Definition and How to Perform Drilling, Boring, Reaming and Tapping
Drilling serves as a method employed for fabricating apertures in solid materials, with the potential to produce apertures ranging in diameter from φ = 0.1 to 80 mm.
Boring is the procedure for expanding apertures within equipment such as drills, lathes, milling machines, or boring machines.
Reaming denotes the operation of finalizing an aperture subsequent to drilling, boring, or turning.
Taps are capable of processing cylindrical threads, tapered threads, metric threads, and imperial threads. Thread machining involving tapping is frequently utilized for fabricating standard hole threads, particularly those with a moderate diameter.

1. Drilling - Characteristics and technological capabilities of Drilling
Drilling is an essential process for fabricating apertures in solid materials. This method can produce apertures with diameters ranging from φ = 0.1 to 80 mm, commonly used for machining apertures with diameters ≤ 35 mm. Drilling is typically carried out on various drilling machines including vertical drilling machines, boom drilling machines, and combination drilling machines, as well as on other equipment such as lathes, milling machines, and boring machines, often on machining centers.
The cutting tool used during drilling is referred to as a drill bit and is available in various types.
For drill hole l/d ratios of ≤ 5, the drill bit structure is typically utilized. Conversely, when the l/d ratio exceeds 5, specialized deep drill bit structures are commonly employed, with drill bits featuring alloy pieces being the most prevalent.
When drilling large diameter apertures, the cutting force can be reduced by expanding the aperture multiple times with a hollow drill bit or by utilizing a rim drill structure.
The precision achieved in drilling is typically modest, usually reaching an accuracy level of 12-13, with surface roughness at levels 3-4. As a result, drilling is best suited for machining apertures that do not necessitate high precision, such as those for bolts, threads, or as a preliminary step for subsequent finishing processes like boring, reaming, and turning.
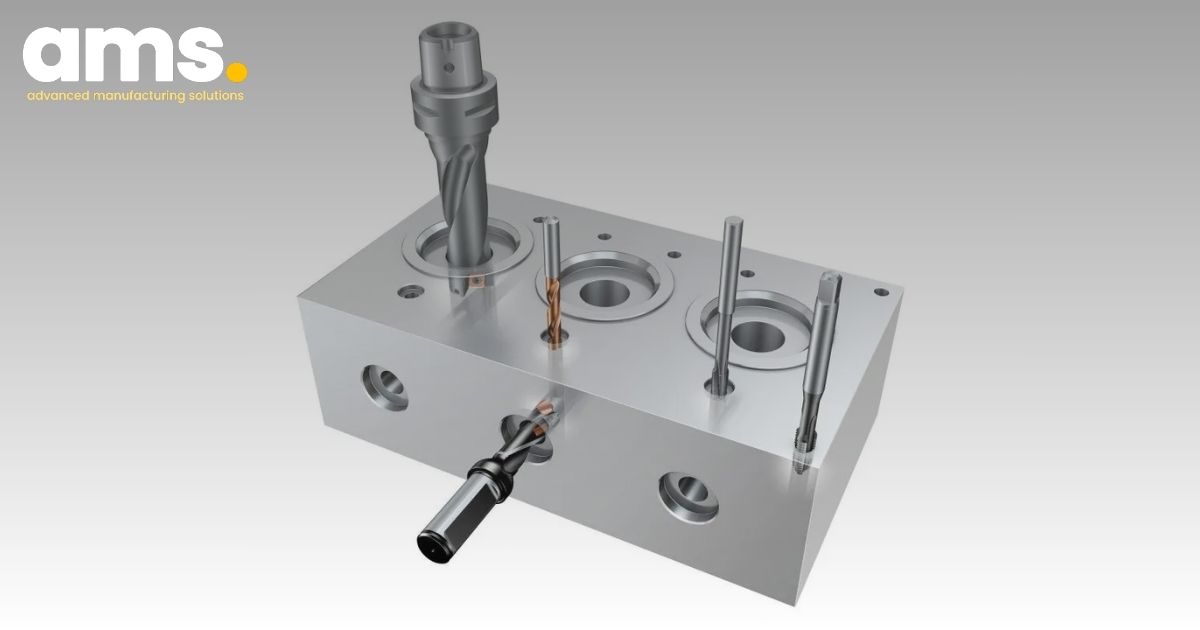
1.1 Some things to pay attention to when drilling
Issues related to damage
-
The drill hole skewing phenomenon typically occurs when utilizing a rotating and advancing drill or reamer. This issue arises when there is an absence of perpendicularity between the tool's feed direction and the part's tip surface.
