What is a CNC EDM Wire Cut Machine? Signs That Indicate Repair is Needed
Repairing CNC EDM wire cut machines is crucial for businesses involved in precision machining, especially mold-making workshops, automotive and motorcycle parts manufacturers, electronics and semiconductor companies, and medical device manufacturers. But when does a CNC wire cut machine require repairs? What are the key signs indicating the need for maintenance? Find out the detailed answers in the article below.
1. What is a CNC EDM Wire Cut Machine?
A CNC EDM wire cut machine (also known by other names such as CNC wire cutting machine or electrical discharge cutting machine) is a type of machine that uses computer numerical control (CNC) technology to cut electrically conductive materials, typically metals, by employing the EDM (Electrical Discharge Machining) process.
-
EDM (Electrical Discharge Machining): A machining method that utilizes a thin wire electrode to cut electrically conductive materials with high precision using electrical discharges.
-
CNC (Computer Numerical Control): A computer-controlled system that automates the machining process, improving accuracy and enabling the production of complex components.
Thus, a CNC EDM wire cut machine is an EDM wire-cutting system integrated with CNC control, ensuring higher precision, minimized errors, and optimized productivity.
>> See more: EDM CNC Wire Cut Machine Products
2. What Types of Wires Are Used in Wire Cut Machines?
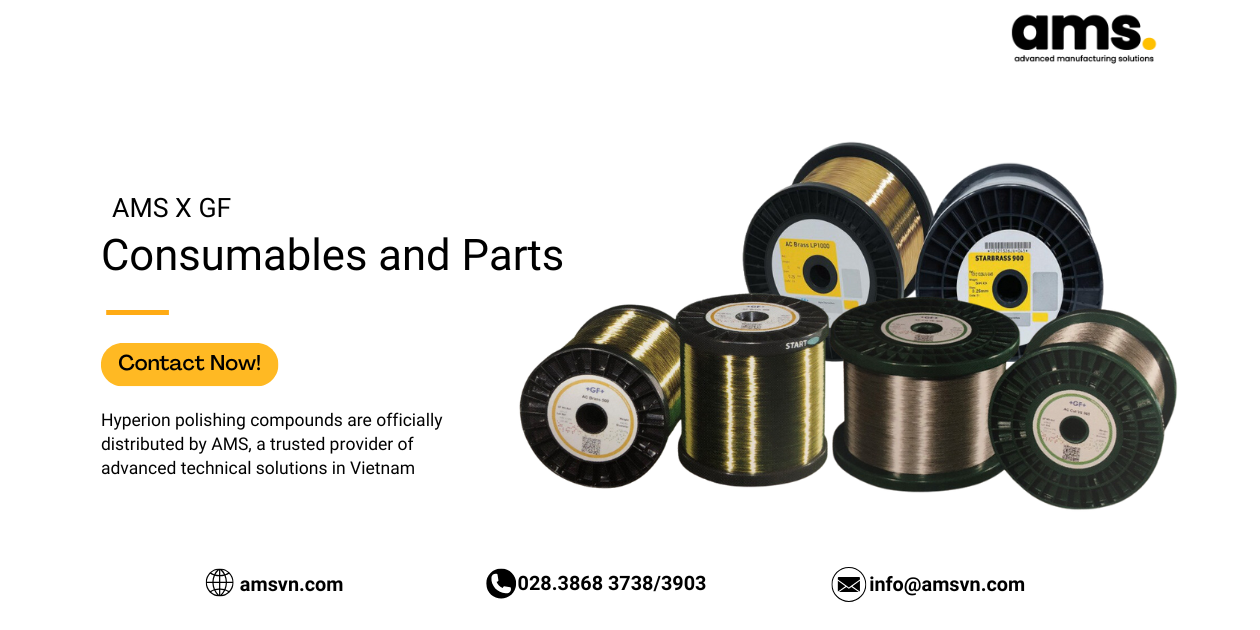
To optimize both performance and cost-efficiency, selecting the appropriate wire for CNC EDM wire cut machines is crucial, as it directly impacts cutting speed, accuracy, and surface finish.
Below are some commonly used wire types in EDM wire cut machines, along with the selection criteria for each:
-
Brass Wire: A popular and cost-effective choice, brass wire caters to a wide range of customer needs. For example, GF’s brass wire lineup includes standard LP brass wire, high-performance brass wire, and AC CUT VE premium brass wire — each designed for different precision and speed requirements.
