducting multiple cutting passes, utilize a cutting depth Ap higher than 0.25 mm.
-
Apply coolant consistently when turning HRSA materials and titanium alloys, regardless of whether carbide inserts or ceramic inserts are used.
-
When using Ceramic Inserts, chamfer the edges first to minimize the risk of scratches when the insert contacts and departs from the cutting object, thus ensuring the highest performance.
This group encompasses non-ferrous soft metals like aluminum, copper, bronze, brass, MMC composites, and magnesium. Machining these materials requires careful consideration of alloy composition, heat treatment, and manufacturing methods (e.g., forging, casting) to ensure optimal machining performance.
5. Turning Non-ferrous materials (Aluminum)

5.1. Turning aluminum alloy - Material classification: N1.2
It's always best to opt for positive Inserts with sharp cutting edges, including uncoated varieties and PCD Inserts. When dealing with aluminum alloys containing more than 13% Si, it's advisable to use PCD Inserts to prolong tool life, as using carbide Inserts will significantly decrease it. In aluminum machining, the use of coolant is typically focused on optimizing chip removal.
6. Turning hardened steel materials

Turning hard steel, typically ranging in hardness from 55-65 HRC, involves the machining of tough steel components, offering a cost-effective alternative to grinding. Machining hardened steel parts enhances flexibility, lead time, and product quality.
The optimal choice for machining case materials and hardened steel is to use CBN Inserts. For steels softer than approximately 55 HRC, Ceramic or Cermet Inserts are recommended.
Guidelines to observe include:
-
Ensure proper operation of machinery and equipment, along with a stable clamping system.
-
Use the smallest feasible entry angle to prepare the edge more accurately for machining, thereby enhancing tool life.
-
Implement Wiper Inserts during machining to achieve the finest surface finish.
7. Machining Hard Materials: Enhancing Precision with Sandvik Coromant
In the world of precision machining, having the right tools for the job is crucial. This is where Sandvik Coromant, a global leading supplier of cutting tools, comes into play. With a legacy of innovation spanning over 75 years, Sandvik Coromant is renowned for its cutting-edge solutions that drive the manufacturing industry forward. Their commitment to research and development has led to the creation of a diverse range of high-quality cutting tools and tooling systems, tailored to meet the specific needs of various materials and machining processes.

When it comes to CNC machining on different material types, Sandvik Coromant offers a plethora of products designed to excel in diverse applications. Let's take a look at a few examples:
-
For Aluminum and Non-Ferrous Alloys: Sandvik Coromant's CoroMill® Plura series provides excellent performance in aluminum and non-ferrous materials, offering precision and durability in milling operations.
-
For Stainless Steel: The CoroTurn® 107 series delivers superior turning performance on stainless steel, ensuring high productivity and surface finish quality.
-
For Hardened Steel: Sandvik Coromant's CoroMill® 390 is an outstanding choice for milling hardened steels, providing reliable and efficient machining solutions.
-
For Exotic Alloys and Heat-Resistant Super Alloys: The CoroMill® 316 face milling cutter is designed to handle the challenges of machining exotic alloys and heat-resistant super alloys with ease and precision.
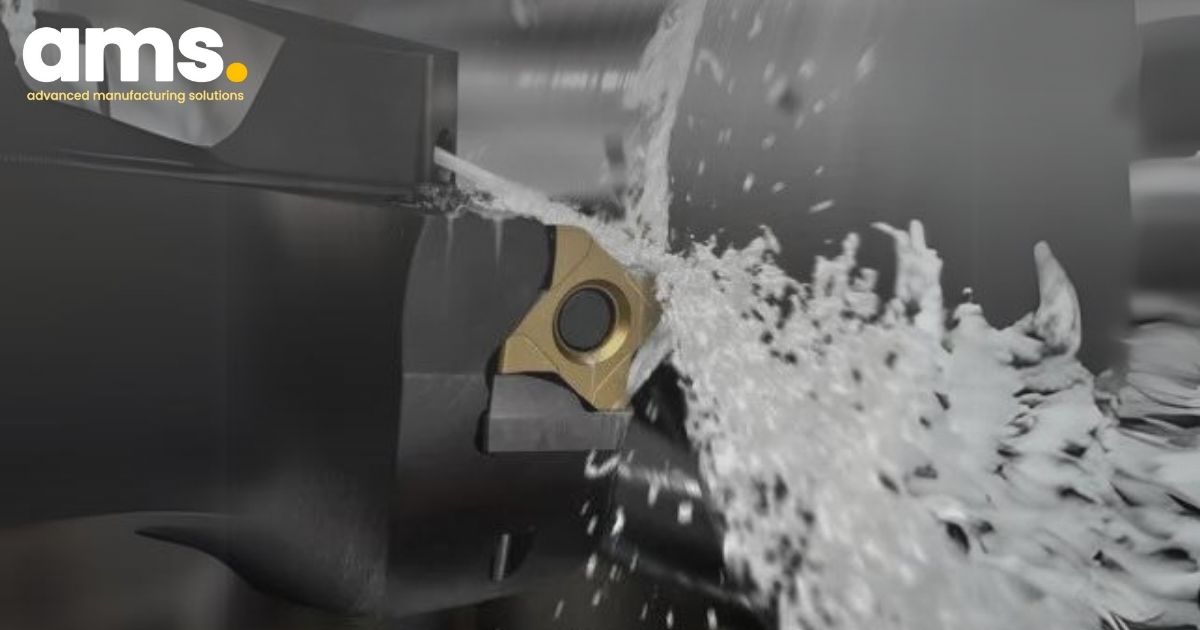
AMS Company Limited, as the official distributor of Sandvik Coromant in Vietnam with over 20 years of experience, stands as your trusted partner in precision machining. Our team is honored to provide expert consulting services, assisting customers in selecting the right Sandvik Coromant products and tools to achieve exceptional results in their machining operations.
Partnering with Sandvik Coromant through AMS Company Limited means accessing world-class cutting tools and unparalleled expertise to elevate your precision machining endeavors to the next level.
AMS Company, Ltd.243/9/10D To Hien Thanh, Ward 13, District 10
Hot line: 028.3868 3738/3903 - Fax: 028.3868 3797