-
The flared hole phenomenon, commonly observed during lathe drilling while the part rotates and the tool advances, is caused by the tool's feed direction not being parallel to the machine's main axis.
-
Non-uniform hole expansion may result from unbalanced grinding of the cutting blades, potential eccentricity between the cutting part and the shank, or due to worn-out drill bits lacking the necessary hardness and stability.
It is advisable not to use drilling to enlarge molded or pre-stamped holes, as alternative methods such as turning or boring should be employed. This caution is necessary as the drill bit may not be sufficiently robust and stable, potentially causing the bit to become stuck or broken during the hole expansion process.
1.2 Some measures to improve precision and productivity when drilling
To enhance precision and efficiency in drilling operations, the following technological approaches can be implemented:
-
Employ drilling diagrams for the rotation of components and feed cutters, particularly beneficial for drilling deep holes.
-
Utilize a rovonve drill head to minimize tool change time when executing hole machining across multiple consecutive steps.
-
Implement a multi-axis drilling head to concurrently machine multiple holes.
-
Introduce a guide bush structure to enhance the rigidity and stability of the drill bit, thereby improving accuracy and productivity.
-
Prior to drilling, use a center drill to create a pilot hole, enhancing the relative position accuracy of the hole, and employ a small feed to reduce cutting force and prevent drill bit breakage.
-
Utilize jigs for marking and reducing jig placement time.
-
Optimize the geometric parameters of the cutting part to diminish the cutting force P0.
-
Employ effective coolant application to lower temperature and reduce wear during drilling.

1.3 Drilling deep holes
During deep hole machining (where the hole length/area ratio exceeds 5) employing a hollow drill bit, challenges may stem from the drill bit's low hardness and stability, inadequate guiding properties, and difficulty in managing fluids. Coolant penetration into the cutting area can impede workpiece drainage and heat dissipation, consequently elevating the likelihood of drill bit breakage, while also compromising accuracy and productivity. To address this scenario, the following strategies are often implemented:
-
Utilize drilling diagrams designed for rotating components and feed tools (similar to lathe drilling diagrams).
-
Employ a specialized deep drill bit structure, typically featuring an alloy piece.
1.4 Optimizing Drilling Efficiency with Sandvik Coromant's Signature Products
Sandvik Coromant offers a range of signature products tailored for drilling operations, designed to optimize efficiency and precision. The CoroDrill 860 is renowned for its versatility and adaptability, suitable for a wide array of materials and applications. Additionally, the CoroDrill DS20 delivers exceptional performance in deep drilling, featuring advanced coolant delivery and chip evacuation capabilities. For those seeking high-performance indexable drilling solutions, the CoroDrill 870 and 880 series provide excellent productivity and tool life. These signature products from Sandvik Coromant are engineered to meet the diverse needs of modern drilling processes, ensuring reliability, performance, and cost-effectiveness.

2. Boring - Characteristics and technological capabilities of boring
Boring is a machining technique utilized to expand apertures in machinery such as drills, lathes, milling machines, or boring machines, with the primary objective of enhancing aperture accuracy and surface quality. This process is capable of achieving high levels of precision, typically around 10 ÷ 12, with a surface roughness of Ra = 2.5 ÷ 10 μm. Additionally, boring can serve as a preparatory step for subsequent finishing processes like reaming, final turning, and aperture grinding.
Boring presents distinct advantages over drilling due to the greater number of cutting edges and superior rigidity of the boring tool, thus contributing to enhanced aperture accuracy and surface quality. Furthermore, boring possesses the capability to rectify discrepancies in the relative positioning of apertures resulting from prior machining operations. Moreover, boring is not restricted to machining cylindrical apertures but extends to processing stepped apertures, tapered apertures, or square-end boring. During the boring process, the utilization of guide bushings at one or both ends of the tool shaft can enhance process accuracy and productivity.