-
Coated Wire: Featuring a brass or copper core coated with another metal, such as zinc, coated wire enhances cutting speed and improves surface finish. It is ideal for applications requiring high precision.
-
Tungsten Wire: Known for its high heat resistance and superior strength, tungsten wire is suitable for cutting ultra-hard metals and achieving exceptionally fine surface finishes.
-
Molybdenum Wire: Recognized for its heat resistance and excellent electrical properties, molybdenum wire is used in applications demanding extreme precision and minimal thermal distortion.
Choosing the right wire type ensures that EDM wire cut machines operate at peak efficiency, meeting both productivity and quality expectations.
3. Some Costs Businesses Face When Using CNC EDM Wire Cut Machines
CNC EDM wire cut machines are valuable assets used continuously and over long periods in business operations. AMS doesn’t just supply products to customers; we also offer cost-effective, sustainable solutions for the challenges businesses face. Let’s take a look at the factors influencing wire cutting costs.
-
Machine Costs: The cost of renting or purchasing an EDM wire cut machine can be significant. It’s advisable to invest in a new machine if it is used frequently and for long-term operations.
-
Labor Costs: Skilled and technically proficient operators contribute to the overall cost. Proper training and expertise are essential to ensure efficient operation.
-
Electricity Consumption: EDM wire cut machines consume a considerable amount of electricity, especially when running for long durations, which impacts operational costs.
-
Consumables and Parts (Spare Parts): These include costs for wire, filters, and dielectric fluids, all of which need to be replaced regularly.
-
Material Costs: The type of material being cut can affect costs, as harder materials may wear down the wire faster and require slower cutting speeds, increasing operational expenses.
-
Maintenance and Downtime: Regular maintenance is essential to keep the machine in optimal condition. Downtime for maintenance can lead to higher operational costs and reduced production capacity.
Considering these factors, businesses must carefully manage and plan for the costs associated with EDM wire cutting to maintain profitability and efficiency.
4. Advantage & Disadvantage
4.1 Advantage
CNC EDM wire cut machines offer several advantages over traditional machines. The products made using CNC EDM wire cutting machines are less dependent on the skill of the operator, as they rely instead on the programming content fed into the machine.
-
Faster machining speed: The production process is quicker, and the machining time is shorter, resulting in more products being created in less time.
-
