The Importance of Precision Mold Polishing in Manufacturing
1. What is a Precision Mold?
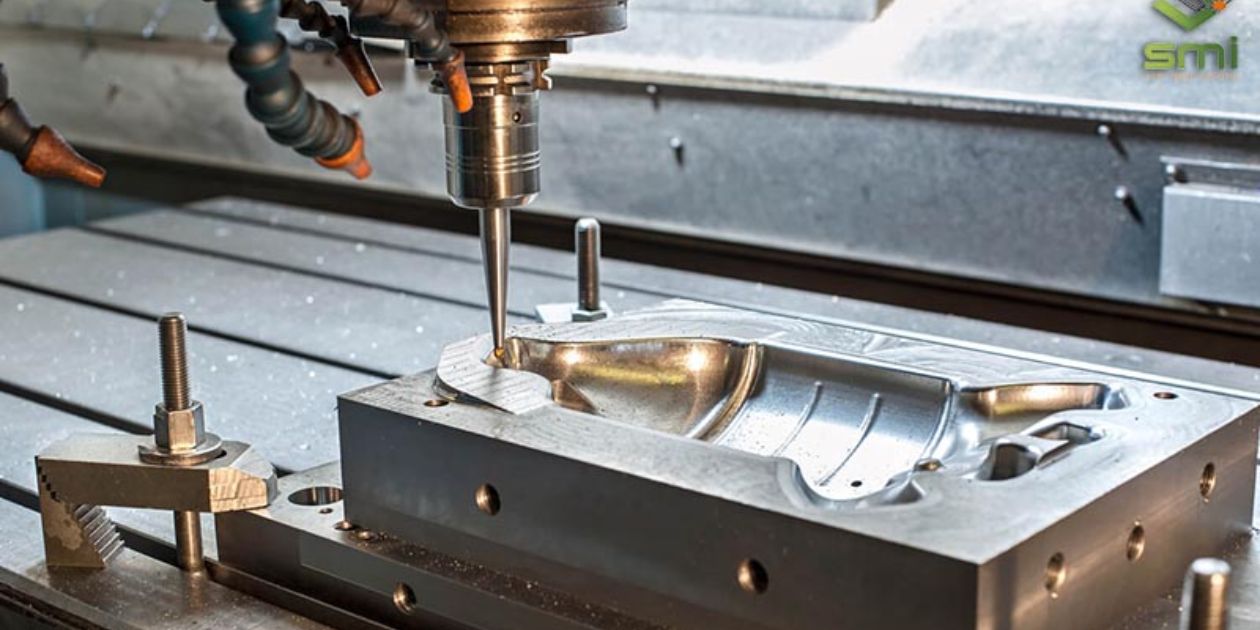
A precision mold is a tool or device designed to shape and form products. Each mold is utilized in an injection or casting process to create a specific product, either as a single-use or multi-use tool. The size, material, durability, and other specifications depend on customer requirements.
2. Applications of Precision Molds
Precision molds are not everyday household items but play a vital role in industrial production. They are indispensable in manufacturing, enabling the mass production of familiar products such as refrigerators, washing machines, beverage cans, and plastic bottles.
Precision molds are widely applied across various industries because most objects we use require molds for shaping individual components before assembly into final products. Some key applications include:
-
Automotive and motorcycle parts manufacturing
-
Medical plastic production: Breathing tubes, syringes, IV tubes, test tubes, etc.
-
Household appliance components: Refrigerators, washing machines, fans, etc.
Precision mechanical parts: Beyond plastic injection molding, molds are also used in producing precision mechanical components.
Most plastic and rubber products are manufactured using injection molding technology. As society advances, product quality and aesthetics become increasingly important. Consequently, the mold-making industry continues to grow to meet market demands.
Precision mold polishing plays a key role in this development by ensuring molds produce high-quality, defect-free components, ultimately improving production efficiency and product performance.
3. The Role of Precision Mold Polishing in Industrial Production
Precision mold polishing is just one step in a series of processes required to achieve a flawless mold surface. However, businesses cannot overlook precision mold polishing for the following reasons:
-
Minimizing Manufacturing Defects: The mold surface directly affects cooling speed and product quality. If the mold is not precisely polished, it may lead to defects such as scratches, air bubbles, and difficulties in removing the product from the mold.
-
Extending Mold Lifespan and Optimizing Costs: Over time, molds accumulate residues that cause chemical and mechanical wear. Precision polishing helps protect the mold surface, extending its lifespan and reducing maintenance and replacement costs.