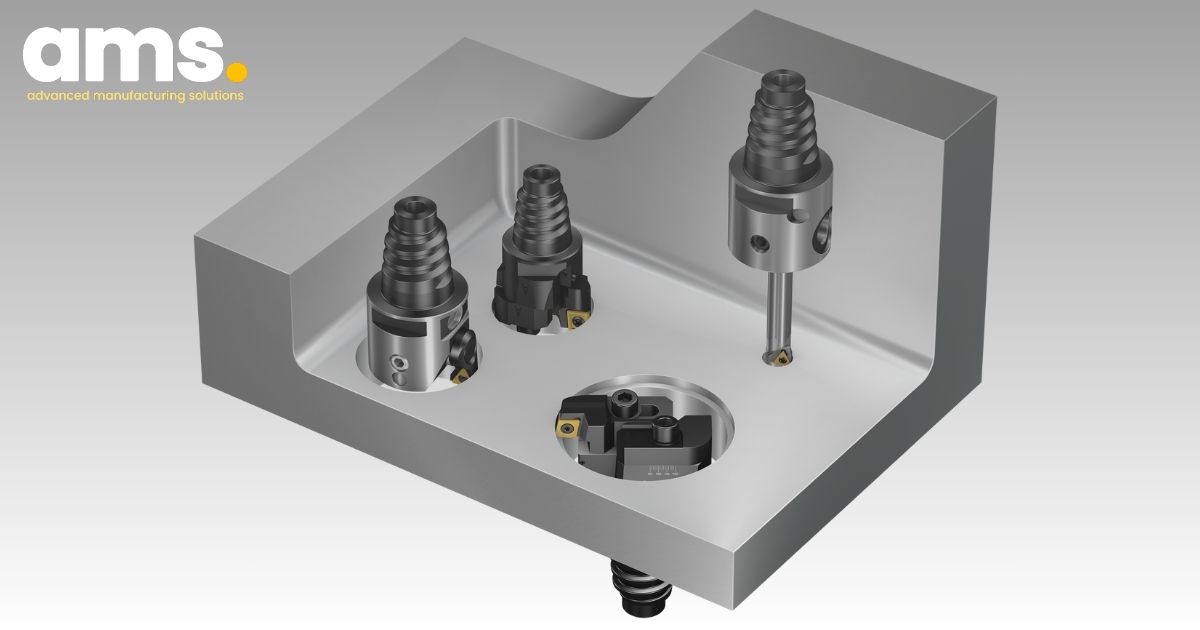
2.1 Enhancing Boring Operations with Sandvik Coromant Precision Tools
Sandvik Coromant offers a comprehensive range of high-quality products designed to optimize performance and accuracy. The CoroBore range of tools, including the CoroBore 825 for rough boring and the CoroBore 826 for fine boring, provides exceptional precision and surface finish. For high productivity in rough and fine boring applications, the CoroBore 827 and 828 offer excellent chip control and reliability. Additionally, the CoroMill range of cutting tools, such as the CoroMill 327 and 328, are ideal for boring applications, providing efficient material removal and surface finish. Sandvik Coromant's expertise in cutting tool solutions ensures that their products are well-suited to meet the demands of modern boring operations, delivering superior results and cost-effectiveness.