Increased precision and capability: CNC wire cut machines can process harder materials due to their robust mechanical structure, enhancing overall performance and accuracy.
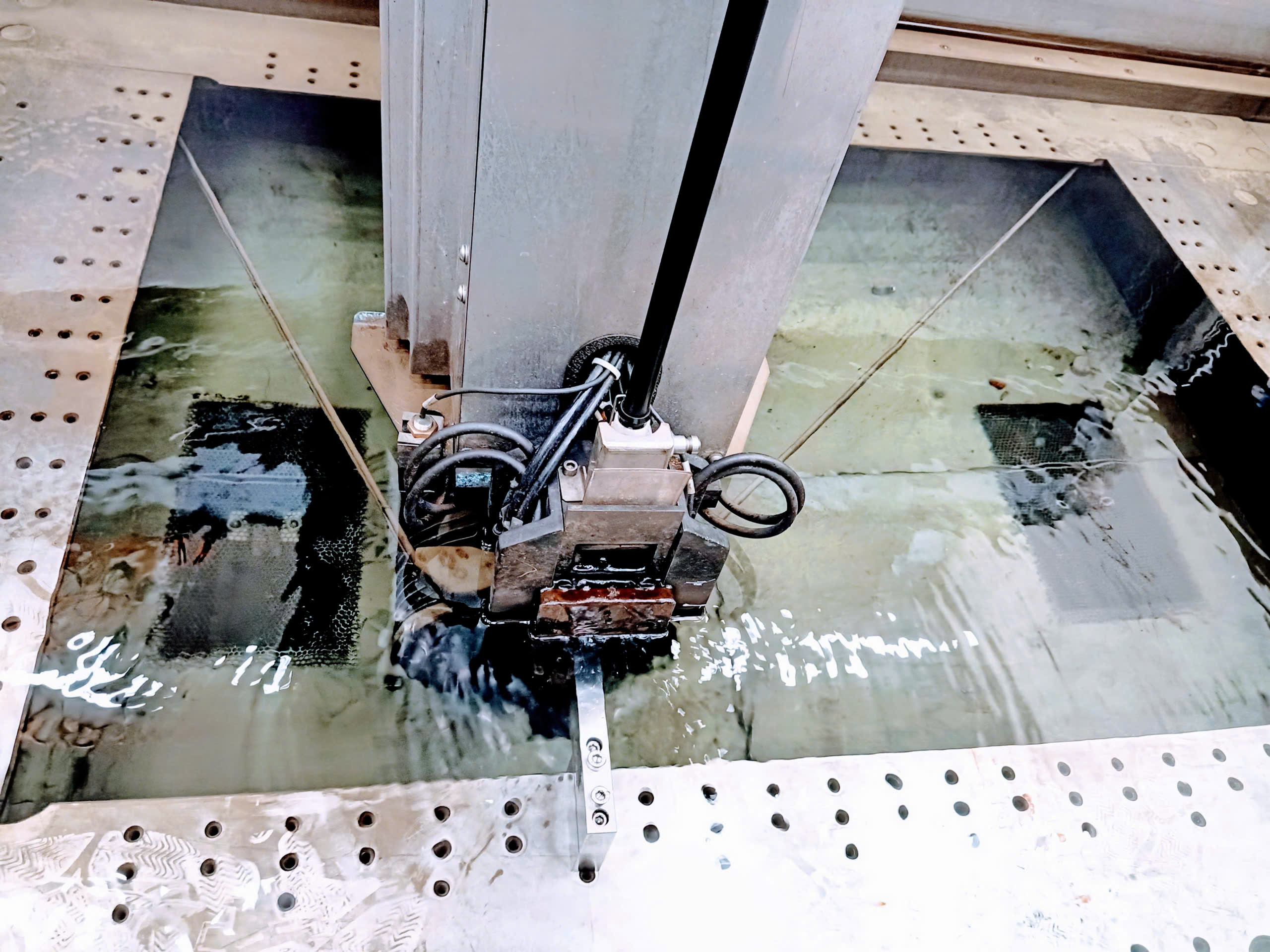
4.2 Disadvantage
-
Higher maintenance and repair costs: Maintaining and repairing CNC wire cut machines can be more expensive compared to traditional manual machines.
-
Higher initial investment: The cost of CNC wire cut machines is higher due to their advanced technology and superior quality.
-
Specialized expertise required: These modern machines require highly skilled engineers, and businesses may need to invest time and resources into training their staff to operate and maintain the equipment efficiently.
5. Target Groups That Need to Pay Attention to Wire Cut Machine Maintenance and Repair
-
Mold Manufacturing Workshops: Companies producing plastic molds, metal casting molds, stamping molds, and injection molds require stable operation of wire cut machines to ensure product accuracy.
-
Automotive and Motorcycle Component Manufacturing Plants: Metal parts in engines, gearboxes, and stamping molds need wire cutting to achieve high precision.
-
Electronics and Semiconductor Component Manufacturers: Wire cut machines are used to process molds and small parts that demand accuracy down to micrometers.
-
Precision Mechanical Part Processing Facilities: Companies specializing in producing shafts, gears, and machine components need to repair wire cut machines to maintain productivity and product quality.
-
Medical Equipment Manufacturing Plants: Surgical tools and medical components require high precision machining, and wire cut machines play a crucial role in this process.
-
Metal Sheet Processing Businesses: Wire cutting machines are commonly used to process parts made from stainless steel, aluminum alloys, and titanium with complex thickness and shapes.
6. Signs That Your Wire Cut Machine Needs Repair
Some common issues with wire cut machines include:
-
Surface imperfections: Workpieces show indentations or rough surfaces.
-
Electrode wire vibration: The wire oscillates excessively during operation.
-
Loose electrode wire: The wire is not held firmly, affecting cutting precision.
-
Abnormal noise from the drive wheel: Unusual sounds or irregular movement during operation.
-
Electrode wire breakage: Frequent wire snapping during machining.
-
Reduced cutting precision: Inability to achieve the required accuracy in machining.
7. Conclusion
Repairing a wire cut machine requires assessing the extent of the damage and selecting the right replacement parts. With over two decades of experience in providing advanced technical solutions, AMS is proud to offer high-quality EDM CNC wire cut machines and top-tier consumable parts. Contact AMS today for expert consultation!
AMS Company, Ltd.243/9/10D To Hien Thanh, Ward 13, District 10
Hot line: 028.3868 3738/3903 - Fax: 028.3868 3797