Top 5 popular mechanical cutting tools today
Mechanical cutting tools in turning, milling, drilling,... are essential tools for processing product details in the mechanical and machinery manufacturing industry.
In the mechanical engineering industry, cutting tools are indispensable for the production of machine components. Whether you are an industrial buyer, a plant engineer, or a workshop owner, this article provides the detailed insights you may be seeking. Join AMS as we explore the top five essential precision cutting tools used in modern machining.
1. The importance of cutting tools in precision engineering
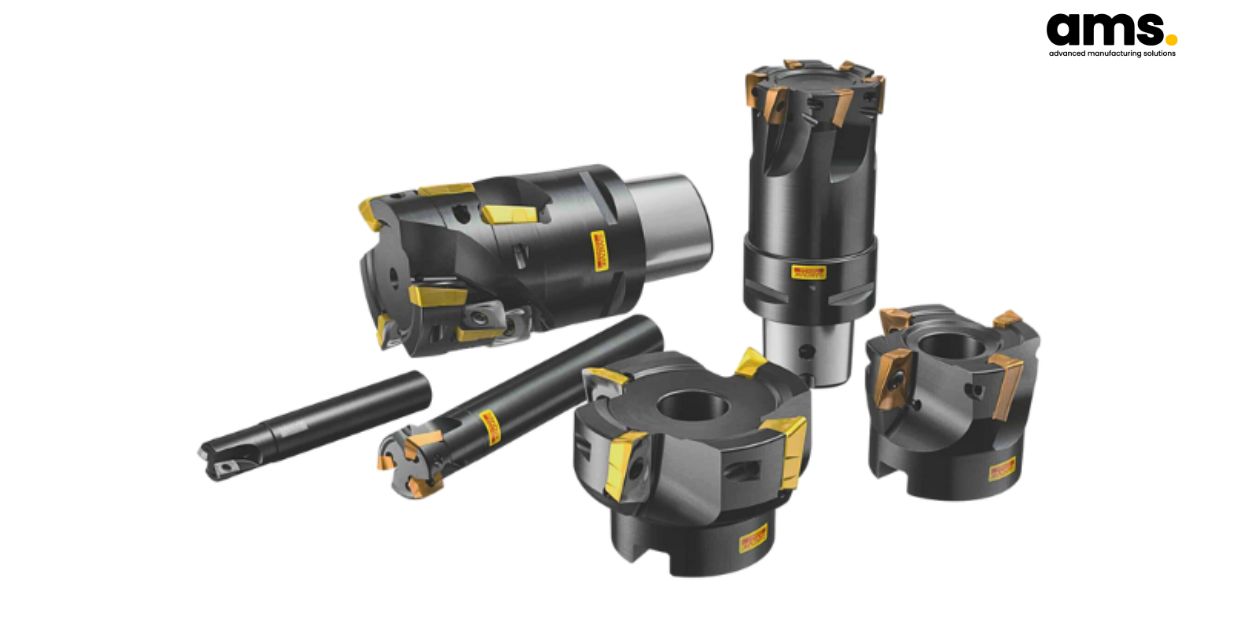
Cutting tools are durable instruments designed to work on materials harder than those being machined. They are attached to machining equipment (such as lathes, milling machines, planers, and CNC machines) to physically interact with the workpiece, applying actions like abrasion or removal to shape it according to technical requirements. Typically, precision cutting tools are compact, easy to store and transport, and optimized for high efficiency.
In the evolving landscape of manufacturing technology, cutting tools must meet exacting standards in durability, accuracy, and performance. This is particularly critical for industries like mold manufacturing, electronics, and mechanical fabrication.
2. Top 5 Essential Precision Cutting Tools
2.1. Drilling Tools
Drilling is a crucial step often carried out in the final stages of production. Companies look for tools that ensure accuracy, stability, and the ability to handle diverse materials. Key features include reduced vibration, precise hole creation, and material surface protection.
-
Solid Carbide Drills: Optimized for precision and durability, these are suitable for high-speed applications with strict tolerance requirements.
-
Indexable Drills: Cost-effective with replaceable inserts, ideal for varied applications where ultra-high precision is not required.
-
Exchangeable Tip Drills: A balance of cost and accuracy with the convenience of quick tip replacements.
-
Taps: Specialized for internal threading rather than standard drilling.
AMS suggests the following for various drilling needs: Coromant U Drill (LCMX 04 03 08-53 1020), CoroDrill® 880 (880-D1750L25-03).
2.2. Turning Tools
Turning tools play a vital role in machining by employing a rotational motion combined with tool advancement to shape parts. Turning processes require high precision to ensure a smooth, unwarped surface finish.
-
General Turning Tools: Versatile for most turning operations, but less suited for parting or grooving.
-
Parting and Grooving Tools: Designed specifically for accurate external grooving and parting-off applications.
-
Internal Grooving Tools: Built for internal grooves, providing precision and high surface finish.
Some recommended turning tools: T-Max® P Turning Tool (DCLNR 3232P 16), CoroTurn® XS for hard carbide threading (CXS-06TH100MM-6215R 1025).