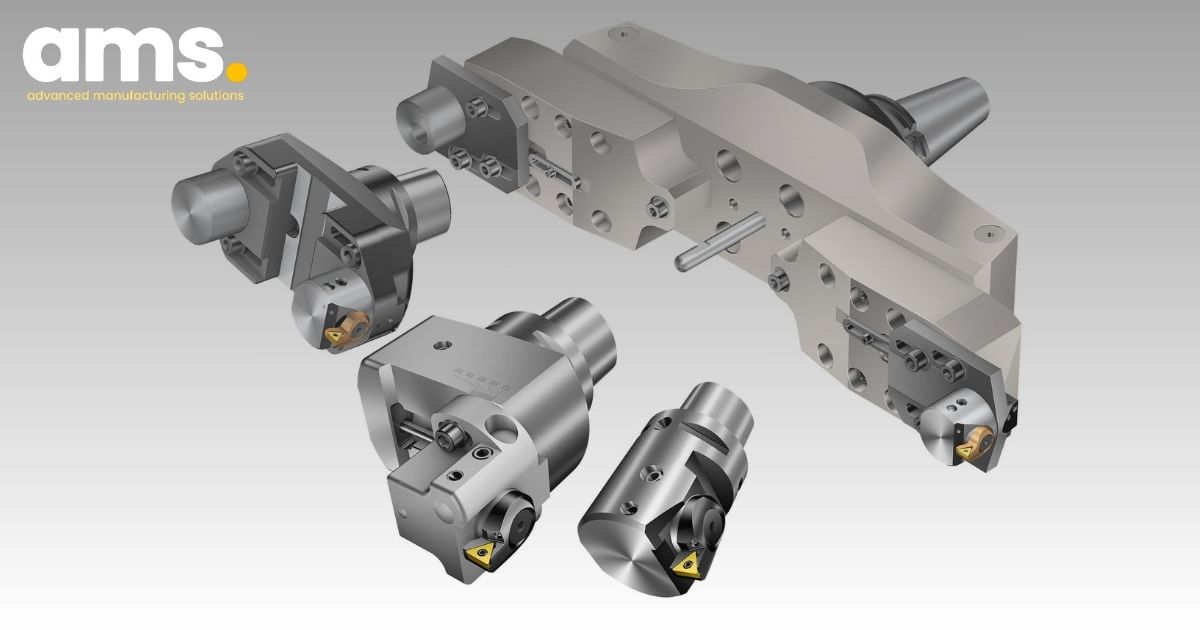
3. Reaming - Characteristics and technological capabilities of reaming
Reaming serves as a technique for refining apertures subsequent to drilling, and after drilling, boring, or turning procedures have been executed. This method can achieve an accuracy level of approximately 9 ÷ 7, with a surface roughness of Ra = 0.63 ÷ 1.25 μm. With the utilization of advanced technology and cutters, reaming can attain a precision level of 6, with a surface roughness of Ra = 0.63 μm. However, due to its high production costs and limited productivity, this method is seldom utilized.
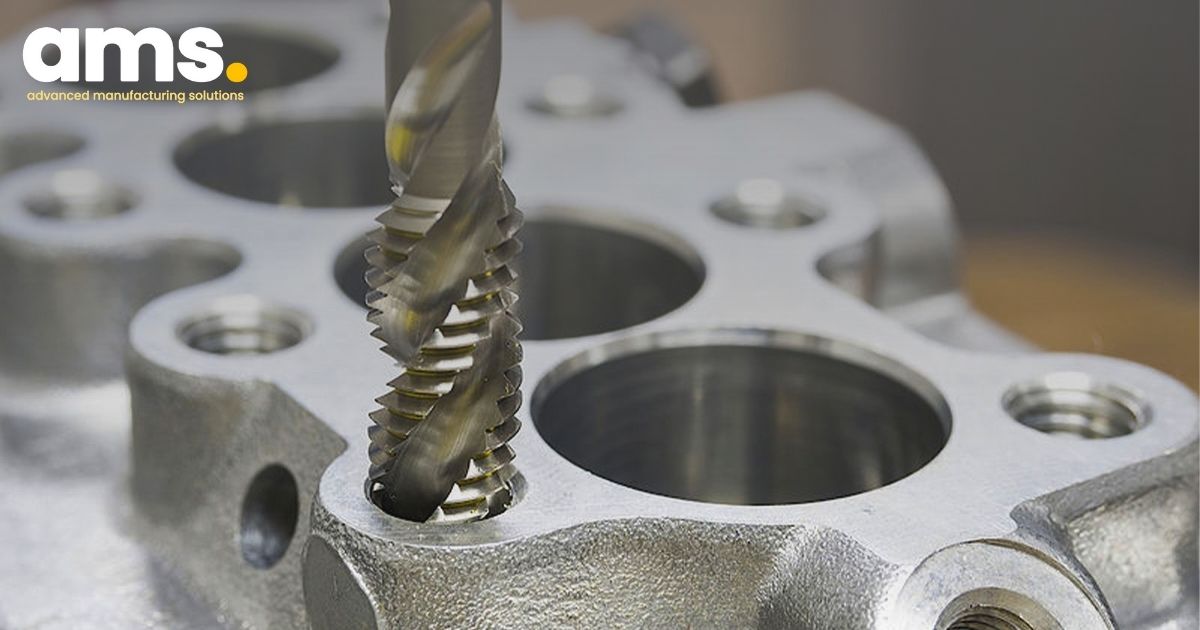
3.1 Cut mode when reaming
The reaming process is characterized by its high rigidity, often featuring an asymmetric cutting edge to minimize cutting vibrations, and a large rake angle that facilitates the cutting of thin chip layers. Controlling the residual amount during reaming is crucial, with coarse reaming typically maintaining a residual amount of approximately t = 0.25 ÷ 0.5 mm, while fine reaming aims for a residual amount of about t = 0.05 ÷ 0.15 mm. Reaming is typically executed at a low cutting speed, approximately 8 ÷ 10 m/min, with the feed rate ranging from s = 0.5 ÷ 3.5 mm/rev. Despite the low cutting speed, the reaming process boasts high productivity owing to its elevated feed rate.