-
Meeting Stringent Industry Standards: Industries such as optical components manufacturing, medical devices, and high-performance plastics require exceptionally smooth mold surfaces. Precision mold polishing ensures compliance with technical standards and enhances a company's competitiveness in precision mold fabrication.
Given these critical roles, precision mold polishing is a key factor in achieving high-quality product finishes.
4. Factors Affecting the Precision Mold Polishing Process
Several factors influence the mold polishing process, including workpiece condition, material quality, heat treatment processes, and the skill level of the technician. Here are some essential considerations:
-
Choosing the Right Grinding Method: Selecting an appropriate polishing technique prevents potential damage to the mold.
-
Using High-Quality Steel: Steel with excessive impurities or internal voids will hinder the polishing process and prevent optimal results.
-
Ensuring Proper Heat Treatment: A well-executed heat treatment process creates a uniform mold surface, essential for achieving a high-polish finish.
-
Combining Quality Workpieces and Polishing Tools: Fifty percent of a super-smooth surface comes from high-quality workpieces and tools, while the remaining fifty percent depends on the technician's expertise.
By focusing on these factors, manufacturers can achieve superior mold polishing results, ensuring efficiency and product consistency.
5. Guide to Choosing the Right Mold Polishing Products
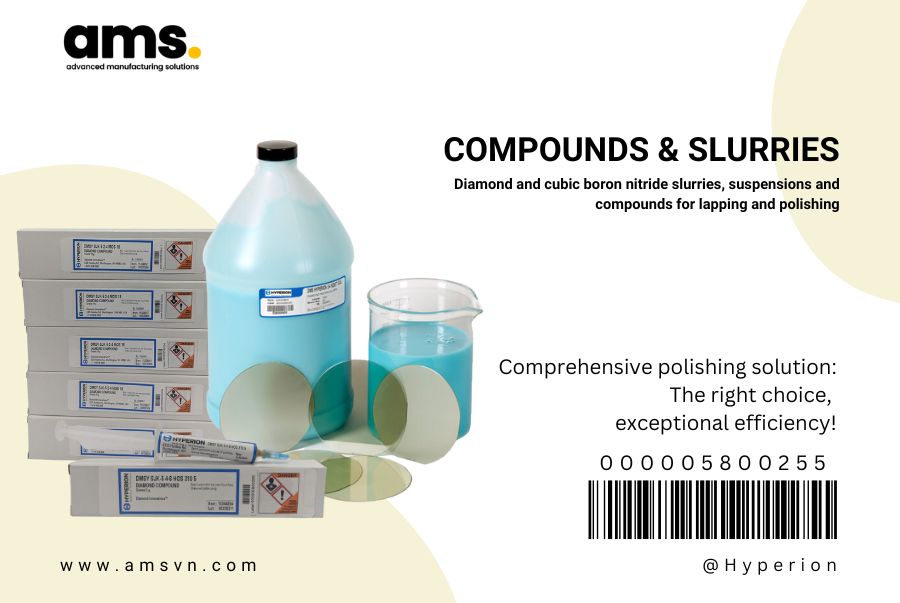
Polishing materials play a crucial role in achieving precision mold finishing. In this article, AMS experts provide recommendations on diamond polishing compounds tailored to specific mold surface requirements.
Today, the market offers a wide variety of polishing compounds from different sources. AMS delivers superior polishing solutions with Hyperion diamond polishing powders, featuring a range of slurries, including:
-
K700: Water-soluble diamond polishing powder
-
K210: Oil-soluble diamond polishing powder
-
G400: Oil/water-soluble diamond polishing powder
Fundamental Polishing Principles from Hyperion’s International Experts
To ensure optimal polishing results, follow these key guidelines:
- Maintain a clean polishing area.
- Use a dedicated polishing tool for each grit size and store each tool separately.
- Polishing tools will gradually become conditioned and improve over time with use.
- Thoroughly wash hands and clean the workpiece between grinding steps.
- Apply diamond compound to the tool for manual polishing and directly onto the workpiece for machine polishing.
- Polish scratches at a 90-degree angle to accelerate material removal and easily track the removal of previous marks.
- For heavy material removal, use high pressure and coarse abrasives. For final finishing, apply low pressure and the finest abrasives.
6. Conclusion
Precision mold polishing plays a vital role in enhancing production efficiency. At AMS, we are committed to providing high-quality polishing solutions with traceable raw materials, durable polishing tools, and, most importantly, cost-effective pricing. Contact AMS today for expert consultation on your mold polishing process!
AMS Company, Ltd.243/9/10D To Hien Thanh, Ward 13, District 10
Hot line: 028.3868 3738/3903 - Fax: 028.3868 3797