2.3. Milling Tools
Milling tools are used for complex surface and shape machining. Popular types include face and groove milling tools for creating flat surfaces, corners, and intricate contours.
-
Face Milling Tools: Used for wide flat surfaces, often in roughing and finishing applications.
-
Shoulder Milling Tools: Creates precise 90-degree grooves and edges.
-
Profile Milling Tools: Suited for complex profile shapes, including curved surfaces.
-
High-Feed Milling Tools: Designed for high-speed, shallow-depth cutting, primarily in roughing applications.
For your needs, consider tools such as CoroMill® 331 Face and Edge Milling Cutter (N331.1A-054508H-NL1025), CoroMill® 200 Face Mill (R200-015A20-10M), CoroMill® Century (Milling Tools - R590-110504H-NL H10);....
>> See more
2.4. Parting and Grooving Tools
These tools are essential for grooving and parting, directly impacting the quality of the final product, especially in applications requiring durability and precision.
AMS offers tools like the CoroCut® MB Carbide Grooving Head (MB-09G200-00-14R 1025).
2.5. Threading Tools
Threading tools are designed for creating internal and external threads with high accuracy to ensure perfect component fit.
3. Why Choose Sandvik Coromant for Precision Cutting Tools?
Sandvik Coromant, established in 1942, is a globally recognized brand. With continuous innovations, particularly in metal cutting solutions, Sandvik Coromant ensures quality and advanced technical solutions. In Vietnam, AMS believes that using superior tools sets the stage for a promising future in manufacturing.
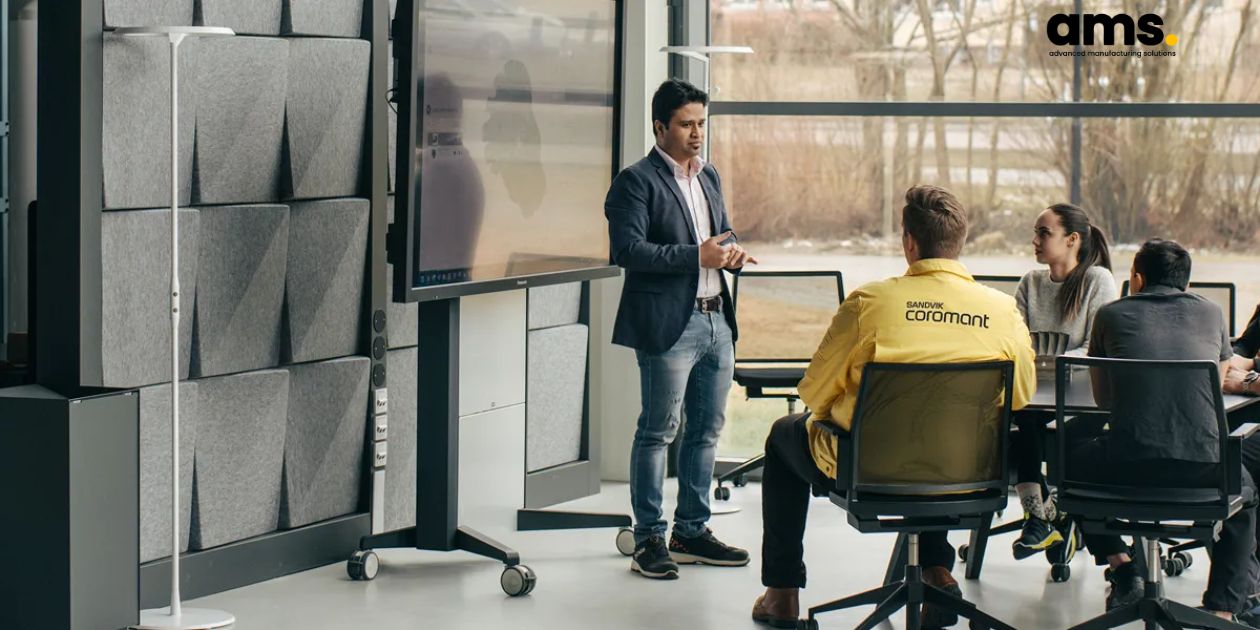
Key reasons to choose AMS as your Sandvik Coromant supplier:
-
Enhanced Profitability and Customer Retention: High-quality tools produce superior products, ensuring customer trust and repeat orders. Investing in quality allows businesses to take on technically demanding jobs with confidence.
-
Reduced Repair Costs and Tool Replacements: Quality tools minimize the frequency of repairs and replacements, saving costs over time.
-
AMS guarantees high standards, clear brand origins, dedicated technical support, and a stable pricing and purchasing policy.
4. Conclusion
These top five precision cutting tools—drills, turning tools, milling tools, parting and grooving tools, and threading tools—are vital for minimizing maintenance costs and enhancing productivity. AMS proudly distributes Sandvik Coromant tools, ensuring quality and expert guidance. For more information on our mechanical cutting tools, please contact us via the hotline below or explore our product catalog on amsvn.com.
AMS Company, Ltd.243/9/10D To Hien Thanh, Ward 13, District 10
Hot line: 028.3868 3738/3903 - Fax: 028.3868 3797