However, a fundamental limitation of the reaming process is its inability to correct significant deviations in the relative positioning resulting from preceding machining operations.
The reaming process is applicable across a variety of machinery including drills, lathes, milling machines, and can even be performed manually.
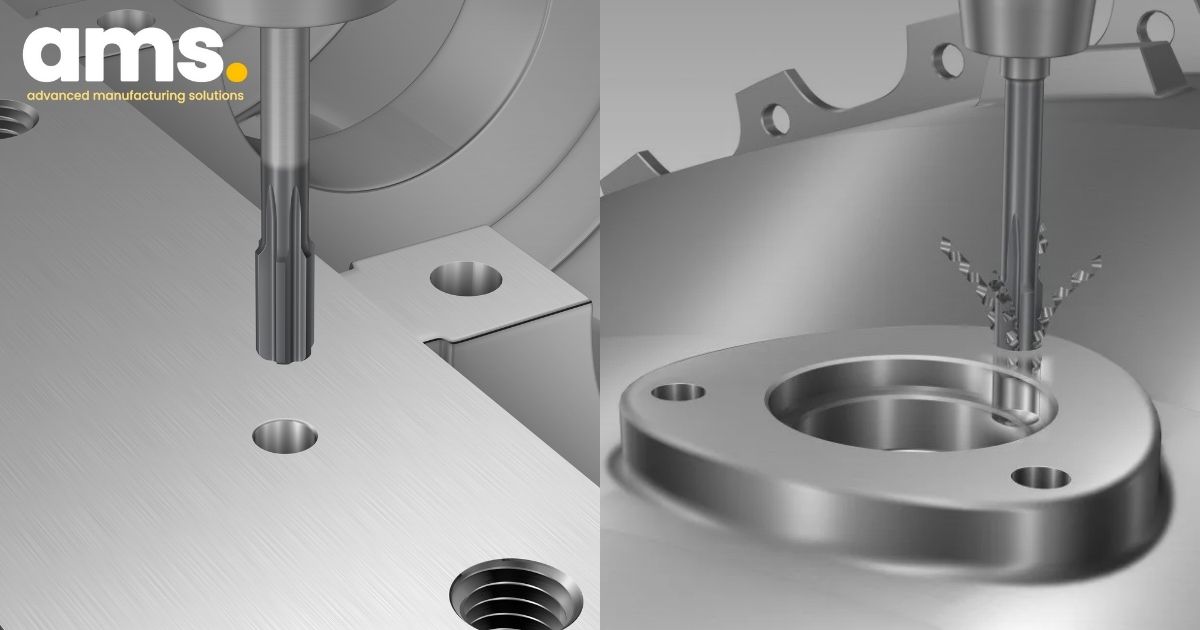
3.2 Some notes when performing the reaming process
-
Employ enforced cutters exclusively for specific cases, for instance: drilling apertures, boring apertures, or reaming apertures in a singular jig, or short and large apertures. Otherwise, automated reaming is preferable.
-
Avoid executing the reaming process on excessively large apertures, apertures with non-standard sizes, brief apertures, ambiguous apertures, apertures with grooves, and apertures within materials of extreme hardness or softness.
-
Typically, the reaming process occurs within a sequence of drilling, boring, and reaming stages, and the reaming cutter commands a considerable cost, therefore proving effective solely when the processing output is sufficiently substantial.
3.3 Achieving Precision and Surface Quality with Sandvik Coromant's Reaming Tools
When it comes to reaming tasks, Sandvik Coromant provides a diverse array of premium products aimed at optimizing precision and surface quality. The CoroReamer series, which encompasses tools like the CoroReamer 435 and 445, is meticulously crafted to deliver exceptional accuracy and reliability for high-precision reaming applications. Additionally, the CoroMill 327 and 328 are well-suited for reaming, delivering efficient material removal and superior surface finish. Sandvik Coromant's expertise in cutting tool solutions ensures that their reaming products meet the needs of modern machining operations, ensuring exceptional results and productivity.
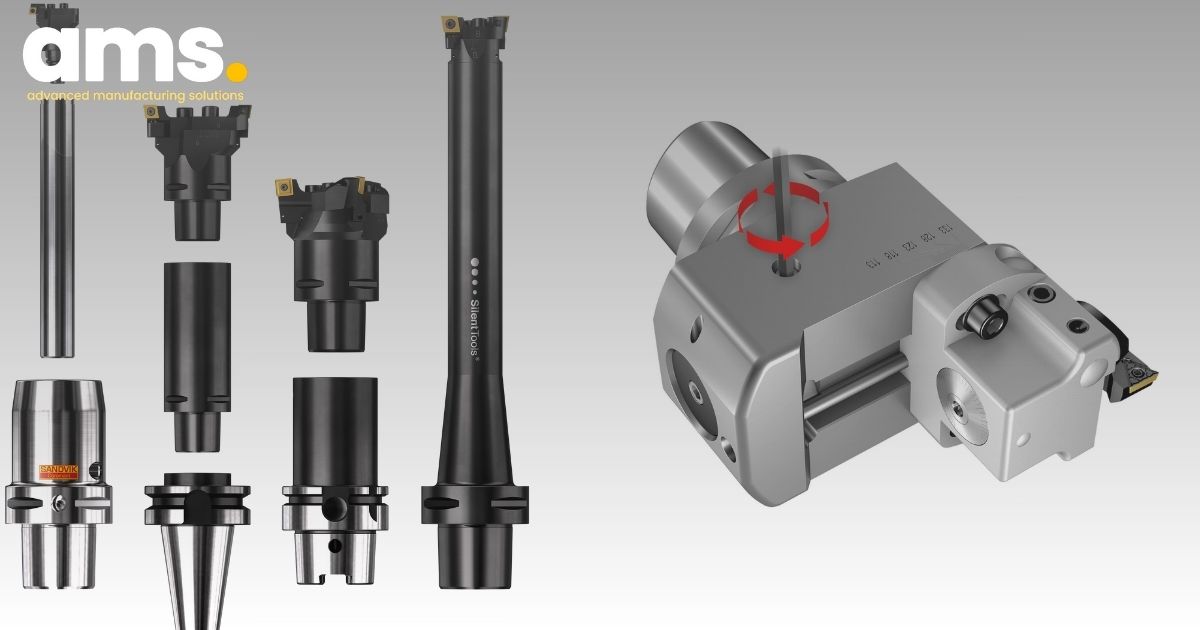
4. Tap - Machining threads with tap
Thread machining utilizing tapping is commonly applied in fabricating standard hole threads, particularly those with moderate diameters. Tapping demonstrates the capacity to process cylindrical threads, tapered threads, metric threads, and imperial threads.
During the cutting of threads using a tap, the involvement of numerous cutting edges simultaneously, coupled with challenging cutting conditions, inadequate heat dissipation, and chip evacuation, often results in substantial torque. To prevent tap breakage, the machining process typically operates at low cutting speeds, approximately 5 ÷ 15 m/min.
The precision and quality of the thread surface rely significantly on the tap manufacturing quality and the technological measures implemented during the thread cutting process. Daily grinding of the thread cutting blade can result in achieving a threading accuracy reaching level 7.
The process of tapping thread machining is compatible with various machine types such as drilling machines, lathes, boring machines, and can even be carried out manually.
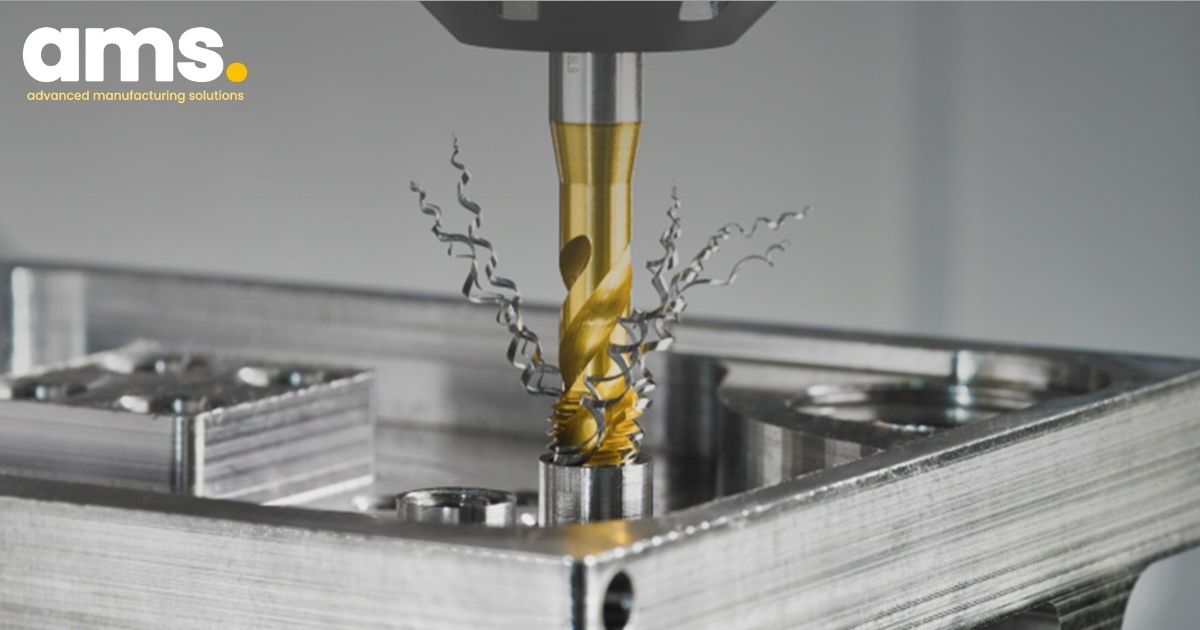
4.1 Tapping by machine
The rigid connection of the tappet to the machine's main shaft poses the risk of the threaded hole being prone to tilting and the tap being easily stuck or broken. This approach is typically restricted to scenarios involving simultaneous drilling and tapping, or when tapping threads on short holes.
In an automatic tappet setup, the tappet is connected to the machine's main shaft, allowing the tap to rely entirely on the existing hole for guidance, effectively mitigating the drawbacks associated with the previous method.
When employing a tap for thread cutting, there are two approaches to tooling motion:
Forced tooling involves the tooling movement being driven by the machine's tooling chain. However, this method is susceptible to tap breakage due to thread pitch errors between the lead screw and the tap.
In contrast, utilizing a self-retracting tool involves pressing the tap to engage a few thread loops, following which the tap automatically retracts into the machined hole based on the thread step. This method effectively overcomes the deficiencies of the prior approach.
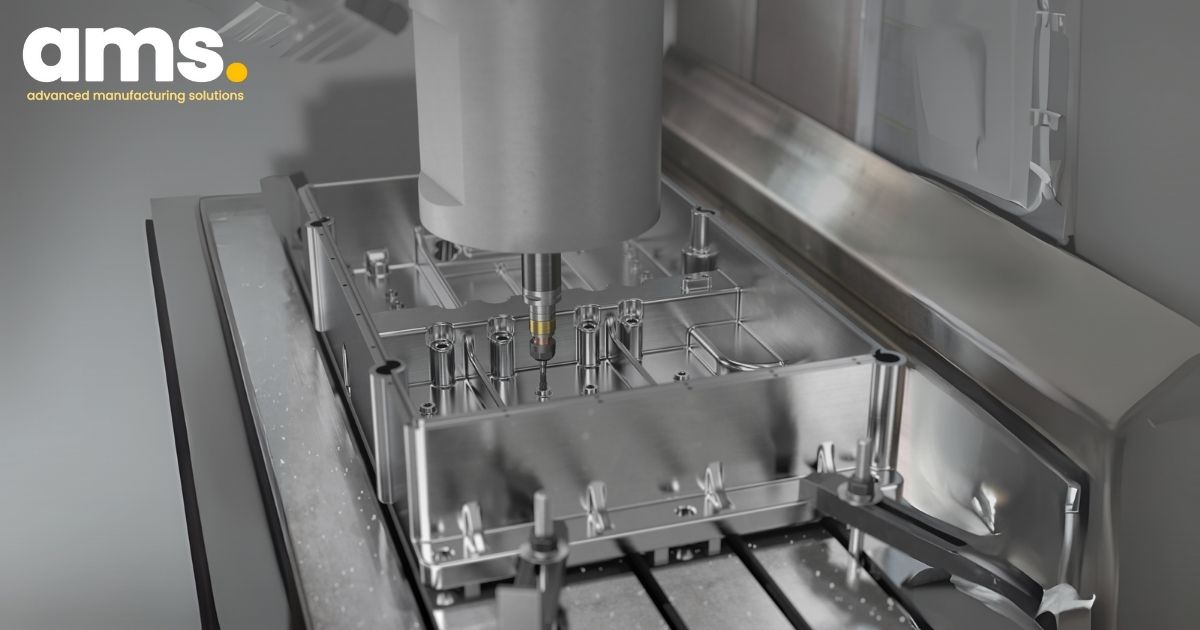
4.2 Tapping by hand
All cutting procedures are executed manually by operators. Hand-cut taps distinguish themselves from machine-cut taps in that they typically feature a longer guide taper (with a smaller ϕ angle) and are commonly manufactured in sets of 2 to 3 pieces. This design aims to minimize cutting forces during operation.
4.3 Methods to increase efficiency in tapping thread cutting process
Typically, the efficacy of thread cutting via tapping is limited, primarily due to the low cutting speed and idle stroke of the tap during tool reversal. To enhance performance, the following measures can be implemented:
-
Employ a self-reversing tap to facilitate swift withdrawal through the machined hole.
-
In nut machining, utilize spiral tapping to enable continuous machining and minimize tool backtime.
-
Utilize a combination tapping drill to integrate drilling and tapping into a single operation.
-
Perform thread machining on a specialized machine employing a combined drilling and thread milling tool, featuring a cutting blade on the front side for hole drilling and cutting blades on the side for thread milling.

4.4 Enhancing Precision and Efficiency with Sandvik Coromant's Tapping Solutions
The CoroTap series, including options such as the CoroTap 100 and 200, is engineered to deliver exceptional performance and reliability for various tapping applications. Additionally, the CoroMill series, particularly the CoroMill 331 and 332, provides superior thread milling solutions, ensuring efficient material removal and exceptional thread quality. Sandvik Coromant's expertise in cutting tool solutions ensures that their tapping products are well-suited to meet the demands of modern machining operations, delivering superior results and cost-effectiveness.

5. Elevate Your Manufacturing Efficiency with AMS and Sandvik Coromant
AMS Company Limited serves as Sandvik Coromant's official distributor in Vietnam. Our knowledgeable sales team is extensively trained and adept at assisting you in finding the ideal Sandvik Coromant product for your drilling, reaming, boring, and tapping applications. With over 20 years of experience in the precision industry, we have garnered the trust of esteemed businesses in Vietnam for delivering high-quality products for manufacturing operations, along with unparalleled after-sale service in the market. As the official distributor of Sandvik Coromant, we can provide the best prices available. Purchasing from other sources may compromise the product's quality, leading to potential consequences in cost, time, and labor within the manufacturing process. Reach out to AMS today to streamline your manufacturing process with Sandvik Coromant products and avoid potential setbacks.
AMS Company, Ltd.243/9/10D To Hien Thanh, Ward 13, District 10
Hot line: 028.3868 3738/3903 - Fax: 028.3868 3797